Аннотация
В.Г. Нечепаев, В.А. Голдобин, Н.В. Гутаревич, К.В. Гончаренко – Разработка и апробация комплексной методики прочностного расчета приводов скребкового конвейера типа спц 26 в среде САПР APM WinMachine. В статье предложена методика прочностного расчета трансмиссии и элементов корпусной группы скребкового конвейера типа СПЦ 26 с применением высокотехнологичного программного обеспечения APM WinMachine. Установлены опасные сечения и запасы прочности элементов привода.
Постановка проблемы, ее актуальность.
Скребковый конвейер является базирующим элементом ряда механических комплексов для выемки углей в условиях тонких пластов. В настоящее время остро стоит вопрос автоматизации прочностных расчетов, что особенно актуально при проектировании современных машин. Как показывает проведенный анализ, энерговооруженность приводных станций конвейеров неуклонно повышается в связи с ростом интенсификации процессов горного производства. Кроме того, конвейер используется в основе различных механизированных комплексов применительно к многообразию условий производства. Это обусловливает необходимость комплектования конвейеров редукторами различных типов и параметров. Для оперативной модернизации конструкций приводов конвейера необходима методика прочностного обоснования модернизированных вариантов их редукторов, позволяющая оперативно с достаточной точностью и с небольшими затратами выполнить соответствующий анализ. Этими требованиями определяется актуальность и необходимость создания комплексной методики прочностного анализа весьма специфических и сложных конструкций, являющихся основой системы привода исполнительных органов комбайнов.
Анализ последних исследований.
Существует ряд работ, посвященных исследованию параметров и конструкций приводов машин. Анализ работ [1, 2] показывает, что применение систем автоматизированного
проектирования (САПР) позволяет значительно сократить трудоемкость расчетов и повысить их точность. Однако различие устройств, режимов нагружений и других условий эксплуатации требуют разработки специальных методик прочностного анализа.
Цель и постановка задач.
Цель исследований заключалась в разработке методики прочностного расчета приводов скребкового конвейера типа СПЦ 26. Для достижения указанной цели были решены следующие задачи:
- разработаны пространственные модели редукторов;
- выполнены проверочные расчеты элементов трансмиссии;
- проведены исследования прочности корпусной группы.
Эти задачи решены с использованием САПР АРМ WinMachine, которая позволяет реализовать все современные требования для проектирования машин. Объектом исследования являлась редукторная группа шахтного скребкового конвейера типа СПЦ 26, общий вид которого представлен на рис. 1. В исследуемом конвейере редуктор головной приводной станции цилиндрический и редуктор концевой приводной станции коническо-цилиндрический. Особенностью объектов является то, что оба редуктора имеют одинаковые корпуса, но комплектация, крепления отличаются. Оба имеют по 4 вала, 3 передачи, одинаковые передаточные отношения, одинаковые числа зубьев и модули колес на соответствующих передачах, в цилиндрическом – передачи цилиндрические прямозубые и косозубая, а в коническо-цилиндрическом – первая передача коническая. На рис. 2, 3 представлены твердотельные модели редукторов.
Рис. 1. Общий вид
Материалы и результаты исследования. Для расчетов элементов трансмиссии применялись модули APM Trans, APM Shaft, APM Bear, APM Joint среды САПР APM WinMachine. Расчет передач выполнен в модуле APM Trans. Все передачи прошли проверку по вращающему моменту и по заданному ресурсу.
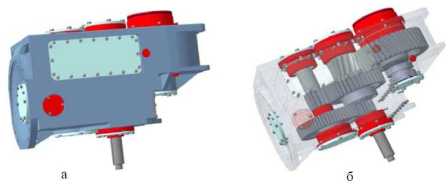
Рис. 2. Твердотельная модель цилиндрического редуктора головной приводной станции: а - внешний вид; б - сборка
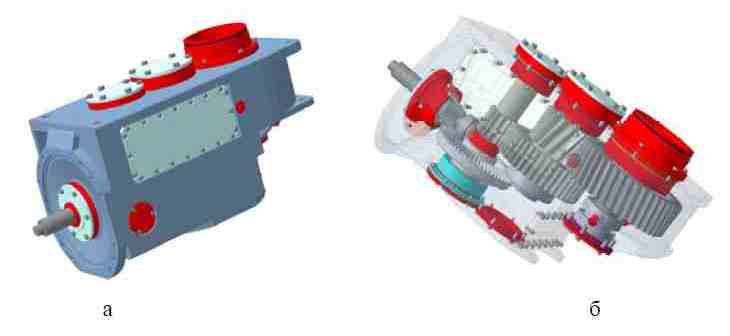
Рис.3. Твердотельная модель коническо-цилиндрического концевого редуктораконцевой приводной станции:
а - внешний вид; б - сборка
Результатом расчета являются действительные напряжения, которые имеют оптимальные значения, не превышающие допускаемые и не требующие изменений.
Следующим этапом проведен расчет валов при помощи модуля APM Shaft. В результате была получена эпюра распределения коэффициента запаса прочности. Используя эту эпюру, определяем минимальные запасы прочности. Значения коэффициентов находятся в пределах от 3 до 13,5, что значительно превышает минимально допустимое значение.
Рис.4. Результат проверочного расчета
конической передачи
Исходя из этого, можно применить меры, обуславливающие оптимизацию значений коэффициента запаса усталостной прочности, в частности изменение марки стали. Пример результатов указан на рис. 4, 5.
Рис.5. Результат проверочного расчета
вал-шестерни с цилиндрическим венцом
Расчет радиальных, радиально-упорных и сферических роликовых подшипников качения выполнен в модуле APM Bear. Суть расчета – определение долговечности, срока службы подшипника в данных условиях эксплуатации и сравнение с требуемыми значениями. Рассчитанные значения долговечностей удовлетворяют заданным условиям, не требуют подбора и замены на другие типы подшипников, с большим сроком службы. Шлицевые и шпоночные соединения проверены модулем APM Joint. Анализ полученных результатов расчета позволяет сделать вывод о том, что расчетные значения длин соединений соответствуют, а в ряде случаев превышают требуемые значения. Это обуславливает надежную работу, исключающую преждевременный выход из строя.
На заключительном этапе выполнения работы проведен расчет корпусной группы. Расчет базируется на методе конечных элементов, выполняется в модулях APM Studio и APM Structure. Число конечных элементов твердотельной модели, а следовательно, длительность времени расчета устанавливается в соответствии с желаемой точностью получаемых результатов и рядом других соображений. Для начала составлена расчетная схема в модуле APM Studio: сопряжены грани деталей, примыкающих к корпусу, приложены нагрузки, ограничения в виде закреплений, учтена масса двигателя. Примеры расчетных схем корпусов представлены на рис. 6.
Полученные расчетные схемы разбиты на сетку конечных элементов с заданным шагом разбивки 25. Указанный шаг разбивки выбран после ряда проведенных исследований.
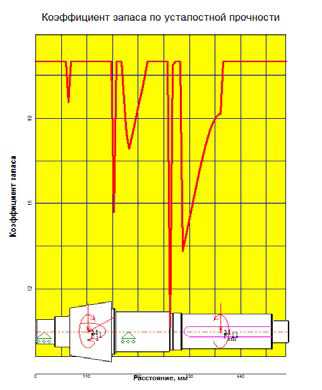
Рис. 6. Расчетная схема: а - корпус цилиндрического редуктора, б - корпус цилиндрическо-конического редуктора
При разбиении корпуса цилиндрического редуктора на сетку конечных элементов получили 33930 узлов, 124434 объемных элемента, из которых все 4 – узловые. При разбиении корпуса коническо-цилиндрического редуктора концевой приводной станции на сетку конечных элементов получили 33603 узла, 122371 4 – узловой элемент (рис.7)
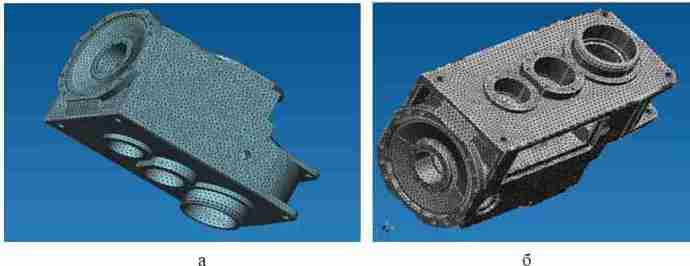
Рис. 7. Конечно-элементная сетка: а - корпус цилиндрического редуктора, б - корпус цилиндрическо-конического редуктора
После разбиения сетка конечных элементов загружается в модуль APM Structure3D, где проводится расчет корпуса. Результатами расчетов являются карты распределения напряжений, перемещений, коэффициента запаса прочности. Примеры для обоих вариантов сборок указаны на рис. 8, 9.
Анализ напряженно-деформированного состояния показал, что у цилиндрического редуктора головной приводной станции максимальное значение действующего напряжения составило 81,28 МПа в
области стакана для расположения подшипников выходного вала. Также значительные напряжения имеют место в прилегающих зонах. В остальных зонах напряжения более низкие. Коэффициент запаса по
текучести у этого редуктора составил 6,64, по прочности – 11,59; максимальное перемещение – 0,105 мм; максимальная нагрузка 839,4 Н; главные напряжения – 35,05 МПа; запас по усталости – 6,53.
Сравнивая значение максимального напряжения с допускаемым, можно сделать вывод о том, что конструкция является недогруженной, следовательно целесообразно принять меры по снижению металлоемкости в недогруженных зонах корпуса.
В корпусе коническо-цилиндрического редуктора значение максимального напряжения составляет 35,3 МПа в зоне расположения расточек под подшипники на вертикальной боковой стороне корпуса. Максимальное перемещение составило 0,0315 мм; максимальная нагрузка – 603,9 Н; коэффициент запаса по текучести – 14,98, по прочности – 26,14; запас по усталости – 15,7; главные напряжения – 17,01 МПа.
Рис. 8. Корпус цилиндрического редуктора: а - карта напряжений, б - карта перемещений
Рис.9. Корпус коническо-цилиндрического редуктора: а - карта напряжений, б - карта перемещений
Корпус коническо-цилиндрического редуктора, также как и цилиндрического, является недогруженным, следовательно, рекомендации по равномерному распределению напряжений будут аналогичны цилиндрическому корпусу: снизить металлоемкость в недогруженных областях корпуса.
Выводы
1. Разработана методика прочностного расчета приводов шахтных скребковых конвейеров в среде САПР APM WinMachine.
2. Проведено сравнение значений максимальных напряжений с допускаемыми и установлены коэффициенты запаса прочности. Так, максимальные напряжения в цилиндрическом редукторе достигают 81,28 МПа и для коническо-цилиндрического - 35,3 МПа. Максимальное смещение от номинальных размеров составляет 0,105 мм, а запас по усталостной прочности – 6,53.
3. Достоверность предлагаемой методики прочностного расчета подтверждается совпадением значений основных прочностных параметров привода шахтного скребкового конвейера СПЦ 26, эксплуатируемого на шахтах Донбасса.
Список использованной литературы
1. Голдобин В.А., Коробко Ю.Н. Анализ напряженного состояния приводных колес коксовыталкивателяАвдеевского коксохимзавода, Машинознавство/ Матеріали12-ї регіональної науково-методичної конференції. – Донецьк, ДонНТУ, 2010, с. 16-19.
2. Гончарова О.Е. Методика прочностного расчета балок осей мобильных машин. Труды Одесского политехнического университета. Выпуск 1(5),1998, с. 137-139.
3. Шелофаст В.В. Основы проектирования машин. М. Изд-во АПН., 2000.-472с.
4. Сладковский А., Ханишевский Т., Матыя Т. Динамика мостового крана Часть 1. Определения характеристик мостового крана. Вісник Східноукраїнського національного університету імені Володимира Даля №10(152) Частина 1, 2010, с. 200-205.