Реферат за темою випускної роботи
Зміст
- Вступ
- 1. Актуальність теми
- 2. Аналіз особливостей пристрою і експлуатації об'єкта досліджень
- 3. Цілі і завдання дослідження
- 4. Теоретичний аналіз властивостей пристроїв прискореного гальмування АД
- Висновки
- Перелік посилань
Вступ
Основою технічного процесу на вугільних шахтах є широке використання високопродуктивних видобувних комплексів, оснащених сучасним вибухобезпечним електрообладнанням. Їх впровадження забезпечує значне підвищення продуктивності роботи підприємства. Висока ефективність вуглевидобутку в значній мірі залежить від ефективної роботи шахтного транспорту, зокрема конвеєрного, значення якого стає все більш важливим у зв'язку із збільшенням потужності вугледобувних машин. В даний час в якості забійних повсюдно використовуються скребкові конвеєри, які найбільш адаптовані до умов функціонування очисного механізованого комплексу. Для провідних вугледобувних шахт характерне підвищення ступеня концентрації гірничих робіт, зростання навантаження на очисний вибій, при скороченні їх числа і одночасному збільшенні довжини і швидкості посування. Це обумовлює підвищення навантаження на забійний скребковий конвеєр. Як наслідок, розробляються і впроваджуються у виробництво скребкові конвеєри більшої довжини і з більш потужними приводами.
1. Актуальність теми
З аналізу конструкції та умов експлуатації скребкових конвеєрів виходить, що пуск їх супроводжується високим моментом опору, який створюється ланцюгом зі шкребками і переміщуваної гірською масою. Крім цього конструкція скребкового конвеєра допускає заштибовки і заклинювання тягового органу, що є критичною для скребкового ланцюга. З метою здійснення зниження перевантажень приводу вони оснащені нерегульованої гідромуфтою. Досвід експлуатації показує, що свої пускозахисні функції гідромуфта виконує незадовільно, має малий фактичний термін служби, низьку надійність. Володіючи значним моментом інерції, обертаюча частина муфти підвищує розтяжне зусилля в скребковому ланцюгу в момент заклинювання, чим сприяє не захисту, а пориву останньої.
Спрацьовування захисту гідромуфти пов'язане з простоями скребкового конвеєра. Здійснюється витрата часу на повторну заливку в неї емульсії, встановлення нової плавкої пробки. Таким чином обумовлюється актуальність створення більш ефективного методу захисту скребкового конвеєра від стопоріння.
2. Аналіз особливостей пристрою і експлуатації об'єкта досліджень
На наш час скребкові конвеєри залишаються самим розповсюдженним видом транспортних засобів на шахтах, стрічкових конвеєров менше, ніж скребкових в 1,6 рази, електровозів – в 2,5 рази (рис. 1) [5].
Привід конвеєра складається з рами приводу, одного або двох приводних блоків (двигун – гідромуфта – редуктор) і двох привідних зірочок, яка передає тягове зусилля на скребковий ланцюг конвеєра.
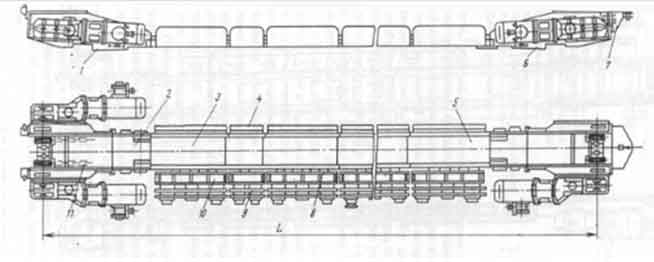
Рисунок 1 – Типова конструкція шахтного скребкового конвеєра: привід головного 1, перехідні секції 2 у головного і кінцевого приводів, перехідні рештаки 3 та 5, лемеші 4, привід кінцевий 6 (або кінцевий голівки) лінійний рештак, що відхиляє ролик 7 для направлення каната запобіжної лебідки комбайна, направляючі комбайна 8, борту кабелепрокладача 9, борту 10, скребковий ланцюг 11, кронштейни для розміщення кабелів, кронштейни світильників [5].
Функціональним елементом приводу конвеєра, спеціально призначеним для уповільнення розгону, є гідромуфта, що містить оребрені насосні й турбінне колеса, порожнина між якими заповнена емульсією. Вплив гідромуфти на динаміку пуску електроприводу скребкового конвеєра пояснює її механічну характеристику (рис. 2):
Mm = a1vн2 + a2vн vm + a3vm2 , (1)
де а1, а2, а3 – постійні для окремих зон сімейства механічних характеристик; Мm – момент на валу турбінного колеса гідромуфти; vн, vm – кутові швидкості насосного та турбінного коліс [5].
Близький до номінального момент на валу турбінного колеса гідромуфти в процесі пуску може бути отриманий при кутовій швидкості насосного колеса, близькою до номінальної. Тому, на початку пуску двигун конвеєра розганяється майже без навантаження, а наприкінці розгону ротора рух ривком передається до скребкового ланцюга, що є чинником підвищення динамічних навантажень у трансмісії конвеєра.
Різке гальмування, викликане раптовим стопоріння тягового органу, є найбільш небезпечним режимом роботи конвеєра, оскільки його рухомі елементи, крім статичних сил, які розвиваються двигуном за рахунок електромагнітного моменту, знаходяться під впливом динамічних сил, викликаних уповільненням рухомих мас.
За умови, що стопоріння тягового органу відбувається миттєво (перетин, який заклинило, залишається нерухомим), і в разі нехтування масою заклиненого ділянки тягового органу і пружністю трансмісії, тобто вважаючи, що маса частин приводу, яка рухаються, є зосередженої в одній точці, модель конвеєра, буде мати вигляд [6].
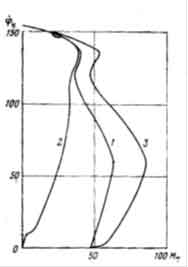
Рисунок 2 – Сукупність механічних характеристик гідромуфти: 1 – робоча, 2 – пускова, 3 – при роботі на стопоріння
Характер руху конвеєра і величини виникаючих зусиль після стопоріння визначаються в часі пружною деформацією u заклиненої ділянки тягового органу довжиною l як невагомого пружного тіла з твердістю с = E0 / l :
md2u/dt2 + cu - Fдв(v) = 0 , (2)
де m – сумарна приведена маса приводу; Fдв – зусилля в тяговому органі, що розвивається двигуном за рахунок електромагнітного моменту; v – швидкість маси приводу.
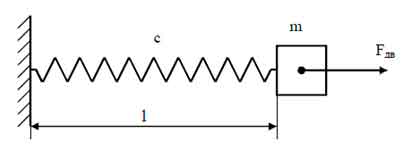
Рисунок 3 – Розрахункова схема процесу стопоріння конвеєра
Визначення максимального зусилля в тяговому органі, що розвивається двигуном за рахунок електромагнітного моменту при стопорінні скребкового ланцюга виконується за формулою:
Fmax = Fкр + √(F0 - Fкр) + cmvн2 , (3)
де Fкр – зусилля, при критичному моменті двигуна F0 – зусилля, що розвивається двигуном на початку гальмування; vн – номінальна швидкість тягового органуа.
З виразу (3) випливає, що в момент стопоріння скребкового ланцюга до зупинки турбінного колеса гідромуфти вся її маса обертається, складаючись з масою ротора АД, викликає значне додаткове розтяжне зусилля, підвищуючи загальне розтяжне зусилля в ланцюзі.
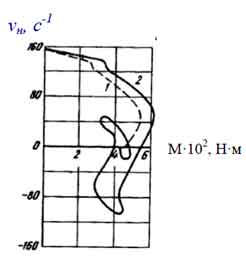
Рисунок 4 – Експериментальна перехідна характеристика гідромуфти ГПЕ-345 при стопорінні конвеєра [5]
Дослідженнями встановлено, що при стопорінні тягового органу в приводі конвеєра з гідромуфтою, виникають коливання навантаження і швидкості обертання турбінного колеса муфти (рис. 4). Це обумовлено тим, що динамічні навантаження при стопорінні призводять до значних деформацій розтягування ланцюгів. Пружна реакція ланцюгів після зупинки турбінного колеса розкручує його у зворотному напрямку, і гідромуфта працює деякий час у режимі противмикання, поки ланцюзі не витратять певну частину запасеної потенційної енергії. Після цього знову починається рух турбінного колеса і подальше стопоріння (рис. 5). У малопотужних конвеєрах коливання досить швидко загасають, однак, при збільшенні потужності приводів до 55 кВт коливання можуть носити стаціонарний характер при дуже великих амплітудах до виплавки запобіжних пробок гідромуфт. Таким чином, захисна дія гідромуфти полягає в кінематичному відділенні валів двигуна і редуктора шляхом злиття під тиском в зовнішнє середовище емульсійної рідини (що, як правило, розігріта до температури, більшої за 100 0С) через виплавки плавкою пробки. Ця дія відбувається у випадку зупинки турбінного колеса за умови, що на початку стопоріння не відбулося пориву скребковий ланцюга конвеєра.
Простої через відмову конвеєра складають 5-6% загального часу видобувних змін. Статистичні дослідження, проведені на 18 вахтах різних виробничих об'єднань Донбасу показують, що питома вага простоїв, пов'язаних з відшуканням і усуненням пориву скребкових ланцюгів становить, в середньому, 59,3% від загального часу простоїв скребкових конвеєрів. Найбільша кількість простоїв конвеєрів через пориви верхніх гілок їх ланцюгів становлять получасові та часові простої – відповідно, 25,8% і 23%. Найбільш часто зустрічаються простої скребкового конвеєра через пориви гілок скребкового ланцюга складають 2-2,5 години, але багато також простоїв тривалістю 6-8 годин (рис.1.1) [5].
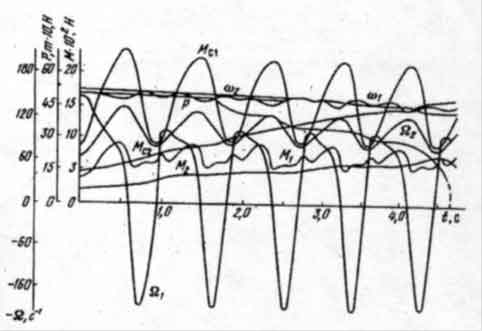
Рисунок 5 – Осцилограми параметрів приводу двоприводного скребкового конвеєра, оснащеного гідромуфтами, при стопорінні:Мс1, Мс2 – приведені до турбінних колес гідромуфти моменти опору головного і хвостового приводів, Нм;М1, М2 – гідродинамічні моменти, прикладені до турбінних колес головного і хвостового приводів, Нм; Р – максимальне зусилля в скребкових ланцюгах, Н; ω1, ω2 – кутові швидкості двигунів, с-1 [5]
Особливістю гідромуфти є низький рівень технологічності, обумовлений тим, що спрацьовування її захисту визначає тривалу зупинку конвеєра на час, необхідний для повторної заливки гідромуфти емульсією і установки нової запобіжної плавної вставки (рис. 6). Інтенсивність виплавнення вставок залежить від завантаженості конвеєра, рівня рідини в гідромуфті, якості гідромуфти і самої вставки, і в ряді випадків досягає 3-4 разів на зміну.
Таким чином, використання гідромуфт в приводах конвеєрів ставить у залежність роботу останніх і очисних комплексів у цілому від наявності плавких вставок на добувних ділянок. Відсутність таких змушує обслуговуючий персонал встановлювати замість плавких вставок сталеві болти, тобто йти на порушення вимог щодо експлуатації конвеєрів. У цьому випадку при перевантаженні конвеєра або спрацьовує друга ступінь захисту гідромуфти, або гідромуфта від надлишкового тиску розривається, руйнуючи, як правило, і приводний двигун. Це створює небезпеку травматизму людей [4].
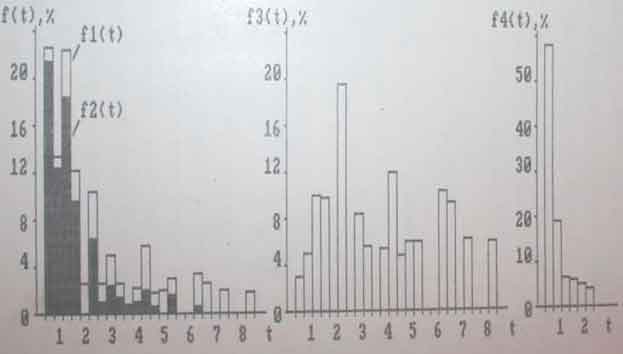
Рисунок 6 – Гістограми розподілу простоїв видобувних ділянок за відмов скребкових конвеєрів: f1(t) – пориви скребкових ланцюгів, у тому числі: f2(t) – пориви у верхній гілці, f3(t) – пориви у нижній гілці; f4(t) – виплавлення плавких вставок гідромуфт (t, час.)
Практичне застосування гідромуфти у складі приводу забійних конвеєрів показує що вона погано справляється зі своїми функціями. Також залишається невирішеним питання низького рівня технологічності, пов'язаного зі спрацьовуванням її захистів які супроводжуються зупинками конвеєра для заміни запобіжної плавкої вставки, а також низька надійність гідромуфти. Простої пов'язані із заміною плавких вставок, а також усуненням інших несправностей гідромуфт суттєво уповільнюють роботу всього очисного ділянки.
Особливості конструкції гідромуфти дозволяють судити про те, що вона є не тільки морально застарілим пусковим і захисним засобом через громіздкість робіт при монтажі і ремонті, низької надійності і як наслідок малим терміном служби, а й є не ефективним засобом пуску і захисту скребкового конвеєра [4].
3. Цілі і завдання дослідження
Метою дослідження є підвищення продуктивності роботи шахтного скребкового конвеєра шляхом запобігання пориву скребкового ланцюга при стопорінні на основі обґрунтування параметрів, структури і технічної реалізації засобів швидкодіючого захисту від динамічних перевантажень.
Для досягнення цієї мети повинні бути вирішені наступні завдання:
- Виконано аналітичний огляд досліджень і технічних рішень з проблематики забезпечення безаварійної експлуатації шахтних скребкових конвеєрів.
- Розробити математичну модель дослідження процесів в приводі скребкового конвеєра при стопорінні з метою визначення інформаційного параметра для застосування в засобі захисту.
- Обґрунтувати алгоритм та розробити структурну і принципову схеми засобів автоматичного захисту скребкового ланцюга від поривів при стопорінні.
- Обґрунтувати вимоги з безпечної та безаварійної експлуатації розробленого засоби автоматизації.
4. Теоретичний аналіз властивостей пристроїв прискореного гальмування АД
Специфічні умови експлуатації конвеєра викликають часті стопоріння його тягового органу, що призводить до поривів ланцюга і обумовлює необхідність створення відповідного захисту. При цьому, захисний пристрій не повинно істотно ускладнювати конструкцію електроприводу [2].
У зв'язку з викладеним, практичний інтерес представляє з'ясування властивостей відомих способів виявлення стопоріння приводу конвеєра:
- за інтенсивністю зміни кутової швидкості двигуна;
- за інтенсивністю зміни струму споживана двигуном.
Початковим станом будь-якого процесу гальмування є рушійний режим роботи двигуна. Ознакою гальмівного процесу є формування двигуном електромагнітного моменту, напрямок якого є зворотним щодо направлення кутовий швидкості вала двигуна. Одним з варіантів забезпечення захисту скребкового конвеєра від стопоріння може бути вимкнення і подальше гальмування електропривода.
Принцип індукційно-динамічного гальмування асинхронного двигуна.
Ефективність процесу динамічного гальмування асинхронного двигуна значною мірою визначається величиною постійного (випрямленого) струму у фазах його статора. З іншого боку, величина цього струму визначається напругою підведена до статора величиною ЕРС обертання, яка індукована в обмотках статора обертовим полем струмів ротора. У разі, якщо ЕРС обертання за своєю полярністю буде збігатися з полярністю підведеної напруги, її дія буде спрямована на зменшення величини струму гальмування. Це буде визначатися різницею потенціалів миттєвих значень підведеної напруги і ЕРС обертання і приводити до зменшення інтенсивності гальмування двигуна. Таким чином, ефективне динамічне гальмування асинхронного двигуна може відбуватися за відсутності в його статорних обмотках зворотного ЕРС обертання.
Ефективність способу індукційно-динамічного гальмування асинхронного двигуна полягає в усуненні зазначеної ЕРС обертання (на початку гальмівного процесу), яке супроводжується створенням значних за амплітудою імпульсів гальмівного струму. У гірській промисловості режим індукційно-динамічного гальмування використовується для повільної зупинки електроприводів бремсбергових стрічкових конвеєрів, екстреної зупинки електроприводів інших гірських машин. Процес індукційно-динамічного гальмування створюється в силовій тиристорної схемою в ланцюзі статора асинхронного двигуна відповідно до рис. 7 і припускає чергування станів динамічної (ДГ), індукційного (ІГ) і, власне, індукційно-динамічного (ІДГ) гальмування двигуна.
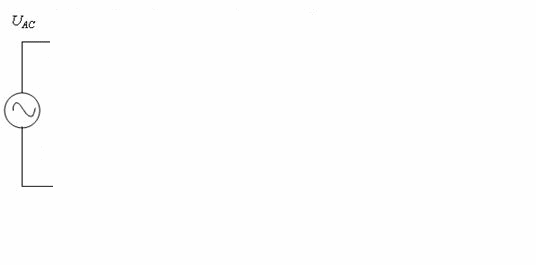
Рисунок 7 – Розрахункова схема проведення аналізу дослідження процесу індукційно-динамічного гальмування асинхронного двигуна
(анімація: 11 кадрів, 5 циклів повторення, 24 кілобайт)
Струм динамічного гальмування створюється за допомогою подачі на статор через тиристор VS1 и VS2 півхвиль лінійної напруги UАВ мережі. Ефект індукційного гальмування створюється при замиканні через тиристор VS3 ЕРС обертання ротора АД:
eоб = (1/√3)pωb(L0(2Is(k+1) + Isk) + Lr(2Ir(k+1) + Irk)) , (4)
де p – число пар полюсів асинхронного двигуна; Is; Ir – струми статора і ротора; L0 - индкутивность главного магнитного поля в расчете на фазу асинхронного двигателя.
Процес індукційно-динамічного гальмування ілюструється діаграмами відповідних параметрів асинхронного двигуна і живильної мережі (рис. 8). На інтервалах динамічного гальмування полярності UAB и eоб співпадають. При цьому UAB > eоб. ДГ визначається кутом відпирання a тиристорів VS1 и VS2, а закінчення – кутом їх провідності β. Гальмівний струм I визначається відмінністю між миттєвими значеннями UAB и eоб.
IТrн + LнdIТ/dt = UAB - eоб(АВ) , (5)
де rн; Lн – агальні активний опір і індуктивність ланцюга протікання гальмівного струму. На інтервалі ІГ тиристор 3 знаходиться у провідному стані, в той час як, тиристори VS1 і VS2 – у непровідному. Величина гальмівного струму IТ визначається миттєвим значенням ЕДС обертання двигуна (eоб).
IТrн + LнdIТ/dt = |eоб(АВ)| , (6)
На кожному з інтервалів ДГ і ІГ величина ЕРС обертання визначається відповідними її амплітудою (Евр mi) та початковою фазою (γ):
Eоб = I′Тr′Т((1 - s)/s) , (7)
eобi = Eобmi sin(ωbit + γ) , (8)
де ωbi = ω0(1 - s) – кутова частота ЕРС обертання, що відповідає i-му інтервалу гальмування, зменшується, остаточно, до нуля. У міру зменшення кутової швидкості асинхронного двигуна зменшуються амплітуда і частота його ЕРС обертання, і настає стан, коли полярності UAB і eоб будуть відмінними один від одного. У цьому випадку тиристори VS1; VS2; VS3 перебувати у відкритому стані, а гальмівний струм двигуна IТ визначатися сумою абсолютних величин миттєвих значень UAB і eоб (інтервал ІДГ):
IТrн + LнdIТ/dt = UAB + |eоб(АВ)| , (9)
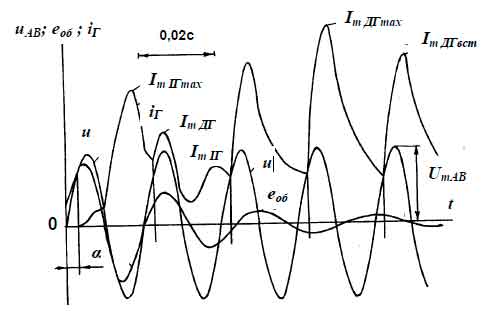
Рисунок 8 – Діаграми формування струму статора асинхронного двигуна в процесі його індукційно-динамічного гальмування
Вирази (1.52; 1.53; 1.56) вирішуються поетапно у порядку появи інтервалів з характерними, розглянутими вище станами гальмування. При цьому враховуються відповідні початковим умовам, величина і частота ЕРС обертання асинхронного двигуна. Їх рішенням є такий вираз:
Ir(t) = e-t/Tn(c + tk∫tn(U(t)/Lн)) e-t/Tn dt , (10)
де tn; tk – моменти початку і закінчення відповідного гальмівного інтервалу, c = U(tн) / zн; Тн - постійна часу обмоток ротора двигуна (Тн = Lн/rн).
За відсутності струму через VS1 і VS2 струм в тиристорі VS3 визначається величиною ЕРС самоіндукції асинхронного двигуна:
Ir(t) = Ir(tni) e-t/Tn , (11)
де tni – момент початку зазначеного вище i-го стану;
Гальмівний струм істотно залежить від величини кутів α відпирання тиристорів VS1; VS2. Його величина визначає рівень гальмівного моменту (МТ), що впливає на інтенсивність гальмування двигуна:
Mг = 2Ir2r21 / ω0Sнач , (12)
де ω0 і Sнач – відповідно, синхронна частота обертання ротора асинхронного двигуна і його ковзання на початку ІДГ.
Ir(t) = Irначe-t/Tn , (13)
де Irнач – початкова величина гальмівного струму відповідного інтервалу. По закінченні гасіння зворотного ЕРС обертання асинхронного двигуна його гальмівний струм буде визначатися тільки провідним станом тиристорів VS1; VS2 з урахуванням кута α їх фазового регулювання [2].
Висновки
Таким чином, процес індукційно-динамічного гальмування асинхронного двигуна дозволяє отримати високий гальмівний струм АД у встановленому режимі за рахунок ефективного зменщення ЕРС обертання, при цьому в процесі зниження ЕРС обертання для отримання початкових сплесків струму індукційного гальмування. Залежно від кутів відмикання тиристорів, інтенсивність гальмування АД середньої потужності знаходитися в межах 0,3-6 с. Такий результат робить систему індукційно-динамічного гальмування АД допустимої щодо до електроприводу гірничих машин.
Перелік посилань
- Чугреев Л. И. Динамика конвейеров с цепным тяговым органом / Л. И. Чугреев – М.: Недра, 1976. – 256 с.
- Маренич К. М. Автоматизований електропривод машин і установок шахт и рудників: навч. посібник для вузів [Під загальною редакцією К. М. Маренича] / К. М. Маренич, Ю. В. Товстик, В. В. Турупалов, С. В. Василець, І. Я. Лізан – Донецьк: ДонНТУ, Харків: УІПА, 2011. – 245 с.
- Маренич К. Н. Асинхронный электропривод горных машин с тиристорными коммутаторами / К. Н. Маренич – Донецк : ДонДТУ, 1997. – 64 с.
- Маренич К. Н. Асинхронный электропривод подземного скребкового конвейера с тиристорным пуско-защитным аппаратом [Дис. канд. техн. наук: 05.09.03] / К. Н. Маренич – Донецк., ДПИ, 1991. – 238с.
- Лаусенко А. В. Скребковые конвейеры. Справочник [Под ред. А. В. Леусенко] / А. В. Лаусенко – М.: Недра, 1992. – 221 с.
- Штокман И. Г. Расчёт и конструирование горных транспортных машин и комплексов: учебник [для студ. высших учебных заведений] под ред. И. Г. Штокмана. / И. Г. Штокман, П. М. Кондрахин, В. Н. Маценко и др. – М.: Недра, 1975. – 464 с.