Реферат за темою випускної роботи
Зміст
- Вступ
- 1. Актуальність теми
- 2. Мета і задачі дослідження та заплановані результати
- 3. Технологічний процес очищення газів як об’єкт автоматизації
- 4. Огляд розробок та досліджень
- 5. Моделювання технологічного процесу
- Висновки
- Перелік посилань
Вступ
На сучасному етапі розвитку економіки Україна загострилися проблеми розвитку виробничого сектора і, зокрема, металургійного виробництва, яке в недавній час становило значну частку ВВП. Причинами цього стали як і застарілі технологічні установки, обладнання та їх низький рівень автоматизації, так і внутрішня політична обстановка в країні. Тому слід всіляко прагнути до зниження собівартості продукції шляхом впровадження нових технологій, збільшення обсягів випущеної продукції, підвищення якості і збільшення рівня автоматизації виробництва, а не шляхом зниження оплати праці та скорочень штату.
Так, у виробництві сталі з застосуванням як застарілих, так і більш нових технологій є перспективним застосування установок позапічної обробки сталі, які дозволяють прискорити технологічний процес шляхом зниження тривалості плавки і підвищити якість сталі. Це незмінно призводить до зниження собівартості продукції.
Для нормального функціонування таких установок необхідна наявність установок газоочистки. Основним робочим елементом таких установок є мішечні фільтри, термін служби яких безпосередньо залежить від температурного режиму системи фільтрації. Підвищені температури призводять до передчасного зносу фільтрів, що призводить до збільшення витрат і накладається на собівартість продукції. Метою даної роботи є створення системи автоматичного контролю температури відведених газів з метою подальшого використання цих даних для створення ефективного режиму роботи системи газоочистки.
1. Актуальність теми
Ні для кого не є таємницею, що екологічна обстановка нашого регіону залишає бажати кращого, а обсяги промислового виробництва поступово зростають. Тому гостро постає необхідність очищення промислових відходів. Однак, будівництво та експлуатація таких установок – дороге задоволення, тому слід підтримувати в належному стані існуючі установки очищення і продовжувати термін їх служби усіма можливими способами.
Дана магістерська робота присвячена дослідженню процесу керування охолодженням відхідних газів системи газоочистки установки «піч-ковш», в якій можливе підвищення температури, що призводить до передчасного виходу з ладу фільтруючих елементів. У зв’язку з цим виникає необхідність дослідження процесу охолодження відпрацьованих газів повітрям, визначення його математичної моделі та отримання якісних характеристик, а також, на основі отриманих даних, автоматизації даного процессу. Метою даної роботи є створення системи автоматичного контролю температури відведених газів з метою подальшого використання цих даних для створення ефективного режиму роботи системи газоочистки.
2. Мета і задачі дослідження та заплановані результати
Метою даної роботи є створення системи автоматичного управління установкою очистки відхідних газів для забезпечення ефективного режиму роботи системи газоочистки.
Основними задачами при розробці даної системи є:
- Розробка математичної моделі процесу розведення димового газу повітрям.
- Підтримка температури у фільтрі на заданому рівні – 110 °С.
- Забезпечення ефективного завантаження установки шляхом своєчасної очистки мішків фільтрів.
- Передача на керуючу ЕОМ поточних значень технологічних параметрів.
- Видача попереджувальної сигналізації про відмову тих чи інших пристроїв або виникненні аварійних ситуацій.
- Самодіагностика системи – автоматичне визначення аварійного вузла.
Об’єкт дослідження: система газоочистки.
Предмет дослідження: процес охолодження димового газу повітрям.
За підсумками виконання даної роботи планується отримання наступних практичних результатів:
- Продовження терміну служби мішків фільтра. Це досягається шляхом швидкого встановлення необхідного значення температури в фільтрах і недопущенням тривалого впливу підвищених температур. Також знос зменшується за рахунок зменшення кількості імпульсів для очищення мішків. Це істотно знижує кількість повстяного матеріалу, який йде на заміну і зменшує витрати на його придбання.
- Усунення мікропоривів мішка дозволяє підвищити якість очищення газів, що важливо, бо збільшення викидів тягне за собою накладення штрафних санкцій на підприємство державними екологічними службами.
- Обмеження нижньої межі температури дозволяє домогтися більш ефективного завантаження установки і виключити перевитрати електроенергії на зайві присоси повітря в систему імпульсної фільтрації.
- Застосування сучасних засобів діагностики справності обладнання дозволяє виявляти і оперативно усувати виникаючі в ході експлуатації несправності, скорочуючи тим самим простої установки.
3. Технологічний процес очищення газів як об’єкт автоматизації
Система газоочистки установки позапічної обробки сталі піч-ковш
призначена для очищення газів, що йдуть з метою зниження кількості шкідливих викидів в атмосферу, а також підтримання сталості внутрішнього інертного середовища в установці піч-ковш
(УПК).
Димовий газ видаляється з під склепіння установки піч-ковш
і по трубопроводу діаметром 1250 мм надходить в систему газоочистки. Перед надходженням сирого газу в фільтр відбувається його змішування зі свіжим повітрям в зсувному зазорі з метою його розведення і охолодження до прийнятної температури впускання в фільтр.
Для того, щоб регулювати кількість газу, є демпфер для регулювання потоку Печі–Ковша. Зазор, призначений для розбавлення відпрацьованих газів повітрям, також має демпфер жалюзійного типу для регулювання припливу свіжого повітря в систему фільтрації.
Після проходження відпрацьованих газів через іскроуловлювач й охолодження його до прийнятної температури шляхом змішування його зі свіжим повітрям відбувається його очищення в фільтрі імпульсної очистки. Даний тип фільтрів призначений для очищення димів з сталеплавильних агрегатів за допомогою мішечних фільтрів, які самі очищаються стисненим повітрям за певним циклом. Конструкція фільтра імпульсної очистки наведена на рисунку 1.
Сирий газ входить у фільтр через отвори в бункерах пилу (5) і проходить в корпус фільтра з нижньої сторони. Шляхом зміни напряму досягається попереднє осадження більш великих часток пилу. Ці більші частки осідають безпосередньо в бункері для пилу під корпусом пилу (1).

Рисунок 1 - Конструкція фільтра з імпульсною очисткою
Відділення газу від часток пилу здійснюється з зовнішньої сторони мішків фільтра 2, які встановлені над корпусом фільтра. Газ проходить мішки фільтра зовні всередину, чистий газ потім проходить через трубку Вентурі (9) в головку фільтра з боку чистого газу (3). Під час фільтрації мішки притискаються до корпусу фільтра.
Блок управління фільтром відкриває мембранні клапани (7) на короткий час (імпульс приблизно на 0,15 секунди), так що стиснуте повітря пульсує (впорскується) в мішки фільтра через складальну трубку (4), сопло складальної трубки (8) і трубки Вентурі. Трубка Вентурі зверху мішків фільтра, збільшує ефект шляхом насасивання додаткового навколишнього повітря з боку чистого газу в мішок фільтру. Очищений повітря, що складається з стисненого повітря і чистого газу, входить всередину мішка фільтра з високою швидкістю. Мішок фільтра розширюється з високою швидкістю, і частинки пилу зовні мішків випадають на поверхні мішка. Імпульс повітря, який входить в мішок фільтру, також діє як повітря продувки, який продувається через мішок фільтру в протилежному напрямку звичайної фільтрації і посилює очищаючий ефект.
Пил, який зчищається з мішків фільтра, падає в бункер для пилу. Пристрій збору пилу утворено одним ланцюговим конвеєром під фільтром і роторним клапаном, за допомогою якого вона видаляється з системи газоочищення на подальшу утилізацію.
Головний вентилятор з’єднаний з виходом фільтра трубопроводом діаметром 1250 мм. Головний вентилятор газоочищення - відцентровий агрегат, який приводиться в рух асинхронним трифазним двигуном з короткозамкненим ротором потужністю 315 кВт. Вентилятор працює на всмоктування, створюючи розрідження в підвідному трубопроводі і фільтрах, забезпечує надходження сирого газу на очистку. Після проходження газом фільтрації, очищений газ надходить через димосос в димову трубу, за допомогою якої і скидається в атмосферу [1].
Автоматизація даного об’єкта здійснюється за допомогою комплексу апаратних і програмних засобів, які об’єднані в загальну систему АСУ ТП Газоочистка
. Дана система є інтегрованою в систему управління установкою піч-ківш
, так як управління газоочисткою знаходиться в тісному взаємозв’язку з управлінням установкою позапічної обробки сталі. У свою чергу, система автоматизації УПК інтегрована в загальну систему АСУ ТП мартенівського цеху.
Управління здійснюється за допомогою за допомогою команд, що вводяться оператором з керуючою ЕОМ РС сталевара. Від засобів відбору інформація надходить безпосередньо на входи програмованого логічного контролера чи до локальних пристроїв управління. Інформація про стан останніх також передається на керуючу ЕОМ з метою моніторингу їх стану. У програмованому логічному контролері відбувається прийом інформації, її обробка і вироблення керуючих впливів згідно закладеному в ньому алгоритму. Деякі з отриманих даних передаються на керуючу ЕОМ, де відбувається їх аналіз, опрацювання та вироблення керуючого впливу згідно з алгоритмами і вказівками оператора.
Основними контрольованими параметрами в цій системі є:
- Дані, про положення демпферів і заслінок. Температури їх приводних двигунів і підшипникових вузлів, а також захист від заклинювання контролюються вбудованими блоками управління. При цьому на екрані монітора РС сталевара відображаються лише дані про положення заслінок, а решта видаються тільки у разі перевищення уставок у вигляді аварійного повідомлення про непрацездатність того чи іншого механізму.
- Температура підшипникових вузлів і двигуна димососа.
- Розрідження в фільтрі, яке регулюється шляхом зміни положення заслінок газоходу.
- Різниця тисків у фільтрах з боку забрудненого і очищеного газів для визначення ступеня засміченості фільтра.
- Температура газу на вході в трубопровід газоочищення і в фільтрі.
Технологія очищення газів, що йдуть безперервно пов’язана з технологією обробки стали установки піч-ківш
. Регулювання деяких параметрів системи газоочищення, таких як положення димового демпфера УПК, здійснюється за параметрами технологічного процесу доведення сталі. У зв’язку з цим виникає необхідність інтеграції системи автоматизації газоочищення з системою управління установкою піч-ківш
. Загальний вигляд системи управління установкою піч-ківш
наведено на рисунку 2.
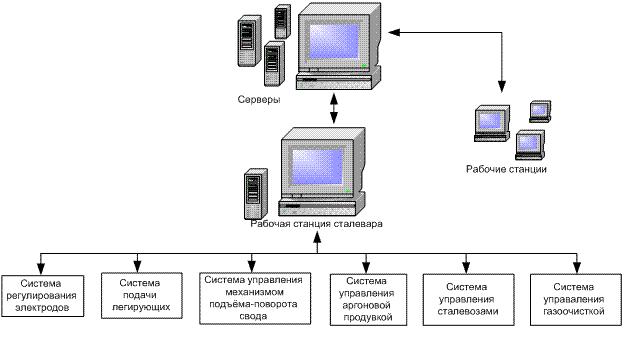
Рисунок 2 - Загальний вигляд системи управління установкою піч-ківш
.
(анімація: 6 кадрів, 4 цикли повторення, 52 кілобайти)
Hа даному рисунку показано взаємозв’язок всіх підсистем з керуючою ЕОМ – Робоча станція сталевара (РС сталевара). З окремих підсистем передаються дані про хід технологічного процесу на керуючу ЕОМ, де відбувається їх обробка та видача відповідних команд. Отримані дані передаються до загальноцехового серверу, де відбувається їх архівація і зберігання.
4. Огляд досліджень і розробок
В цьому розділі розглянемо теоретичні та практичні досягнення вітчизняних і зарубіжних дослідників в області газоочищення і автоматизації подібного роду систем.
Існує достатня кількість способів уловлювання промислового пилу. Основні конструктивні особливості та рекомендації щодо вибору способів для конкретних технологічних умов містяться в працях Г.М.Аліева [2].
У підручнику Юдашкіна М.Я. наведені основні положення по вибору матеріалів фільтруючих елементів рукавних фільтрів. Вибір здійснюється на основі температури газів, діаметрах мікрочастинок пилу, необхідного ступеня очищення газів, термінам служби і ін параметрам [3].
Підхід до автоматизації установок даного типу носить індивідуальний характер, тому серійна уніфікована апаратура автоматизації для даного обладнання не випускається. Загальні положення по автоматизації металургійних об’єктів містяться в книгах Глінкова Г.М. [4].
У книзі [5] розглянуті технологічні процеси як об’єкти автоматичного управління. Коротко викладені основні принципи побудови автоматизованих систем управління, питання організаційного, інформаційного, математичного, програмного і технічного забезпечення АСУ ТП. Розглянуто особливості автоматизації металургійних установок.
У збірнику доповідей міжнародної конференції МЕТАЛУРГІЯ-ІНТЕХЕКО
[6] наведено конструктивні особливості, характеристики, а також порівняльний аналіз рукавних фільтрів і електрофільтрів.
В Україні розробкою та монтажем автоматизованих систем імпульсної фільтрації займається Український державний науково-технічний центр
Енергосталь. УкрДНТЦ
Енергостальрозроблені і впроваджені суміщені системи газовідводу, уловлювання та сухої очистки пічних газів і неорганізованих викидів крупно-і середньотоннажних електропечей, що включають: водоохолоджуваний газовідвід гарячих технологічних газів від склепіння печі, даховий парасольку для уловлювання потоків неорганізованих викидів, сухі пиловловлювачі (рукавні фільтри з імпульсною регенерацією), димососи, систему газоходів, систему пилоприбирання і огрудкування пилу [7].
Існує безліч зарубіжних виробників автоматизованих систем імпульсної фільтрації, які пропонують автоматизовані системи рукавних фільтрів з імпульсною регенерацією: FLSmidth Airtech, VAI Fuchs і багато інших. Системи автоматизації цих виробників побудовані на програмованих контролерах
Інформація щодо технологічних датчиків і їх основних параметрах, сфери їх застосування, а також поведінці в складі систем автоматичного управління викладена в підручнику, виданому на кафедрі ГЕА [8] Основні відомості по мікросхемах, застосовуваним схемам гальванічної розв’язки і їх елементної бази, графічному представлення елементів електричних схем представлені в джерелах [9–11].
5. Моделювання технологічного процесу
У зв’язку з цим виникає необхідність дослідження процесу охолодження відпрацьованих газів повітрям, визначення його математичної моделі та отримання якісних характеристик, а також, на основі отриманих даних, автоматизації даного процесу.
При побудові підсистеми управління температурою газу ан впуску фільтр враховуємо, що залежність між кутом повороту заслінок припливного демпфера і температурою газу в фільтрі можна виразити таким аналітичним виразом [12]:
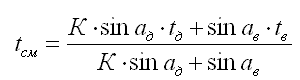
где К – усереднений коефіцієнт, що враховує відношення середніх теплоємкостей димових газів і повітря;
sinaд – синус кута відкриття (ступінь відкриття) димової заслонки;
sinaв – синус кута відкриття (ступінь відкриття) повітряної заслонки;
tсм – температура димовоздушной суміші;
tд – температура диму;
tв – температура повітря.
Трубопровід може характеризуватися діаметром, об’ємом, випромінюючої здатністю і т.д. В даному випадку нас цікавить його інерційність, тобто за який час відходить газ пройде від точки розбавлення до точки входу в фільтр. Виходячи з цього міркування, будемо вважати його аперіодичною ланкою першого порядку. Постійні часу на різних ділянках трубопроводу, визначимо знаючи середню швидкість газового потоку та довжини даних ділянок.
Структурна схема модельовання з використанням середовища Matlab [13] наведена на рисунку 3.
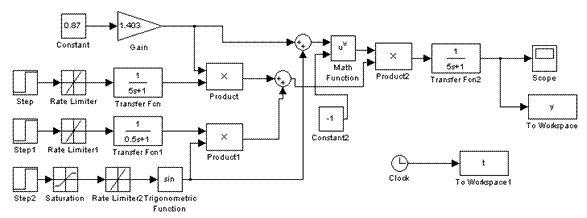
Рисунок 3 – Структура моделі охолодження димових газів
Заслонки, разом зі своїми електроприводами обмежують швидкості наростання димового і повітряного потоку. Для спрощення аналізу в даній системі будемо вважати їх лінійними функціями. Блоки математичних операцій реалізують залежність між кутом повороту заслінок припливного демпфера і температурою газу в фільтрі
За допомогою моделі, наведеної на рисунку 3, отримуємо перехідний процес охолодження димового газу повітрям, наведений на рисунку 4.
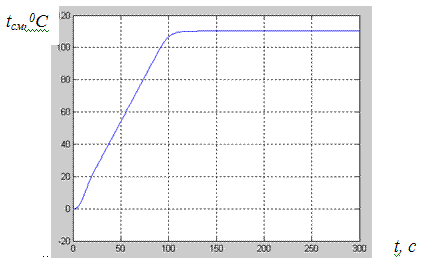
Рисунок 4 – Графік перехідного процесу системи охолодження
На рисунку 4 відображено процес встановлення температурного режиму при запуску газу в систему фільтрації. Як видно з графіка, стале значення (110 °С) є прийнятною робочою температурою. Але так відбувається далеко не завжди, тому що реально в даній системі можуть відбуватися різкі зміни температури димових газів, що зумовлено роботою системи підтримки постійного горіння дуги – регулювання електродів установки піч-ківш
або зміни положення заслонки на газоході КПК, керованою системою аргонової продувки і перемішування. Можливий вплив даних факторів врахуємо при подальшому моделюванні. Перехідний процес встановлення температури в системі охолодження, в даному випадку, наведений на рисунку 5.
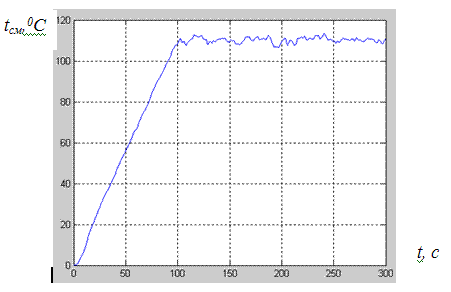
Рисунок 5 – Графік перехідного процесу системи охолодження з урахуванням зовнішніх збурень
Коливання температури в зоні сталого значення не є значними, тобто не призводять до аварійного перевищення температури, але все ж є небажаними, так як можуть викликати постійні включення приводів заслонок без вагомої на те причини, що спричинить за собою передчасну відмову останніх. З цією метою слід ввести нечутливість системи до малих відхилень температури від сталого значення.
Ще однією важливою проблемою є перевищення допустимої робочої температури або зайве її зниження. Перше тягне за собою пошкодження мішків фільтра, а втричі – недовантаження технологічної установки і зниження її ККД. З урахуванням даних особливостей прейдем до моделювання процесу охолодження з використанням системи автоматичного управління.

Рисунок 6 – Модель процесу охолодження з використанням системи автоматичного управління
Для порівняння подамо на вхід моделі 6 впливи, аналогічні тим, результати яких наведені на рисунку 5. Результат моделювання наведено на рисунку 7.
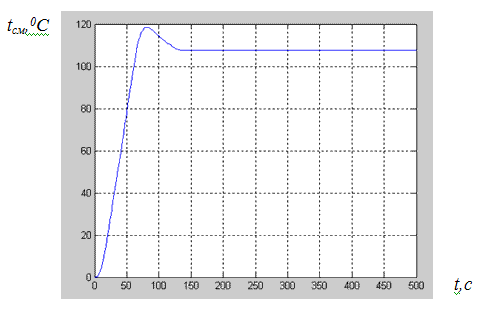
Рисунок 7 – Автоматичний запуск і встановлення температури
Незважаючи на невелике перевищення температури, отриманий графік більшою мірою задовольняє технологічним параметрам установки, тому що стале значення знаходиться поблизу необхідного за технологічними параметрами установки, чим забезпечується оптимальне навантаження приводу вентилятора і підвищується ККД технологічного процесу.
Висновки
В ході проектування було розроблено систему автоматизованого управління системою газоочистки установки позапічної обробки сталі, відповідна технологічним вимогам як за якісними характеристиками, так і за конструктивним виконанням.
Завдяки спеціальному способу установки вимірювального перетворювача і відповідної конструкції системи управління забезпечується більш оперативне регулювання температури. Тим самим буде забезпечуватися максимально-ефективне завантаження технологічної установки, що призведе до скорочення споживання електроенергії, а також продовження терміну служби мішків фільтра імпульсної фільтрації.
Найважливішою перевагою даної системи є використання більш точної математичної залежності між зміною кута відкриття заслінки демпфера і температурою газу.
Управління очищенням мішків на підставі їх засміченості дозволяє знизити кількість струшуючих імпульсів і тим самим зменшити кількість мікропошкоджень мішків, що не тільки подовжує термін їх служби, а й підвищує якість самої очищення газів, що викидаються в атмосферу.
Розроблені схеми дозволяють впровадити дану систему в загальноцехового систему автоматизації на всіх трьох рівнях і забезпечити її нормальне функціонування в умови інтеграції з іншими системами металургійного виробництва. Для більш оперативного виявлення і усунення несправностей розроблена система діагностики, яка знижує простої установки на їх усунення.
Ці заходи спрямовані на зменшення витрат виробництва, зниження собівартості продукції і, як наслідок, підвищення конкурентоспроможності підприємства.
Перелік посилань
- Руководтво по эксплуатации системы газоочистки УПК. – Д.: ЗАО «Донецксталь МЗ», 2003 г. – 465 с.
- Алиев Г.М. Техника пылеулавливания и очистки промышленных газов: Справ. изд. – М.: Металлургия, 1986 г. – 544 с.
- Юдашкин М.Я. Пылеулавливание и очистка газов в черной металлургии. Изд. 2-е, перераб. и доп. М.: Металлургия, 1984 г. – 320 с.
- Глинков Г.М., АСУ ТП в черной металлургии / Глинков Г.М., Маковский В.А. М.: Металлургия, 1999 г. – 427 с.
- Бойко В.И. Автоматизированные системы управления технологическими процессами в черной металлургии / Бойко В.И. Смоляк В.А. – Днепродзержинск. 1997 г. – 574 с.
- Гольцев А.В. Системы снижения выбросов пыли (FLSmidth Airtech, Дания). Сборник докладов международной конференции
МЕТАЛЛУРГИЯ–ИНТЕХЭКО
г. Москва, 30-31 марта 2010 г. – 140 c. - "Сталь" №12. 2006г. с. 73-74 – 288 с.
- Груба В.И. Технические средства автоматизации в горной промышденности / Груба В.И., Никулин Э.К., Оголобченко А.С. – К.:ИСМО, 1998 г. – 373 с.
- Гутников В.С. Интегральная электроника в измерительных устройствах. – 2-е издание, перераб. и доп. – М.: Энергоатомиздат, 1989 г. – 431 с.
- С.Т. Усатенко. Графическое изображение электрорадиосхем: Справочник /С.Т. Усатенко, Т.К. Каганюк, Н.В. Терезова. – К.:Техныка, 1986 г. – 210 с.
- В.И. Иванов. Полупроводниковые оптоэлектронные приборы: Справочник / В.И. Иванов, А.И. Аксенов, А.М. Юшин – 2-е издание, перераб. и доп. – М.: Энергоатомиздат, 1989 г. – 448 с.
- А.В. Павленко. Аналитическое определение температуры газов в фильтре системы газоочистки / Прикладные задачи математики в механике, экономике, экологии: Материалы IX международной студенческой научной конференции. А.В. Павленко, В.И. Ахонин, И.К. Юрченко – Севастополь, 18-22 апреля 2011 г. – 175с., с. 85-88.
- Дьяконов В.П. MATLAB. Анализ, идентификация и моделирование систем. Специальный справочник. / Дьяконов В.П., Круглов В.В. – Питер, 2001 г. – 448 c.