Реферат по теме магистерской работы
Содержание
- Введение
- 1. Актуальность темы
- 2. Цель и задачи магистерской работы
- 3. Научная новизна
- 4. Анализ существующих решений и разработок
- Выводы
- Список источников
Введение
Очистной забой является основным технологическим процессом угольного предприятия. От его ритмичной работы зависит экономические показатели шахты.
Выемка угля осуществляется с помощью комбайнов, стругов и гидромониторов. Доставка угля по забою осуществляется с помощью скребкового конвейера. Поддержание выработки осуществляется с помощью механизированных крепей.
Автоматизация горного производства позволяет заменить функцию человека по управлению, регулированию и контролю технологического производства с помощью специальных устройств.
Автоматически действующее устройство работает более надежно, исключает ошибки персонала, а главное, при сокращении количества работников, которые непосредственно принимают участие в производстве, обеспечивают рост производительности труда, а освобожденная рабочая сила используется на другом рабочем месте. Эксплуатация забойных машин, комплексов и агрегатов связанная со значительными трудностями, обусловленными горно-технологическими условиями, пылегазовым режимом шахты, ее микроклиматом и вторыми факторами.
1. Актуальность темы
В настоящее время комбайновой выемкой обеспечивается 65–70 процентов добычи угля. Изменяющиеся в широких пределах залегание и физико-механические свойства углей, мощность пласта, условия крепления и транспортирования, наличие различного рода нарушений, особенности технологии ведения работ, особенно в высоконагруженных лавах, практически непрерывно изменяют режим работы комбайна. Причем возникает необходимость одновременно выполнять несколько операций, например управлять скоростью подачи и раздвижкой режущих органов. К тому же зона выемки угля является одним из наиболее опасных участков лавы. Поэтому проблеме автоматизации забойного оборудования уделяется большое внимание. Современные горные машины не оборудованы устройством для плавного изменения скорости резания, поэтому регулирование работы двигателя производится при помощи авторегуляторов, поддерживающих заданную нагрузку двигателей путем изменения только скорости подачи [1]. Известны многочисленные исследования и разработки по созданию датчиков открытой границы «порода-уголь» с использованием перечисленных характеристик.
2. Цель и задачи магистерской работы
Целью работы является повышение срока службы электромеханического оборудования за счет создания системы автоматизированного управления комбайном по границе порода-уголь.
Для создания данной системы необходимо решить ряд задач, а именно:
3. Научная новизна
Анализ литературных источников по существующим системам автоматизации процесса добычи угля показал, что основными недостатками данных систем являются быстрое изнашивание исполнительного органа (бурильной коронки) и высокая нагрузка на двигатель при резком переходе бурения на более крепкую породу [2].
Вмещающие породы разрабатываемых угольных пластов имеют среднюю устойчивость. Преобладающими боковыми породами угольных пластов являются глинистые сланцы. В отдельных района бассейна в связи с изменением литологического состава пород, слагающих отдельные свиты, преобладающими боковыми породами являются песчаники и песчаные сланцы, значительно реже известняки. Механическая прочность горных пород крайне неравномерна и колеблется в широких пределах [3].
Угли Донецкого бассейна относятся к гумусовым. Сапроелитовые разности углей встречаются только в виде отдельных линз и угольных прослоев. Угли пластов, залегающих в отложениях среднего и верхнего карбона, обладают почти одинаковым материнским растительным веществом, но имеют различные качественные показатели, что объясняется в основном их различной степенью углефикации, различной степенью восстановления и окисления в процессе их формирования, а также неодинаковой зольностью и сернистостью. Содержание фосфора в угле весьма незначительно. Выход летучих веществ колеблется в широких пределах – от 2 % (антрациты) до 50 % (длиннопламенные угли). Теплота сгорания углей находится в пределах от 7500 до 8750 ккал/кг. Наиболее чистые и малосернистые угли имеются в западном секторе Большого Донбасса (Южный и Западный Донбасс) и относятся к отложениям нижнего карбона. В Донбассе установлено закономерное изменение содержания летучих веществ в углях с уменьшением их содержания в направлении с северо-запада на юго-восток и от стратиграфически вышележащих к нижележащим. Зольность и содержание серы в углях колеблются в широких пределах. Среднее содержание природной золы в большинстве угольных пластов находится в пределах 7–20 %. Малозольных углей с зольностью до 7–8 % в бассейне немного. В Донбассе преобладают угли среднесернистые (1,5–3 %). Угли Донецкого бассейна в основном имеют лёгкую и среднюю обогатимость.
В Донецком каменноугольном бассейне распространены все основные марки каменных углей: длиннопламенные (Д), газовые (Г), жирные (Ж), коксовые (К), отощённые спекающиеся (ОС), тощие (Т), полуантрациты (ПА) и антрациты (А), а также переходные от бурых углей к длиннопламенным. Петрографический состав углей довольно однороден [4].
Сопротивляемость угля резанию в призабойной части пласта Апр, кН/см, определяется из выражения
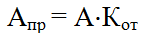
где Кот – коэффициент отжима, учитывающий снижение сопротивляемо-сти угля резанию в зоне отжима по сравнению с сопротивляемостью резанию неотжатого массива угля;
А – сопротивляемость угля резанию в неотжатом массиве, кН/см.
Средняя сопротивляемость угля резанию в зоне отжима Аот, кН/см, определяется из эмпирического выражения

где L – ширина призабойного пространства, м;
Р – сопротивляемость (жесткость) крепи в лаве, МПа.
Скорость подачи Vп определяется по следующей зависимости:

где Vп.пр – скорость подачи комбайна, рассчитанная по установленной мощности привода при известных величинах сопротивляемости угля резанию Aр и мощности пласта m, м/мин;
Vп.тяг – скорость подачи комбайна по тяговому усилию, м/мин;
kв.п – коэффициент увеличения скорости подачи комбайна в зависимости от марки углей, поэтому при вязких углях kв.п = 1,002; при хрупких углях kв.п = 1,15; при весьма хрупких углях kв.п = 1,303.
К вязким углям относятся:
Определенная по формуле скорость подачи Vп при разработке тонких и весьма тонких пластов проверяется по скорости задвижки конвейера в лаве при управлении работой комбайна (Vм).
При 0,8 ≤ m < 1,1 м Vк = 1,7–2,3 м/мин.
При 1,1 ≤ m < 1,3 м Vк = 2,3–4,5 м/мин.
Для конкретного забоя скорость подачи комбайна следует определять по фактической сопротивляемости пласта резанию в зоне работы исполнительного органа Aр.ф.. Также можно использовать данные о сопротивляемости резания пласта в массиве, скорректированные по фактической мощности и ширине захвата комбайна (так называемый коэффициент отжима kот)
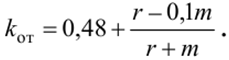
Тогда

Fп – составляющая силы резания в направлении подачи комбайна, кН;
Fт – тяговое усилие подающей части комбайна, кН;
G – вес комбайна, кН;
α – угол падения пласта при работе по простиранию, град. При работе лавами по падению или восстанию принимается равным нулю.
Интерполяция Vп.пр по сопротивляемости пласта резанию производится по зависимости
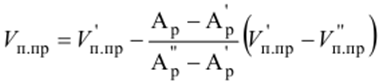
Составляющая силы резания в направлении подачи комбайна при конкретном значении сопротивляемости пласта резанию находится путем интерполяции из выражения
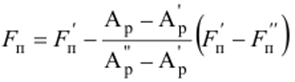
Fп' и Fп" – составляющие силы резания в направлении подачи комбайна, соответствующие Aр' и Aр", кН [5].
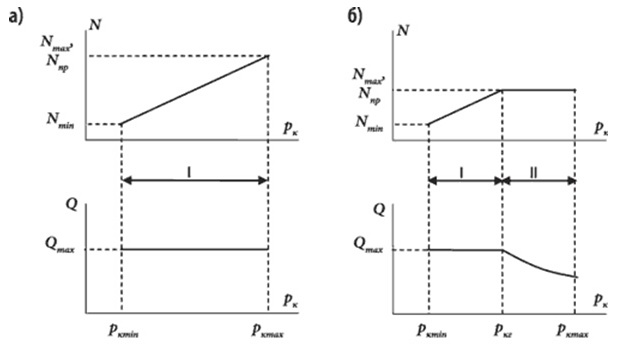
Рисунок 1 – Зависимости мощности резания и теоретической производительности комбайна от контактной прочности разрушаемой породы при отсутствии регулирования (а), плавном (б) регулировании нагрузки [6]
Процесс добычи угля очистным комбайном представлен на рисунке 2.
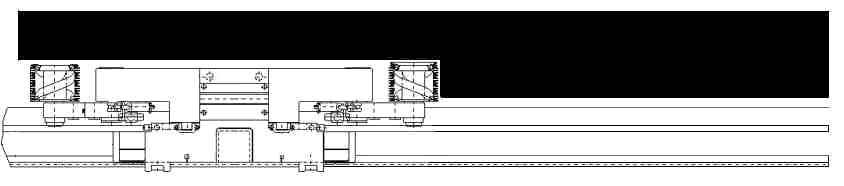
Рисунок
2 – Процесс
добычи угля очистным комбайном
(анимация: 9 кадров, 5
циклов повторения, 115 килобайт)
На практике фактически скорость передвижения определяется следующими факторами: скоростью задвижки конвейера, скоростью воздуха, параметрами крепи [7].
Существующие системы управления не позволяют одновременно управлять скоростями резания и подачи.
Ранее уже были попытки создания подобных систем, работа которых основывалась на величинах, получаемых различными датчиками порода-уголь. Однако применение радиоизотопного датчика не безопасно для обслуживающего персонала, а тензометрический датчик, который закрепляется непосредственно на исполнительном органе, имеет низкую долговечность. Из рассмотренных предложений вытекает необходимость создания системы управления, построенной на следующих принципах:
4. Анализ существующих решений и разработок
Замкнутым циклом автоматизации обладают автоматические регуляторы нагрузки, работающие по программе, заранее установленной человеком. Такая система автоматического регулирования (САР) нагрузки двигателя комбайна может иметь три варианта с изменением: скорости подачи; резания; подачи и резания. Из теории работы механизмов известно, что для поддержания постоянной нагрузки на двигатель и обеспечения максимальной производительности машины (комбайна) необходим выбор оптимальных значений скорости подачи и скорости резания в зависимости от крепости угля. При этих условиях также должна производиться автоматическая корректировка на снижение тока нагрузки в зависимости от температурного режима двигателя, так как двигатели горных комбайнов работают на переходной мощности (часовая – длительная). Такой регулятор САР требует создания современного тиристорного регулируемого привода для комбайнов, где оптимальные параметры работы будут обеспечиваться вычислительной машиной, выполненной с регулятором. В настоящее время на основе первого варианта регулирования Макеевским заводом шахтной автоматики выпускается регулятор нагрузки УРАН, который обеспечивает:
Функциональная схема регулятора УРАН представлена на рисунке 3.
Регулятор имеет два канала: скорости и нагрузки, которые совместно работают на устройства выхода, К каналу скорости относятся: датчик скорости ДС, программа скорости ПС, блок контроля скорости БКС и блок выходных устройств. К каналу нагрузки относятся: датчик тока ДТ, программа тока ПТ и импульсное устройство ИУ. В блоке канала скорости производится сравнение двух напряжений: датчика скорости и программы скорости, которые пропорциональны скорости подачи UП и установки скорости программы UУ. В случае разности между ними вырабатывается сигнал на включение электрогидрораспределителя ЭГР по уменьшению или увеличению скорости подачи.
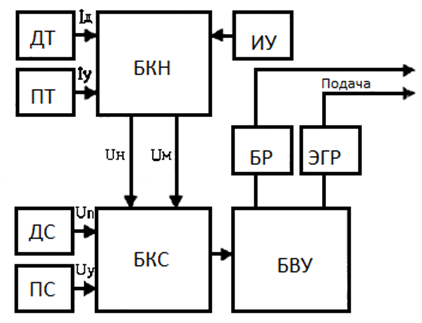
Рисунок 3 – Функциональная схема регулятора УРАН
В блоке канала нагрузки сравниваются напряжение пропорциональное фактическому току двигателя Iд и напряжение программы токовой уставки, пропорциональное уставке Iу. При разности этих значений пределах ± 5 % Iу регулятор по каналу нагрузки не работает (зона нечувствительности). При разности значения в пределах 5-25 % больше Iу из блока БКН в блок БКС выдается напряжение Uн на импульсное уменьшение скорости подачи до значения установления тока Iд в . пределах ±5 % Iу. Если рассогласование тока Iд больше 25 % тока Iу, то блок БКН выдает непрерывный сигнал на уменьшение скорости подачи. При недогрузе двигателя комбайна, т.е. когда Iу >> Iд, блоком БКН выдается напряжение Uм на увеличение скорости подачи до значения установленного программой скорости ПС. В случае применения в комплексе с комбайном предохранительной лебедки ее управление осуществляется блоком реле БР. При пуске комбайна в блоке БКС работает реле временя, которое выдает сигнал да установку нулевой скорости подачи, а через 2–3 с осуществляет процесс на нормальное её регулирование. В регулятор УРАН входят устройства: электронный блок, датчик скорости, датчик тока, панель индикации, источник питания и пульт управления. В комплексе с регулятором УРАН устанавливается аппарат контроля работы электродвигателей КОРД, который обеспечивает защиту при технологических перегрузках, опрокидывании и обрыве одной из фаз.
Аппаратура ИПИР-3М это импульсный пропорционально-интегральный регулятор нагрузки на приводе выемочной машины. Она выпускается серийно в аналоговом варианте. Структура этого устройства представлена на рисунке 4.
Регулятор ИПИР-3М импульсного типа. Как и аппаратура САДУ-2 он содержит два контура управления. Один из них является контуром управления по мощности двигателя, другой по скорости подачи машины на забой. Как и в предыдущем случае, первый контур имеет наибольший приоритет.
Задающий и фактический сигналы по нагрузке двигателя подаются на элемент сравнения критического и заданного тока нагрузки двигателя сигнал с элемента сравнения С1, который формирует два выходных сигнала импульсного типа. Первый импульсный сигнал появляется в том случае, если ток нагрузки двигателя будет превышать заданное значение. Этот сигнал подается на первый широтно-импульсный преобразователь ШИМ1, который преобразует сигнал положительного рассогласования в широтно-модулированный импульсный сигнал. Ширина импульса этого преобразователя пропорциональна величине положительного рассогласования между заданным и фактическим током нагрузки. Сигнал с ШИМ1 через логические элементы И-НЕ и релейный элемент (ключ К1), импульсно подается на логический ключ И второго контура управления. При отрицательном рассогласовании фактического и заданного тока нагрузки двигателя сигнал с элемента сравнения С1 подается на ШИМ2 , работающего по такому же принципу как и ШИМ1. Выходной сигнал этого модулятора импульсно включает релейный ключ А4, который через блок логики управляет исполнительными электромагнитами.
Контур регулирования скорости подачи содержит элемент сравнения С2, предназначенный для сравнения заданной и фактической скорости подачи комбайна. Причем сигнал от задающего устройства поступает через логический ключ И, на который одновременно подается с ключа К1 импульсный сигнал положительного рассогласования токовой нагрузки двигателя. Вторым входным сигналом элемента сравнения С2 является сигнал с датчика скорости ДС. Сигнал этого датчика включает одновременно релейный ключ К4, который регистрирует направление перемещения выемочной машины.
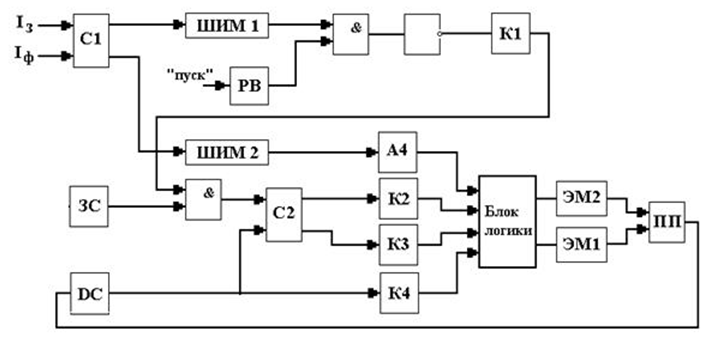
Рисунок 4 – Структурная схема аппаратуры ИПИР-3М
Принцип управления, заложенный в аппаратуре ИПИР-3М, может быть реализован в микропроцессорном варианте. Так как контур регулирования нагрузкой двигателя является приоритетным, то в начале этого цикла фактическая нагрузка двигателя сравнивается с заданной ее величиной, которая считывается из памяти микроконтроллера. Если фактическая нагрузка не будет превышать заданной, то происходит переход к оператору проверки равенства фактической и заданной скоростей подачи комбайна. В случае выполнения этого условия происходит возврат на начало этого цикла (к опросу датчиков), в противном случае производится проверка условия неравенства этих скоростей. При этом, если фактическая скорость подачи комбайна не будет превышать заданную, то включается режим импульсного увеличения этой скорости, до тех пор пока заданная скорость не сравняется с фактической [8].
Работа данных регуляторов основана на измерении тока в обмотках приводного двигателя и обеспечивает номинальную нагрузку, изменяя обороты двигателя. При этом происходит быстрое изнашивание исполнительного органа, а также становится невозможным управление комбайном по гипсометрии пласта. Применение других датчиков порода-уголь не дает желаемого положительного эффекта, так как они не охватывают значительную часть диапазона сочетаний разнообразных по характеристикам вмещающих пород и углей. Невозможно использование датчиков при значительной нарушенности пластов переходными мелкоамплитудными нарушениями. Отрицательное влияние на работу большей части датчиков порода-уголь оказывают обводненность и предварительное увлажнение угольных пластов, а также отсутствие четкой границы между углем и породой [9].
Вместе с тем проблема определения и контроля границы «порода-уголь» может быть решена устройством, структурная схема которого приведена на рисунке 5.

Рисунок 5 – Структурная схема устройства контроля границы «порода-уголь»
Устройство контроля границы «порода-уголь» устанавливается на удалении от рабочего исполнительного органа горной машины, что повышает надежность эксплуатации и увеличивает срок службы чувствительного элемента. Включение измерительного преобразователя по дифференциальной трансформаторной схеме позволяет повысить точность определения контролируемой границы, обеспечивает достоверность получения информации [10]. Работа устройства контроля границы «порода-уголь» заключается в следующем. Усилие воздействия F массива угля (породы) на поверхность режущего органа преобразуется в осевое перемещение L механического чувствительного элемента, что приводит к изменению положения сердечника дифференциального трансформаторного преобразователя, на выходе которого формируется сигнал U, соответствующий воздействию угольного или породного массива. Для приведения выходного сигнала U в стандартное значение Uст используется нормирующий преобразователь.
Структурная схема САУ комбайном представлена на рисунке 6.
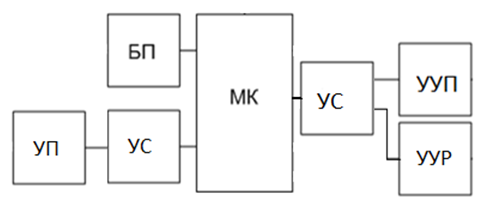
Рисунок 6 – Структурная схема системы автоматизированного управления комбайном
На рисунке 6 приняты следующие условные обозначения: УП – устройство преобразования усилия в изменение напряжения; УС – блок согласования; МК – микроконтроллер; УУП – устройство управления скоростью подачи; БП – блок питания; УУР – устройство управления скоростью резания.
Данная система управления построена на новом устройстве, которое ранее не применялось. Применение данного устройства дает возможность системе быстро реагировать на изменение крепости массива при прохождении границы порода-уголь, оперативно изменяя скорости резания и подачи.
Выводы
Использование системы автоматизированного управления комбайном по гипсометрии пласта, созданной на основе устройства компенсации нагрузки, позволит значительно увеличить срок службы как комбайна (отсутствие сильных нагрузок на двигатель), так и самого исполнительного органа за счет компенсации резкого изменения усилия при переходе работы комбайна на горный массив более высокой крепости.
При написании данного реферата магистерская работа еще не завершена. Дата окончательного завершения – декабрь 2012 года. Полный текст работы и материалы по теме могут быть получены у автора или его руководителя после указанной даты.
Список источников
- Ямщиков В.С. Контроль процессов горного производства: Учебник для вузов. – М.: Недра, 1989, 446 с.
- Горбатов П.А., Петрушкин Г.В., Лысенко Н.М., Павленко С.В., Косарев В.В. Горные машины для подземной добычи угля. / П.А. Горбатов, Г.В. Петрушкин, Н.М. Лысенко, С.В. Павленко, В.В. Косарев – М.: Недра, 1990, 305 с.
- Паффенгольц К.Н. Геологический словарь: в 2-х томах. / К.Н. Паффенгольц – М.: Недра., 1978.
- Горная википедия [Электронный ресурс]. – Режим доступа: http://miningwiki.ru.
- Практикум по курсу «Процессы подземных горных работ» для студентов специальности 7.090301.02 всех форм обучения / под редакцией докт. техн. наук проф. Ярембаша И. Ф., изд. 3-е, дополненное – Донецк: ДонНТУ, 2008, – 118 с.
- Электронная библиотека [Электронный ресурс]. – Режим доступа: http://library.stroit.ru.
- Солод В.И., Гетопанов В.Н., Рачек В.М. Проектирование и конструирование горных машин и комплексов. Учебник для вузов. / В.И. Солод, В.Н. Гетопанов, В.М. Рачек – М., Недра, 1982, 350 с.
- Портал [Электронный ресурс]. – Режим доступа: http://geofut.com.
- Богданов Б.В., Зуев В.С., Гаврилов П.Д., Орлянский В.В. – Системы дистанционного и автоматизированного управления выемочными машинами (патентный обзор) / Б.В. Богданов, В.С. Зуев, П.Д. Гаврилов, В.В. Орлянский – ЦНИЭИуголь, Москва, 1974.
- Шидлович Л.Х. Дифференциальные трансформаторы и их применение. / Л.Х. Шидлович – Энергия, 1966, 96 с.