Abstract
Content
- Introduction
- 1. Theme urgency
- 2. Purpose and research problem
- 3. The object of study
- 4. Methods of research
- 4.1 Semi-coking
- 5. The experimental part
- Conclusion
- References
Introduction
Significance of coal in Ukraine is enormous, because it is the only energy carrier, explored reserves of which can meet the requirements energy and industry of the country in the next 300 years. In this case, if the structure of the world's coal fuel is 67%, oil – 18%, gas – 15%, in Ukraine – 94.5%, 2%, 3.5% respectively. Resources of solid fuels in Ukraine as of 2010 are 117.5 billion tons, ofwhich 56.7 billion tons – proved balance reserves, including 39.3 billion tons – coal of power marks. Every year in Ukraine is produced 65–80 million tonnes of salable coal production. Coke industry consumes 8.1% of the country's fuel [1].
Ukraine has so far been neglected the development of integrated resource-processing techniques bad quality coals. Rational use of Donbass coal assumes the optimization of an existing semi-coking process.
1. Theme urgency
A big problem in Ukraine is the use of low–rank coals unsuitable for coke production. Lately increasingly raised the question about the use of Donbass coal low-grade metamorphic non–energy processes. They can be used with success as raw materials for synthetic solid, liquid and gaseous fuels. In connection with the above are the topical studies aimed at developing the most effective methods of processing sulfur fuels
One of the most promising methods for processing low–grade coal is semi–coking. Currently semi-coking solid fuels considered not only as a supplier hydrocarbon feedstock, but also as one of the major steps in the various industrial processes (plants for the production of synthetic liquid of fuel energy technology and gas chemical processing plant solid fuel). From tars carbonization with appropriate processing of can be produced a large number of products such as motor fuel, phenols, paraffin, etc.
Thus, the optimization of semi–coking process using the latest advances in science will allow a rational recycle subbituminous coals, which constitute a significant part of the reserves of steam coal in Ukraine (developed and trained to develop reserves of 5.04 billion tons).
2. Purpose and research problem
Purpose – to improve the standard method of long-flame coal carbonization by their prior learning method with derivatography followed by determining the optimal conditions for obtaining the primary resin and evaluation of their possible use as fuel, raw materials for the chemical industry. Available in the literature data on the composition of various semi–coking coal products do not transmit features of the allocation of liquid products by thermal degradation of sulfur coals, which is the Donbass coal.
3. The object of study
The study samples of were subjected to long–flame coal sulfur (Wa – 0,9; Ad – 4,6; Vdaf – 46,2; Sdaf – 76.1; Ndaf –5,43; Std – 5,85),
and the products the heat treatment at different temperatures. Coal was selected from the mine Trudovskaya, plast k8. Given type of of coal – rebuilt.
The term recovery
displays the nature of the environment that arises in a given period (mainly reducing environment). Coal of reduced
type formed at flooding (of transgression) peaty sediments salty sea water, rich in sulphate – ions. Therefore, all the coal type usually
have high yield of volatile matter, high sulfur content (overall and pyrite), hydrogen, and ash, as compared with coal type а
[2].
This coal is not used in the production of coke, as it is not sinters and belongs to the energetic coals. From the D–grade coal can be produced a number of valuable chemicals and fuels ennobled. Studies have shown that long-flame coal with low ash content can serve as a good raw material for the production of synthetic liquid fuel.
4. Methods of research
In this paper we used the following methods:
- semi-coking;
- definition the yield of products semi–coking;
- derivatography;
- method of structural–group analysis of liquid products semi–coking.
4.1 Semi–coking
The method is an industrial process carbonization processing of solid fuels, which aims at and their comprehensive use as a source of energy and raw materials for chemical industry. Semi–coking gives you the opportunity develop a ennobled by solid fuel – char calorie gas and the low temperature tar suitable for production of chemical products and liquid fuels.
From a theoretical standpoint thermolysis in a temperature interval 500 – 550 °С is used for evaluation of coal as a feedstock for the process of processing, therefore the method of semicoking is the basis of laboratory methods for studying the chemical nature of solid fuels. Semicoking stage is the main and defining stage of coker, which includes the period of the main thermal decomposition formation stage plastic mass of coke (for coking fuels) that is a great value in terms of looking the behavior of different coals upon Thermal Decomposition. This method can be successfully used only if the products produced in the Semicoking process are the primary degradation products organic mass. However, the primary products are known to readily involved reaction between themselves and with unreacted mass to produce secondary substances yield and composition of which depends on the conditions of pyrolysis [3]
Among the existing methods special attention is deserved low-temperature coker process, which yields valuable volatile products and ennobled solid fuels – coal char. Until now, the country has not paid much attention to the development of of the above method.
5. The experimental part
By the analysis of the DTG curves and TG derivatograms were determined temperature intervals and maximum temperature (Tmax) of the main thermal decomposition of coal, i.e. high temperature endoeffect on the DTG curve. Maximum temperature corresponding to maximum rate of of weight loss is of the characteristic of the temperature point that provides objective information structure of coal and its behavior during the pyrolysis [4].
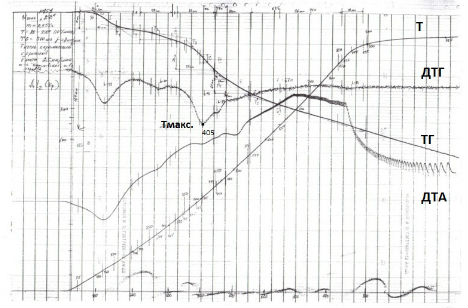
Figure 1 – Derivation of coal of grade D
These data are used for Semicoking investigated sample at a temperature of Tmax. = 405 °C in the retort Fischer medium heating rate 16,3 °C / min. Was calculated material balance of the process.
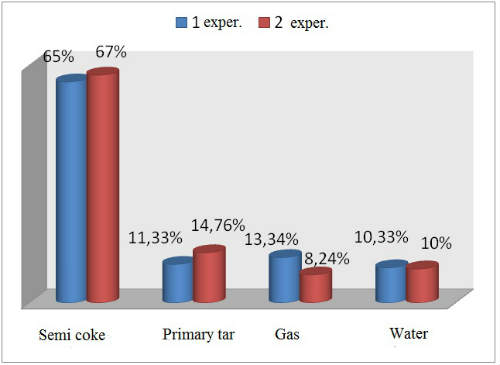
Figure 2 – Output semicoking products at T max. = 405 °C, %
Conclusion
The standard method of Semicoking can not be extended to the whole range of coal metamorphism, as the temperature of the process not corresponding to temperature of the maximum degradation rate of of the least sustainable component of the organic mass of coal (Tmax). The obtained results show that the standard semi-coking does not allow the primary decomposition products coal, as the temperature of the process for the coal overstated.
Conducting semicoking at the optimum temperature set by derivatograms allows to increase yield of liquid products by 1.5 times, which can serve as feedstock for the chemical industry and energy. In the primary tar obtained at T max. = 405 °C detected a high content of maltenes (a mixture of phenols, carboxylic acids, organic bases), which are used to produce liquid fuels.
In writing this essay master's work is not yet complete. Final completion: December 2013. Full text of the work and materials on the topic can be obtained from the author or his manager after that date.
References
- Калечиц И.В. Химические вещества из угля / Калечиц И.В.— М.: Химия, 1980. — 616 с.
- Гюльмалиев А.М., Головин Г.С., Гладун Т.Г. Теоретические основы химии угля / Гюльмалиев А.М., Головин Г.С., Гладун Т.Г.— М.:Издательство Московского Государственного Университета, 2003. – 556с.
- Гойхрах И.М., Пинягин Н.Б. Химия и технология искусственного жидкого топлива / Гойхрах И.М., Пинягин Н.Б. – М.: Государственное научно-техническое издательство нефтяной и горно-топливной литературы, 1954. – 488 с.
- Скляр М.Г., Тютюнников Ю.Б. Химия твердых горючих ископаемых./Скляр М.Г. – Киев: Выща школа, 1985. – 247 с.
- В.Н. Шевкопляс, Л.Ф. Бутузова, С.Н. Лящук, Л.Я. Галушко Дериватографические исследования твердых топлив в интервале температур основного термического разложения. Вопросы химии и химической технологии. 2007, №3 – с.142-146
- Тамко В.О., Шендрик Т.Г., Матвеев О.А. Удосконалення методу комплексної переробки бурого вугілля з метою поліпшення якості продуктів.
- Шевкопляс В.Н., Лящук С.Н., Бутузова Л.Ф. Новый показатель для оценки качества углей / Химия твердого топлива.-2006.-№ 4. – С.12-21.
- Макарова Г.Н., Харлампович Г.Д., Химическая технология твердых горючих ископаемых. – М.: Химия, 1986. – 492 с.
- Аналитическая химия и технический анализ угля: Учебник для техникумов / Авгушевич И.В., Броновец Т.М., Еремин И.В. и др. – М.: Недра, 1987. – 336 с.
- Акимова Л.Н., Новицкий П.Л. Методические указания к лабораторному практикуму «Исследование технологических показателей твердых горючих ископаемых». – Донецк: ДПИ, 1985. – 36 с
- Бутузова Л.Ф., Маковский Р.В., Рожков С.П., Рожкова Н.Н., Бутузов Г.Н. Влияние радикальных реакций при термической переработке низкокачественных углей // Вопросы химии и химической технологии. № 5 – Днепропетровск. – 2008. – С. 68 – 73.