Abstract
Содержание
- Introduction
- 1. Relevance of the topic
- 2. Analysis of technology
- 3. Formulation of research problems
- 4. Presentation of the material and results
- Conclusions
- References
Introduction
The most valuable products are derived from petroleum - gasoline and diesel fuel. More than 95% of the energy used in transport, is made from oil, its use in this sector is growing steadily in the near future is difficult to find fuel, which could permanently replace oil. In developed countries, the growing demand for oil due to the increased consumption of motor fuel. Each year, world oil demand will increase by 2% per year. Matures acute problem of shortage of petroleum products and their cost. Methanol can be used as raw material for synthetic hydrocarbons and their products. The annual production capacity of most existing plants ranged from 100 000 to 800 000 t gradually become the norm to construct plants with an annual capacity of about 1 million tons or even more, known as "Megafactories to produce methanol." The main developers of technology for synthesis of methanol to gasoline are Mobil, Cenetix, Lurgi, Haldor-Topsoe.
Basics conversion of methanol to hydrocarbon fuels have been developed by the company, "Mobil" (USA) during the implementation of a comprehensive program of work on the synthesis and application in catalysis vysokokremnezemnyh new zeolite ZSM series. Since the mid-1970s began working out a process known as "Mobile-MZHT" in pilot plants. The formation of hydrocarbons from methanol takes place in several stages. First, a reversible reaction occurs in the dehydration of methanol, dimethyl ether, which is then dehydrated to produce olefins. Last react polymerization and cyclization leading to the formation of paraffin, cyclo-paraffins and aromatic hydrocarbons. As used in the process of ZSM-5 catalyst has a specific crystalline structure that ensures the formation of hydrocarbons over a maximum of 11 carbon atoms, which corresponds to a relatively precise composition and limits boiling gasoline fractions of petroleum. [ 1,2 ]
1. Relevance of the topic
A feature of this nascent industry should serve as a high capacity for adjustment to new technological options is not only experienced, but the pilot and commercial reactors. Thus, the special role of the reactor system of ACS, which should be available as a function of the expert system to interpret the information from the sensors to dynamically "doissledovaniya" process. The application of this system makes it possible to determine the important process parameters on the basis of signals from a standard set of sensors, it is important to optimize the operation of the reactors.
2. Analysis of technology
Schematic diagram of the production of gasoline from methanol involves several successive stages of synthesis to the final product. In the general process involves the preparation of synthesis gas - to receive methanol - getting petrol. This scheme assumes that the feedstock for synthetic fuel is methanol, derived previously in the appropriate stage.
Description of technology.
Mixture of methanol and sin.gaza with a flow rate G = 8 t / h after fusion reactors (SNM and SNM-U1-U2), and heat exchangers (MOT number 4 and number 5 OT) while in the gaseous state with the swarm-Tg = 90 C, enters the gas-liquid THAT number 7, where the space between the tubes is heated to a temperature of Tg = 170 C over a finite set of heat fusion. product coming from these pipes. Emanating from teploobmіnnogo mashines Sereda to consider the course of 8 t / h and a pressure of 37 atm, should be the bottom of the reactor, the synthesis of NKT-2, where it is heated again, being in the tube bundle reactor by the heat of the final synthesis. product going to the annulus.
Going from the top of the central segment of the gathering with a temperature of Tg = 300 C and pressure of 36.4 atm and the pressure goes to the bottom of the reactor NKT-1. The reactor is a gaseous medium in tubes in which the catalyst is located (on substrates), where the reatsy Wednesday changed its composition: the input, we have 8 t / h of methanol and the remaining conversion products, the output stream of 8 t / h composed of a finite partially product, methanol, and the remaining conversion products. As a result of the synthesis reaction temperature within the working space is increased to 350 C (at a pressure of 108 atm) and kept constant by cooling water located in the annulus.
constant temperature in the cavity of the reactor is maintained by the installation of vapor pressure with the relevant regulatory authorities. Steam-water mixture formed in the boiling water in the annular space, up to the separator, which is separated and removed dry saturated steam. Restores coolant mass is realized through the supply of fresh feed water. Makeup water flow rate is determined from the condition of maintaining a given level of coolant in the reactor or the space between the tubes of a given mass of coolant in the reactor. In the first case, the use of a level sensor in the second weighing of the reactor with the help of strain gauges. According to the authors, because a small fraction of evaporated liquid as compared to its total mass in the reactor, the upper level of liquid in the reactor will have at least a few wavering but rather a clear boundary, that allows the use of such capacitive level sensors.
Also fill water mass separator is implemented by supplying a seed from the outside and a pair of feed water used in heat transfer devices (TO4, TO5, TO6) with a flow rate of 2.1 t / h and a temperature of 50C.
Synthesis.
Product and unreacted starting material goes from the upper part of the collecting system and at a pressure of 36.8 atm is fed back to the NKT-2, which follow in the annulus of the reactor, unreacted doreagiruet iskh.produkta at about 280 C. Also, the synthesis. product going to the space between the tubes, giving the heat source product, cooled to a temperature of 190 C at the output and consumption of 8 t / h
Next step on the path of gaseous sintez.produkta (at a pressure of 36 atm) is TO6. In TOprodukt cooled set the pit .. water to a temperature at the exit 178S, following in the shell side of THAT. itself, the water is heated by the temperature of 15C (input) to a temperature of 50 ° C (output) at a rate of 1.05 t / h following the further into the separator p>
Partially cooled product must be in the heat of fusion TO7.Gde. product is used to heat the starting material (methanol + conversion products). Following in the synthesis of heat exchanger tube space. vyodit product out of it with a temperature of 125C and flow rate of 8 t / h
Sintez produkt Final cooling occurs in TO12, in which the cooling medium is water at a rate of 3.05 t / h and a temperature of 15C, going through the pipes. The final temperature of water at the outlet of the 75S TO. The synthesis of the product in the following ohdazhdaetsya annulus to a temperature of 80 ° C enters the separator repaired under the pressure of 35 atm, where the synthesis of the product mixture is separated into the residual gas, water, and the actual synthesis of the product. Synthesis. product with a flow rate of 4 t / h is used to further tehnologich.skhem (production of nanotubes, etc) [ 3,4,6 ]
3. Formulation of research problems
The main tool used in the synthesis reactor fuel - pin device, whose design depends mainly on how the removal of heat and the principle of the synthesis process. In the modern technological schemes used three types of reactors. In this paper we investigate the thermal performance of tubular reactors in which the catalyst is placed in the tubes through which the reaction mass, cooled condensate water, boiling in the annulus.
4. Presentation of the material and results
Сircuit water cooled reactor for methanol synthesis with the proposed collection of items instrumentation and control system for the diagnosis of thermal performance is presented in Figure 2.
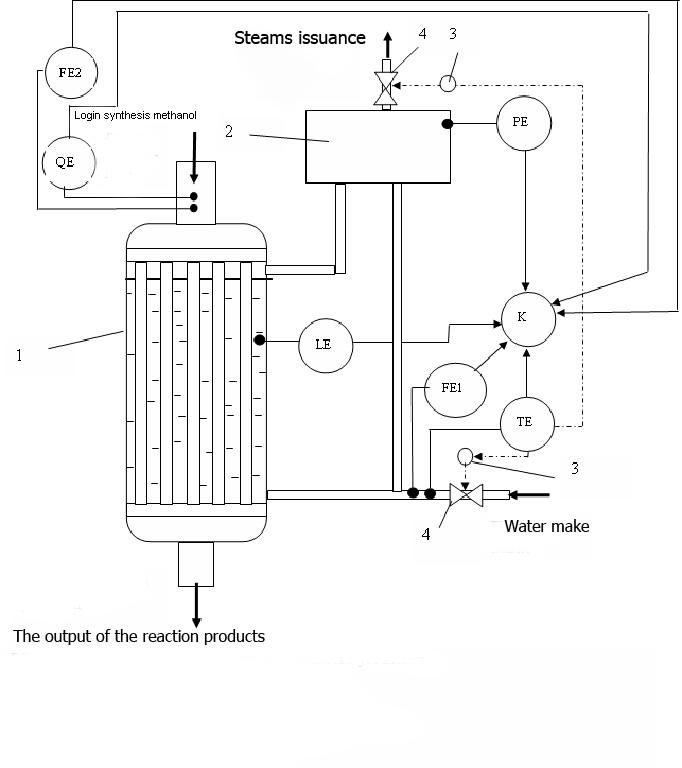
Figure 2 - Diagnostic systems of thermal reactor fuel synthesis
(1 - a water-cooled reactor, 2 - separator, 3 - actuators, 4 - regulators)
Conclusions
Master's thesis is devoted to the feasibility of developing diagnostic systems of water-cooled thermal reactor synthesis of gasoline from methanol. Propose a concrete scheme of thermal diagnostics of water cooled reactors, fusion fuel.
References
- Дж. Ола, А. Геперт, С. Пракаш “Метанол и энергетика будущего. Когда закончатся нефть и газ”;пер с англ. - М.:БИНОМ.Лаборатория знаний,2009 - 416 с. : ил.
- Мановян А.К. "Технология переработки природных энергоносителей" - М.:Химия ,КолосС,2004.-456с.ил(учебное пособие для студентов высш. заведений)
- М.М.Караваев,В.И.Леонов,И.Г.Попов "Технология синтетического метанола" под ред.проф.М.М.Караваева- М.Химия.,1984 240с.,ил.
- И.П.Гойхрах,Н.Б.Пинагин "Химия и технология искусственного жидкого топлива",2-е переработанное издание,Гостоптехиздат, М. - 1954.
- А. Гретц "Химия нефти и искусственного жидкого топлива",перевод Д.Н.Андреева,Л.Н.Петровой,под.ред проф.А.Д.Петрова,М. - 1936, 526 с.
- И.П.Мухленов,А.Я.Авербух,Д.А.Кузнецов "Общая химическая технология",в 2-х частях,под ред. А.П.Мухленова.Учебник для вузов.Ч.II.Изд.3-е,"Высшая школа", - 1977.288 с.с ил.
- Бесков В.С."Общая химическая технология:Учебник для вузов"- М:ИКЦ "Академкнига",2005 - 452с с ил.
- "Моторные топлива из альтернативных сырьевых ресурсов"/Г.А.Терентьев,В.М.Тюков,Ф.В.Смаль - М.:Химия,1989 - 272 с. : ил.