Abstract
Содержание
- Introduction
- 1. Relevance of the Work.
- 2. Goal and tasks of the research.
- 3. The technological characteristics of the mine.
- 3.1 Analysis of mine technical situation when developing reserves in this layer.
- 4. Identification of factors affecting the extraction of coal from the working layer.
- 4.1 Gaseous factor.
- 4.2 The scheme of ventilation excavation of the section.
- Conclusion
- References
- 4.2 The scheme of ventilation excavation of the section.
Introduction
Coal is the main source of fuel energy in Ukraine.
In the transition to a market economy necessity to increase the level of coal production while reducing its cost increases.
The most important task of the coal industry is to continue modernization and reconstruction of the mines of Donbass based on advanced techniques and technology of coal and mines, as well as the progressive introduction of new types and lining, and new ways to maintain the roof.
In Ukrain, about 70% of the mines are in poor working conditios. With increasing depth of coal mining, there is decrease in strength of the rock surrounding the coal seam. There is decrease in the knowledge of mine excavation to meet up with the challenging increasing dangers in mines, which can be linked to underfunding or even closures of some of the coal research institutes. The main task of the state is funding science and its development.
1. Relevance of the Work
The issue of increasing the load on the working face is the most important in the mining industry. This question requires constant attention of professionals in the industry.
The load on the working face is an important factor in having a decisive influence on the techno-economic performance of the mine and mining area. Its increase reduces the cost of coal production and increased labor productivity. It is necessary to achieve maximum possible load on the working face, which is limited by the excavation machinery and gaseous factor.
2. Goal and tasks of the research
Purpose – Development of measures to increase the load on the working face.
Scientific novelty: the coefficient of increase of computer time.
Main tasks of the research:
- Analysis of the conditions of ventilation mine site.
- Analysis and remediation of the technological scheme of the plot.
- Development of measures to increase the ratio of machines time.
Research object: Mine V. I. Lenin.
Research subject: mining equipment and mine workings of the mine, V. I. Lenin.
3. The technological characteristics of the mine.
The mine, V.I. Lenin, was designed by "Yuzhgiproshakt" institute and put into operation in 1955 with a production capacity of 750 tons of coal per year. According to the project executed by "Dongiproshaht" institute in 1993, the feasibility of opening and exploring the reserve of Kamenskaya suite, puts the production capacity to be 600 tons per year. But, since 2006, the production has been at 300 tons yearly.
Recent reconstruction of mine made in 1974;
Category of mine gas – dangerous to sudden outbursts of coal and gas;
Relative methane content – 15.7 м3/т.с.д;
Absolute – 13.1 м3/min;
The rate of inflow of water into the mine – 735 м3/hr.
The maximum depth of mining operations – 875 м
The maximum depth of coal treatment works – 658 м
The length of the existing mine workings – 38,59 км
Area of dangerous mining area – 4,7 км. или 12,2 %
The mine is being explored in two layers:
l21 – threatened by sudden outbursts of coal and gas, dangerous for the explosiveness of coal dust, is not prone to spontaneous combustion, geological capacity m = 0,87–0,89 м
Ash layer А = 27,5 %, сера S= 3,9 %;
k6н – dangerous to sudden outbursts of coal and gas, not a dangerous impact on the mountain, dangerous for the explosiveness of coal dust, is not prone to spontaneous combustion, geological capacity m = 0,69–0,75 м
Ash layer А = 25,7 %, сера S = 3,1 %;
Reserve as at 01. 01. 2012 г.:
- Balance – 48,208 million tonnes
- Industrial – 37,721 million tonnes of which:
- l21 – 1,351 million tonnes
- k6н – 6.914 million tonnes
3.1 Analysis of mine technical situation when developing reserves in this layer.
Mine field is dissected by five vertical shafts.
Western ventilation shaft.
The reserve in shaft number 2 has decreased in its economic viability.
Method of preparation of the mine field of reservoir k6н – horizontally.
System design – solid.
The scheme of ventilation shafts – Central region.
Method of ventilation – suction.
Management of the roof layer – a complete collapse.
Pre-production includes combine methods.
Gas release from the reservoir to the wellbore space is
qуч = 8,56 м3/т.с.д., and from gob qв.п = 8,635 м3/т.с.д.
By the end of year 2011, work by ejecting coal seam in k6n has graduated in connection with the noise reservoir capacity. The plan of mine works on layer k is6н shown in Figure 1.
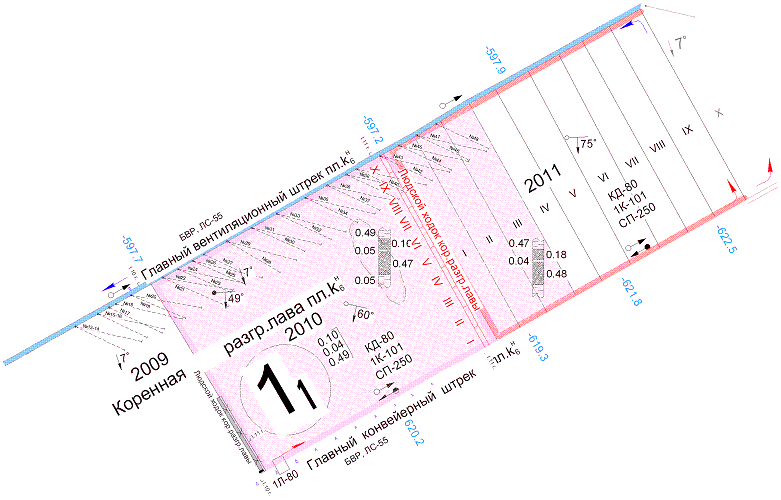
Рисунок 1 – Пласт k6н
План горных выработок (анимация: 7 кадров, 7 циклов повторения, 300 килобайт)
4. Identification of factors affecting the extraction of coal from the working layer.
The maximum possible load on the working face is taken as a minimum of two values: the maximum possible load on the cutter machine performance and maximum load factor of the gas.

where:
Ал.м – the maximum possible load on the working face of performance cutter machine, т/сут;
Ал.в – possible load on the working face by the condition of gas release into the lava and ventilation, т/сут.
Maximum Daily Load for the lava to combine the performance is given by:

where:
Асм – average shifts load on the working face, т/сут;
nсм – The number of shifts for excavation of coal per day;
kгн – Reduce the load factor at the working face (under average conditions, and no violations within the excavation area, according to [2] kгн = 1;
kи – Coefficient of extraction of coal in the working face.
Interchangeable load on the face is calculated as follows:

where:
Тсм – the duration of the work shift, мин;
qк – The average performance of the combine, т/мин;
kм – The replacement ratio of machines time on the excavation of coal.
For different values of the coefficient of machines time for excavation and replacement of coal daily production from the working face are shown in Table 1.
Км | Асм, т/см | Ал.м, т/сут |
0,25 | 122,4 | 359,8 |
0,3 | 146,88 | 431,8 |
0,35 | 171,36 | 573,8 |
0,4 | 191,84 | 564 |
0,45 | 220,32 | 647,7 |
0,5 | 244,32 | 719,7 |
0,53 | 273 | 905 |
Table 1 shows that increasing rate of machines time is directly proportional to increased production of the face.
Ratio of machines time indicates the proportion of working time on the working face at coal mine[4–7]. For a larger face to reduce downtime for various reasons (cutter machine breakdowns, lack of stress, delays in the transport chain, collapsed roof rock in the working face, repair, and sections of mechanized roof supports in the long wall conveyor, seizure and attachment of niches, reducing the productivity of the transport chain in connection with unsatisfactory state of development workings, adjacent to the treatment and working face, etc.)[8–10].
Analysis of actual outages and development of measures to increase them, and, consequently, to increase the ratio of machine time will be made according to the report of the mine.
4.1 Gaseous factor.
Necessary to ensure the maximum load on the working face, which is limited to the terms of ventilation for gas-oil ratio.
4.2 The scheme of ventilation excavation of the section.
Maximum load on the working face of the gaseous factor. factor [1] is calculated as follows:
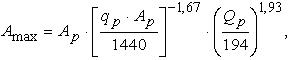
where:
Ар – the planned coal production, Ар = 450 т/сут;
qр – Relative methane, м3/т;
Qр – maximum flow of air into the development of waste water treatment (Qоч) or on the working areas (Qуч), which can be used to dilute the methane to acceptable dangerous values, м3/мин;
Maximum air flow is calculated by the formula:

where:
Vmax – the maximum allowable air velocity into the working face, м/с;
Fоч – section of the face, free for the passage of air, м2;
kут.в – coefficient taking into account leakage of air through the goaf.


where:
m – removable seam thickness based on rock layers, м;
f – the average coefficient of roof rock strength at a distance from the top layer is taken out equal 8m;
Expected production of methane from the waste water treatment scheme for the 1–M determined by the formula

where:
qпл – relative methane from the reservoir, м3/т;
kд.пл – coefficient of degassing reservoir kд.пл = 0,3 is selected as the scheme developed by degassing reservoir wells drilled to the rise of the haulage drift in columnar development system;
qв.п – the relative methane from adjacent layers and interlayers of host rocks in the explored face;
kд.в.п – coefficient of degassing sources of methane from the gob kд.в.п = 0,4 is selected as the scheme developed by degassing reservoir wells drilled on the dome collapsed rocks from the ventilation output.
Expected production of methane from the sewage, and the maximum possible load on the working face of the gas factor in the various schemes of ventilation and other conditions being equal are shown in Table 2.
A typical scheme the direction of the ventilation area | outgoing air stream | Qр, м3/мин | qр, м3/т.с.д. | Алг, т/сут |
1-М | on an array of | 638 | 8,56 | 866 |
1-В | on the goaf | 708 | 8,83 | 1009 |
2-В | on the goaf | 708,5 | 4,45 | 3160 |
3-В | on the goaf | 708,5 | 4,45 | 3160 |
In Table 2, the following notation: 1, 2, 3 – the type of ventilation schemes excavation site in the degree of isolation of the sources of methane diluted income (1 - with serial 2 – with a partially detached, 3 – with a completely isolated by diluting the hazard), M, B – indicate the direction of the outgoing stream of lava, respectively, in the direction of the array and the explored face.
Table 2 shows that the maximum possible load on the working face on the gaseous ratio is 3 times higher with co-current aeration scheme to with the influx of fresh air outgoing air stream than with the return air ventilation scheme. This is due to the fact that the scheme with the return air airing the maximum allowable concentration of methane in PB at the outlet of the lava is 1 %, and in co–current aeration scheme to with the return air outgoing air stream, the maximum allowable concentration of methane in PB at the outlet of the lava is 2 % [3]. Also important are the coefficients of the drainage layer and drainage sources of methane from the explored face. These factors affect the expected methane production and the treatment depends on the accepted method of decontamination.
Conclusion
Thus, to increase the production of working face, it is necessary to reduce downtime and implement advanced system design with co-current aeration scheme with the influx of fresh air excavation site and the outgoing air stream.
References
- Руководство по проектированию вентиляции угольных шахт: Учебник для всех организации и предприятий угольной промышленности при проектировании и реконструкции угольных шахт, включая строительство / С.В. Янко, С.П. Ткачук, Л.Ф. Баженова, А.И. Бобров, В.Е. Елисеев, Д.В. Еременко, А.Г. Заболотный, Н.Е. Именитов, Б.Н. Иотенко, Д.В. Кузьмин, В.П. Орлик, М.А. Патрушев, Г.М. Суслов – Киев; 1994 - С. 311.
- Технологія підземної розробки пластових родовищ корисних копалин: Підручник для ВНЗ. Частина II / Д.В. Дорорхов, В.І. Сивохін, О.С. Подтикалов. Під загальною редакцією Д.В. Дорохова. – 2-е вид., перероб., доповн. та перекл. – Донецьк: ДонНТУ, 2005. – 265с.
- Правила безопасности в угольных шахтах. – Х.: Изд. «Форт», 2010. – 256 с.
- Комплексная механизация и автоматизация очистных работ в угольных шахтах. Под общей ред. Б. Ф. Братченко. М., «Недра», 1977. – 415с.
- Способы отработки выемочных полей. Гусев Ю.В., Самойлов В.Л., Бондаренко Ю.В. – Донецк: ДУНВГО,2002. – 124с.
- Правила технической эксплуатации угольных шахт. – М.: Минуглепром Украины, Киев – 2006, 350 с.
- Указания по рациональному расположению, охране и поддержанию горных выработок на угольных шахтах СССР. – Изд. 4-е, дополнительное. – Л, 1986. – 222 с.
- Нагрузки на очистные забои действующих угольных шахт при различных горно-геологических условиях и средствах механизации выемки. – М.: ИГД им. А.А. Скочинского, 1991. – 48 с.
- СОУ10.1.00185790.011:2007. Підготовчі виробки на пологих пластах, вибір кріплення, способів і засобів охорони. – К.: Мінвуглепром України, 2007. – 113 с.
- Инструкция по безопасному ведению горных работ на пластах, опасным по внезапным выбросам угля, породы и газа М.: МУП СССР, 1989. – 191 с.