Реферат по теме выпускной работы
Содержание
- Введение
- 1. Анализ существующих методов оптимизаци режимов шлифования по упругой схеме
- 2. Анализ существующих конструкций устройств для шлифования по упругой схеме
- 2.1 Устройство для внутреннего и наружного круглого шлифования
- 2.2 Устройство для круглого внутреннего шлифования
- 3. Постановка задач исследования
- 4. Расчет динамических характеристик шпиндельного узла
- Выводы
- Перечень ссылок
Введение
В современной промышленности широкое распространение получили твердые сплавы, которые относятся к труднообрабатываемым материалам. Для их эффективной обработки используются алмазы, а также шлифовальные круги на металлической связке, заправленные электроэрозионным способом.
Оптимизация режимов обработки классическим способом требует больших затрат времени, которые могут быть существенно уменьшены за счет использования нового способа определения режимов, предложенного на кафедре металлорежущих станков и инструментов ДонНТУ, с использованием мгновенной лимитированной режущей способности круга, определяемой при шлифовании по упругой схеме. Применение способа нахождения режимов с учетом текущей лимитированной режущей способности круга способствует уменьшению трудоемкости поиска режимов и позволяет полностью использовать режущую способность рабочей поверхности круга (РПК).
Актуальность темы: исследование режущей способности РПК при внутреннем шлифовании твердых сплавов алмазными кругами в литературе отсутствуют, что свидетельствует об актуальности данной работы.
Объект исследования: закономерность изменения режущей способности поверхности круга при внутреннем шлифовании твердого сплава кругами из сверхтвердых материалов, заправленных электроэрозионным способом.
Цель работы: повышение производительности внутреннего шлифования твердых сплавов за счет полного использования режущей способности круга.
Научная новизна работы заключается в том, что впервые будут получены уравнения, описывающие изменение режущей способности круга при внутреннем шлифовании по упругой схеме.
Практическая ценность результатов работы: разработка новой конструкции шлифовальной бабки, в которой за счет новых конструктивных элементов обеспечивается возможность внутреннего шлифования отверстий, радиус которых превышает ход передней бабки, а также выполнения шлифования наружной цилиндрической поверхности при сохранении качества обработки и материальных затрат, а также получения уравнений, описывающих изменение режущей способности поверхности круга, которые впоследствии могут быть использованы для оптимизации процесса шлифования.
1. Анализ существующих методов оптимизаци режимов шлифования по упругой схеме
Обеспечение высокопроизводительной механической обработки различных групп материалов при условии получения необходимых показателей качества и минимизации затрат на осуществление процесса обработки является перманентно актуальной задачей, которая постоянно решается на этапе технологической подготовки машиностроительного производства.
Обязательной процедурой при решении указанной задачи является поиск оптимальных режимов обработки. Применительно к процессам шлифования, самым распространенным и одним из наиболее точных методов, к этому времени, является классический экспериментально-теоретический метод нахождения режимов, который включает следующие этапы [1]:
- составления системы уравнений, описывающие технические ограничения, накладываемые на режимы резания требованиями к детали, станком, инструментом и условиями производства;
- математическое описание целевой функции, которая отмечает цель оптимизации;
- совместное рассмотрение технических ограничений и целевой функции и определение на этой основе оптимального режима шлифования.
Главным недостатком этого метода, который существенно ограничивает практические возможности его использования в технологической подготовке производства деталей из новых конструкционных материалов или в условиях шлифования кругами с новыми характеристиками, является его высокая трудоемкость, обусловлена большими затратами времени на эксперименты, которые необходимы для получения всех уравнений и зависимостей, описывающих технические ограничения. Кроме того, он дает результаты, которые невозможно использовать в случае, когда режимы или обработке выходит за пределы, в которых были найдены уравнения технических ограничений, а также не учитывает изменение режущей способности РПК во время работы.
В течение длительного времени на кафедре Металлорежущие станки и инструменты
ДонНТУ ведутся исследования, связанные с изучением следующих вопросов:
- определение параметров процесса шлифования, обеспечивающих заданную шероховатость обработанной поверхности [2];
- нахождения допустимой силы взаимодействия рабочей поверхности круга (РПК) с поверхностью заготовки, при которой не состоится фазово-структурных изменений в поверхностном слое обрабатываемой заготовки [3];
- нахождения допустимой силы взаимодействия РПК с поверхностью заготовки, при которой не произойдет изменений физико-химических свойств инструментального материала [4,5];
- поиском интегрального технического ограничения на режимы шлифования, обеспечивающих максимальную производительность при соблюдении заданных требований по качеству обработки [4,5].
По результатам проведенных исследований разработан ряд методик, которые позволяют определять элементы режима для обработки различных материалов и условий шлифования при условии соблюдения всех требований к качеству обработанной поверхности.
В работе [6] проведенное составления целостного комплекса методик назначения режимов шлифования, обеспечивающих стабильные показатели качества обработки и определения обобщенных режимных параметров процесса для упругой и жесткой схем обработки.
Рассмотрим комплекс методик, применяемых для определения оптимальных режимов плоского врезного алмазного шлифования с электроэрозионными влияниями на РПК (по упругой схеме) согласно предложенной нами последовательностью оптимизации, которая включает следующие этапы [7]:
- Расчет скорости детали, при которой достигается необходимая шероховатость обработанной поверхности.
- Расчет максимально допустимого усилия подавления заготовки до круга в процессе шлифования по упругой схеме, при котором удовлетворяется лимитированное техническое ограничение.
- Экспериментальное определение закона изменения предельной режущей способности круга во времени при шлифовании по упругой схеме, которая кинематически является аналогичной жесткой схеме.
- Определение режимов электроэрозионных воздействий на РПК, обеспечивающих минимальную удельную себестоимость обработки, с учетом явлений, вызвавшие ухудшение режущих свойств круга.
- Описание закона изменения глубины шлифование по упругой схеме в соответствии с законом изменения предельной режущей способности круга без учета процесса засаливания РПК.
- Определение величины подачи при врезании по жесткой схеме.
При алмазном шлифовании производительность обработки зависит от режущей способности круга, поэтому необходимо найти такой параметр режима резания, с помощью которого можно будет в любой момент обработки уравнять количество материала, который подводится для удаления за счет рабочих движений, и количество материала, который может удалить рабочая поверхность круга за счет ее режущей способности. Для этого пользуются параметром – мгновенной текущей лимитированной режущей способностью круга [8] – которая представляет собой объем материала, который удаляется в единицу времени, в любое время обработки, при этом выполняются технические ограничения, накладываемые на режим обработки качеству обработанной поверхности или инструментом (например, температурой порога фазово-структурных преобразований в поверхностном слое детали, температурой графитизации алмаза, его прочностью и прочее).
Определение режимов максимальной производительности с использованием режущей способности круга в качестве ограничивающего параметра осуществляется в следующие этапы:
- находят предельные значения технических ограничений, которые накладываются на режим требованиями к качеству обработанной поверхности, и шлифовальным кругом в пределах технологических возможностей станка;
- использование технического ограничения, которое удовлетворяет требованиям всех рассмотренных выше ограничений (лимитированное ограничения), рассчитывают силу поджатия образца до рабочей поверхности круга с использованием параметров рабочей поверхности, сложившейся во время правки;
- с использованием упругой схемы шлифовка, кинематика которой идентична жесткой, экспериментально определяется регрессионная зависимость, описывающая изменение режущей способности РПК при шлифования.
Как показало сравнение классического метода нахождения оптимальных режимов шлифования [9] и предложенного метода [8], использование текущей лимитированной режущей способности круга позволяет значительно сократить затраты времени на поиск режимов внутреннего шлифования, которые обеспечивают минимальную себестоимость обработки при удовлетворении требований лимитированного технического ограничения.
2. Анализ существующих конструкций устройств для шлифования по упругой схеме
2.1 Устройство для внутреннего и наружного круглого шлифования
Известно устройство (рис. 1) [10], которое может использоваться для внутреннего и внешнего круглого шлифования. Оно состоит из нижней плиты 1, которая неподвижно соединена с передней бабкой внутришлифовального станка, корпуса 2, расположенного в ласточкиных направляющих плиты 1 с возможностью перемещения в отношении плиты 1 в направлении к рабочей поверхности шлифовального круга.
![Расположение элементов устройства для круглого шлифования перед обработкой [10]](images/prustriy dlya narugnogo shlifovaniya.png)
Рисунок 1 – Расположение элементов устройства для круглого шлифования перед обработкой [10]
В цилиндрической полости корпуса на подшипниках размещена втулка 3 устройства для закрепления заготовки (например, трехкулачковый патрон (на чертеже не показан)). Поверхность 4 втулки 3 контактирует с колесом 5, жестко посаженным на вал 6, расположенным в отверстии корпуса 2. На противоположном конце вала 6 жестко закреплено колесо 7, поверхность которого контактирует с поверхностью паразитного колеса 8, размещенного на одной из осей водила 9. Водило 9 имеет форму треугольника, на одной из вершин которого расположена ось паразитного колеса 8, а на других вершинах – оси колес 10 и 11.Планка 12 предназначена для обеспечения постоянного межосевого расстояния между колесами 8 и 7. Поверхности колес 8, 10 и 11 находятся в контакте с поверхностью оболочки 13, закрепленной на шпинделе шлифовального станка и обеспечивают постоянный совпадение осей шпинделя и водила 9 независимо от положения вала 6. Груз 14 через систему рычагов путем перемещения корпуса 2 относительно нижней плиты 1 обеспечивают поджатие поверхности заготовки, закрепленной в трехкулачковом патроне, к поверхности РПК.
Работает устройство для круглого шлифования таким образом.
Перед шлифованием элементы устройства расположены согласно рисунку 1. После включения электродвигателя привода главного движения шпиндель начинает вращаться, а вместе с ним и оболочка 13. Движение от оболочки 13 через паразитную колесо 8 передается на колесо 7 и через вал 6 на колесо 5, далее на поверхность 4 втулки 3 с патроном в котором закреплено заготовку. После включения привода шлифовального круга корпус 2 под действием груза 14 начинает перемещаться в направлении РПК, обеспечивая шлифования с постоянной силой прижима заготовки до рабочей поверхности круга. После удаления определенной величины припуска расстояние между осями шпинделя и обрабатываемой заготовки характеризуется величиной Н1 (рис. 2), которая меньше величины Н.
Учитывая то, что межосевое расстояние между осями колес 8 и 7 остается за счет планки 12 постоянной, при перемещении верхней плиты в направлении РПК колеса 8 и 7 находятся в постоянном контакте, а водило 9 меняет свое положение в оболочке 13 относительно своего предыдущего положения.
![Расположение элементов устройства для круглого шлифования после удаления определенной величины припуска [10]](images/prustriy dlya narugnogo shlifovaniya_2.png)
Рисунок 2 – Расположение элементов устройства для круглого шлифования после удаления определенной величины припуска [10]
При использовании устройства при круглом внешнем шлифовании плита 1 устанавливается на стол круглошлифовального станка, а в патрон закрепляют заготовку цилиндрической формы, внешняя поверхность которой подлежит обработке.
Для обеспечения вращения заготовки в конструкции устройства используется бесступенчатый привод главного движения, который есть на станке. Это достигается благодаря выполнению верхней плиты в виде корпуса, установке на шпинделе станка оболочки, с внутренней поверхностью которой контактируют поверхности колес, расположенных на водиле, причем одно из них является паразитным; колесо, которое установлено на одном из концов вала, расположенного в корпусе, имеет возможность контактирования с поверхностью паразитного колеса, а колесо, которое расположено на другом конце этого же валу, установленное с возможностью контакта с поверхностью втулки устройства для закрепления заготовки; кроме того, постоянное расстояние между осью паразитного колеса и валом, расположенным в корпусе, обеспечивается с помощью планки, установленной с возможностью поворота относительно оси паразитного колеса и корпуса.
Недостатком конструкции является ее сложность при изготовлении.
2.2 Устройство для круглого внутреннего шлифования
На рисунке 3 приведена модель внутреннего шлифования.
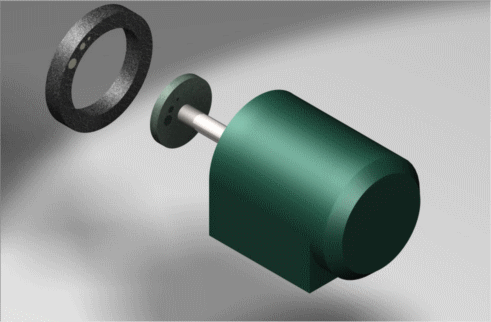
Рисунок 3 – Модель внутреннего шлифования
В качестве устройства для внутреннего шлифования используется шлифовальная бабка (рис. 4) [11], которая состоит из корпуса 1, который расположен на столе 2. Шлифовальная головка 3 со шлифовальным кругом 4 закреплена с двух сторон в обоймах 5, которые имеют сверху и снизу призматические канавки с расположенными в них шариками 6. С шариками 6 находятся в контакте призматические канавки планок 7, которые закреплены на торце стаканов 8, закрепленных в отверстии корпуса 1. Канавки планок 7 образуют шариковые направляющие, в которых в горизонтальном направлении может перемещаться относительно стола шлифовальная головка, поджимая рабочую поверхность шлифовального круга 4 к обрабатываемой поверхности заготовки с постоянной силой, которую задают при помощи нагрузочного устройства.
Нагрузочное устройство состоит из груза 9, который пластинчатой цепью 10 соединено со шлифовальной головкой 3 через ролик 11. Электродвигатель 12 закреплен на столе 2 с помощью стойки 13 таким образом, что ось шкива 14 электродвигателя 12 и шкива 15 шлифовальной головки 3 находятся в одной вертикальной плоскости.
Такое расположение осей шкивов 14 и 15 направляет силу натяжения ремня 16 перпендикулярно направлению перемещения шлифовальной головки и при величинах перемещений, характерных для выполнения шлифования по упругой схеме, практически не влияет на величину силы поджима РПК к обрабатываемой поверхности заготовки, которая задается грузом 9.
![Шліфувальна бабка [11]](images/prustriy dlya vnutrennego shlifovaniya.png)
Рисунок 4 – Шлифовальная бабка [11]
Шлифование по упругой схеме выполняется следующим образом.
После установки заготовки в патроне бабки изделия, устанавливают величину перемещения стола вдоль оси заготовки, при которой шлифовальный круг должен находиться по высоте в контакте с обрабатываемой поверхностью, включают привод вращения заготовки, потом электродвигатель, а шлифовальный круг вводят в обрабатываемый отверстие. Перемещая бабку изделия в направлении, перпендикулярном оси шлифовальной головки, вводят РПК в контакт с обрабатываемой поверхностью, обеспечив при этом зазор между наружной цилиндрической поверхностью шлифовальной головки с внутренней цилиндрической поверхностью стаканов. В этом случае шлифования будет производиться с постоянным поджатием РПК к обрабатываемой поверхности заготовки, величину которого задает груз. Во время удаления припуска при шлифовании, зазор между внешней поверхностью шлифовальной головки и внутренней поверхностью 8 стаканов будет уменьшаться, требуя компенсации перемещением бабки изделия, и обеспечивая постоянное отсутствие контакта между шлифовальной головкой и стаканами.
При закреплении шлифовальной головки в корпусе неподвижно, например, с помощью винта установленного в корпус (на графических материалах винт не показан), возможно выполнение шлифования по жесткой схеме.
Использование упругой схемы шлифования обеспечивает уменьшение трудоемкости поиска оптимальных режимов и повышения производительности обработки до 30%.
Предложенная шлифовальная головка может быть применено на машиностроительных предприятиях и в лабораторных условиях при проведении исследований.
3. Постановка задач исследования
Из приведенного анализа видно, что определение оптимальных режимов шлифования с использованием обобщающих показателей обработки позволяет уменьшить трудоемкость поиска оптимальных режимов.
Для определения изменения текущей мгновенной режущей способности круга используется упругая схема шлифования с постоянной силой поджатия заготовки к РПК. Для выполнения шлифования по упругой схеме разработаны устройства, которые с одной стороны являются сложными, а с другой – их невозможно использовать для шлифования по упругой схеме в широком диапазоне изменения смещение шлифовальной бабки относительно поверхности заготовки. В связи с этим в магистерской работе ставятся следующие основные задачи:
- Предложить конструкцию шлифовальной бабки, которая позволяет выполнять на внутришлифовальном станке не только внутреннее шлифование по упругой схеме, но и шлифования наружных поверхностей.
- Выполнить расчет динамических характеристик шпиндельного узла.
- Проанализировать напряженно-деформированное состояние шлифовальной бабки.
- Разработать рабочий чертеж шлифовальной бабки.
- Исследовать влияние вида сверхтвердых материалов (алмаз и эльбор) на изменение текущей режущей способности круга при внутреннем шлифовании быстрорежущей стали Р6М5Ф3.
- Выполнить статистический анализ исследований.
- Подобрать уравнения регрессии, описывающие изменение режущей способности кругов из алмаза и эльбора при шлифовании стали Р6М5Ф3.
4. Расчет динамических характеристик шпиндельного узла
Среди численных методов расчета статических и динамических характеристик шпиндельных узлов станков как линейных упругих систем получил распространение метод начальных параметров в матричном формулировке (метод переходных матриц). Метод заключается в том, что шпиндель (рис. 5) рассматривают как балку на упругих опорах с вяжущим демпфированием, которая состоит из участков, разделенных изменением момента инерции сечения самого расположением шпинделя, опор, сосредоточенных масс деталей, смонтированных на шпинделе, внешних сосредоточенных нагрузок. Пользуясь этим методом, при известных значений параметров в начале каждого участка шпинделя находят значения параметров в конце участка. Данный метод существенно упрощает и систематизирует динамический расчет, позволяет применять ЭВМ [14].
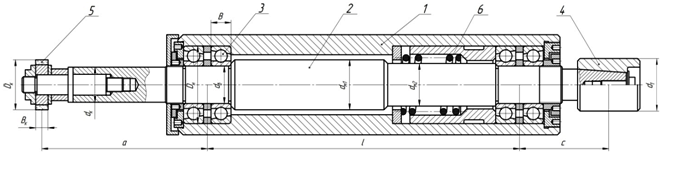
Рисунок 5 – Схема конструкции шпиндельного узла шлифовальной бабки станка модели 3А227П: 1 – корпус шпиндельного узла, 2 – вал шпинделя, 3 – подшипник скольжения, 4 – ведомый шкив, 5 – оправка с шлифовальным кругом, 6 – распорная втулка
Рассмотрим шпиндель приведенный на рисунке 5, как балку на упругих опорах с вяжущим демпфированием, и составим расчетную схему (рис. 6).
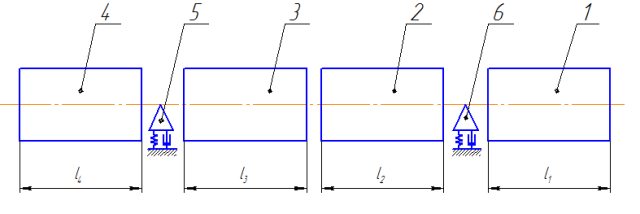
Рисунок 6 – Расчетная схема шпиндельного узла: 1 – ведомый шкив; 2, 3 – участки шпиндельного узла; 4 – вылет шпинделя; 5,6 – опоры подшипниковые
Расчет динамических характеристик шпиндельного узла проводится с помощью программы на ПЭВМ в пакете Mathcad. В качестве исходных данных для расчета являются: погонные массы и моменты инерции участков шпиндельного узла, жесткость и величина демпфирования в опорах.
Результатом расчета являются графики амплитудно-частотной характеристики (АЧХ) и амплитудно-фазово-частотной характеристики (АФЧХ), что показаны на рисунке 7 и рисунке 8.
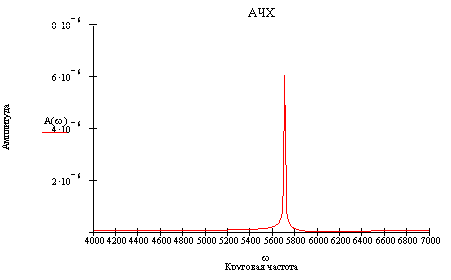
Рисунок 7 – График амплитудно-частотной характеристики шпиндельного узла внутришлифовального станка мод. 3А227П
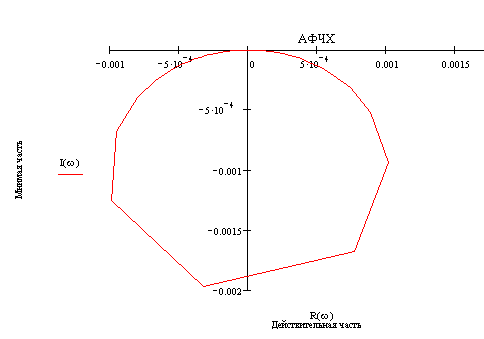
Рисунок 8 – График амплитудной фазово-частотной характеристики шпиндельного узла внутришлифовального станка мод. 3А227П
По графику АЧХ определяем, что изменение амплитуды происходит, когда круговая частота ω = 5700 рад/с, что соответствует собственной частоте колебаний шпиндельного узла f = 907 Гц. Проводить обработку в 30% диапазоне от собственной частоты колебаний шпиндельного узла, то есть 272 Гц, не рекомендуется, так как возможно возникновение явления резонанса колебаний – система становится неуправляемой. Это явление является негативным, вследствие чего невозможно провести механическую обработку с заданной точностью.
Рассмотрим диапазон частот вращения, в котором выполняется обработка на внутришлифовальном станке 3А227П. Шлифование отверстия D=45 мм выполняется при скорости вращения шлифовального круга Vк = 20 м/мин.
Число оборотов электродвигателя nд=2880 об/хв (ωд=302 рад/с), что соответствует частоте вынужденных колебаний fд=48 Гц; шпиндель шлифовального круга вращается с частотой nк = 9555 об/мин (ωк=1000 рад/с), что соответствует частоте вынужденных колебаний fк=160 Гц. Как видно, вынуждены частоты колебаний шпиндельного узла не совпадают с частотой собственных колебаний, и не попадают в 30% диапазон, и, следовательно, резонансные явления не возникнут.
Выводы
В даной работе проведен анализ существующих методов оптимизации режимов шлифования и установлено, что использование обобщающих показателей режимов шлифования, обеспечиващие стабильные показатели качества, позволяют уменьшить трудоемкость поиска оптимальных режимов.
На основе анализа существующей конструкции устройства для шлифования по упругой схеме планируется предложить конструкцию шлифовальной бабки, которая может быть применена при внутреннем шлифовании по упругой схеме с постоянной величиной поджатия РПК к поверхности образца, обеспечивая возможность внутреннего шлифование отверстий, радиус которых превышает ход передней бабки, выполнения шлифования наружной цилиндрической поверхности при сохранении качества обработки и материальных затрат.
Также был проведен расчет динамических характеристик шпиндельного узла методом начальных параметров в матричном виде, который позволяет определить нижнюю собственную частоту собственных колебаний шпиндельного узла, при которой может возникать явление резонанса.
Важное замечание
При написании данного реферата магистерская работа еще не завершена. Окончательное завершение: декабрь 2012 года. Полный текст работы и материалы по теме могут быть получены у автора или его руководителя после указанной даты.
Перечень ссылок
- Резников А.Н. Абразивная и алмазная обработка материалов. Справочник / Под ред. А.Н. Резникова. – М.: Машиностроение, 1977. – 391 с.
- Матюха П.Г. Научные основы стабилизации выходных показателей алмазного шлифования с помощью управляющих воздействий на рабочую поверхность круга: Автореф. дис.... докт. техн. наук: 05.03.01 / Матюха Пётр Григорьевич, Харьк. госуд. политехн. ун-т. – Харьков, 1996. – 48 с.
- Полтавец В.В. Обоснование режимов шлифования труднообрабатываемых материалов при электроэрозионном воздействии на рабочую поверхность круга: Автореф. дис…. канд. техн. наук: 05.03.01 / Полтавец Валерий Васильевич, Донецк. национальн. техн. ун-т. – Донецк, 2001. – 19 с.
- Матюха П.Г. Определение режимов плоского шлифования твердых сплавов с использованием нового критерия о текущей лимитированной режущей способности круга/ П.Г. Матюха, В.Б. Стрелков, В.В. Полтавец // Сверхтвердые материалы. Научно-теоретич. журнал. – Киев: 2004. – № 3. – С. 67-73.
- Матюха П.Г. Определение оптимальных режимов при алмазном шлифовании твердых сплавов по упругой схеме с периодическими электроэрозионными воздействиями на рабочую поверхность круга / П.Г. Матюха, В.Б. Стрелков // Сучасні технології в машинобудуванні. Зб. Наукових статей/ Уклад. А.І. Грабченко: За заг. ред. А.І. Грабченка. – Харків: НТУ „ХПІ”, 2007. – С. 330-332.
- Матюха П.Г. Узагальнені режими процесу шліфування, які забезпечують стабільні показники якості / П.Г. Матюха, В.В. Полтавець // Наукові праці Донецького національного технічного університету. Серія: «Машинобудування і машинознавство». Випуск 7 (166). – Донецьк: ДВНЗ «ДонНТУ», 2010. – С.35-49.
- Матюха П.Г. Определение оптимальных режимов шлифования с электроэрозионными управляющими воздействиями на рабочую поверхность круга/ Физические и компьютерные технологии в народном хозяйстве. / П.Г. Матюха, В.В. Полтавец // Труды 8-й международной научн.-техн. конф. 9-10 декабря 2003 г. – Харьков: ХНПК “ФЭД”, 2003. – С. 151-155.
- Матюха П. Режущая способность рабочей поверхности круга как ограничивающий параметр производительности шлифования / Петр Матюха, Валерий Полтавець // Надежность инструмента и оптимизация технологических систем. Сб. научных трудов. – 2003. – вып. 13, – с. 159-164.
- Корчак С.Н. Производительность процесса шлифования стальных деталей / Корчак С.Н. – М.: Машиностроение, 1974. – 280с.
- Патент України №91235 С2 МПК В24В47/00 Пристрій для круглого шліфування / Матюха П.Г., Полтавець В.В., Жулін І.С., Габітов В.В. Заявка а200803398 від 17.03.2008. Опубл. 12.07.2010 бюл. №13, 2010 р.
- Патент України №94813 С2 МПК В24В41/00 Шліфувальна бабка / Матюха П.Г., Габітов В.В., Войтов М.С., Благодарний А.О. Заявка а200911849 от 19.11.2009. Опубл. 10.06.2011 бюл. №11, 2011 р.
- Заявка а201012927 Україна, МПК В24В41/00. Навантажувальний пристрій для шліфування / Матюха П.Г., Габітов В.В., Благодарний А.О. заяв. 01.11.2010.
- Машиностроение. Энциклопедия в 40 томах. Том 4-7. Металлорежущие станки и деревообрабатывающее оборудование. М.: - Машиностроение. 2002. – 864 с.
- Орликов М.Л. Динамика станков / М.Л. Орликов – 2-е изд.,перераб. и доп.- К.: Выща шк.. Головное издательство,1989, - 272с.