Выполнен анализ железорудной базы металлургического производства Украины. Представлены данные об объемах производства и поставок предприятий горно-добывающей отрасли. Проанализирован уровень материальных затрат металлургических предприятий и возможности их снижения за счет использования вторичных материалов.
Черная металлургия является базовой отраслью украинской экономики, которая
определяет величину внутреннего валового продукта (ВВП), а также темпы роста
других отраслей промышленности. Украинский металл пользуется спросом на мировых
рынках - большая часть продукции металлургических предприятий (более 80% от общего
объема производства, который в 2004 г составил 39,74 млн. т) реализуется за рубежом.
По данным Национального института экономических исследований горно-металлургический
комплекс (ГМК) в 2003 г обеспечил около 26% ВВП и почти 40% валютных поступлений в
Украину. Доля металлургии в промышленности составила: по производству товарной
продукции – 13,4%, по основным фондам – 13% и по численности работников – 6,5%.
Еще недавно черная металлургия была наиболее рентабельной отраслью производства:
средняя рентабельность металлургических предприятий в 2003 г составляла 16,6%, в 2004
г – 17,7%. Многие предприятия имели более высокую рентабельность, так, например, в
2004 г рентабельность ММК им. Ильича составляла 33,4%; Криворожстали 39,6% [1].
Это значительно выше рентабельности металлургического производства многих развитых, в
том числе европейских стран. Высокой рентабельности способствовали конъюнктура
мирового рынка черных металлов, более низкая стоимость украинских сырьевых и трудовых
ресурсов, а также высокий внутренний потенциал отрасли, интенсивное инновационное
развитие которой предусматривает использование наиболее прогрессивных мировых
технологий в различных областях науки и техники.
Одной из особенностей металлургического производства является высокая материало- и энергоемкость металлопродукции. Примерный расход шихтовых материалов и топлива на предприятиях с полным металлургическим циклом представлен в таблице 1.
Таблица 1 – Интегрированный (с учетом предыдущих переделов) удельный расход сырья и топлива на 1 т стали на предприятиях с полным металлургическим циклом на примере ММК им. Ильича
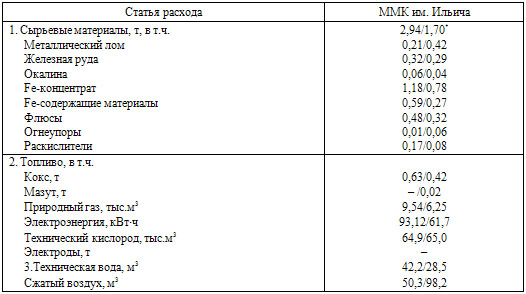
* числитель- конвертерное, знаменатель- мартеновское производство
В среднем по отрасли на выплавку 1 т сырой стали расходуется более 2 т железорудных материалов, 0,54 т твердого топлива (кокса и коксовой мелочи), а также до 20 кг различных видов раскислителей и более 350 кг флюсов (извести и известняка). Одновременно с этим расходуется 9,2 м3 природного газа и 92 кВт•ч (331,2 МДж) электроэнергии. Доля металлургии в общем потреблении энергоресурсов Украины составляет: по электроэнергии – 15,6 %; по топливу – 14,2 % [2].
По данным Министерства промышленной политики структура операционных затрат металлургических предприятий в 2003 г составляла, %[3]:
- амортизация основных фондов – 3,26;
- на оплату труда – 7,75;
- отчисления на социальные нужды – 2,90;
- прочие расходы – 0,89;
- материальные затраты, (всего) – 85,2; (100)*, в т.ч.:
- железорудное сырье – 14,9; (17,50);
- кокс – 17,7; (20,75);
- лом стальной – 6,4; (7,55);
- газ природный – 6,8; (8,00);
- электроэнергия – 6,8; (8,00);
- другое сырье – 27,3; (32,00);
- железнодорожный тариф – 5,3; (6,20).
*- % материальных затрат.
Как следует из представленных данных, основное количество затрат металлургических предприятий связано с приобретением сырья и топлива. Общие материальные затраты на производство продукции постоянно растут. В 2004 г в результате роста цен на сырье, топливо и энергоносители материальные затраты предприятий увеличились на 64 %. В абсолютном выражении за 9 месяцев 2004 г они составили 33,8 млрд. грн по сравнению с 20,41 млрд. грн в 2003 г.
Столь высокий уровень материальных затрат (80-85 % от общего объема) в структуре себестоимости продукции является основным дестабилизирующим фактором отрасли. Высокая материало- и энергоемкость продукции связывает основную часть оборотного капитала в фактических (складских) и виртуальных (предоплата) запасах, а также в кредитах НДС (закупка сырья на внутреннем рынке, а реализация основной части продукции – на внешнем), возмещение которых происходит с опозданием. Поэтому любые изменения в структуре цен сырьевых материалов и топлива или в их расходе оказывают существенное влияние на технико-экономические показатели и эффективность работы предприятий.
Проанализируем фактический уровень и возможность снижения указанных затрат в условиях рыночной экономики Украины. Данный вопрос рассмотрим в трех аспектах - с позиции стабильного обеспечения металлургическим сырьем (дефицит сырья существует, и в дальнейшем будет увеличиваться), с точки зрения регулирования цен и экономии материалов.
Основные затраты металлургов связаны с приобретением железорудного сырья (железной руды, концентрата и окатышей), кокса и металлического лома. Дефицит сырья и цены на эти материалы отражают общие тенденции экономического развития и определяют проблемы украинской металлургии на внешних и внутренних рынках.
Ведущей тенденцией мирового развития стала глобализация. В результате глобальных изменений произошла концентрация капитала и собственности, в том числе резко возросла степень монополизации производства многих видов продукции. Сегодня на мировом рынке железорудных материалов семь корпораций контролируют производство и продажу около 80% этого сырья. А рынок металла (второй по объему продаж после нефтяного) является самым непрозрачным товарным рынком.
Внутренние цены на металлургическое сырье и продукцию в силу объективных причин значительно отличаются от мировых - на многие виды сырья и топлива они существенно ниже. По сути дела экономическая политика предприятий связана с балансом внутренних и мировых цен на сырьевые материалы и конечную продукцию. Это создает предпосылки для экспорта необходимых для собственного производства сырьевых материалов и постоянное напряжение на внутреннем рынке.
Напряженность усиливается и другими факторами – повышением цен на энергоносители и железнодорожные тарифы, а также монополизацией внутреннего рынка. За последние четыре года отечественным финансово-промышленным группам (ФПГ) удалось создать вертикально-интегрированные схемы «руда – кокс – металл» и приватизировать практически всю горнодобывающую отрасль. В результате этого многие, не входящие в состав групп, предприятия не имеют степени свободы в выборе поставщиков в плане стоимости и объема поставок и вынуждены часть сырья приобретать за рубежом по более высоким ценам. Отечественные производители, наоборот, не всегда могут найти надежных покупателей и поэтому часть сырья экспортируют за пределы Украины. Рассмотрим причины этих процессов на конкретных примерах.
Обеспечение железорудными ресурсами является самой актуальной проблемой стабильной работы металлургических предприятий. С точки зрения возможности обеспечения железорудным сырьем (ЖРС) у отечественных производителей не должно быть проблем.
Промышленные запасы железной руды Украины оцениваются в 16,8 млрд. т. Содержание железа в рудах отдельных месторождений колеблется в широких пределах – от 25 до 58%. Богатые руды применяют в металлургическом производстве без предварительной подготовки, бедные – обогащают на горно-обогатительных комбинатах (ГОКах) с целью увеличения содержания железа и используются в виде концентратов. Основные запасы и добыча (70-80%) приходятся на Криворожский железорудный бассейн.
Основными видами железорудного сырья являются железная руда (обычная и аглоруда, которая идет на аглофабрику), железорудный концентрат, используемый для производства агломерата, товарный агломерат и окатыши, применяемые в доменном и сталеплавильном производстве.
Отечественные запасы и производство этих материалов достаточны для обеспечения всех предприятий отрасли – табл. 2. Рынок традиционно распределен между поставщиками и потребителями в соответствии с особенностями производства. Структура этих связей и объемы поставок представлены в табл. 3 и 4. Производителями железорудной продукции в Украине являются Ингулецкий, Северный, Полтавский, Центральный ГОКи, которые постоянно увеличивают производство железорудного концентрата. Лидером производства концентрата выступает Ингулецкий ГОК (13,7 млн. т концентрата в 2003 г). Среди производителей неагломерированной железной руды следует отметить высокие темпы производства ОАО «Криворожсталь» и ГОКа «Сухая балка». Объемы и темпы производства окатышей также растут. В 2003 г железорудные окатыши производили Центральный, Северный и Полтавский ГОКи в количествах 2,0; 5,9 и 7,0 млн. т соответственно. О дефиците этого вида сырья свидетельствуют более высокие внутренние цены, которые почти в 1,5 раза выше европейских.
Таблица 2 – Объемы и структура производства (потребления) железорудных материалов в 2003 г по данным Укррудпрома, тыс. т. [4]
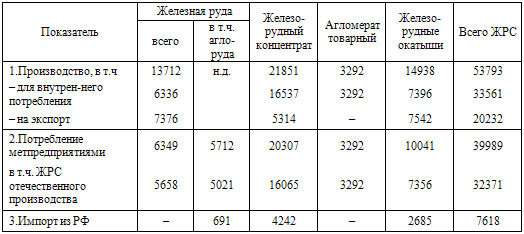
В Украине только два предприятия – ОАО «Южный ГОК» и ОАО «ММК им. Ильича» производят товарный агломерат с годовым объемом 4,3 и 3,0 млн. т соответственно. Весь производимый агломерат распределен между предприятиями, которые его не производят – ОАО «ДМЗ им. Петровского», ОАО «Донецкий МЗ» и ОАО «Макеевский МК» и частично ОАО «Азовсталь», производственная мощность аглофабрики которого составляет 2,0 млн. т в год, что недостаточно для собственных нужд предприятия.
Таблица 3 – Анализ производства основных видов ЖРС предприятиями Украины в 2003 г. по данным открытых источников: (www.ukrindustrial.com, www.context.ua.com,«Контракты» 2004. – № 42)
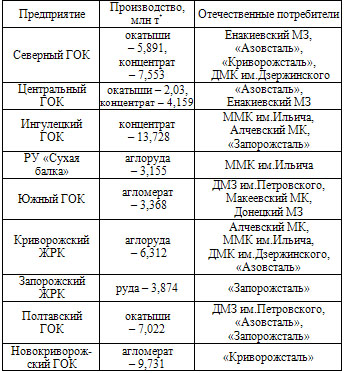
Таблица 4 – Структура и объемы потребления железорудной продукции металлургическими предприятиями Украины в 2003 г., тыс. тонн [4]
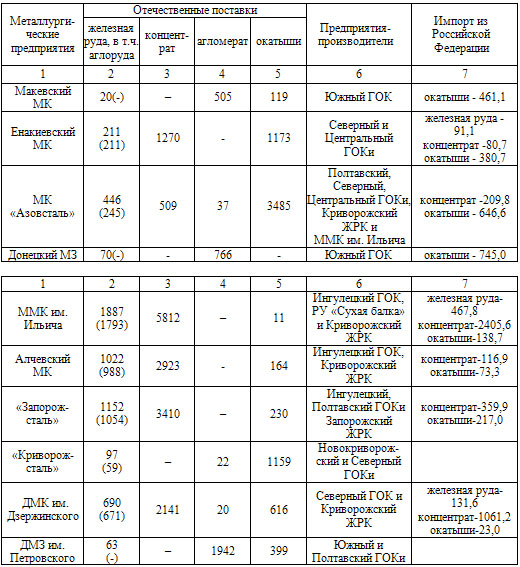
Основная проблема предприятий горнодобывающей отрасли – высокая степень износа оборудования (60-70%), которое при существующем уровне рентабельности не может быть восстановлено за счет собственных средств. По ряду причин, средняя рентабельность предприятий горнодобывающего комплекса ниже рентабельности металлургических предприятий (14-15% в 2004 г). Указанной рентабельности недостаточно для внутренних инвестиций с целью обновления имеющихся мощностей. По мнению ведущих специалистов, горнорудные предприятия могут нормально работать только при рентабельности 46%, которая являлась плановым показателем отрасли до 1990 г. [4] Однако, несмотря на эту и другие проблемы отрасли, объемы производства железорудных материалов постоянно растут. В 2003 г в Украине несмотря на неполную загруженность мощностей горнорудных предприятий (около 60%), было произведено 62,6, в 2004 г – около 70,0 млн. т железорудного сырья (из них 50,5 млн. т концентрата и 16,3 млн. т аглоруды) [1]. При этом, несмотря на постоянный дефицит сырья, часть продукции (15-18 млн. т) ежегодно экспортируется за рубеж.
Экспортные поставки производители мотивируют более высокой стоимостью продукции на внешних рынках (в среднем стоимость вывозимого сырья на 6,5–7% выше) и частыми срывами договорных обязательств, которые подписываются предприятиями разной формой собственности и не всегда выполняются. Срывы поставок происходят также за счет отсутствия необходимого количества подвижного состава. В отрасли существует общий дефицит полувагонов, часть из которых находится у частных операторов.
Некоторые предприятия после заключения договора, стремясь снизить цены, затягивают оплату сырья. Поэтому опасения ГОКов, что произведенная для внутреннего рынка продукция может оказаться невостребованной, а долго хранить на складах концентрат и окатыши нельзя, так как в процессе складирования они теряют в качестве, вполне реальны.
С целью сокращения экспорта Министерством экономики Украины введено (и сохранено на 2005 год) решение лицензирования поставок ЖРС. Несмотря на это, многие предприятия ГОКа заявляют об увеличении экспорта своей продукции.
Дефицит железорудной продукции компенсируется импортными поставками из России - из Стойленского (концентрат), Лебединского и Михайловского ГОКов. Российские компании также контролируют добычу и производство около 20% ЖРС украинских предприятий, в том числе практически все производство и поставки Ингулецкого ГОКа.
Крупнейшими потребителями импортного сырья являются ОАО ММК им. Ильича, ЗАО «Донецксталь» и ОАО «Запорожсталь».
В 2003 г объем импорта составил 7,6 млн. т., в 2004 г он сократился почти в 2,5 раза - до 3 млн. т. (из них концентрат- 63%, окатыши – 19%, агломерат - 18%). При этом следует отметить, что вопрос сокращения импорта сырья из России до конца не решен, т.к. связан не только с внутренним дефицитом сырья, но и с высокими качественными показателями импортируемой продукции, которая имеет более высокое содержание железа. Поэтому, несмотря на ввозные пошлины, ряд предприятий продолжают работать на импортном сырье. Будут ли в дальнейшем предприятия отрасли потреблять импортную продукцию, пока не известно. Тем более, что по некоторым видам сырья (в том числе - по окатышам) внутренние цены значительно превосходят мировые.
Таким образом, периодические перебои в снабжении предприятий отрасли ЖРС объясняются высокой степенью монополизации горно-обогатительного комплекса, которая оказывает доминирующее влияние на стоимость и механизм распределения производимой продукции.
В условиях экономической нестабильности предприятий, а также глобализации капитала и производства из-за отсутствия конкуренции рыночный механизм регулирования цен не действует. Потребитель практически не может влиять на стоимость приобретаемого сырья. Цены на ЖРС устанавливаются производителями в одностороннем порядке.
За последние четыре года цены на железорудное сырье постоянно росли. Так, например, за 2001 г стоимость железорудного сырья возросла на 30-52%, за 2002 г – на 5-11%, за 2003 г – на 21-34%. В первом квартале 2004 г стоимость сырья возросла на 10-32% и составила в среднем: железная руда - 97,2; концентрат - 110,9; окатыши -129,7; агломерат - 228,0 грн/т. Цены по отрасли относительно стабильны.
По мнению ген. директора ПХО «Металлургпром» В. Харахулаха [5], пока на внутреннем рынке не будет создан нормальный экономический инструмент регулирования цен, нельзя рассчитывать на стабильность внутренних поставок ЖРС и резкое снижение экспорта. Вместе с тем вопрос о стабильном обеспечении ЖРС отечественных предприятий может быть решен только за счет сокращения экспорта.
Мировые процессы и цены формируют взаимоотношения отечественного рынка, и если внутренние цены меньше мировых, то часть сырья всегда будет экспортироваться из страны. Поэтому, несмотря на то, что ЖРС в Украине производится в достаточном количестве, получить его могут не все предприятия. Сократить затраты на ЖРС можно за счет снижения расходных коэффициентов этих материалов, в том числе в результате использования различных железосодержащих материалов вторичного происхождения. В отрасли накоплен достаточный опыт использования в составе агломерационной шихты металлургических шламов и шлаков, пыли электрофильтров, колошниковой пыли а также других материалов. Проблемы – в стереотипе взглядов на химический и фазовый состав шихты - в количестве используемых добавок и стабилизации их состава по содержанию железа, а также в их предварительной подготовке к использованию.
Наиболее апробированной является технология использования в составе агломерационной шихты металлургических шламов. Масштабы накопления этих материалов на многих предприятиях соизмеримы с масштабом собственного агломерационного производства. Так, например, на ММК им. Ильича при выплавке одной тонны стали в среднем образуется около 250 кг жидких шламов: из них 192 – в агломерационном, 25 – в доменном, 18 кг– в сталеплавильном производстве [2]. Часть этих материалов после дополнительной подготовки - усреднения, сушки, окомкования или брикетирования может быть использована при производстве агломерата.
В качестве осушающих добавок влажных шламов традиционно используют известь, а также углеродсодержащие материалы (кокс, торф и другие), которые хорошо поглощают влагу и придают материалам сыпучесть. Для повышения прочности железорудных брикетов также применяют доступные материалы (жидкое стекло, ССБ, лигносульфаты), в том числе с относительно высоким содержанием серы. Последнее объясняется высокой степенью удаления серы из шихты в процессе агломерации (до 80%).
Некоторые предприятия в состав агломерационной шихты вводят металлосодержащие отсевы сталеплавильных шлаков в количестве 15-40 кг/т. В агломерационной шихте ЕМЗ содержится до 34 кг обогащенного мартеновского шлака с Feобщ 26-50%, около 25 кг колошниковой пыли и 17-25 кг осушенных шламов [6]. На ММК им. Ильича в качестве металлосодержащих добавок используют около 25 кг отсевов дробленного конвертерного шлака, 12-15 кг прокатной окалины, около 8 кг колошниковой пыли, 350 кг осушенной смеси собственных шламов и шламов других предприятий отрасли (МК «Азовсталь» и МЗ им. Петровского) с содержанием железа от 30 до 55%.. Влажность применяемых шламов составляет от 5 до 15%.
Использование при агломерации вторичных материалов позволяет вернуть в производство значительное количество минерального сырья, заменяющего концентрат, аглоруду, известняк и топливо. Агломераты, полученные с использованием вторичных железорудных материалов, обладают повышенной температурой начала, но достаточно узким интервалом размягчения. Это повышает их ценность при доменной плавке. По технологическим параметрам они практически не отличаются от традиционной продукции полученной на основе концентрата. В условиях ММК им. Ильича одна тонна такой добавки позволяет сэкономить до 750 кг концентрата, 200 кг известняка, 25 кг марганцевой руды, 48 кг аглотоплива.
Согласно прогнозам максимальное содержание железосодержащих добавок в агломерационной шихте украинских заводов может достигать 500 кг/т агломерата и обеспечивает содержание Feобщ 40-48% в готовом продукте [7]. При этом следует отметить, что в мировой практике известны примеры более высокого расхода в агломерационной шихте указанных материалов. Так, например, на аглофабрике «Инленд Стил» в Ист-Чикаго (США) агломерат производится только из железосодержащих отходов металлургического производства без добавок руды. Отходы включают дробленые шлаки (конвертерный, мартеновский и электропечной) с размером частиц до 10 мм, прокатную окалину, отсев окатышей трех типов (менее 6,3 мм), а также колошниковую пыль доменных печей и агломерационные шламы [8].
Снизить общий расход железосодержащих материалов на выплавку стали можно за счет использования вторичных материалов в шихте доменной плавки. В настоящее время с этой целью широко применяют металлодобавки (окалину, сортированные сталеплавильные шлаки, отходы готового металла), расход которых на металлургических предприятиях США составляет около 250, Украины и России – до 30 кг/т чугуна. В шихте доменной печи ММК им. Ильича используется более 20 кг дробленного конвертерного шлака с содержанием железа до 18% и около 5 кг сварочного шлака с содержанием железа 60-65%.
Согласно расчетам расход этих материалов в шихте доменных печей украинских предприятий может достигать 135 кг/т чугуна при сохранении общего содержания железа в рудной части шихты 55-57%. При этом в результате сокращения расхода извести и соответственно уменьшения выхода шлака примерно на 10% прогнозируется одновременное снижение расхода кокса до 30 кг/т чугуна [8].
На предприятиях, имеющих установки по вдуванию пылеугольного топлива, возможна подача порошкообразного железорудного сырья в объем доменной печи через фурмы. Однако этот вопрос находится в стадии теоретических разработок, и не прошел промышленного опробования.
Особый интерес для металлургов представляют красные шламы - железосодержащие шламы глиноземного производства, которые содержат 43-45% окиси железа и 13-22% окиси алюминия. Объемы образования этих материалов в Украине соизмеримы с производством некоторых предприятий Укррудпрома. На Николаевском глиноземном заводе (НГЗ) ежегодно образуется около одного, а в шламонакопителях содержится более 20 млн. т. этого материала [10,11].Наиболее перспективным считают использование красного шлама при производстве агломерата и окатышей. Такие работы велись на металлургических комбинатах им. Ильича, «Азовсталь», «Криворожсталь» а также в СевГоке. Однако в результате высокой влажности 45-55% даже после длительного хранения красные шламы могут быть использованы в аглодоменном производстве только после специальной обработки – обезвоживания (в гидроциклонах или мембранных фильтпрессах), а затем окомкования или брикетирования.
Использованию красного шлама в составе доменной шихты помимо высокой влажности препятствует наличие до 6% щелочных металлов в виде оксидов натрия, калия и циркония, которые оказывают существенное влияние на физико-химические свойства доменных шлаков.
Многие считают целесообразным использовать красный шлам в виде брикетов с прокатной окалиной [10]. Баланс щелочных металлов, выполненный авторами этой работы для МК «Азовсталь» позволяет регламентировать состав (%, красный шлам – 50, окалина – 43, связующие – 7) и расход брикетов – 120-150 кг/т чугуна, которая позволяет использовать это железорудное сырье в шихте доменной печи без ухудшения шлакового режима плавки. В настоящее время в условиях НГЗ разработана технология брикетирования красных шламов совместно с окалиной, известью, металлургическим шламом и другими материалами, что значительно расширяет диапазон применения брикетов в металлургическом производстве.
Список использованных источников:
- Цифры в контексте ГМК. // Металл. – 2005. – №1(61). – с.6-9
- Назюта Л.Ю., Лактионова О.Е., Рыбко А.С. Затраты в
производственно-сбытовых логистических системах: механизм управления:
Монография/ НАН Украины. Ин-т экономики пром. – Донецк, 2004. – 297 с.
- А. Неустроев. Удержать цены.// Металл. – 2004. – № 2 (50). – с. 8-11.
- Уйти от нестабильности. // Металл. – 2004. – № 1 (49). – с. 29-34.
- Еще раз о сырье. // Металл. – №1(61) – 2005. – с. 10-12.
- Пархоменко А.Д., Рузина А.В. Опыт использования обогащенного
мартеновского шлака в агломерационной шихте ОАО «АМК» // Металлургическая
и горнорудная промышленность. – 2004. – №4. – с.11-12.
- Дембицкий Ю.В., Демура Н.Т, Падалка В.П. Технология использования в
агломерационной шихте частично подготовленных шламов металлургического
производства // Металл и литье Украины. – 1997. – №6-7. – с.9-10.
- Отчет о НИР «Разработка технологии агломерации с максимальным
расходом железосодержащих отходов», ПГТУ. Мариуполь, 1994. – 86 с. с илл.
- Шеремет В.А., Кекух А.В., Орег Г.А. и др. Исследования
эффективности применения мелкофракционных металоотсевов шлаковых
отвалов в доменной шихте // Сталь. – 2004. – №6. – с. 9-10.
- Антипов В.М., Дидевич А.В., Овчинников Н.А. и др. Брикетирование
красных шламов глиноземного производства // Металлургическая и горнорудная
промышленность. – 2004. – №6. – с.19-22.
- Л. Волошина. Отходы в доходы // Металл. – 2002. – №4. – с.20-22.