Рисунок 1 - Схема технологической системы при наружном круглом шлифовании заготовки – тонкостенной оболочки вращения из ситалла: 1 – оправка; 2 - шпиндель станка; 3 - обрабатываемая заготовка; 4 – шлифовальный круг IАI 200х10х3х76 А 315/250-4- М2-01, установленный в агрегатной головке. Точки 1…10 – точки, ограничивающие области изменения параметров рассматриваемой технологической системы
Также предполагается, что в зоне контакта шлифовального круга с заготовкой возникают параметрические колебания детали - тонкостенной оболочки вращения, под воздействием перемещающейся силы резания. На основании данных, приведенных в работе [3], проведен анализ устойчивости системы на параметрические колебания, который показал, что наибольшей неустойчивостью обладают области заготовки в районе точек 1 – 5 (см. рисунок 1). Области, ограниченные точками 6 – 10, находятся в зоне устойчивости к параметрическим колебаниям.
Схема алмазно-абразивной обработки оболочки, представлена на рис. 2.
Рисунок 2 - Схема шлифования (а) и расчетная схема (б) алмазно-абразивной обработки тонкостенной обо-лочки вращения из ситаллa
Обрабатываемая заготовка представляет собой тонкостенную оболочку вращения, динамику которой невозможно описать при помощи системы с сосредоточенной массой, к которой приводится рассматриваемая технологическая система. Поэтому анализ динамического поведения оболочки необходимо провести в соответствии с законами теории оболочек.
Динамические характеристики рассматриваемой системы обозначены следующим образом: m1, m2, m3 – приведенные массы, соответственно, агрегатной шлифовальной головки с инструментом, заготовки (оболочка вращения), оправки, закрепленной в шпинделе станка,; k1, k2, k4 – соответственно,приведенные жесткости агрегатной головки, заготовки, оправки со шпиндельным узлом; c1, c2, c4 – линейные коэффициенты демпфирования, показывающие величину рассеивания энергии рассматриваемых элементов, соответственно, агрегатной головки, заготовки, оправки со шпиндельным узлом. ck, kk – соответственно, линейный коэффициент демпфирования и жесткость контакта инструмента и заготовки.
– сила резания, зависящая от динамических характеристик технологической системы обработки и возмущающего воздействия со стороны шлифовального круга, вызванного его биением и огранкой; где P0 – статическая составляющая силы резания.
Силовой баланс для рассматриваемой
технологической системы можно представить как:

После преобразования получим уравнения движения вида:
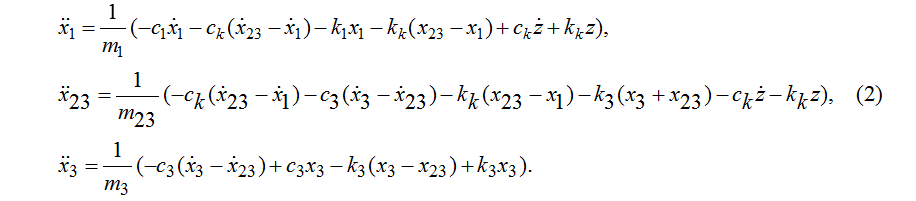
Решение системы уравнений (2) реализовано с использованием системы имитационного моделирования Simulink.
Статическую жесткость k в направлении оси Х для рассматриваемой подсистемы (см. рисунок 2, а) в точках приложения нагрузки (см. рисунок 1) определяем по данным работы [1] как
, где P – прилагаемая в точке статическая нагрузка, x – суммарные радиальные перемещения подсистемы «шпиндельный узел-оправка-деталь». В модели учитываются две собственные частоты рассматриваемой подсистемы 60±5 Гц и 123±10 Гц. Выполненные экспериментальные исследования показали, что при перемещении инструмента от носка детали к ее фланцу основная собственная частота изменяется в сторону увеличения. То есть, при расчете вибраций в области точек 5 – 10 основной собственной частотой является более низкая, со значением 60±5 Гц, в области точек 1-6 преобладает более высокая частота - 123±10 Гц, что и учтено в расчетной модели.
Приведенную массу определяем по формуле
. Обобщенный коэффициент демпфирования для каждой точки определяем по формуле
, где Ψ= 0.8…0.9 – коэффициент рассеивания энергии, m – приведенная масса в i-й точке, k – статическая жесткость в i-й точке.
По результатам экспериментальных исследований подсистемы «шпиндель - агрегатная головка – суппорт» получено, что ее податливость - 0,25 мм/кН, собственная частота - 710 Гц, динамические характеристики составляют: приведенная масса m = 0,0002 кг, k= 4000 Н/мм, с= 1,13 Нс/мм.
Во время алмазно-абразивной обработки происходит удаление материала припуска с заготовки при заданной глубиное резания t. Динамические процессы, происходящие при обработке заготовки, изменяют глубину резания на величину Δt, что, в свою очередь, изменяет силу резания в зоне контакта инструмента и заготовки.
При установке шлифовального круга с биением e=0,02 мм (значение определено экспериментальным путем и использовалось для последующего расчета) при обработке возникает источник возбуждения с частотой ω1 = 63 Гц (для скорости круга 40 м/с) или ω1 = 48 Гц (для скорости круга 30 м/с). По круглограммам поверхности круга установлено, что в процессе обработки на поверхности круга образуются три волны высотой r. В этом случае при шлифовании возникает возбуждение с частотами ω2= 189 Гц и ω2= 144 Гц, что соответствует скоростям шлифовального круга 40 и 30 м/с. Таким образом, глубину резания можно представить как:

где t0 – заданная технологическим процессом глубина резания, zk – перемещения, вызванные биением шлифовального круга и его некруглостью, zd – перемещения, вызванные волнистостью детали, полученной на предыдущих операциях или переходах, x1, x23, x4 – перемещения центров осей шлифовального круга и заготовки в результате вибраций при обработке, x2 – перемещение поверхности обрабатываемой детали - тонкостенной оболочки вращения. В данном случае не учитываем параметры zd и x2. Таким образом, наиболее влиятельным источником возбуждения вибраций приняты инерционные силы, вызываемые биением и огранкой шлифовального круга. Параметр zk можно представить в виде зависимости 
Выражение
в системе уравнений (1) моделирует динамические явления, происходящие в зоне контакта шлифовального круга и обрабатываемой заготовки. Для данного случая известна экспериментально найденная величина силы резания (статическая составляющая силы резания) для применяемых параметров режима резания: t0 = 1 мм,s = 0,73 мм/об, n = 73 об/мин, vk = 30 м/c. Жесткость контакта шлифовального круга и заготовки определяем как
, где Pnd, td – динамические составляющие силы резания и глубины резания. Демпфирование в зоне контакта определим как
, где
, где g=9.8 м/с2; Pn – нормальная составляющая силы резания (экспериментально найденное значение).
Для решения задачи обеспечения качества поверхности тонкостенной оболочки вращения при алмазно-абразивной обработке важно знать величину радиального перемещения поверхности оболочки в точке контакта со шлифовальным кругом. В этот момент формируется высотный параметр качества поверхности, по которому в данном случае можно судить об уровне вибраций во время обработки. За основу берем дифференциальное уравнение второго порядка с периодическими коэффициентами, полученное в работе [3] при исследовании поведения круговой конической оболочки под действием подвижной сосредоточенной массивной нормальной нагрузки:
В уравнении (4) выполняются граничные условия шарнирного опирания конической оболочки. Учитывается влияние тангенциальных сил инерции и скоростей - нагрузка движется в окружном направлении на определенном расстоянии от торца оболочки с постоянной скоростью. Получаем, что
– компонент радиального перемещения серединной поверхности рассматриваемой области оболочки; n – количество волн по окружности оболочки; m – количество волн в осевом направлении. Параметры m и n описывают форму колебаний оболочки. Для колебаний оболочки изгибного типа
Для последующего расчета принималось n=3, m=1;
– параметр, зависящий от величины нагрузки и места её приложения; А – параметр, зависящий от скорости движения нагрузки по окружности, собственной частоты оболочки, количества волн по ее окружности. Для расчета принималось: низшая собственная частота оболочки для используемой схемы установки в приспособлении 1584 Гц, скорость движения нагрузки по окружности 7,64 с-1 (частота вращения детали 73 об/мин); x – безразмерный параметр времени, учитывающий геометрию и физико-механические свойства оболочки, форму исследуемых колебаний, скорость перемещения нагрузки по оболочке и время; P* - параметр, который описывает характер прилагаемой нагрузки, учитывающий форму колебаний, физико-механические свойства материала оболочки, скорость перемещения нагрузки. Решение уравнения (4) реализовано с использованием системы имитационного моделирования Simulink.
Результаты расчетов
Для каждой области, ограниченной точками, указанными на рисунке 1, при помощи модели, разработанной в программе Simulink, были определены частота и амплитуда колебаний. Динамическое поведение технологической системы при обработке рассматриваемой заготовки – тонкостенной оболочки вращения из ситалла при перемещении инструмента от вершины изделия к фланцу не постоянно, что сказывается на качестве обработанной поверхности. Характер колебаний, их амплитуда, частота, форма изменяются в зависимости от участка относительно оси заготовки, который проходит инструмент.
На рисунке 3 приведены сравнительные кривые величины амплитуды вибраций, полученные по результатам выполненного расчета и экспериментально.
Для определения факторов, влияющих на динамику процесса шлифования, проанализируем поведение каждого элемента рассматриваемых подсистем. Представленные результаты расчета были получены как совмещенные вынужденные колебания и колебания оболочки в зоне контакта шлифовального круга и заготовки. Вибрации заготовки были определены как параметрические колебания, возникающие при движении с постоянной скоростью по окружности оболочки постоянной сосредоточенной локальной нагрузки.
Полученные результаты расчетов показали, что частота и амплитуда колебаний оболочки значительно увеличиваются на участках заготовки 1 – 5 (см. рисунок 1), где оболочка находится в неустойчивом состоянии относительно параметрических колебаний. Это оказывает отрицательное влияние на качество обработки заготовки и сопровождается появлением волнистости на ее поверхности.
Рисунок 3 - Зависимость амплитуды вибраций в зоне контакта инструмента и заготовки вдоль оси обраба-тываемой детали (1 – экспериментально полученные результаты; 2 – расчетные значения)
Основными факторами, оказывающими влияние на амплитуду и частоту колебаний оболочки, являются: собственная частота и форма колебаний оболочки (зависят как от самой формы, размеров, геометрии, толщины оболочки, так и от точности её установки на станке, в том числе и от конструкции оправки - приспособления); величины прилагаемой нагрузки (сила резания); параметры режима резания (скорость вращения заготовки при обработке в рассматриваемых условиях, но возможно и скорость подачи при других схемах обработки).
Как было сказано ранее, заготовка представляет собой крупногабаритную тонкостенную оболочку вращения из хрупкого материала - ситалла. Она устанавливается на консольной оправке, имеющей две опоры (см. рисунок 1). В расчетной схеме изгибных колебаний заготовка с оправкой представляются одной массой m23. Одно из основных свойств этой массы - переменная жесткость и изменение собственной частоты вдоль оси подсистемы. На рисунке 4 представлено изменение амплитуды вынужденных колебаний подсистем «оправка - заготовка», «шпиндель – агрегатная головка – суппорт», «шпиндель станка» в зависимости от места приложения нагрузки.
Рисунок 4 - Изменение амплитуды вынужденных колебаний подсистемы «оправка-заготовка» - m23, «шпиндель-агрегатная головка-суппорт» - m1, «шпиндель станка» - m4.
Из графиков, представленных на рисунке 4, видно, что амплитуда колебаний подсистемы «оправка - заготовка» при движении инструмента от носка изделия к фланцу уменьшается от 0,03 мм до 0,001 мм, что можно объяснить увеличением жесткости. Возрастание амплитуды колебаний на участке 2 – 3 связано с увеличением силы резания. Амплитуда колебаний подсистемы «шпиндель - агрегатная головка – суппорт» изменяется в незначительном диапазоне (от 0,001 до 0,01 мм) и зависит от величины силы резания и динамических характеристик технологической системы. Амплитуда колебаний подсистемы шпинделя станка изменяется в диапазоне от 0,001 до 0,02 мм и также зависит от величины силы резания и динамических характеристик технологической системы шлифования.
Уровень колебаний, возникающих в системе при абразивной обработке оболочки, существенно сказывается на качестве формируемой поверхности изделия, прежде всего, на ее волнистости. Сравнение результатов расчета динамического состояния системы, изменяющегося во времени, с экспериментально полученными данными профилограммы обработанной поверхности заготовки для области, ограничен-ной точками 4-3 (см. рисунок 1), представлено на рисунке 5.
На рисунке 5, а - верхний график представляет изменение общей амплитуды колебаний в зоне контакта круга и оболочки (наложение средней и нижней временной характеристик); средний – отражает динамическое поведение оболочки; нижний – изменение амплитуды изгибных колебаний в зоне контакта подсистем «шпиндель - агрегатная головка – суппорт» и «шпиндельный узел – оправка - деталь». Из приведенных графиков видно, что в зоне контакта в области, ограниченной точками 4 - 3, основная час-тота колебаний составляет 0,17 Гц (параметрические колебания оболочки).
Рисунок 4 - Изменение амплитуды вынужденных колебаний подсистемы «оправка-заготовка» - m23, «шпиндель-агрегатная головка-суппорт» - m1, «шпиндель станка» - m4.
Результаты сопоставления верхнего графика, приведенного на рисунке 5, а, с профилограммой поверхности детали, обработанной в рассматриваемых условиях (см. рисунок 5, б), свидетельствуют о том, что микропрофиль, прежде всего волнистость формируемой поверхности, в значительной мере определяется интенсивностью колебательного процесса, возникающего в зоне контакта инструмента и маложесткой заготовки. Частота колебаний оболочки, определенных по результатам обсчета профилограммы шлифованной поверхности, составила 0,11 Гц, против 0,17 Гц, полученных по результатам аналитического расчета. Таким образом, волнистость, как параметр качества обработанной поверхности тонко-стенной оболочки вращения после алмазного шлифования, в значительной степени определяется харак-теристиками колебаний, вызванных вибрациями, возникающими в зоне контакта инструмента и заготовки.
Выводы
В представленной работе приведены результаты исследований динамического состояния технологической системы алмазно-абразивной обработки тонкостенных оболочек из ситалла. Расчетным путем, на основании разработанной эквивалентной схемы колебаний технологической системы были найдены амплитуды и частоты колебаний, возникающих в зоне контакта заготовки и шлифовального круга.
Результаты расчетов показали следующее.
1. Основное влияние на возбуждение вибраций изгибных колебаний в технологической системе оказывает биение шлифовального круга (величина биения колеблется от 0,02 до 0,06 мм, частота возбуждаемых колебаний 48 Гц и 63 Гц при скорости шлифовального круга, соответственно, 30 м/с и 40 м/с ). Меньшее влияние оказывает огранка шлифовального круга, создающая источник возбуждения с частотой от 144 Гц до 189 Гц. В конусной части заготовки на вибрации в зоне резания оказывают влияние изгибные колебания подсистемы «оправка - заготовка», и в меньшей степени - шпиндельный узел, что объясняется пониженной жесткостью подсистемы обработки в этой области заготовки. Результатом этих вибраций является уровень шероховатости и волнистости поверхности обработанной оболочки.
2. В параболической части заготовки на интенсивность вибраций в зоне резания оказывают влияние параметрические колебания оболочки, вызывающие значительное возрастание амплитуды и частоты колебаний, приводящее к появлению волнистости формируемой поверхности. Шаг волнистости зависит от частоты колебаний в зоне контакта. Расчетная частота колебаний составила 0,17 Гц против реальной частоты колебаний в 0,11 Гц, найденной по профилограмме обработанной поверхности заготовки, что свидетельствует о достоверности выполненных расчетов.
3. Основными факторами, определяющими амплитуду и частоту колебаний оболочки, являются: собственная частота и форма ее колебаний (зависят как от самой формы, размеров, геометрии, толщины оболочки, так и от схемы её установки на станке, в том числе и от конструкции оправки); величины приложенной нагрузки (силы резания); режима резания (в частности, скорости вращения заготовки при обработке).
На основании полученных результатов планируется разработка технологических мероприятий по повышению устойчивости процесса шлифования тонкостенных оболочек вращения.
Список использованной литературы
1. Капанец Э.Ф. Точность обработки при шлифовании / Э.Ф Капанец, К.К. Кузьмич, В.И. Прибыльскийи др.; под ред. П.И. Ящерицына. – Мн.: Наука и техника, 1987. – 152 с.
2.Гусев В.В. Исследование динамических характеристик элементов системы СПИД при шлифовании деталей сложной пространственной формы из ситаллов / В.В. Гусев, Л.П. Калафатова, И.С. Каракуц // Надійність інструменту та оптимізація технологічних систем. Збірник наукових праць. – Краматорск, 2007. – Вип. №21. – С. 148 – 155.
3. Якушев Н.З. Коническая оболочка под действием подвижных нагрузок / Якушев Н. З., Якушев Р. С. // Исследования по теории пластин и оболочек. - Казань: Изд-во Казанского ун-та, 1975. - С. 303 - 316.
4. Гусев В.В. Обоснование расчетной схемы для исследования динамического состояния технологической системы алмазно-абразивной обработки тонкостенных оболочек из ситалла / Гусев В.В., Калафатова Л.П., Олейник С.Ю. // Сучасні технології в машинобудуванні. - Харьков: Изд-во НТУ "ХПИ", 2011. - С. 14-23.