Аналіз та розробка заходів щодо попередження стояночної корозії котлів ТП-109 блоку 200 МВт Кураховської ТЕС
Зміст
Вступ
Як правило устаткування, що знаходиться в резерві або в стадії консервації, при поганому дотриманні технології і не достатньою мірою осушки, піддається стояночній корозії і виходить з ладу.
Відомо, що корозія протікає на межі метал - робоче тіло (метал - теплоносій). Вона призводить до часткового або повного руйнування кристалічної решітки і відповідної зміни властивостей металу. Це руйнування може викликатися різними причинами: хімічними, електрохімічними, механічними, впливом нейтронного поля та інших факторів.
Стояночна корозія є найбільш поширеним видом руйнування котельного металу. Їй піддаються всі елементи котлів, виготовлені з вуглецевих і низьколегованих сталей, які контактують з водою практично з будь-яким вмістом в ній кисню. Однак, на практиці корозія набуває небезпечного характеру лише при вмісті кисню в живильній воді, що перевищує 10-20 мкг / кг. Корозія, як правило, проявляється у вигляді виразок з діаметром до 5 - 10 мм, часто покритих пухким шаром іржі. При простоюванні котлів корозія практично захоплює всі елементи парових котлів, де є кисень і волога.
ОСНОВНІ МЕТОДИ БОРОТЬБИ ЗІ СТОЯНОЧНОЮ КОРОЗІЄЮ
Методи боротьби зі стояночною корозією діляться на сухі і мокрі.
Найпростішим методом боротьби зі стояночною корозією парогенераторів є спуск із них ще гарячої води з температурою 80 ° С і висушування шляхом відкривання всіх люків, лазів і повітряників для виходу утвореної пари. В окремих випадках для поліпшення та прискорення висушування можна застосовувати слабкий обігрів спорожненного парогенератора газом або гарячим (t = 200 - 250 ° С) повітрям. Температура стінок повинна перевищувати 100 ° С.
При тривалій стоянці парогенераторів в резерві в барабани їх після спорожнення і висушування поміщають листи з вологопоглиначем (хлористим кальцієм CaCl2, негашеним вапном CaO, силікагелем (висушений золь кремнієвої кислоти H2SiO3) тощо) і герметично закривають усі лази, лючки, арматуру. На 1 м3 повного обсягу котла потрібно не менше 2 кг прожареного CaCl2, 3 кг свіжо СаО або прожареного силікагелю. Стан вологопоглинача перевіряють кожні 3-6 місяців і в разі распливанія CaCl2 або руйнування грудок СаО в результаті перетворення їх в Са (ОН) 2 вологопоглиначі замінюють свіжими. Однак ці методи пов'язані з додатковими витратами для нейтралізації цих розчинів після їх використання. в світовій практиці, де враховують не тільки початкові, досить значні витрати, але і вартість утилізації відпрацьованого розчину, екологічно небезпечні сполуки не знайшов широкого застосування.
Консервація нейтральним газом (як правило, азотом) з подальшим підтриманням невеликого надлишкового тиску (5-10 кПа) запобігає доступ зовнішнього повітря. Цей спосіб вимагає безперервну подачу азоту і якісну герметизацію системи. При цьому великі труднощі викликає герметизація проточної частини турбін. Практика показала, що витоку азоту при консервації енергоблоку 300 МВт складають (в залежності від якості запірної і запобіжної арматури) від 2-3 до 40-50 м3 / ч, тобто фактично необхідно власне азотне виробництво. Незважаючи на високу надійність цього методу консервації, він є досить дорогим через наявність великої кількості місць можливих витоків азоту і складності їх ущільнення.
У багатьох випадках для того, щоб запобігти корозії, досить зниження відносної вологості повітря до 60%. Зниження відносної вологості повітря може бути досягнуто двома шляхами: 1) нагріванням і 2) осушенням. Якщо повітря з температурою 20 ° C і відносній вологістю 70% підігріти на 10 ° С, то відносна вологість знизиться нижче 40%.
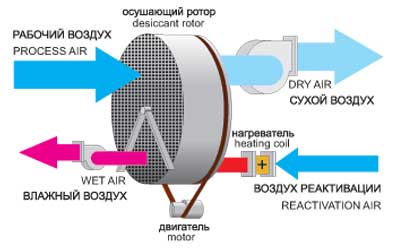
Рисунок 1 - Схема осушення повітря
Потім підігріте повітря подається всередину обладнання і, підвищує температуру металу в порівнянні з навколишнім середовищем, що перешкоджає випаданню вологи, забезпечує випаровування вологи, що залишилася в обладнанні після дренування, і оберігає поверхні від корозії. Тому застосування такого методу передбачає високі енергетичні витрати. У реальних умовах після подачі підігрітого атмосферного (а значить, вологого) повітря в непрогрітому обладнання він остигає, особливо в слабо продуваються каналах, і його відносна вологість знову опиняється в критичній зоні активної корозії. Також є небезпека конденсації вологи, якщо є поверхні зі зниженою температурою. Виходячи з цих міркувань, необхідно, щоб усі частини обладнання були доведені до температури вище точки роси подається з метою консервації підігрітого повітря Крім того, необхідно вимірювати характерні температури різних ділянок консервіруемой системи.
"Мокрі" методи консервації припустимі при плюсових температурах і зручніші, ніж "сухі", але вони придатні тільки при збереженні води або консервуючої розчину в парогенераторі. До них відносяться також:
- перебування парогенераторів в гарячому резерві з підтриманням у них надлишкового тиску 0,3 - 0,5 МПа паром від інших парогенераторів, від деаераторів, від відборів турбін, від розширювачів безперервної продувки, від лінії власних потреб або розпалювальної;
- заповнення парогенератора деаерірованной водою і підтримання в ньому тиску вище атмосферного в самій верхній точці котла (воздушник). Тиск у ньому підтримується за допомогою деаерірованной живильним або мережної води як після деаераторів ДП (0,5 - 0,7 МПа), так і після живильних насосів.
ВИСНОВКИ
Аналіз усіх відомих методів консервації дозволяє виявити найбільш перспективні, одним з яких є застосування методу заповнення котлів деаерірованной живильною водою у поєднанні з підтриманням у них постійного надмірного тиску. Десорбціонной знекиснення води досить перспективно. Метод заснований на десорбції розчиненого у воді кисню газоподібним азотом, одержуваних на місці. Він ефективний, дешевий і екологічно прийнятний.
На підставі цього методу, була запропонована корисна модель установки для десорбціонной знекиснення води.
ПЕРЕЛІК ПОСИЛАНЬ
- Акользин П.А. Основы расчета установок для десорбционного обескислороживания воды. – «Теплоэнергетика», 1954, №2, с.31.
- Мейкляр М.В. Как работает металл парового котла – Госэнергоиздат, 1961, 95с.
- Роберт Д. Порт, Харви М. Херроу. Практическое руководство компании НАЛКО по анализу причин повреждения котлов – McGraw-Hill, Inc. 278с.
- Баранов П.А. Предупреждение аварий паровых котлов – М. Энергоатомиздат, 1991, 272с.
- Либерман Г.Р Предупреждение аварий и неполадок котельного оборудования – М., Энергия, 1972, 312с.
- Методические указания по консервации теплоэнергетического оборудования – ОРГРЭС, 1997,49с.