Abstract
Table of contents
- Introduction
- 1. Actuality of theme
- 2. Purpose and research tasks, planned results
- 3. Review of research-and-developments
- 4. Combined spotfacers
- Conclusions
- References
Introduction
After a downstream, conditioned a world economic crisis, the engineer of Ukraine acquires the dynamics of development. To one of main tasks in any industry of engineer there is an improvement and development of new equipment and toolpiece for providing of high quality of wares, and also increase of the productivity.
Treatment of openings occupies a no less important place in an engineer and on volume does not yield to the processes of treatment of outward surfaces. Openings in the details of machines are cylindrical smooth and step. Under a step understand openings of different diameters, located on one axis, one is successive after other. Openings can be opened both-side or from one side (deaf). Openings with correlation of length to the diameter more than five considered deep.
Treatment of openings some more difficult, than outward surfaces of bodies of rotation. In this connection exactness (kvalitet) on openings is assigned for one order more rough and, as a rule, not more precisely 7th kvaliteta. Treatment of openings can be produced with a removal and without the removal of shavings. Treatment with the removal of shaving is carried out lezviynym and abrasive instrument. To treatment a lezviynym instrument, boring, coredrilling, development, boring and reaching behave. Polishing and honing behaves to abrasive treatment.
Treatment of openings without the removal of shaving is produced by calibration by the pressing sewings (dornov) and marbles, and also by a pinning-out [1]. For the increase of exactness of openings after boring and decline of roughness of their surface apply coredrilling. Can be processed coredrilling also openings in foundings and stamping. Coredrilling can be a rough-down under subsequent development, boring or reaching. After the draft coredrilling in a purveyance exactness is provided for 11.12 kvalitetu and roughness of surface of Ra=20.10 mkm. The clean coredrilling depending on material and construction of spotfacer allows to get exactness for 9.10 kvalitetu and roughness of Ra=6,3.3,2 mkm. Therefore at treatment of openings for 11.13 kvalitetam coredrilling can be a final operation.
Pripusk under coredrilling of the preliminary drilled or bored openings is approximately 1/8.1/10 opening diameter. Cutting speed for a hard-alloy instrument at treatment sostovlyaet became 25.120 m/mines, serve of 0,4.0,5 mm/ob. For cast-iron purveyances accordingly cutting speed is made by 50.150 m/mines and serve – 0,3.0,6 mm/ob. Openings to 12 mm does not coredrill a diameter, and at once develop a draft involute.
A wideuse was found by the combined instrument. Combination of draft and clean treatment, treatment of shaped, step or a few soosno the located openings, combination of different operations, is executed such instrument for one passage-way.
The construction of the combined instrument depends also on configuration and sizes of the processed opening, form, sizes, location and amount of a few soosnykh openings, requirements of exactness, cleanness of treatment, size of taken off pripuska, and also from the method of direction of instrument [2].
1. Actuality
Presently an engineer did enormous gallops in the field of treatment of hard-processing materials with the use of progressive toolpiece, from new instrumental materials of the improved geometry and enhanceable firmness, by application of different ways of the combined treatment with bringing of additional streams of energy and new kinematics charts.
This master's degree work is devoted actual task are increases of the productivity due to the change of geometrical parameters of instrument.
2. Purpose and research tasks, planned results
Purpose of work is an increase of efficiency of treatment of openings due to optimization of geometrical parameters and construction of the collapsible combined spotfacer.
Basic tasks:
- To conduct the analysis of existent constructions of collapsible spotfacers, expose basic progress of similar instruments trends.
- To conduct the analysis of influence of geometrical parameters and modes of cutting of collapsible spotfacers on the productivity of treatment and providing of the required exactness.
- To offer the rational construction of collapsible spotfacer, able to provide the required exactness of treatment at the maximal-possible productivity.
- To produce optimization of the modes of cutting for the offered construction of collapsible spotfacer.
- To develop the method of determination of the optimum modes of cutting at the use of collapsible spotfacer.
Research object: treatment of openings a collapsible spotfacer.
Article of research: Processes, having influence on exactness and productivity of treatment collapsible spotfacers.
Research methods.Achievement of the put purpose is provided rational combination of theoretical and experimental methods of researches.
3. Review of research-and-developments
Planning of the combined axial toolpiece, and in particular, constructions of collapsible spotfacer during some time got busy:
A. Cherepanov in-process «Perfection of constructions of toolpiece by means of the searching planning» [3],considered the features of realization of this methodology as it applies to the questions of planning of collapsible spotfacers.
A. Shmelev [4] the constructions of the axial combined instruments are partly systematized and analytical dependences are given for determination of some structural parameters of step drills.
I. Malyshko in-process [5] brought recommendations over on planning and exploitation of the axial combined instruments.
4. Combined spotfacers
Spotfacers make the combined spotfacers the tail whole (pic.1), tail combined teams with the inserted knives, nasadnymi whole and nasadnymi combined teams (pic.2). Spotfacers make out of high-speed steel or with the plates of carboloy, made drunk on the corps of spotfacer or on the corps of knives at collapsible constructions. Tail spotfacers like drills fasten by cylindrical or conical tailpresss, nasadnye spotfacers have the conical landing opening (konusnost' 1:30) and cutoff key for a protection from provertyvaniya during work. On the construction of working part tail spotfacers are analogical spiral drills, but does not have a transversal cutting edge and have three teeth, due to what the best direction is provided during work, and the best cilindrichnost' and quality of the treated surface. Four-six points have nasadnye spotfacers.
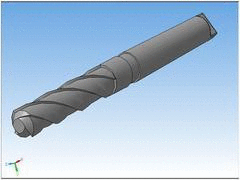
Picture 1 - is the Animated model of tail whole spotfacer (is made on mp_gif_animator 125 KB, 5 Frame)
Spotfacers from high-speed steel make tail whole diameters from 10 to 40 mm, by the tail combined teams with the inserted knives by a diameter from 32 to 80 mm, nasadnymi whole a diameter from 25 to 60 mm and by the nasadnymi combined teams by a diameter from 40 to 120 mm. Tail spotfacers do weld-fabricated is working part from high-speed steel, tailpress from staley 45, 40Kh, 45Kh. A welding place is usually done on a neck. A back surface at whole spotfacers is designed on a spiral or conical surface, at the spotfacers of collapsible construction – on a plane. For fastening of knives on a corps does do slanting slots, inclined to the axis under a corner ω=10...20°. The front surface of corps is flat. Knives have a vee with the corner of wedge of 5°, they are fastened in a corps by rifleniy. Three teeth, nasadnye whole, have tail whole spotfacers – four.
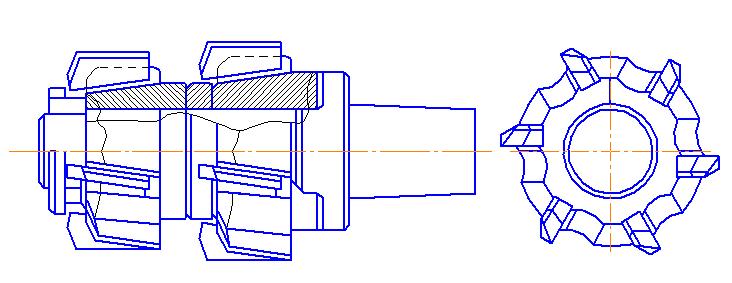
Picture 2 - is the Nasadnoy collapsible spotfacer
Height of tooth of these spotfacers of h=(0,1...0,16) d. The back of tooth is curvilinear, that allows to process a tooth for one passage-way. Most often spotfacers make with the location of cutting edge on a radius (λ= 0°). Spotfacers, equipped hard-alloy plates, can be component and collapsible. Component tail spotfacers make a diameter 14–50 mm, nasadnye 32–80 mm, nasadnye collapsible spotfacers by a diameter 40–120 mm.
Three teeth, nasadnye, have tail spotfacers — four, collapsible spotfacers are four-six points. The corps of spotfacers and knives, equipped plates from a carboloy, do from staley 40Kh or 45Kh (36... 46hrce), 9KHs (57...63HRCy) or from high-speed steel (57...63HRCy). For their equipment apply plates from the carboloies of VK6, VK8, VK6-M, VK8-V, T5K10, T14K8, T15K6. Fastening of plates is produced napaykoy [6].
Conclusions
The Important value, especially for the automated production, has reliability of instrument, adjusted to automation, small expense of instrumental material and low prime price. These requirements are answered by collapsible spotfacers with the mechanical fastening of cuttings plates. Replacement of component, in particular napaynykh, spotfacers the combined teams is one of major progress of technology of treatment of openings trends in an engineer.
At writing of this abstract master's degree work is not yet completed. Final completion: December, 2013. Complete text of work and materials on the topic can be got for an author or his leader after the indicated date.
References
- Костюкевич С. С. Точность обработки глубоких отверстий / Костюкевич C. C., Дечко Э. М., Долгов. В. И. – Минск: Вышейшая школа, 1978. – 144 с.
- Пазюк Е.И. Инструмент для обработки отверстий (сверла, зенкеры, развертки и расточной инструмент). - Л.: Ленинградское газетно-журнальное и книжное издательство, 1952. - 128 с.
- Совершенствование конструкций режущего инструмента посредством поискового проектирования // СТИН. – 2006 г. – №2.
- Максимов М.А. Комбинированные режущие инструменты./ Максимов М А., Киселева Л П., Шмелев А.Я. – Горький: Горьковский государственный университет, 1977, 86 с.
- Малишко І. О. Основи теорії проектування осьових комбiнованих інструментів: автореф. дис. на здобуття наук. ступеня доктора техн. наук : спец. 05.03.01 „Процессы механической обработки, станки и инструменты” / І. О. Малишко. – Київ, 1996. – 33 с.
- Сахаров Г.Н. Металлорежущие инструменты./ Сахаров Г.Н. Арбузов О.Б., Боровой Ю.Л., Гречишников В.А., Киселев А.С. – М.: Машиностроение, 1989. – 328 с.
- Технология обработки типовых отверстий деталей машин [электронный ресурс]. - Режим доступа:http://elite-instrument.ru/category/zenkery-/