Реферат по теме выпускной работы
Содержание
- Введение
- 1. Актуальность темы
- 2. Цели и задачи исследования
- 3. Состояние коксохимической промышленности Украины
- 4. Состояние зарубежного коксохимического производства
- 5. Экологизация коксохимического производства
- 5.1. Разновидности и источники образования вредных выбросов коксохимии
- 5.2. Повышение эффективности существующей технологии подготовки и коксования углей
- 5.3. Снижение вредных выбросов путем совершенствования технологии охлаждения кокса
- Заключение
- Список источников
Введение
Повышение качества основной продукции коксохимии — металлургического кокса является одним из основных направлений сокращения вредных выбросов в доменном и коксохимическом производствах. Это связано, в частности, с возможным сокращением потребления, а, следовательно, и производства кокса улучшенного качества.
Резкое ужесточение экологических требований к коксохимическим предприятиям, основным агрегатам и оборудованию, которые выработали свои нормативные сроки эксплуатации, морально и физически устарели, стало требовать от коксохимиков концентрации усилий для реконструкции и технического переоснащения предприятий по решению вопросов охраны воздушной и водной среды. Поэтому совершенствование технологических процессов коксохимического производства должно осуществляться на основе комплексных эколого-экономических оценок.
1. Актуальность темы
Актуальность данной темы обусловлена тем, что в настоящее время в Украине функционирует 13 крупных коксохимических предприятия, 7 из которых сосредоточены в Донецкой области. Экологические проблемы усугубляются еще и тем, что эти предприятия расположены в регионах со значительной концентрацией промышленного производства и высокой плотностью населения. Крайне неблагоприятная экологическая обстановка, сложившаяся в последние годы в крупных металлургических центрах, в определенной степени обусловлена низкими темпами технического перевооружения коксохимической подотрасли, медленным внедрением в практику новых технологических процессов, современных агрегатов и оборудования [1].
Коксохимическое производство занимает «ведущее» место по разнообразию, высокой токсичности и специфическому удушающему запаху многих газообразных выбросов, сбросов и твердых отходов. К ним относят пыль, оксиды азота, диоксид серы, оксид углерода, аммиак, фенол, бензол, нафталин, сероводород, цианистый водород и графит. Поэтому важнейшей социальной задачей, стоящей перед коксохимическими предприятиями, является повышение экологической безопасности производства, техническое переоснащение коксохимических предприятий, осуществление крупномасштабной программы строительства природоохранных объектов, внедрение современных экологически безопасных технологических процессов.
На современных заводах внедряют передовые технологии, позволяющие снизить выбросы загрязняющих веществ в атмосферу. К основным из них относят установки бездымной загрузки угольной шихты в камеры коксования, установки беспылевой выдачи и сухого тушения кокса. Однако, в последнее время все большую актуальность приобретает совершенствование технологических процессов на всех стадиях производства кокса (подготовка, загрузка, коксование углей, выдача, охлаждение и сортировка кокса). Этим стадиям производства кокса принадлежит сейчас более 70 % залповых выбросов. При разработке и внедрении природоохранных мероприятий особое внимание также обращают на обновление коксовых батарей.
Повышение качества основной продукции – металлургического кокса является одним из наиболее перспективных направлений экологизации коксохимического и доменного производств. При использовании в доменной плавке более качественного кокса значительно уменьшается потребность в нем, а следовательно появляется возможность вывода из эксплуатации изношенных коксовых батарей с естественным снижением производства кокса и убылью сопряженных с ним выбросов, сбросов и твердых отходов.
Наилучшие мировые технологии предполагают совершенствование процессов подготовки шихты: трамбование угольной шихты перед загрузкой в коксовые печи и регулирование ее влажности.
Исходя из сказанного, снижение вредных выбросов на всех стадиях производства кокса является актуальной задачей.
2. Цель и задачи
Целью является исследование технологических процессов и определение рациональных технологий производства кокса, позволяющих повысить качество кокса и одновременно сократить вредные выбросы.
Для достижения поставленной цели необходимо решить такие задачи:
- Изучить современные отечественные и зарубежные технологии производства кокса;
- Рассмотреть возможные способы экологизации традиционной технологии коксования;
- Проанализировать различные методы подготовки угольной шихты к коксованию и определить оптимальный состав сырья нужного качества;
- Дать характеристику факторам, влияющих на основные характеристики металлургического кокса, и разработать предложения по улучшению качества кокса;
- Поиск оптимальных путей совершенствования технологических процессов производства кокса;
- Рассчитать экономический и экологический эффект от внедрения технологии производства высококачественного кокса.
Объект исследования: существующие технологии производства кокса в коксовых батареях
Предметом исследованияявляются технологические процессы производства кокса и методы улучшения качества исходного сырья.
3. Состояние коксохимической промышленности Украины
Коксохимическая промышленность является одной из основных подотраслей горно-металлургического комплекса (ГМК) Украины и предназначена обеспечивать доменное производство необходимым количеством кокса, а также широким спектром продукции для химической отрасли, цветной металлургии и др. Из 81 млн. т рядового угля, добытого в Украине, 37,5% приходится на долю коксующегося.
В стране работают 14 коксохимических предприятий (КХП), на которых в эксплуатации находятся 57 коксовых батарей. Их средний возраст составляет 24 года. 63% от общего количества печей имеют срок эксплуатации более 20 лет (нормативно-амортизационный срок батарей), а 20% – свыше 35 лет.
Основные фонды коксохимическогo производства в большинстве своем выработали эксплуатационный потенциал, физически и морально устаревшее основное и вспомогательное оборудование не отвечает современным требованиям и достижениям мировой науки и практики в области охраны окружающей среды, труда и техники безопасности.
Основным направлением в решении проблемы защиты окружающей среды является совершенствование технологических процессов с доведением их до безотходного или малоотходного производства. Однако, учитывая, что существующая технология коксования сохранится в ближайшие годы, основной задачей по защите окружающей среды в коксохимическом производстве является вывод из эксплуатации устаревших агрегатов и оборудования и замене их современными, оснащенными эффективными природоохранными установками.
Наиболее остро стоит проблема качества кокса. Низкое качество отечественного кокса является основной причиной его перерасхода в доменном производстве. Согласно рейтингу качества кокса различных стран и фирм, выполненному украинской ассоциацией производителей чугуна и мнению основных потребителей, коксохимические предприятия Украины производят худший в мире кокс, как по прочностным характеристикам, так и по химическому составу.
Украинский кокс не соответствует мировым стандартам по химическому составу (он имеет более высокое содержание серы – 1,3-1,5%), техническим характеристикам (зольность – 10-12%), а также прочностным свойствам, которые оцениваются показателями холодной прочности М40 , М25 и истираемости М10. В мировой практике в качестве основных показателей качества все чаще используют определяемые по методу фирмы «Ниппон Стил» реакционную способность (CRI) и термомеханическую прочность (CSR) — прочность нагретого до 1100 °С кокса после его взаимодействия с диоксидом углерода.
По европейским стандартам высококачественный доменный кокс должен иметь следующие показатели:
— высокую прочность в холодном состоянии М40 > 80% при М10 < 7,0 %;
— низкую реакционную способность CRI < 25-30%;
— высокую прочность в горячем состоянии CSR > 60-70%.
Согласно исследованиям УХИНа, качество украинского кокса, получаемого из обычного сырья, при оценке по методу «Ниппон Стил», почти в два раза ниже качества кокса зарубежных фирм Германии, Австрии, а также России [2].
Украинский государственный научно-исследовательский углехимический институт выполняет большой комплекс работ по природоохранной тематике для коксохимических предприятий Украины. Так, разработаны отраслевые удельные выбросы (показатели эмиссии) для основного производства КХП, а также непосредственно для конкретных предприятий; технологические нормативы выбросов из коксовых печей, оборудования помола угля и производства углехимических продуктов коксования. На основании комплексных исследований по выбросам загрязняющих веществ из дымовых труб коксовых и пекококсовых батарей, котельных установок, работающих на коксовом газе, а также из других источников нами предложены технологические нормативы для действующего оборудования с учетом его возраста и технического состояния. Разработаны перспективные технологические нормативы с учетом строительства новых коксовых батарей и нормативов, установленных для аналогичных производств в европейских странах.
Большой объем работ выполняется по инвентаризации выбросов загрязняющих веществ с рекомендациями по их снижению, по разработке обосновывающих документов для получения разрешения на выбросы загрязняющих веществ.
В ближайшей перспективе планируется внедрение технологии по вдуванию не менее 5 млн. т в год пылеугольного топлива в доменную печь, что приведет к уменьшению потребления кокса на 4 млн. т. Предполагаемое сокращение производства кокса должно обеспечить уменьшение валовых выбросов до 15 тыс. т в год. Очистка коксового газа от сероводорода до 0,5 г/м3 на большинстве коксохимических заводов снизит выбросы сернистого ангидрида более чем на 5 тыс. т. Оптимизация производства кокса позволит полностью исключить неквалифицированное использование избытков коксового газа, так как весь он будет расходоваться на обогрев коксовых батарей и другого топливоиспользующего оборудования, производство пара и электроэнергии.
Техническая политика коксохимической подотрасли основывается на постоянном внедрении последних достижений в области технологии коксования и переработки углехимических продуктов с обязательной разработкой природоохранных мероприятий, что позволяет существенно снизить экологическую нагрузку на население и окружающую среды в городах, где расположены коксохимические предприятия [3].
4. Состояние зарубежного коксохимического производства
Традиционная технология производства кокса в печах камерного типа с косвенным обогревом в результате постоянных усовершенствований на протяжении всегo периода своего развития достигла к настоящему времени практически предельного уровня технического прогpесса. Основными достижениями современного коксохимического производства являются:
— высокая единичная мощность коксовых батарей (l,0 – 1,2 млн т/год) в результате увеличения габаритов коксовых печей (полезный объем печной камеры достигает 70–80 м3, высота увеличена до 7,85 м, длина — до 18 м, ширина — до 620 мм);
— освоение эффективных процессов подготовки угольной шихты к коксованию (частичного брикетирования, подсушки и термической подготовки, требования, контролируемого избирательного измельчения и др.), что обеспечило улучшение качества получаемого кокса и дало возможность снизить расход дорогостоящих хорошо спе¬кающихся углей и затраты на шихту в результате увеличения доли слабоспекающихся и неспекающихся углей в шихтах для коксования;
— повышение уровня автоматизации производства кокса, что позволяет решать проблему обеспечения коксохимического производства обслуживающим персоналом;
— сокращение примерно на 40 % энергозатрат на производство кокса в результате применения технологии сухого тушения кокса и освоения других энергосберегающих технологий (в том числе внедрения автоматизированных систем управления тепловым режимом коксования);
— разработка и внедрение новых технологий, предотвращающих или сокращающих образование пылегазовых выбросов на коксовых батареях, а также оснащение коксовых батарей эффективным пылеулавливающим и газоочистным оборудованием с целью максимально возможной степени защиты окружающей среды (на современных батареях практически на 100 % устранены выбросы при загрузке коксовых печей; с 0,5-1,0 кг/т до менее 5 г/т снижены выбросы пыли при вьдаче кокса из печей; сокращены объемы неорганизованных пылегазовых выбросов) [4].
В области науки, техники и технологии коксохимического производства бесспорным лидером научно-технического прогресса является Германия. В других странах Западной Европы коксохимическое производство также пере¬живает стадию серьезной реорганизации, хотя стратегическая концепция здесь отлична от германской. Если процесс структурной перестройки в Германии шел по пути строительства новых коксовых батарей высокой производительности и технического уровня, то другие страны Евросоюза (Бельгия, Нидерланды, Испания, Франция, Италия, Швеция, Великобритания) провели (или проводят) перестройку коксовой отрасли, главным образом, путем ремонта и реконструкции действующего печногo фонда.
В последнее десятилетие развитие коксохимического производства Японии xapaктеризуется прогpессирующим снижением производственных мощностей в условиях их избытка и eстественного старения печного фонда (после 1982 г. новые батареи в стране не вводили). Значительный прогресс в коксохимическом производстве Японии достигнут в тexнологиях, обеспечивших расширение сырьевой базы коксования и продление эффективного срока службы коксовых печей. Среди технологий, обеспечивших увеличение использования слабспекающихся и полуспекающихся углей в шихтах для производства кокса, в Японии, кроме внедренных в 70-80-e годы технологий подготовки шихты к коксованию путем ее частичного брикетирования (на 16 коксовых батареях), избирательного дробления (на четырех батареях), термоподоготовки (на одной батарее), в 90-e годы получила дальнейшее распространение эффективная технология СМС peгyлирования влажности угольной шихты путем ее частичной подсушки (применяется на 22 коксовых батареях) [5].
5. Экологизация коксохимического производства
5.1. Разновидности и источники образования вредных выбросов коксохимии
Технологическая схема производства кокса заключается в следующем: выбранные угли просеивают, размалывают до размера < 3 мм и смешивают в зависимости от их петрографии для производства высококачественного кокса из наиболее эффективных по стоимости углей. Смесь загружают в печные камеры, где кокс формируется благодаря разрушающей дистилляции угля при температурах 1100 °C и выше. По окончании цикла коксования горячий кокс выталкивается из печи в вагон для тушения, который транспортирует его к башне тушения для охлаждения и стабилизации. Тушение проводится при помощи воды (мокрое тушение) или азота (сухое тушение). Затем кокс транспортируется к доменной печи или укладывается в штабеля [6]. Упрощенная схема процесса производства кокса приведена на рис. 1.
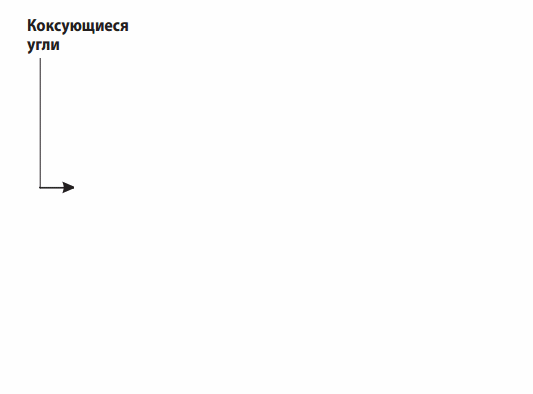
Рисунок 1 – Технологическая схема производства кокса
Основной комплекс технологических процессов коксовой батареи (подготовка, загрузка, коксование шихты, выгрузка, тушение и обработка кокса) является источником 75-80% и более выбросов коксохимического производства, 30% образуется в отделениях обработки коксового газа.
Коксохимическое производство занимает ведущее место по разнообразию и токсичности газообразных выбросов, сбросов и твердых отходов. Если при производстве окускованного рудного сырья (агломерата и окатышей), чугуна, стали, проката контролируют в основном выбросы пыли, оксидов углерода, серы и азота, то в коксохимическом производстве дополнительно определяют концентрации в технологических, аспирационных газах и атмосферном воздухе еще минимум 7-10 вредных веществ: аммиак, сероводород, фенол, бензол, цианистый водород, нафталин, сажистый углерод.
Отделения подготовки и коксования угля являются основными источниками газопылевых выбросов. Загрязненные сточные воды формируются в основном в отделениях обработки «грязного» коксового газа и, в существенно меньшей степени, в цехах переработки химических продуктов коксования.
Отделения специальной подготовки угля, включающей процессы складирования, усреднения, дробления, дозирования, обогащения, смешивания и транспортировки углей, характеризуется, главным образом, большим пылевыделением, достигающим 480-500 г/т кокса. При обогащении углей образуется до 35-40% от их массы твердых отходов, из которых 30-50% составляет отходы флотации – угольные шламы с влажностью до 50-60%.
Загрузка угольной шихты с влажностью 7-9% и более в раскаленные коксовые печи с температурой греющих стен 1100-12000С сопровождается образованием залповых выбросов парогазовой смеси в количестве 3-5м3/т шихты, уносящей в атмосферу вредные вещества, в количестве, г/т кокса: 400 пыль; 46 СО; 22 Н2S; 17NH3; 0,6 HCN; 1,1 C6H5OH; 190 CnHm; 32 SO2 и 55 NOx.
Очень важна правильная эксплуатация коксових печей. Нарушение режимов нагрева, несолюдение пропорций, правильной шихтовки, т. е. планирования угольной шихты и недоведение до конца процесса коксования, все это может привести к зносу печи, образованию трещин и прогаров в кладке стен. В этом случае значительное количество газа из камер коксования попадает в отопительную систему. Углеводороды прямого коксового газа в отопительной системе разлагаются с образованием Н2 и сажистого углерода. В результате из дымовых труб коксових батарей удаляются газы, окрашенные густым черням цветом сажи, которая является очень концерогенной.
Выдача кокса из камер коксования в тушильный вагон приводит к залповым, в течение 30-40с газопылевым выбросам, г/т кокса: 750 пыль; 7,6 H2S; 51 NH3; 0,5 C6H5OH; 22 SO2; 3,6 NOx; 36 CnHm, 0,1 HCN. При движении тушильного вагона с выгруженным из печи горящим коксовым спеком к установке мокрого или сухого тушения в атмосферу выделяются вредные запыленные газы в количестве примерно 100 м3/т кокса. Концентрация отдельных загрязнителей в этих газах составляет, г/м3: 110 пыль; 31 CO; 16 SO2; 0,2 Н2S; 2,9 NOx; 70 CnHm. Многие другие ингредиенты выбросов не исследованы [7].
5.2. Повышение эффективности существующей технологии подготовки и коксования углей
Главным направлением дальнейшего роста эффективности коксового производства становится eгo интенсификация. Согласно теории слоевого процесса, в основу технологических решений для этой цели должны быть положены разработки, способствующие повышению спекаемости углей, снижению общей напряженности в коксуемой массе, получению кокса однородной структуры. В наибольшей степени этим условиям отвечает избирательное измельчение с пневмосепарацией и термическая подготовка шихт.
Раздельное, последовательное осуществление при подготовке угольной шихты к коксованию, сначала, путем ее избирательного измельчения с пневматической сепарацией, а затем – термическим нагревом нерационально, так как: при нагреве измельченной шихты газовым теплоносителем с неизбежным остаточным кислородом, в присутствии паров воды, происходит окисление вновь образованной поверхности зерен углей, что снижает их спекаемость: неравномерно нагреваются разные классы крупности [8].
Одним из направлений интенсификации коксохимического производства на основе научно-технического прогресса являются глубокая сушка и термическая подготовка углей. Глубокая сушка связана с удалением практически всей свободной влаги, а термическая подготовка — это нагрев шихты до 150-250 °С. В результате глубокой сушки и термической подготовки шихты для коксования происходят существенные изменения ее свойств, что непосредственно влияет на ход коксования, механизм термохимических превращений угольной загрузки и качество кокса.
Основной целью термической подготовки углей и шихт является повышение производительности коксовых печей и вовлечение в сырьевую базу коксования слабоспекающихся углей. Неизменный состав шихты способствует улучшению качества кокса и повышению газопроницаемости его насыпной массы. При этом эффект влияния термической подготовки тем значительнее, чем хуже спекаемость углей. Например, при термической подготовке углей марок Г и ОС газопроницаемость насыпной массы кокса увеличивается соответственно на 23 и 13,6 %, в то время как термическая подготовка угля марки Ж способствует увеличению газопроницаемости кокса всего лишь на 4 %. Аналогичная картина наблюдается и для шихт. Если при термической обработке шихты с участием углей Г 6 + ОС 70 % газопроницаемость кокса увеличивается на 23 %, то для кокса из шихты с участием угля марки Г 6 26 % этот показатель увеличивается только на 1 3 %. [9].
Внимание, которое уделяется этому методу, объясняется тем, что при его реализации создается возможность: значительно интенсифицировать процесс слоевого коксования — повысить производительность коксовых печей; использовать в шихте для коксования значительно больше слабоспекающихся углей; улучшить технико-экономические показатели производства кокса при некотором повышении его качества.
Кроме указанных основных преимуществ этого метода можно еще назвать снижение расхода теплоты на коксование, уменьшение термических ударов на огнеупорную кладку камер коксования, снижение нагрузок на конденсационную аппаратуру химических цехов в связи с уменьшением количества водяных паров в коксовом газе, а также значительное сокращение количества сточных вод.
Метод термической подготовки углей перед коксованием является одним из наиболее эффективных среди других новых методов интенсификации производства кокса. Нагретая до 200-2500С шихта теряет более 90% влаги, и насыпная плотность её увеличивается на 15-20%.
Наиболее резко повышается насыпная масса трамбованием шихты. В трамбовочную машину слоями загружается измельченная шихта, а получаемый угольный блок вдвигается в камеру коксовой печи. Если при обычной загрузке насыпью можно достичь насыпной массы до 0,85 т/м3, то плотность трамбованного угольного блока составляет 1,0-1,1 т/м3. Трамбование шихты существенно влияет на коксуемость: уменьшается крупность кусков, увеличивается прочность тела кокса, изменяется трещиноватость.
5.3. Снижение вредных выбросов путем совершенствования технологии охлаждения кокса
Первым процессом подготовки кокса для доменних печей является охлаждение (тушение) до температур, при которых возможны его транспортирование и сортировка. При тушении свойства кокса изменяются. Следовательно, тушение представляет собой первый посткоксовальный процесс формирования свойств доменного кокса.
Известны два способа тушения: сухое и мокрое. Установки сухого тушения и мокрого тушения кокса представлены на рис. 1, 2. Мокрое (охлаждение кокса водой) стали применять с появлением процесса производства кокса. Этот способ пока еще применяется на предприятиях Украины, хотя во многих отношениях является отсталым. Более прогрессивным является сухое тушение кокса – постепенно внедряется в практику на зарубежных и отечественных предприятиях [10].
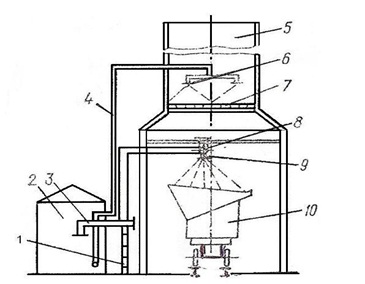
1 – колонна с опорой под трубопровод; 2 – насосная тушильной башни; 3 – трубопровод для подачи воды на тушение; 4 – трубопровод для подачи воды на промывку насадки каплеотбойника от коксовой пыли; 5 – тушильная железобетонная башня; 6 – форсунки для промывки насадки каплеотбойника; 7 – деревянная насадка каплеотбойника; 8 – коллектор оросительного устройства; 9 – форсунка оросительного устройства; 10 – тушильный вагон.
Рисунок 2 – Схема установки мокрого тушения кокса
Мокрое тушение кокса имеет ряд крупных недостатков, среди которых: громадные вредные выбросы, сниженная, из-за резкого охлаждения, прочность, повышенная и непостоянная влажность товарного кокса, полная утрата теплоты раскаленного кокса. Выход запыленных парогазовых выбросов от установок мокрого тушения кокса достигает 600 – 650 м3/т кокса, удельные выбросы в среднем составляют, г/т кокса: 20 H2S; 42 NH3; 89 C6H5OH; 9 HCN.
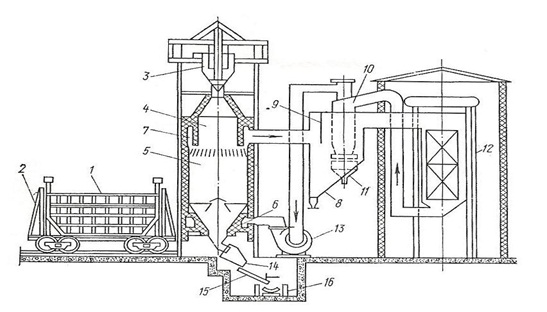
1 – тушильный вагон; 2 – направляющие стойки; 3 – загрузочное устройство; 4 – форкамера; 5 – камера тушения; 6 – газокамера; 7 – кольцевой отвод газов; 8 – пылеосадительная камера; 9 – перегородка; 10 – циклон; 11 – бункер циклона; 12 – котел-утилизатор; 13 – дымосос; 14 – разгрузочное устройство; 15 – коксовая рампа; 16 – транспортер
Рисунок 3 – Схема установки сухого тушения кокса
Циркулирующий газ представляет собой смесь горючих и негорючих составляющих. Появление горючих компонентов в газе обусловлено реакциями первично образовавшихся продуктов горения с раскаленным коксом, а также выделением етучих веществ кокса в камере УСТК. Количество СО в газе может увеличиваться до 23-24%. Горючие компоненты в значительной степени затрудняют эксплуатацию УСТК, делают установку взрывоопасной, а газ высокотоксичным.
Утилизация тепла немаловажное, но не единственное достоинство способа сухого тушения. Сухое тушение кокса имеет следующие эколого-экономические преимущества:
1) отсутствие выбросов ядовитой паро-газопылевой смеси в атмосферный воздух;
2) отсутствие стоков загрязненных токсичных вод в систему оборотного водоснабжения;
3) значительное улучшение качества кокса: снижение от 3-5 до 0,3-0,4% влажности, стабилизация ее уровня, повышение прочности, улучшение гранулометрического состава кокса.
Несмотря на преимущества УСТК, во многих случаях отечественной практики мокрое тушение продолжают использовать как основной или резервный вариант охлаждения кокса. В последние годы установки мокрого тушения существенно модернизировали, применив импульсное орошение кокса тонкораспыленной водой, охлаждение кузова тушильного вагона снизу, отвод паро-газопылевой смеси в атмосферу через диффузорно-конфузорную вытяжную трубу, изготовленную, как и вся установка, из железобетона. Однако, основная цель преобразования коксохимического производства - полное выведение из эксплуатации установок мокрого тушения кокса [11].
Заключение
В связи с дефицитом энергетических ресурсов в Украине развитие и освоение техники сухого тушения кокса приобретает особое значение и актуальность. Широкое внедрение этого процесса в коксохимическом производстве позволит существенно улучшить экологическую обстановку в промышленных центрах и условия труда на коксохимических предприятиях, уменьшить потери от коррозии оборудования, значительно повысить качество кокса.
Появляющиеся в ближайшие 8-10 лет возможности по существенному сокращению потребления производства кокса и заменой его пылеугольным топливом (частично антрацитом, коксовым, природным газом), целесообразно использовать для сноса старых, строительства новых коксовых батарей, модернизации технологии производства кокса с целью улучшения его качества и практически полной ликвидации газопылевых выбросов на всех стадиях коксохимического производства
Список источников
- В. И. Рудыка, Трембач Т. Ф., Каменюка В. Б. Защита окружающей среды: основне мероприятия и их эффективность // Кокс и химия. – 2003 – №12 – С. 34-35.
- Анализ сырьевой базы металлургического производства. Стратегический аспект. Кокс доменный / Л. Ю. Назюта, Н. В. Косолап, А. В. Губанова // Металл и литье Украины . - 2005. - № 11-12. - С. 3-9.
- Ковалев Е.А. Коксохимические предприятия Украины и проблемы экологии // Деловой вестник. - 2008. - № 3 [Электронный ресурс] – Режим доступа: http://www.ucci.oгg.ua/synopsis/dv/2008/dv0803161.гu.html.
- Ухмылова Г. С. Современное состояние коксохимического производства // Приложение №3 к журналу «Новости черной металлургии за рубежом». – 2000 – с. 10 – 18.
- Антонов А. В. Технический прогресс в технологии производства кокса в Китае // ОАО «Черметинформация». Новости черной металлургии за рубежом – 2010 г., – № 4 — c. 10 – 12.
- Товсей П., Камерон Я., Гордон Я., Красавцев А. Сравнение технологий производства кокса рекуперативного типа и с улавливанием побочных продуктов коксования // Кокс и химия. – 2013 – №1 – С. 9.
- Черная металлургия и охрана окружающей среды: учебное пособие / И.М. Мищенко. – Донецк.: ГВУЗ «ДонНТУ», 2012. – c. 97-103.
- Научные основы совершенствования техники и технологии производства кокса. Сухоруков В. И. Екатеринбург. 1999 г. – с. 273-280.
- Перспективные нaпpaвлeния развития коксохимического производсва. Браун Н. В.,Глущенко И. М. – М.: Металлургия, 1989. С. 59-70.
- Мучник Д. А. Перспективы совершенствования внекамерных процессов производства кокса // Кокс и химия. – 2011 – №3 – С. 45-49.
- Мучник Д. А. Анализ состояния вопроса сухого тушения кокса // Кокс и химия. – 2011 – №2 – С. 23-31.
Важное замечание
При написании данного автореферата магистерская работа еще не завершена. Окончательное завершение: декабрь 2013 г. Полный текст работы и материалы и материалы по теме могут быть получены у автора или его руководителя после указанной даты.