Abstract
Contents
- 1.Characteristics of Makeyevka city.
- 2. Overview of Open Joint Stock Company (OJSC)
Yasynovka Chemical Plant
. - 2.1 Characteristics of PJSC
Yasynovka Coke Plant
as a major source of air pollution. - 2.2 Description of the main sources of pollution in the hydrosphere.
- 2.3 Management of solid and liquid waste products.
- 3. Characteristics of waste products to the Department of condensation.
1. Characteristics of Makeyevka city.
Makeyevka is a large administrative industrial and cultural center of south-east Ukraine.Makeyevka is a typical industrial city where the metallurgists and the miners have been essential for more than two hundred years. On the city territory there are more than 4 thousands companies. Among the main production are metallurgy and metalwork, coke plants, coal mines, processing factories, machine-building enterprises, light industry, food industry and agricultural enterprises.
Basic industries in the city are: metallurgy and metal processing, coking and coal industry, food industry and processing of agricultural products, and machine building.
The total sales of the business industries are almost 95%. Industries in Makeyevka provide 6.5% of the total production in the Donetsk region. City gives more than 3% of exports commodities and products of the region, it accounts for about 13% of foreign investment in the regional economy.
2. Overview of JSC Yasynivskyi Chemistry Plant
The PJSC "YCP" - a modern enterprise, dynamic and full of coke production cycle. The plant is developed and implemented a comprehensive program of strategic development company in 2015, providing a further increase in production of coke and chemical products using new environmentally friendly technologies.
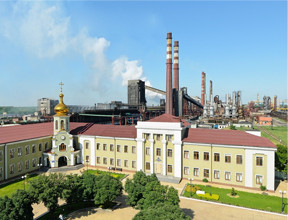
Image 1 – Yasynivskyi Chemistry Plant
The principal production facilities of the plant are:
- the coal preparation plant;
- the coke plant consisting of six coke oven batteries (to use KB - 1, 3, 5, 6);
- the workshop for trapping chemical products
- workshop for cleaning coke oven gas desulfurization;
- distillation - a gas workshop;
- combined Heat and Power (CHP)
The structure of auxiliary includes departments: Automotive, Energy, Railway, mechanical, repair - construction, repair Coke equipment and the Central plant laboratory (CPL), the Military-technical control (MTC) and factory management. The main industrial products are coke 6% moisture and Related Product Manufacturing coke oven gas: coal tar, ammonium sulphate 20% moisture, crude benzene.
2.1 Characteristics of PJSC "YCP" as a major source of air pollution
The PJSC "Yasinovka Coke Plant" has the following basic technological units: Coal preparation, coke, catching, cleaning coke oven gas desulfurization, distillation of crude benzene.Auxiliary units include: power plants, repair mechanical, repair building, motor department, railway department.The Coal preparation plant is appointed for receiving and storing, dispensing and crushing of coal, mixing and delivery charge for coking coal in a coke plant.
The Coke plant has a composition of three coke batteries: ¹ 1 (61 furnace chamber effective volume 21.6 ) and ¹ 5,6 (over 77 furnaces with a useful volume of 30.0 chamber). Workshop trapping chemicals coking where the coke oven gas cooling and cleaning it from ammonia and benzene carbohydrates followed by obtaining resin, ammonium sulfate and benzene carbohydrates.
Workshop distillation of crude benzene is designed to clean coke oven gas desulfurization with standard established specifications.The PJSC "Yasinovka Coke Plant" according to an inventory identified 120 sources of pollutants, including 106 from the primary production from 14 complementary.In the Coal preparation plant - 14 emission sources are organized 7.In the coke plant - 37 emission sources, of which 6 are organized.For sources are organized stacks coke oven batteries, SEI on coke sorting plant without dust coke oven battery ¹ 1.Unorganized sources include - loading coal charge, coke, coke oven door leaks batteries, manholes and pipes, quencher wagons, quencher towers, coke ramps.
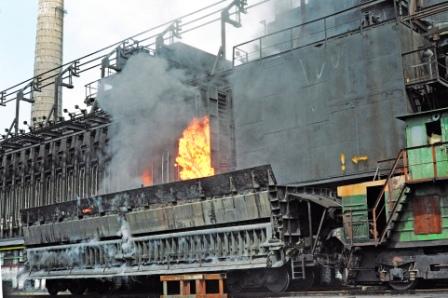
Image 2 – Issuance of coke from the coke oven battery
In recovery workshop cooking chemical products - 33 emission sources, 27 of them organized, it stacks tubular furnaces, collection and storage. Unorganized sources include open cooling tower capacity and final cooling of coke oven gas.In distillation plant 13 emission sources, including unorganized 2 (load products and steaming cisterns). In plant desulfurization 8 emission sources, all organized. Sources volley emissions at PJSC "Yasyni]ovka Chemistry Plant" absent.
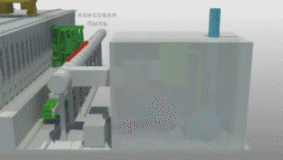
Image 3 – A dust-free coke from the coke oven battery
(Animation: 10 frames, 10 cycles of repetition, 114 KB)
According to the "List of the most common and dangerous pollutants emitted into the atmosphere must be regulated" pollutants emitted by sources of PJSC "Yasynovka Coke Plant", belong to the following categories:
a) The most common pollutants are:
- nitrogen oxides;
- sulfur dioxide;
- hydrogen sulfide;
- carbon disulfide;
- sulfuric acid;
- carbon monoxide;
- a substance in the form of suspended solids (microscopic particles and fibers);
b) dangerous pollutants include:
- volatile organic compounds: benzene, naphthalene, xylene, toluene, phenol;
- cyanides;
- fluorine and its compounds: hydrogen fluoride.
Solid waste products stored at Grygor'yevsky dumps. Dimensions to SPZ Hryhor'yevskyh dumps approximately 500m. but the size of the SPZ is not adhered. Analysis of the dispersion calculation showed maximum permissible concentration at points on BA is for these substances:
- naphthalene (5.9 MAC), the main contribution (99%) makes the cooling tower of the final cooling of coke oven gas;
- hydrogen sulfide (1.49 MAC), the main contribution to make such emission sources: cooling tower final cooling of coke oven gas (71.8), tower fire KB ¹ 5,6 (9,9), fire tower number 1 (2.4);
- tsianovoden (3.28 MAC), the main contribution to make such emission sources: cooling tower final cooling of coke oven gas (98.4), tower fire KB ¹ 5,6 (0,9), fire tower KB Number 1 (0.25);
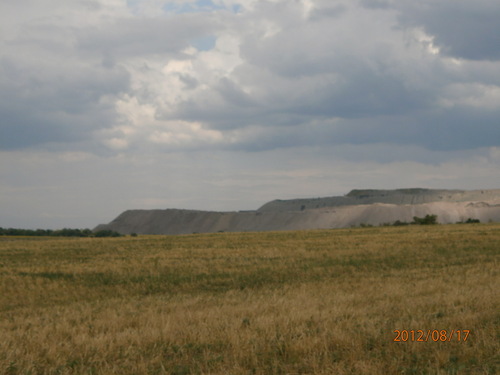
Image 4 – Grigorievsky dumps
2.2 Characteristics of PJSC "YCP" as a major source of air pollution
To ensure their water needs of the plant has production and drinking water supply.For two conduits (450mm) the undertaking comes only processed water that is removed from the channel "Seversky Donets-Donbass", which is operated by ME "Company" Water of Donbas ". Industrial Water supply plant organized mainly by drainage scheme. Fresh process water used to replenish the welfare loss of working cycles of plants.Technical water in the coke plant is consumed for cooling compressors, hydraulic injection, the coke, the filling of small volume water seal lap risers coke side.Technical water in plant desulfurization spent for working cycle.
Technical water distillation workshop spent feeding working hydraulic and hydro cycle, the wash cistern. CHP is a major consumer of industrial water to produce steam.Drinking water in an amount of about 100.0 thousand m3/year from ME "Makeevsky Gorvodocanal" served the needs of the population of factory dormitories, kindergartens ¹ ¹ 15,17, Palace of Culture, the stadium, and a small part on hosppobutovi needs of the plant.
For disposal on the premises are four drainage systems:
- economic - household;
- storm water drain;
- phenol designed to drain Collection of chemical pollution of wastewater generated in the production process and the system ;
- shlamovaja drain is used to transport water to hasylni towers and multiple re-applying for coke, the water is fed to tailing pond to keep the water table;
Cleaning of industrial and storm-water drainage is to install biochemical (Bhu).The device is intended for sewage coke production of resins, oils, phenols and other substances biochemically oxidized, to use treated wastewater for wet coke quenching. Wastewater entering the Bhu of phenolic workshop sumps capture.
2.3 Management of solid and liquid waste
At present JSC "YCP" - is a modern enterprise, , with 4 existing coke oven batteries (¹ 1, 3, 5, 6) reconstructed chemical workshops and reliable source of raw materials.The main products are: Metallurgical Coke (with quality indicators as required by customers), foundry coke, nut coke, coke fines, coal tar, ammonium sulfate, benzene distillation products (benzene for synthesis, solvent, toluene).
To ensure the company built its power 12 MW turbine power plant on the basis of their own elektronosiya - COG. In 2006 the company fully achieved its energy target.The plant was inventoried during which it was revealed that the company produced 32 types of waste including:
- first-class risk (mercury lamps);
- the second hazard class (paying acidic sulfate separation, oil waste, sawdust oiled, oiled rags, oiled filters waste solution, desulphurization, sludge washing cars, batteries worked);
- third hazard class (nozzle chordates, vanadium catalyst, carbide sludge, waste lacquer paints);
- Fourth hazard class (and lining brick acid, waste rubber, waste sumps tarry, container from the paint, power plant ash, road dust, and brick refractory linings, construction debris, the remains of electrodes, household waste, spent abrasive materials, waste tires, waste electric insulation, concrete sleepers, railway sleepers, wood, waste insulation).
Let's take a detailed look at catching shop. The shop trap chemicals coking coke oven gas cools and purifies it from ammonia and benzene hydrocarbons followed by obtaining ammonium sulphate and crude benzene.
The shop is cools and processes coke oven gas in the amount of 100 thousand.The Workshop has the following departments:
- department of condensation;
- sulfate office;
- benzene-skruberne office;
- chemical unit;
- departments dehydration and resin shipment;
- departments of pre-treatment of wastewater;
3. Characteristics of waste in the Departments of condensation
The gaseous products of coking coke to exit the chambers with temperature 700-800 C are assigned to parking in gas collector. Coke oven gas, having the primary gas coolers, going through smolovovidbiyynyky served in office for ochyshennya sulphate of ammonia to obtain ammonium sulfate.
Resin vidstoyalasya the water cycle barelyetnoho from the bottom through teleskopini regulator, as replenishment, displayed on the resin intermediate collection.Lighted (bas-relief) water from the top of mehosvitlyuvachey continuously flows into the intermediate collections and over podyetsya gas collector for irrigation and resin (aqueous resin emulsion) that vidstoyalasya, available in the collection of gas condensate.
Gas condensate after the primary gas cooler enters collections, resin, separated from the gas condensate available in store. This forms a vicious cycle and cycle tar water cycle gas collector. Fusy that settled to the bottom of mechanized clarifiers are removed by scraper in bins from which fusy unloaded and transported in a car in Coal preparation plant for utilization of fusiv their submission to the charge.
Stone coal tar with mechanized clarifiers pumped in radial clarifier for additional sludge from water by heating deaf couple. Dewatering water by gravity settling from the water by heating deaf couple. Dewatering water gravity fed to the mechanical lights and gum resin is fed into storage, and pumped into mothballs washers final gas coolers (coolers) benzene - scrubber department purification of naphthalene from coke oven gas by extracting it from the water cycle coolers.
A mixture of resin and water coolers naphthalene cleaners goes to resin storage, in which separation of resin and water occurs. Water through the water seal coolers enters the septic naphthalene (benzene - skruberne Branch) for the final settling of the resin. resin is pumped from storage sink for chemical plant for cleaning ammonia water and extraction of germanium oxide.