Abstract
Content
- Introduction
- 1. Relevance of the topic
- 2. The purpose and objectives of the research, the expected results
- 3. Review of existing polyolefin compositions and methods of analysis
- 3.1 Analysis of the current active time-layer polyolefin composition
- 3.2 Polyethylene, its properties
- 3.3 Methods for assessing three-layer coatings and their appropriateness
- 3.4 Cathodic protection
- 3.5 Adhesion
- 4. The results of their research and further development of the theme
- References
Introduction
Transportation of oil, gas and petroleum products by pipeline is the most efficient and safe way to transport them over long distances. This method of delivering oil and gas from the areas of their production to consumers for over 100 years. Durability and trouble-free operation of pipelines depends on the effectiveness of their corrosion protection. To minimize the risk of corrosion damage to pipelines corrosion protection coatings to protect and further electrochemical means. At the same time insulating coatings provide primary (passive) protecting pipelines from corrosion by acting as diffusion barrier through which hampered access to the metal korroziynoaktivnih agents (water, oxygen, air). When the defects in the coating provides for a system of cathodic protection of pipelines – active protection against corrosio.
To a protective coating to function effectively, it must satisfy a number of requirements, the main ones are: low влагокислородопроницаемость, high mechanical properties, high and stable over time coating adhesion to steel, resistance to cathodic delamination, good dielectric properties, resistance coating to UV and heat aging. Insulation coating shall perform its functions in a wide temperature range of construction and operation of pipelines, providing protection from corrosion to the maximum possible service life [1].
1. Relevance of the topic
That question arises in the fact that on the one hand, constantly improving the quality of protective coatings of pipelines, almost every 10 years, there are new insulation materials, new technologies and equipment for the coating of the pipe in the factory and field conditions. On the other hand, are becoming more stringent conditions for the construction and operation of pipelines (pipelines in the Far North, in Western Siberia, the development of offshore oil and gas fields, deep-laying, construction of pipeline sections methods directional drilling, mikrotonneliruvaniya exploitation piping temperatures up to 100C or higher, etc.) [2].
It should be noted that in the last 7-8 years, the overall level of corrosion protection of pipelines has increased significantly due to the introduction of new technologies, high-quality insulating materials, a wide use in the construction of pipelines pipes and fittings with factory coatings. One can also argue that the current coverage provided that the requirements for the construction and installation of pipelines are able to provide their flawless (due to corrosion) work for the entire period of operation (40-50 years or more).
This paper will discuss:
- The three-layer polyethylene coating, its composition. Its differences advantages of unlike-layer.
- Requirements polyethylene coating composition forms polyethylene. Polyethylene of high and low pressure, its properties.
- An assessment of the physical and mechanical properties of polyethylene coating OEMs and IPA in the central laboratory of PJSC HTZ.
2. The purpose and objectives of the research, the expected results
The aim of the study is to develop a polyethylene composition for steel that can withstand critical temperature operation.
The main objectives of the study:
- Analysis of three-layer polyethylene coating. Revealing its drawbacks and advantages.
- Investigate density polyethylene and high-pressure epoxy adhesive composition and choose the new quality cover.
- Assess existing methods of analysis and process improvement of a three-layer coating for steel pipes.
- Evaluate the physical and mechanical properties of polyethylene coating of high and low pressure.
- Analyze the coating characteristics such as adhesion and resistance to cathodic delamination.
- Suggest ways to improve the polyethylene composition.
object of study : a three-layer polyethylene coating.
subject of study : technological methods and systems to improve coverage for use in the Far North.
As part of the master plan to get topical scientific results span> in the following areas:
3. Review of existing polyolefin compositions and methods of analysis
Since the three-layer coating of steel pipes is a key issue, but now the issue is devoted to a number of universities of oil and gas, both domestic and foreign. Therefore, to be used in the scientific findings made in the last few years.
3.1 Analysis of the current active time-layer polyolefin composition
This section provides a description of the two-layer and three-layer polyethylene coating is carried out analiz.Vpervye single-layer polyethylene coating of pipes on the basis of polyethylene powder were introduced in the late 50's – early 60-ies of the last century. A single-layer coating technology polyethylene coating similar to the coating technology of epoxy powder paint. Because of the low water resistance and adhesion resistance to detachment of the cathode-layer polyethylene coating is not sufficiently known applications. They were replaced by two-layer coating with a soft adhesive sublayer. The design of the coating layer is applied as an adhesive insulating bitumen-rubber mastic (soft adhesives) with a thickness of 150-300 microns, applied over a layer of primer, and as an external shock resistant layer extruded polyethylene used a minimum thickness of 2,0-3, 0 mm [3].
For the first time three-layer polyethylene coating design has been developed and patented by the specialists of BASF and Mannesmann, Germany 20 years ago. The three-layer coating of MAPEK consists of a layer of epoxy primer with a thickness of 60 to 200 microns, the adhesive layer thickness of 200 to 500 microns and an outer plastic layer having a thickness of 1.5 to 3.0 mm. Depending on pipe diameter and the estimated destination pipelines coating-layer thickness can vary from 2.0 to 3.5 mm. Today, a three-layer polyethylene coating is the most effective external anticorrosion coating pipe factory naneseniya.Etot type of coating is widely used throughout the world for corrosion protection of pipelines for various purposes (gas pipelines, oil pipelines, product pipelines, pipelines and public utilities, etc.). With the right choice of insulation materials , with strict observance of technological modes of treatment and the outer pipe insulation design life of three-layer coating at temperatures of up to +60°C is not less than 50 years [4][5]. The growth of the world's oil and gas production will be inextricably linked with the complexity of the conditions of the fields: development of offshore hydrocarbon production sites and increased corrosiveness of funds being transported. Continuous market research now allows Khartsyzk Tubes (based on the master's work is done) to work actively for the development of promising new products.
Currently, the Center for basic insulation VNIIST tested more than 10 different systems, three-layer coating of pipes. Evaluation of the coating was carried out on 15 indices of properties including: a dielectric sploshnist, coating adhesion to steel, water resistant adhesion, resistance to detachment of the cathode, the impact resistance in a temperature range, resistance to cracking, to UV and thermal aging, and others. Despite the relatively high requirements of the Russian standard GOST R 51164, greatly exceed the requirements of the German standard OGM 30670 and 49710 French standard MRA, several systems of three-layer coatings withstood comprehensive tests have been recommended for practical use [6].
The best results were obtained when the test plant sandwich systems using epoxy powder paint companies BASF, 3 M, BS Coating, Akzo Nobel, the adhesive composition and the production of polyethylene Borealis, Basell, Atofina , UBE.
It should be noted that to date has not certified any system of three-layer coatings on the basis of domestic insulation materials. The problem is that the Ukrainian manufacturers of insulation materials work every man for himself, and for the development of the coating system requires an integrated approach. For a certain epoxy primer is required is exactly what is combined with an adhesive primer undercoat and polyethylene. This is to ensure that, when layered coating between the epoxy primer and adhesive underlayer could form chemical bonds that are resistant to water, excessive heat and prolonged exposure to electro-chemical protection. In addition, tests conducted VNIIST various domestic polyethylene compositions used in the Ukrainian factories for two-layer pipe insulation, have shown that these songs do not comply with the requirements of GOST R 51164 on parameters: resistance to stress cracking, thermal stability, flexibility in sub-zero temperatures [7].
Due to the fact that the three-layer coating system is used, typically high density polyethylene or a bimodal polyethylene, a two-layer coating is applied to a low density polyethylene coating sandwich impact strength 2-3 times the impact resistance of two-layer coatings. When the coating thickness of approximately 3 mm, the impact strength of the coating is 50-60 sandwich J, while the case of two-layer coating in impact strength is not more than 20 J.
Three-layer coating based on a bimodal polyethylene and high density polyethylene characterized by high mechanical strength. Tensile coating exfoliation at 20°C in this case is from 22 to 28 MPa, while the figure for the two-layer coating on low density polyethylene cable brands ranges from 11 to 13.5 MPa. Elongation at break at -40°C for domestic grades of polyethylene 102-10K 153-10°K does not exceed the 40 to 60%, whereas for imported brands of high-density polyethylene, the figure is 90-100%, and for the bimodal polyethylene dostigabelnogo polyethylene grades 102-10 and to 153-10 to cracking resistance is 200-500 hours. At the same time, resistance to cracking certified VNIIST imported polyethylene compositions used in the three-layer pipe coating systems, over 2000 hours, and in case of a bimodal polyethylene reaches values of 10000 h [8].
3.2 Polyethylene, its properties
Polyethylene – the cheapest polymer, ranked first in the world production of polyolefins. This unique material combines the valuable properties and are capable of handling all the high-performance methods that exist for thermoplastics.
Polyethylene – it's plastic, it has good dielectric properties, increased shock resistance, low absorbency. Do not break, have a low gas and water vapor permeability. Physiologically neutral, odorless. Polyethylene is not susceptible to any alkali concentration solutions of any salt, carbonic, hydrofluoric and hydrochloric acids. Resistant to oil, vegetable juices, alcohol, water, and gasoline. Destroyed by nitric acid, liquid and gaseous fluorine and chlorine. Insoluble, only slightly swells in organic solvents. Resistant to heat in a vacuum, but is destroyed when heated in air from eighty degrees.
Polyethylene frost (up to seventy degrees). Under the action of UV rays – exposed photodestruction. Can be easily modified. Additional chlorination, sulfonation, bromination or provide fluoridation polyethylene rubber – like properties, improve the chemical and thermal stability. Copolymerization with other polyolefin or polar monomers improves its transparency, flexibility, adhesion properties and resistance to cracking. Mixing polyethylene with other polymeric materials improves other physical properties. Polyethylene is harmless to humans, it does not stand out dangerous for his health matter. View of a molecule of polyethylene is shown in Figure 1.
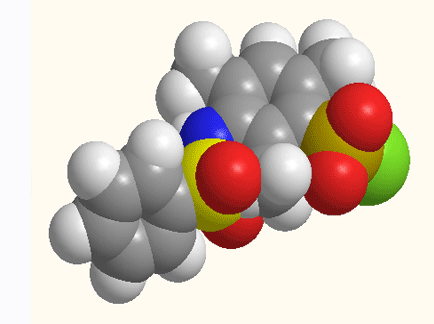
Figure 1 – A molecule of polyethylene
(Animation: 6 shots, 5 cycles of repetition, 150 KB)
(xi – inputs, yi – condition code bits, zi – outputs)
3.3 Methods for assessing three-layer coatings and their appropriateness
Indicators by which give an estimate of the polyethylene coating are:
- high corrosion resistance;
- high degree of adhesion to the base material;
- high impact resistance and resistance to the deforming effects of the transport and laying of pipes;
- high electrical resistance required for the corrosion protection and to prevent leakage current protective tube;
- cathode peeling resistance caused by the action of cathodic polarization;
- stability in time of physical, mechanical and chemical properties of the coating;
- good dielectric properties;
- resistance to UV radiation;
- resistance to thermal aging;
- a wide range of operating temperatures (ambient and pumped);
- long term efficient operation [9].
3.4 Cathodic protection
Shift potential of the metal may be done by using an external DC power source (cathodic protection station) or a compound with another metal, in its more electronegative electrode capacity (so-called sacrificial anodes.) The surface is protected by the sample (details of the structure) and becomes an equipotential at all sites occur only cathodic processes and anode that contribute to corrosion transferred to auxiliary electrodes. If, however, the potential shift in the negative direction exceeds a certain value, it is possible the so-called perezaschita associated with hydrogen evolution, changing the composition of the electrode layer and other phenomena that can lead to accelerated corrosion. Cathodic protection is usually combined with the application of protective coatings to be mindful of peeling of the coating.
3.5 Adhesion
Try on the equilibrium work of adhesion between the polymer and the solid in most cases it is not possible because of the very high viscosity polymers. Therefore, with respect to the polymers is determined not by the adhesion and adhesion durability. It is measured as the specific job or specific force the destruction of the relationship between the adhesive and the substrate. From a practical point of view, the use of polymers as adhesives or matrix for the PCM is important, not the work of adhesion and the mechanical strength of the bond of the polymer on the other poverhnostyu.Odnako mechanical destruction adhesive bonding work done in the two-body exfoliation, is not only to overcome the adhesion, but and other secondary processes (deformation body, overcoming the forces of mechanical linkages, etc.). Therefore, not only the magnitude but also the concept of adhesion and adhesive strength are not the same, and they must be clearly distinguished [10].
Methods for determining the adhesive strength very much. Their choice depends on what the load is subjected to an adhesive connection during operation. But these methods are three commonly used – is the adhesion strength at normal isolation (Figure 3. A) when detachment (Figure 3. P) and shear (Figure 3.B).
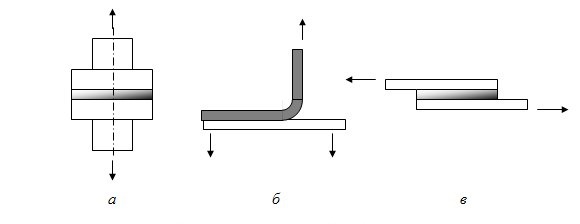
Figure 2 - Views adhesion strength
4. The results of their research and further development of the theme
Experiment number 1 – Determination of elongation and tensile strength.
Properties of the finished product is substantially polyethylene depends on the mode of manufacture (and uniform cooling rate), and, of course, their operating conditions (pressure, temperature, duration of load, etc.). Therefore, the laboratory analysis CFL subjected polyethylene coating, processed in an extruder. To be determined: meet the physical and mechanical properties of polyethylene GOST producer after processing in the extruder and how it will behave in service as coverage (at a temperature of 25 degrees and a load of 700 MPa). Also to be determined, it is possible to use polyethylene coating special naznacheniya. TU 27.2-00191135-009:2005 experiment will be extended to electric-welded steel pipes and cold-resistant expanded the usual run of diameter from 530 mm to 120 mm with an external three-layer polyethylene coating, designed to construction of underground main pipelines and subsea installation [11].
The experiment shows that the strength of the material – of low density polyethylene, high pressure is 26,727 MPa, while low density polyethylene high pressure – 17.04 MPa. There is a high density polyethylene strength 36.45% higher than low density polyethylene.
When choosing a polyethylene composition for the base layer of external three-layer polyethylene coating pipe gas and oil production of PJSC Khartsyzsk Tubes on the basis of this experiment, low-density polyethylene does not pass on technical requirements. It can only be used for the coating of normal, heat-resistant and cold-resistant coating. A polyethylene composition for coating a special design of high density polyethylene extends strength characteristics. According to a rate of 27.2 TU - 001911135-009:2005 tensile strength exfoliation of the coating shall be for 18 MPa for a special performance, and 12 MPa for the average [12].
Poor strength characteristics of high pressure polyethylene can be attributed to its molecular structure and physicochemical properties in particular. Feature of the structure of polyethylene LDPE is the large number of long and short branches, which do not allow the molecules with a high molecular weight to create a crystalline structure. Relations between them are not so strong, and it say about those that polyethylene has a low resistance to tearing and increased flexibility, as well as a high turnover in the melt.
Given the results of the experiment number 1, polyethylene coating for corrosion protective coating of a special type of high-density vibriaetsya brand HE 3450.The next requirement to cover the production of special purpose, ie for use in the critical temperature is high corrosion resistance, resistance to detachment of the cathode and a high degree to the base material clutch.
Experiment number 2 – Test polyethylene coating for resistance to cathodic delamination
Moving underground pipeline in the surrounding soil, and the effect of pressure on the part of the latter are the main causes of delamination of the coating. Prolonged exposure to cathodic polarization can also lead to delamination of the coating line – cathodic delamination. With unstuck linked most popular type of corrosion of pipelines – underfilm corrosion, and stress corrosion cracking.
At present, the problem of underfilm corrosion remains relevant still unclear role of cathodic protection in isolated detachments. Some experts believe that the protection provided by the cathode current flowing through the coating (essentially via the contact resistance of insulation) or through a medium that penetrates the coating may peel off other authors argue that cathodic protection has no little influence, and others – believe that the cathodic protection is the source of corrosive galvanic couples, ie its action under cover exclusively negative [13].
The experiment – to investigate the effectiveness of the cathode current in flaking of the coating and to determine its usefulness in keritichnih temperatures.
Materials for the test:
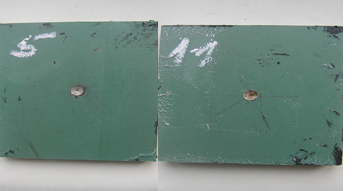
Figure 3 – Materials testing
From the results of the experiment revealed that, according to the requirements of TU 27.2 – 00191135-009:2005 results satisfy coverage requirements nomalno type of performance, ie, intended for the construction of pipelines by means of trench lining. Radius povingen detachment of not more than 4 mm at 20°C is not greater than 7 and at a temperature of 60°C.But if you use pipes analyzed in a three-layer coating 80°C, the resistance to detachment of the cathode is very weak. It is greater than the allowable 0.7. Is the temperature of the transported fluid as well as the environment can not be 80°C.
Results of experiments allow us to say that the optimum conditions in compliance with temperature 60°C and exposure to water, and 500 hours at 80–1000 hours. These values are included in the allowable to use a three-layer coatings in the normal version, but for the special conditions necessary to improve the quality parameters of adhesion and cathodic vidsharuvannya.Tse clearly demonstrate dependence in Figure 4.
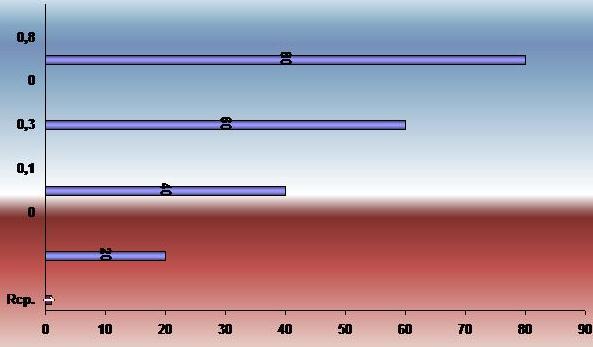
Figure 4 – The dependence of the cathodic delamination
Experiment number 3 – Determination of adhesion of the coating to the steel at different temperatures in the laboratory tests.
Adhesion between the primer and the material basis of a three-layer-coating steel to a rate of 27.2 TU – 00191135-014:2007 is satisfactory. According to experiments, it is at 20°C – 350HP (ie cohesive detachment) at 50°C – 235°K, at 60°C – 200°K. On the chart we can clearly see that as the test temperature decreases adhesion resistance. Upon exposure to water, from 500 to 1500 hours – performance decrease adhesion.
Optimally, the compliance with the conditions at a temperature of 60°C, and exposure to water, and 500 hours at 80–1000 hours. These values are included in the allowable to use a three-layer coatings in the normal version, but for the special conditions necessary to improve the quality parameters of adhesion.
The results of the experiment can be seen in Table 1.
Тable 1 – Adhesion strength after aging in water,
Т, ºС | Adhesion strength after aging in water, h | |||
0 | 500 | 1000 | 1500 | |
60 | 25а | 25а | 30 | |
160а-к(70:30%) | 58а | 55 | ||
150а-к(65:35%) | 102а | 5 | ||
340 | 112а-к | 62а | 30а | |
80 | 200 а-к(15-85%) | 277 а-к(40:60%) | 230 | |
210а-к(15-85%) | 262а-к(30:70%) | 223 | ||
210а-к(15-85%) | 255а-к(50:50%) | 185 | ||
340к | 207а-к(15-85%) | 265а-к(40:60%) | 212а-к(10: |
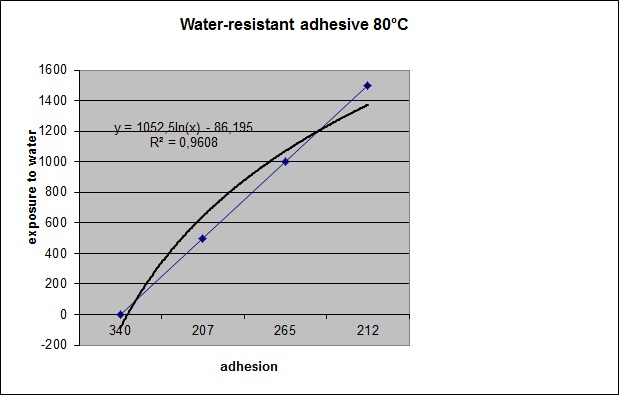
Figure 5 – Processing of the results of adhesive strength
All studies were conducted in the laboratory Khartsyzsky Pipe Plant.
Conclusion
As a result of this work was a three-layer polyethylene coating studied, its composition, its differences, the advantages of unlike-layer. Also discussed requirements polyethylene coating composition forms polyethylene, in particular high density polyethylene and low pressure, its properties. At the stage of the experiment evaluated the physical and mechanical properties of polyethylene coating OEMs and PND, the value of the cathodic delamination and adhesion of the coating.
been determined that it is a high density polyethylene and low pressure can be used for application as a polyethylene composition for the core layer-layer polyethylene coating special purpose gas and oil pipes. The experimental results of experiments cathodic delamination and coating adhesion indicate that the coating is not sufficiently high quality for use in temperaruri plus 80°C.
The analysis of the data means Microsoft Exel, the confidence score is determined between the calculated lines on the chart with the data. The conclusions for each experiment. Determined the main problem, the discrepancy in terms of coverage in terms of the critical temperatures, and as a result of further experiments will be carried out to fix it.
Master's thesis is devoted to actual scientific problem – improved three-layer polyethylene coating for use in critical temperatura the trials carried out:
- Designed composition polyolefin composition that satisfies the requirements of the German standard;
- Based on an analysis of literary sources allocated basic characteristics and drawbacks of the coating of steel pipes;
- Conducting a series of experiments to modernize a three-layer coating.
- Identified areas for further action on the master's work.
Further research is focused on the following aspects:
- Improving the coating of steel pipes for use in extreme temperatures.
- Identify further areas of experimentation.
- Checking coating developed in real Laboratories.
- Develop a program to automatically check the quality of the coating.
In writing this essay master's work is not yet complete. Final completion: December 2013. Full text rabotyi materials on the topic can be obtained from the author or his manager after that date.
References
- ТУ У 27.2–00191135–0225:2011 Трубы стальные электросварные прямошовные экспандированные с трехслойным наружным антикоррозионным полиэтиленовым покрытием для магистральных нефтепроводов.
- ГОСТ 11262–80 Пластмассы. Метод испытания на растяжение.
- ГОСТ 24297–87 Входной контроль продукции. Основные положения
- ГОСТ Р 51164–98 Трубопроводы стальные магистральные. Общие требования к защите от коррозии.
- ГОСТ 16337–77 Полиэтилен высокого давления
- ГОСТ 16338–85 Полиэтилен низкого давления
- ТУ У 14–8–23–2000 Трубы стальные электросварные прямошовные диаметром 530-1420 мм с наружным полиэтиленовым антикокоррозионным покрытием для подземной прокладки в различных климатических условиях.
- Методические указания по разделу «Охрана труда» в дипломных проектах и работах. Под редакцией Макарова Г.В. М.: МХТИ им.Д.И. Менделеева, 1990-29 с.
- Н.А. Кочетков, А.Ф. Бочков, Б.А. Дмитриев и др. Химия углеводов // М.: Химия. - 1967. - с.672.
- Лебедев Л.М. Машины и приборы для испытания полимеров, М., 1967.253с.
- Красноярский В. В., Электрохимический метод защиты металлов от коррозии, М., 1961;
- Фрейман Л.И., Макаров В.А., Брыксин Е. И., Потенциостатические методы в коррозионных исследованиях и электрохимической защите, Л., 1972;
- Люблинский Е. Я., Протекторная зашита морских судов и сооружений от коррозии, Л., 1979;
- Кузуб B. C., Глазов Н.П., Шамшетдинов К.Л. и др. Об измерении поляризационного потенциала на подземных стальных трубопроводах/ Практика противокоррозионной защиты – 2000, №2 – с.24-29.
- Зиневич А.М., Храмихина В.Ф. и др. Воздействие катодной поляризации на стальную поверхность под пленочным покрытием / Строительство трубопроводов – 1979. №8 – С. 25-27.
- Ортон М.Д. Измерение защитного потенциала трубопровода в местах отслоения изоляционного покрытия. / Нефть, газ и нефтехимия, №3, 1986, С. 72-75.
- Закон Украины «Об охране труда» 2694-12 от 14.10.1992;
- «Правила охраны труда в трубном производстве», утвержденных приказом комитета Украины по промышленной безопасности, охране труда и горному надзору от 15.10.2009 №171, зарегистрированных в Министерстве юстиции Украины 05.11.2009 за № 1037/17053.
- «Правила охраны труда в металлургической промышленности», утвержденных приказом Государственного комитета Украины по промышленной безопасности, охране труда и горному надзору от 22.12.2008 №289 , зарегистрированных в Министерстве юстиции Украины 29.01.2009 за №87/16103
- «Положения о разработке инструкций по охране труда» НПАОП 0.00-4.15-98, утвержденного приказом Министерства труда и социальной политики Украины №9 от 29.01.1998, зарегистрированного в Министерстве юстиции Украины 07.04.1998 за №226/2666.
- Электронный журнал: физикохимия поверхности и защита материалов [электронный ресурс]. – Режим доступа: http://maik.rssi.ru...
- Электронный журнал: Территория нефти и газа, [электронный ресурс]. – Режим доступа: http://neftegas.info...