Аннотация. Cпециальные марки нержавеющих, жаропрочных и высокопрочных сталей и сплавов, которые широко распространены в деталях и узлах современных машин, имеют низкую обрабатываемость резанием, что обуславливает высокую трудоемкость и высокую себестоимость их изготовления. Поэтому актуальными являются исследования возможностей повышения производительности и снижения себестоимости обработки вышеуказанных материалов за счет применения различных смазочно-охлаждающих технологических сред (СОТС).
Высокие температуры в зоне резания, которые возникают ввиду низкой теплопроводности труднообрабатываемых материалов, указывают на необходимость исследования температурных ограничений в зоне обработки. Для этих видов материалов актуально дальнейшее развитие методики определения температур в зоне обработки при использовании СОТС и учета их влияния на выбор оптимальных режимов резания.
Ключевые слова: смазочно-охлаждающая технологическая среда, оптимизация, высокопрочная сталь, оптимальные режимы.
1. Введение.
Cпециальные марки нержавеющих, жаропрочных и высокопрочных сталей и сплавов, которые широко распространены в деталях и узлах современных машин, имеют низкую обрабатываемость резанием, что обуславливает высокую трудоемкость и высокую себестоимость их изготовления. Поэтому исследования возможностей повышения производительности и снижения себестоимости обработки этих материалов важны. Способом решения этой проблемы является применение оптимальных режимов резания для определенных условий обработки и правильный подбор СОТС. Высокие температуры в зоне резания указывают на необходимость учитывать температурные ограничение режимов резания при их оптимизации. Правильное применение СОТС позволяет существенно изменить характер и величину теплового потока и температуры в зоне обработки.
Способом повышения производительности обработки является оптимизация скорости резания и подачи по критерию максимальной производительности посредством метода линейного программирования [1]. Существующие рекомендации по оптимизации режимов обработки, обычно не учитывают особенности обработки труднообрабатываемых материалов. Также имеются ограниченные сведения о влиянии СОТС на режимы резания [2].
Цель представленной работы – установить влияние основных функциональных свойств СОТС на температуру резания и оптимальные по производительности режимы резания при точении изделий из труднообрабатываемых материалов, а также оценить возможность повышения производительности их обработки.
2. Основное содержание и результаты работы.
Температура лезвия инструмента формируется под воздействием тепловых потоков q1 и q2, которые возникают в зоне обработки (резания) вследствие деформации qд, образования стружки, трения на площадках контакта между образующейся стружкой и передней поверхностью режущей пластины qТП и трения между задней поверхностью режущей пластины и деталью qТЗ (Рис.1.)
Рис. 1. Схема распределения тепловых потоков и расположения источников теплоты
в зоне обработки (резания) с использованием СОТС
Ось X в рассматриваемой системе координат ориентируется в направлении передней поверхности перпендикулярно главной режущей кромке; l – длина контактной площадки в направлении схода стружки; h – износ по задней поверхности; а – ширина среза, а1 – толщина стружки; – угол сдвига.
С учетом действия потока теплоты qо средние температуры на передней и задней поверхностях режущей пластины определяются следующим образом [3]:
где q1 и q2 – тепловые потоки, формирующиеся в режущем лезвии инструмента вследствие образования стружки, трение на площадках контакта между стружкой и передней поверхностью режущей пластины bxl (b – ширина среза) и трения между задней поверхностью режущей пластины и обрабатываемой поверхностью заготовки bxh; и – коэффициент теплопроводности инструмента; M1, M2, N1, N2 – безразмерные функции, которые определяют нагрев площадок на передней и задней поверхностях режущей пластины инструмента; Mо, Nо – безразмерные функции, определяющие охлаждение площадки на передней поверхности под действием СОТС.
Безразмерные функции, определяющие нагрев пластины:
где η – безразмерная величина толщины среза: η1 = b/l, η2 = b/h (η1,2>1); β = 90° - γ - α – угол при вершине; b = t/sinφ – толщина среза; t – глубина резания, φ – главный угол в плане; В1,2(h/l) – специальные функции: В1(h/l) = 2,85 - 0,9(h/l), В2(l/ h) = 2(l/ h)0,54 при β = 90°.
Безразмерные функции, определяющие охлаждение площадок на передней поверхности инструмента под действием СОТС.
При способе подачи СОТС свободным поливом со стороны передней поверхности образуется сток теплоты с равномерным по площадке lо1xlо1 распределением плотностей тепловыделения qо1. В соответствии с законом Ньютона-Рихмана, который описывает процесс конвективного теплообмена при использования СОТС:
где aо – коэффициент теплоотдачи на поверхности контакта инструмента с СОТС; Qср – средняя температура на этой поверхности.
Для расчета коэффициента теплоотдачи при способе подачи СОТС в зону обработки свободным поливом, используется уравнение [3]:
где λо, ωо – коэффициенты теплопроводности и температуропроводности среды; С, m, n, x, y, z – коэффициент и показатели степеней, зависящие от способа подачи среды в зону обработки; lо – характерный размер: lо = BH/2(B+H); В – ширина, Н – высота державки резца; w – средняя скорость потока; n – коэффициент кинематической вязкости среды.
В связи с тем, что температура поверхностей инструмента превышает 100оС, при определении коэффициента теплоотдачи необходимо учитывать изменение агрегатного состояния жидкости. Коэффициент теплоотдачи в кипящую жидкость αк:
при
Движение жидкости относительно инструмента вносит изменения в процесс кипения. Поэтому используется приведенный коэффициент теплоотдачи aпр, учитывающий совместное влияние кипения и конвективного теплообмена:
при
где αк и αо – независимо рассчитанные коэффициенты теплоотдачи при кипении и при конвективном теплообмене соответственно.
Для определения плотности тепловыделения qо необходимо использовать значение средней температуры Θср поверхности контакта инструмента с СОТС, которое заранее неизвестно. Для ее определения принимаем: Θср = moΘ1; mo = ρ-0,86, ρ = 2lo/(b+l) – безразмерный параметр, соотносящий размеры зоны охлаждения с размерами контактной площадки стружки с режущей пластиной инструмента: Θ1 – средняя температура на передней поверхности режущей пластины инструмента. Тогда плотность тепловыделения равна:
Плотности тепловых потоков на передней q1 и задней q2 поверхностях режущей пластины инструмента в случае подачи СОЖ свободным поливом:
где
λд, λи, ωд, ωи – коэффициенты теплопроводности и температуропроводности материалов детали и инструмента соответственно; k – коэффициент усадки стружки; V – скорость резания; с – коэффициент, учитывающий подогрев слоев металла стружки за один оборот детали; Тд – безразмерная функция, которая учитывает распределение температур в заготовки, вызванное тепловой деформацией; b' – коэффициент относительного количества теплоты, которое уходит в стружку; Кс1 – коэффициент, который учитывает закон распределения плотности теплового потока на передней поверхности (для всех случаев Кс1 = 0,77); Кс2 – коэффициент, который учитывает закон распределения плотности теплового потока на задней поверхности (для нормального закона Кс2 = 0,55).
Графики зависимости плотности тепловых потоков на передней q1 и задней q2 поверхностях режущей пластины от износа по задней поверхности h при обработке без СОТС и с применением СОТС показаны на рис. 2.
Рис. 2. Графики зависимости плотности тепловых потоков на передней q1 и задней q2 поверхностях режущей пластины
от износа по задней поверхности h
при обработке без СОТС и с применением СОТс
Учитывая действие потока теплоты с использованием СОТС, средние температуры на передней Θ1 и задней Θ2 поверхностях режущей пластины могут быть определены:
В случае отказа от использования СОТС (α0 = 0) температуры на передней Θ1 и задней Θ2 поверхностях режущей пластины могут быть определены по тоем же формулам, с учетом того, что р1 = 1, р2 = 0.
Температура резания представляет собой среднюю температуру на передней и задней поверхностях режущей пластины
Графики зависимости температуры резания от скорости резания при обработке различных обрабатываемых материалов без применения СОТС представлены на рис. 3.
Рис. 3. Графики зависимости температуры резания Θ от скорости V при обработке различных материалов без СОТС
Изучив зависимости температуры резания Θ от скорости резания V и подачи S при обработке стали Х18Н9Т с использованием различных СОТС установлены следующие степенные зависимости (погрешность не превышает 5%).
При обработке без СОТС :
При обработке с использованием в качестве СОТС эмульсола Э-2:
При обработке с использованием в качестве СОТС эмульсола НГЛ-205:
При обработке с использованием в качестве СОТС эмульсола СДМ, у:
Зависимость скорости резания V от температуры резания Θ при обработке нержавеющей стали Х18Н9Т твердосплавным инстументальным материалом ВК с различными СОТС представлены на рис. 4. (износ по задней поверхности h = 0,2мм). Рассчитанное для этих условий значение приведенного коэффициента теплоотдачи αпр = 40 кВт/м2⋅°С.
Проверка адекватности установленных зависимостей выполнена путем сравнения теоретических зависимостей с результатами экспериентов, представленных в [2].
Результаты сравнения, приведенные на рис. 4, свидетельствуют о том, что с погрешностью, не превышающей 10%, теоретическая зависимость температуры резания Θтеор от скорости резания V при обработке без СОТС подтверждается экспериментальной Θэсп как по уровню температур, так и по характеру зависимостей.
Результаты экспериментальных исследований температур в зависимости от скорости резания V для различных СОТС представлены на рис.4 заштрихованой зоной, также достаточно хорошо совпадающей с расчетными зависимостями.
Рис.4. Графики зависимости температуры резания от скорости при обработке стали Х18Н9Т с различными СОТС
Для оценки эффективности действия СОТС вводится коэффициент снижения температуры резания:
Графики зависимостей коэффициента снижения температуры Ко резания от скорости V для различных СОТС представлены на рис. 6.
Рис.5. Графики зависимости коэффициента снижения температуры резания Ko от скорости V при обработке стали Х18Н9Т с различными СОТС
Снижение температуры резания ΘСОЖ1 с использованием в качестве СОТС эмульсола Э-2 достигается в основном за счет охлаждающего эффекта СОТС. При использовании эмульсола НГЛ-2О5, состоящего из масляного раствора сульфоната натрия и пассивирующих добавок водорастворимых ингибиторов коррозии – нитрита натрия и тринатрийфосфата, к охлаждающему эффекту добавляется эффект смазывающий, что усиливает снижение температуры ΘСОЖ2. Наибольший эффект снижения температуры ΘСОЖ3 наблюдается при использовании эмульсола СДМ,у, представляющего собой безводную систему содержащую масло, сульфонат натрия, водорастворимые ингибиторы коррозии и небольшое количество (до 3 %) дисульфида молибдена (в качестве противоизносной присадки), прошедшего ультразвуковую обработку. Наличие дисульфида молибдена существенно повышает смазывающее действие СОТС, что и обеспечивает максимальное снижение температуры резания.
Полученные коэффициенты используются для учета действия различных СОТС в температурных ограничениях при дальнейшей оптимизации режимов резания.
В качестве целевой функции при оптимизации режимов резания мы принимаем производительность обработки, максимум которой достигается при минимуме основного времени, или максимуме произведения n⋅s → max. В настоящей работе рассматриваются следующие основные ограничения режимов резания при ообработке труднообрабатываемых материалов [4]:
- По возможностям режущего инструмента, которые обусловлены скоростью резания, которая, в свою очередь, соответствует его стойкости:
где D – диаметр обработки, CV, KV – коэффициенты и xv, yv, mv – показатели, которые характеризуют степень влияния глубины t, подачи s и стойкости T на скорость резания v, определяемые в зависимости от условий эксплуатации; n – частота вращения;
- По предельно допустимой температуре резания:
где Сt – постоянный коэффициент, zt, yt, xt – показатели степени, характеризующие влияние на температуру скорости резания, подачи и глубины резания.
- По прочности пластины резца:
где с – толщина пластины; φ – главный угол резца в плане; CР, KР – коэффициенты и xр, yр, – показатели, которые характеризуют степень влияния глубины и подачи на силу резания Рz, котрые определются в зависимости от условий эксплуатации. Кφ=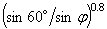
В результате линеаризации целевой функции и ограничений путем логарифмирования определена математическая модель процесса резания, выраженная системой линейных неравенств (X1 = ln n; X2 = ln s), графически представленных на рис. 6.
Определения оптимальных режимов резания выполняется для черновой токарной обработки вала (глубина резания t = 2мм) диаметром D = 100мм, длиной L = 200мм из стали Х18Н9Т (прочность σв = 600Мпа). Обработка осуществляется сборными резцами с механическим креплением твердосплавных пластин ВК8, принятая стойкость Т = 30мин, допустимый износ по задней поверхности h = 0,2мм. При обработке с СОЖ используется эмульсол СДМ,у.
Рис. 6. Схема определения оптимальных режимов резания при токарной обработке стали Х18Н9Т с применением СОТС
Для заданных условий обработки принятые следующие коэффициенты и показатели, характеризующие степень влияния глубины резания, подачи и стойкости на скорость резания [2]: CV =150; xv = 0,15; yv = 0,45; m = 0,25; KV = 1,2;
- коэффициенты и показатели, характеризующие степень влияния глубины, подачи и скорости на силу резания [2]: CР = 3400; xр = 0,95; yр = 0,75; nр = -0,15; KР = 0,8;
Были определенны следующие значения параметров bі:
- при обработке без СОТС: b1 = 5,214; b2 = 3,527; b3 = -0,092; b4 = -2,996; b5 = 1,03; b6 = 2,536; b7 = 7,601.
- при обработке с СОТС: b1 = 5,397; b2 = 4,073; b3 = 1,765; b4 = -2,996; b5 = 1,03; b6 = 2,536; b7 = 7,601.
Область АВСDЕ представляет собой область возможных решений при обработке без СОТС, область АВоDоЕо - при обработке с СОТС. Целевая функция принимает максимальное значение в точке D, для которой сумма расстояний до осей (X1+X2) максимальна. Координаты точек D (X1опт, X2опт) и Dо(X1опт, X2опт) являются оптимальными значениями параметров, на основании которых определяются оптимальные частота вращения и подача. Точка D является точкой пересечения ограничений по предельно допустимой температуре резания (2) и ограничения по прочности пластины режущего инструмента (3). За счет использования СОТС температурное ограничение (2) снимается, точка Dо является точкой пересечения ограничений по режущим возможностям инструмента (1) и ограничения по прочности пластины режущего инструмента (3), вследствие чего оптимальные значения подачи, а также скорости резания возрастают, что приводит к повышению производительности обработки.
Для заданных условий при точении стали Х18Н9Т определены следующие оптимальные режимы:
- при обработке без СОТС: скорость Vо= 62 м/мин, подача Sо= 0,65мм/об;
- при обработке с СОТС: скорость Vо= 73 м/мин, подача Sо = 0,8мм/об.
Графики зависимости подачи от глубины резания и скорости резания от стойкости инструмента для различных обрабатываемых материалов представлены на рис. 7.
Рис. 7. Графики зависимости функции от глубины резания
a) и скорости резания от стойкости Т, b) для различных обрабатываемых материалов
Графики зависимости подачи от скорости резания при обработке стали Х18Н9Т с использованием СОТС и без использования СОТС представлены на рис. 8.
Рис.8. Графики зависимости подачи от скорости резания при обработке с использованием СОТС и без использования СОТС
Оптимальные режимы резания - подача и скорость резания могут быть определены аналитически:
Полученные аналитические выражения позволяют рассчитывать оптимальные режимы резания при обработке труднообрабатываемых материалов для любых условий обработки. На их основании может быть определен коэффициент повышения производительности обработки труднообрабатываемых материалов при использовании СОТС:
Графики изменения коэффициента повышения производительности КП при точении стали Х18Н9Т с применением различных СОТС в зависимости от глубины резания и стойкости, которые представлены на рис. 9, свидетельствуют о том, что с их увеличением производительность обработки снижается.
На основании представленного коэффициента повышения производительности обработки может быть выполнена оценка эффективности применения различных СОТС.
Рис. 9. Графики изменения коэффициента роста производительности КП при токарной обработке стали Х18Н9Т
с применением различных СОТС в зависимости от глубины резания – а) и стойкости – b)
Выводы
Выполнена оценка возможности снижения температуры в зоне резания при обработке труднообрабатываемых материалов с применением различных СОТС. Установлено влияние СОЖ на оптимальные режимы резания, обеспечивающие максимальную производительность обработки.
Полученные аналитические выражения для расчета оптимальных режимов резания обеспечивают возможность количественной оценки повышения производительности обработки изделий из труднообрабатываемых материалов при использовании различных СОТС.
Разработанная методика быть использована для оптимизации режимов резания при различных видах обработки с применением СОТС.
Ссылки
- Старков В.К. Обработка резанием. Управление стабильностью и качеством в автоматизированном производстве. – М.: Машиностроение. 1989. – 296 с.
- Гуревич В.Я. Режимы резания труднообрабатываемых материалов. – М.: Машиностроение, 1986. – 240 с.
- Резников А.Н., Резников Л.А. Тепловые процессы в технологических системах. – М.: Машиностроение, 1990. – 288 с.