Roman Skripnik
Physico-metallurgical faculty
Department of metal forming
Organization of production of cold-rolled strip in Ukraine
Scientific adviser: Professor Yuriy Konovalov
Abstract
Content
- 1. Sovremennoe situation in Ukraine with the cold-rolled sheet and the relevance of the topic
- 2. Tseli and problems solved in this paper
- 3. Vybor type mill
- 3.1 Analysis of existing mills and mill selection
- 3.2 The selection of parameters for this type of mill
- 4. The choice of methodology for calculation of rolling force
- 5.Raschet modes and power rolling on this type of mill
- 6.Rekomendatsii for installing automation systems on the mill
- References
Introduction
High-quality cold-rolled sheet is the basis for the engineering industry, so this type of product has great demand in both domestic and world market. When applying protective coatings on cold rolled strip or sheet of the cost increases significantly. In 2010 Ukraine started two new plants for the production of galvanized and coated flat products - "Yunistil" (Krivoy Rog), and "Metals and Polymers" (Alchevsk). In the near future, both companies plan to substantially increase production. Another plant of the current "Module" specializing in galvanizing cold rolled sheet is in Kamenetz-Podolsk. The total need for these three plants in the cold-rolled to hire approximately 1 million tons per year.
1.Sovremennoe situation in Ukraine with the cold-rolled sheet and the relevance of the topic
Manufacturers of coated steel is mainly used imported cold-rolledto rent, explaining the decision that the rolls of JSC «ZMK" Zaporizhstal "and PAO Mariupol. Lenin did not meet modern requirements: they are too high tolerances on thickness steel and other defects, which explains the outdated equipment of rolling shops of metallurgical enterprises. Stan PSC 1700 Mariupol. Illich cold rolling is the second generation of continuous mills, reconstruction of the main equipment was held in the 70s and now very out of date, all the automation systems at the mill just do not meet modern international standards. The continuous cold rolling mill in 1700 of "MCW" Zaporizhstal "refers to standard first-generation and its modernization is practically impossible. This situation makes our market is dependent on imports of cold rolled sheet.
2. Tseli and problems solved in this paper
The aim of this work is to develop proposals for the organization of production of cold rolled sheet up to 1 million tons / year in the economic situation in Ukraine. Select the type of mill, the establishment of optimum modes of compression, and recommendations on the application of automation systems for the host.
3. Vybor type mill
3.1 Analysis of existing mills and mill selection
Currently, the major cold-rolled sheet steel mills produce a continuous way on continuous mills and endless rolling mills. When small amounts are used to reverse rolling odnokletevyh and only very recently, the reversible rolling mills dvuhkletevyh [1-3]. In terms of the lack of modern cold-rolling mills in the territory of Ukraine it is expedient to build a new cold rolling mill. Total domestic demand in the cold-rolled sheet is about 3 million tons per year. Construction of endless rolling mill capacity of about 2.5 million tons per year would almost completely cover the needs of the domestic market of Ukraine in the form of products. However, the cost of only one mill without auxiliary equipment is more than $ 500 million. For the modern economy of Ukraine, this amount is not real. Therefore, the first stage of solving the problem of cold-rolled sheet in Ukraine and the waiver of import, it is proposed the construction of dvuhkletevogo reversing mill, so that as soon as possible to cover the paramount need to hire three workshops for applying protective coatings. The performance of the mill is 800-1000 tonnes per year, and its cost by more than 2 times lower than the 5-kletevogo continuous rolling mill.
3.2 The selection of parameters for this type of mill
The length of the barrel of the rolling mill stands it is advisable to have a 1700 mm or 1680 mm, which will be used to tackle the hot rolling mill 1700. Mandatory requirement - the establishment of this camp the same reels on both sides of the camp. This will allow to perform any number of passes and if necessary, conducts an intermediate annealing. All of this will be used in hot-rolled wide range of thicknesses from 2 to 6 mm. This allows you to use a sliding tackle with both operating in Ukraine SHSGP, so import tackle (which is much cheaper than cold rolled sheet). Extensive choice of thickness rolled from one side can choose to pursuing the purpose of minimum costs for him and the other to choose the thickness of rolled with the current Ukrainian SHSGP.
The very process of rolling on dvuhkletevom reversing mill is as follows manner. Roll after etching is placed on the mandrel, the front end set in the ruling - the pulling device, and then he goes to the first and second cage. Coming out of the cage front end of the band captured winder, after winding 2.3 turns of the tension and set the required standard will accelerate to set speed rolling. Before the end of the rolling mill bands automatically slows down, reversed, and the process repeats. Since the camp, and from the front and rear of the device is equipped with a pickup coil reels and conveyors rolls, then the mill can produce any number of passes.
In determining the relative reduction and, consequently, the force parameters of rolling should take into account the fact that immediately after the cold rolling with reduction of the band structure of the recrystallization does not occur. That is, each successive band reduction will occur in the presence of increasing work-hardening metal. It is because of the number of breakdowns of work hardening on continuous mills limited, it should not exceed the number of stands. It is therefore very important that the rolling mill on the reverse of the possible intermediate annealing, which makes it possible to obtain a strip of plastic properties specified for the subsequent pass. That is, it is possible to remove the roll after the accumulation of the critical hardening, annealing, and to continue rolling. Rolling on the dvuhkletevom reversing mill, as well as on any cold-rolling mill, is conducted only with lubrication because of the large frictional forces encountered during cold rolling [4-9].
4. The choice of methodology for calculation of rolling force
To select the optimum condition for the principles of technical - economic and qualitative indicators need to study various options for the thickness of the tackle and rolling modes, and for these purposes must select options for calculating the energy-power parameters on it. Engineering analysis (theoretical) and empirical models of the rolling average pressure - a key tool for carrying out preliminary calculations and optimization of technological processes of rolling, and for the automatic control process rolling. Their relative simplicity is advantageous Unlike complex numerical models designed for detailed studies of the process is not time-bound and capabilities of computers.
Most of the domestic procedures for the determination of the average contact pressure based on the methodology of AI Tselikova. In [3] conducted a comparative analysis of the methodology and empirical model VM Lugovskogo in connection with a wider range of functionality. Comparative analysis of the engineering models mean contact pressure AI and VM Tselikova Lugovskogo showed a preference for a theoretical model of AI Tselikova when necessary to make the choice of optimal regime of rolling thin strips with high compression and low coefficient of friction. It is shown that under these conditions, the model ML AI Tselikova allows to consider substantially increasing influence of tensile stresses in the deformation that the model does not account for VM Lugovskogo, the calculation of which leads to high results.
Therefore, when choosing a method to determine the average contact stress was chosen as the method A.V.Tretyakova - BELokshin, based on the methods of AI Tselikova. Methodology A.V.Tretyakova - BE Lokshin has several advantages, chief among which is the definition of force and work during the rolling process, a single energy-power, allowing to determine the exact effect of rolling, rolling moment and the degree of hardening of the metal during rolling.
Despite the fact that the methodology A.V.Tretyakova - B.E.Lokshina usually used to calculate the forces on the rolling mills of continuous rolling, the presence of two consecutive stands on dvuhkletevom mill makes it possible to use methods for the calculation of A.V.Tretyakova. We accepted it, and for reversing mill dvuhkletevom.
The presence of the reverse is also taken into account when calculating the modes of rolling on odnokletevom reversing mill. We can therefore say that the calculation mode for the rolling mill dvuhkletevogo has common features with the calculation of modes, both on odnokletevom camp, and the continuous rolling mill [10,11].
5.Raschet modes and power rolling on this type mill
One of the basic principles for selecting the number of passes on the mill is the principle of uniformity of loading the aisles of the stands. Since the standard dvuhkletevoy, the possible number of passes can only be even. For rolling the strip thickness of 0.35 mm 2 mm tackle, take six passes. Calculation of the rolling force was held in the program Microsoft Excel, for each of the passages and their respective breakdowns. The scheme of the window shown in Figure 1.
The accepted number of passes will receive a strip of a given thickness at the most uniform load of crates that can be seen from the calculation results are shown in Table 1.
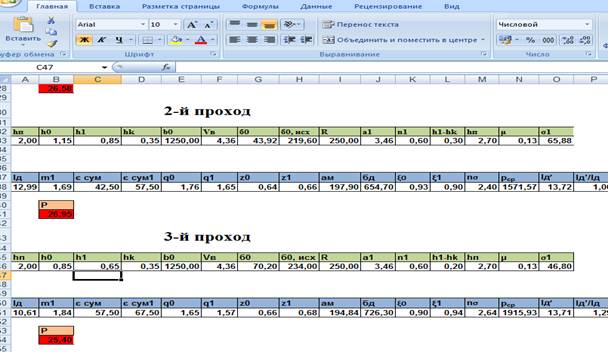
Figure 1. The window of the program Microsoft Excel.
The calculation of rolling force in each of the passages.
Table 2. Mode of breakdown and the strength of the rolling mill for cold rolling dvuhkletevom
Number of;passage |
Thickness, mm |
The relative reduction,% | The strength;of rolling,;MN | |
on input | on output | |||
1 |
2 |
1,15 |
42,5 |
26,58 |
2 |
1,15 |
0,85 |
26,1 |
26,95 |
3 |
0,85 |
0,65 |
23,5 |
25,4 |
4 |
0,65 |
0,5 |
23 |
27,71 |
5 |
0,5 |
0,4 |
20 |
25,11 |
6 |
0,4 |
0,35 |
14,2 |
14,84 |
From these results it is clear that the maximum relative reduction falls on the first pass and is 42.5%, the rolling force in this case is 26.58 MN. In the future, the relative reduction decreased, but this is an increase in rolling force up to 27.7 MN for compressing 23% in the fourth cage. This is associated with an increase in work hardening in metals and hardening, which leads to an increase in rolling force, even at lower compressions. Despite this, the smallest force of rolling (14.8 MN) in the last stand, as the relative reduction in it is only 14.2%.
6.Rekomendatsii for installing automation systems on the mill
Installation of modern automation systems on the mill will be able to provide the necessary requirements for the list, which impose on the world metal market, increase yield and overall productivity of the mill.
In the cold rolling mill dvuhkletevom can produce small lots of rolling and easily change the product mix and the thickness of the metal, depending on customer requirements. To accomplish these tasks quickly reset to the standard, or metal loss due to deviations from tolerances, will reduce its performance. In this connection, setting the mill running mathematical models of the process, establishing the band compression and setting the given parameters (position gidronazhimnyh devices, roll force, position when changing rolls, work rolls protivoizgib, etc.) for the respective actuators.
.References
- Гарбер Э.А.Производство проката. Том 1. Книга 1. Производство холоднокатаных полос и листов. - //: Теплотехник, 2007.368с
- Современный цех холодной прокатки углеродистых сталей / И.В. Франценюк, Ю.Д. Железнов, Л.А. Кузнецов, В.Г. Камышев.-М.: Металлургия, 1984.-154с.
- Особенности современного оборудования и технологии бесконечной холодной прокатки / Г. Финштерманн, Н. Моньер, С. Наппез, Г. Прадайрол // Сталь.-2004.-№1.-С.43-46.
- Ангербауэр А., Джумлия Г., Кенигсхофер М. Новое оборудование для холодной прокатки стали // Сталь.-1999.-№12.-С.48-53.
- Хекуэт Р. Новый двухклетевой реверсивный стан холодной прокатки на металлургическом заводе фирмы «Heartland Steel» // Черные металлы.-2000.-Сентябрь.-С.84-87.
- Создание и освоение двухклетевого реверсивного стана холодной прокатки / В.Ф. Рашников, Р.С. Тахаутдинов, А.И. Антипенко и др. // Сталь.-2003.-№7.-С.41-45.
- Современные концепции управления двухклетевыми реверсивными станами холодной прокатки / И.И. Бондяев, А. Дюммлер, Р. Польтер, Э. Вильке // Сталь.-2004.-№5.-С.70-72.
- Беняковский М.А., Мазур В.Л., Мелешко В.И. Производство автомобильного листа.-М.: Металлургия,1979.-256с.
- . Гусева С.С., Гуренко В.Д., Зварковский Ю.Д. Непрерывная термическая обработка автолистовой стали.-М.: Металлургия, 1979.-224с.
- Третьяков А.В., Зюзин В.И.Механические свойства металлов и сплавов при их обработке давлением, Металлургия 1973.-224с
- Теория прокатки. Справочник/ А. И. Целиков, А.Д. Томленов, В.И. Зюзин Металлургия 1952.-335с
- Бондяев И.И. Современные концепции управления ддвухклетевым реверсивным станом холодной прокатки / И.И Бондяев // «Сталь» Украины. - 204. - №5. - С. 70-71.