Abstract
Contents
- Introduction
- 1. Theme urgency
- 2. Goal and tasks of the research
- 3. Overview of Research and Development
- Conclusion
- References
Introduction
Rapid development of productive forces, is associated with a high consumption of fuels and hydrocarbons, irregularity and complexity of the extraction of fossil fuels is accompanied by a rise in prices and increased transportation costs and material costs.
In the chemical industry's most urgent task is to convert coal production base of fixed nitrogen, synthetic methanol. This translation promises to reduce krupnotonazhnost chemical companies to seasonal fluctuations in the supply of natural gas, free from the use of significant amounts of heat-resistant alloy steels.
transition to solid fuel has a number of negative effects for industrial production. Analysis, preparation of production and overcome the difficulties of the task of science.
Working with solid fuel in hardware and technically more difficult than in liquid and gaseous hydrocarbons. Production and transportation of solid fuel, its drying, grinding, filing into the gasifier, ash removal, cleaning of process gas all require the help of mechanical and technological devices. Moreover, all processing steps require energy expenditure.
Thus, the transition to a new source of raw materials related to: the growth of capital costs, reducing the efficiency of the process, increasing the flow of labor per ton of finished product. But with whatever cost was not associated this transition, it can not be considered as an alternative, it is an inevitable necessity. And the earlier training will be developed for this transition, so it will be less painful. The most important part of solving the problem is the problem of gasification of solid fuel, the product gas.
1. Theme urgency
Due to the current difficulties in securing oil and gas in Ukraine shows interest in finding alternative directions permits the energy problem. Attention is directed primarily to the use of brown coal, shale, low-grade coals and carbonaceous wastes.
Proven and probable reserves of oil and natural gas compared to coal reserves in Ukraine are very limited. At current levels of production, natural gas production in Ukraine will be enough for 50 ... 60 ,oil 40...50, and coal for more than 500 years.
Addressing energy security of the country must be viewed in two ways:
• more efficient use of existing energy resources;
• Development and implementation of new advanced methods of energy production based on existing resource base in the camp.
Currently, one of the areas of Energy is the processing of brown coal, in particular, its semi-coking and gasification to produce power gas. One of the most promising schemes for high-calorific gas from coal gasification technology is based on its carbonization.
2. Goal and tasks of the research
Research purpose: analysis and development of methods for underground coal gasification using coal mine methane.
objective of this study is to provide a gas generator by means of its high caloric preliminary carbonization in the reservoir than conventional air-blown gasification.
3. Overview of Research and Development
Under the process of gasification of solid fuels commonly understood as a complex process of thermochemical conversion of solid fuel to gas. In this case, combustion and gasification should be viewed as a single process, which is primarily supported by common occurrence in these processes of chemical transformations.
in coal gasification process, whether it is a layer or a channel using two stages. The first-stage thermal decomposition at which of coal releases moisture and steam-volatile substances, carbon residue, and remains, a combustible part of which is carbon. The second-stage gasification at which the first, carbon-carbon residue with free or combined oxygen is converted into combustible gas, and secondly, these gases react with oxygen and steam. That is the main stage of gas generation, which determines the composition of the gas underground gasification.
When coal gasification product gas calorific value mainly depends on the composition fed to the center air mixture. When feeding air calorific gas is 3,35-4,19 MJ/m3, the gas may be used for energy (electricity, steam, hot water). However, this gas is uneconomical to transport over a distance of 25-30 km, so its scope is narrowed sharply.
experimentally confirmed that the gasification of coal seams with high oxygen promotes oxidation temperature zone and a more complete response coal carbon. The heat of combustion of the gas reaches the maximum values for brown coal MJ/m3 6.5-6.7, 8.0-8.2 MJ/m3 coal in an oxygen concentration of 65-70% in the blast at normal pressure and 10,2-10 4 MJ/m3 at elevated pressure.
There are various methods of coal gasification. Methods of coal gasification in which the gas is converted to primarily only part volatile coal, called methods incomplete or partial gasification of coal.
Low-temperature expansion, semi-coking coal is carried out at 550-600 °, with the coke residue called char. The calorific value of the gas reaches the semi-coking 25000-34000 kJ/m3. Exit gas in this case, a ton of coal is 60 m 3/t.
medium-temperature decomposition of coal-medium-temperature carbonization is carried out at 700-800 °, coke residue of this process is called medium temperature coke. The calorific value of the gas medium temperature coking is 21000-25000 kJ/m3. Gas output of 200 m3/t.
High-temperature decomposition -coking coal produced at 900-1100 ° and the solid residue of this process is called coke. Coke oven gas has a calorific value of 17000-20000 kJ/m3. The gas output 320 m3/t.
Coal gasification in the reservoir portion of the coal seam is regarded as natural coal bed consisting of pieces of it, separated by pores and cracks. For the gasification of coal seam in this area by the reservoir and flushed lit by natural pores. Pores and crack the vast number of coal seams have a high resistance to passage of air blast, and this requires the use of high-pressure air blast, which is expensive. Given the difficulties in the use of natural pores and cracks, use the methods of coal gasification with artificial fragmentation, creating a semblance of the coal bed. To do this, loosen the plastic mechanical impact or explosion. High cost of funds for crushing coal seam does not provide the technical and economic efficiency of the method. The problem of the permeability of the coal seam gasification method solves the coal seam wells, gas generators. In this case, permeate reservoir closely-spaced wells which serve as a kind of artificial cracks. However, the degasification of coal in this method occur around each well without adjustment. In parallel operation of several wells leads to uneven coal degasification around each of them to the breakdown of the gasification process. Also, a method of gasification of coal seam jet blast, which involves the supply jet fired up the coal surface. This method has not found practical application because of the difficulty of constructive design. Known for underground coal gasification in an array and metanodrenazhe the channels through wells.
Disadvantage is the low calorific value gas generator. The analysis shows that the most effective method gazikatsii-coking.
Proposed use of captured gas to burn in a heap sboyki, due to this heat producer gas of higher calorific value (coefficient increases gasification). This hole is used for degassing the new blast and output gas generator, the output of a high-calorie gas, the gasification efficiency is increased from one ton of coal, has a positive effect on the environment, since the ash and rock is under when mining coal and prevents ingress of methane into the atmosphere which leads to a change in the earth's climate to a greater degree than carbon dioxide. Using a gas-generator from any heat to electricity and chemical processing. Consider the proposed method of coal gasification in a channel with adjustable pass on it and blowing gas and individually controlled gasification process occurring in each channel in parallel to their work. This method of coal gasification is based on the fact that if the surface of the burning coal seam wash streams and blast gas, thus it is possible to obtain a combustible gas and a certain amount of coal vygazovyvat. To maintain the gasification of this method is necessary in the coal seam to create a channel of this section, or more precisely with the hydraulic resistance to blast through it and passed gas in the correct amount, under economically acceptable pressure. The most common site for the degasification of coal seam line method it is outlined the relevant channels gasification, in which one end of the draft is supplied through another vent the gas. Figure 1 is a schematic diagram of the coal seam as heat which is methane obtained in the previous degassing reservoir. This method of coal initially allocated volatile under the action of methane and air blast supplied to its combustion, followed by the gasification of coal coke conventional blown. The heat of combustion gas produced by air-blown 3300kDzh/m3.Letuchaya part of the Donetsk coal basin is 44%. Thus the heat of combustion of the gas produced by the process described above and illustrated in figure 1. be 9400-17000kDzh/m3.
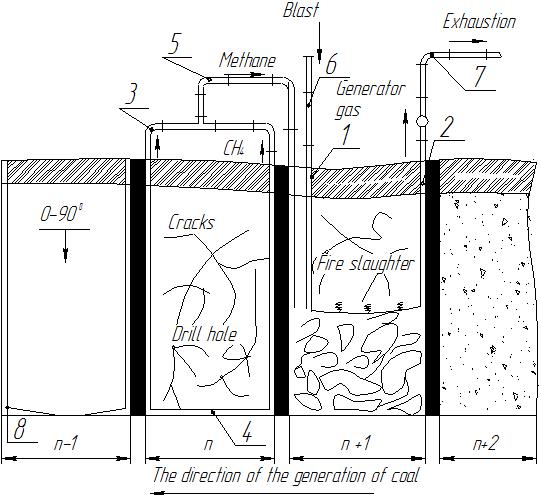
1- the blow-hole gasification panel; 2-hole vapor gasification panel; 3 -metanootvodyaschaya well degassed panels being prepared; 4 sboyka pervonochalny rozzhigovy channel; 5 - assembly line; 6-blow line; 7- the gas exhaust line; n-degassed panel; n +1- gasified panel. n-1-documentation prepared plate (wells drilled is sboyka-face education); n +2- panel degassed and uglegazifitsirovana; n-2-well drilling.
Figure 1 - Schematic of coal mining areasTraditional methods of coal production and consumption are responsible for the conversion of coal-producing regions in the disaster zone. This is typical for coal-fired plants. Per kW of installed capacity of coal power plants is released into the atmosphere each year 500 kg of ash and slag, 75 kg of sulfur oxides and 10 kg of nitrogen oxides.
Therefore, the use of coal as a primary energy source pollution is justified only in two cases:
1. Combustion of coal must be accompanied by trapping of solid and gaseous pollutants.
2. Conversion of coal in its place of occurrence in a more environmentally friendly energy carrier gas.
One way to meet these conditions is - underground coal gasification.
Gas CCGT environmentally compared with combustion of solid and liquid fuels is the most pure, since it burns almost not produced harmful impurities (sulfur dioxide, particulates), and the content of carbon oxides and nitrogen slightly.
produced in the gasifier side an underground gasification products are carried along with the gas to the surface and falls into a condensate, which, as previously stated, can be easily purified according to known methods.
Testing of coal seams is a way in which there is no failure earth's surface and is completely retained soil.
Lessons learned work station "Podzemgaz" it was shown that the earth's surface subsidence over vygazovannym space of 1-3 m at vygazovannoy seam thickness of 8-10 m Landscape and topsoil almost broken, the earth over exhaust gas generators used in the utility agriculture, plant to plant crops and perennial grasses. Special costs for reclamation of the land was not required. Air pollution and water-bearing horizons were observed.
However, the CCP possible contamination of groundwater due to the presence of their direct contact with the hearth gasification, as well as any leaks from underground gas generator.
The degree and extent of groundwater contamination depends on natural conditions. On the whole study shows that the negative impact of the process is local and is not threatening, because the combustion chamber is formed around a depressed area groundwater. Due to contamination, the products contained in the gas leaks, condensed by filtration and returned to the gasifier are extracted to the surface in the form of pumped water and evaporated. The phenol content in groundwater does not exceed 0.01-0.5 mg /L, which makes them suitable for water supply without prior stonecrops.
Exclude or minimize the harmful effects of the gas leak on the environment can be at the following events:
- Leaving the protective pillars that prevent the penetration of gas to the surface and into the depths;
- Establishment of protective screens (gazodrenazh, barrage);
- The use of vacuum-injection delivery system blowing exhaust gas;
- Conducting pumping water from vygazovannogo space in the gasification process and after its completion;
- smothering gasification of waste areas by the path, siltation and flooding;
- Timely elimination breaks casing. Normal manufacturing process eliminates the ingress of UCG gas emissions into the atmosphere, this is achieved by the use of appropriate equipment, piping, automationtion, of instrumentation.
Accidental spills of gas produced in the flare. Cooling water used in the cycle is performed in a closed circuit heat exchanger of the "water-to-water"
Industrial waste water after cleaning the internal circuit used in a closed loop relatively clean waters.
Environmental benefits of underground gasification of coal over traditional methods of coal deposits is mainly on one side in the environmental performance of underground gasification gas as a fuel, and the other - in the smallest degree of the impact of this technology on the natural landscape, which does not go to comparison, such as the devastating environmental impact of such a widely used method of coal mining, as open pit coal seams.
We note in particular that the method allows the CCP does not violate the vegetation layer, and after the gasification of coal seam ground portion can be transferred without any reclamation for agricultural use.
At the stage of production (replacing the traditional methods of using CCP) is excluded waste rock (5-6 t/tce.) prevented the alienation of land (15-20 m /m. tcf ) eliminates the emission into the atmosphere of carbon dust (0.3-15 kg/tce.) and reduced discharge of suspended solids in the wastewater (from 0.452 to 0.044 kg/tce.).
At the stage of transport completely prevented the characteristic of solid fuel dust entrainment (3-6 kg/tce.).
At the stage of burning ash emissions excluded, practically eliminates the emission of sulfur dioxide and reduced to 1.5-2 times the output of nitrogen oxides (from 2-5 to 1-1.5 kg/tce.).
These figures fully reflect the benefits of CCP over other methods of extraction of coal, because this is important in difficult environmental conditions in general.
Conclusion
Coal gasification is a promising process for the production of pure synthesis gas, and on this basis for the combined production of electricity, heat and process steam, hydrogen, methanol, and other valuable products.
Carrying coal gasification under pressure and its integration into the energy cycle combined cycle plant can achieve high economic performance in power generation with minimal impact on the environment.
Energy gas turbine with air-blown gasification for easier and more economical, with gasification on the oxygen blast - create the possibility of chemical reactions for the production of valuable products and output of CO2 before combustion cycle.
Powerful (250-300 MW) power PSU with coal gasification operated abroad for more than 10 years. Actively developed CCGT capacity to 600 MW. The widely held works to improve the processes and equipment gasification and gas cleaning plants. This activity is funded by the government and coordinated by them under government programs.
Development of similar programs and is suitable for Russia, in particular, by the need to limit emissions of CO2 in the atmosphere and the possible consequence of global warming.
Surviving in the country knowledge and experience carried out in recent years, research could generate a small 3-15 MW demonstration plant with integrated coal gasification and power generation and heat. This setup will provide, inter alia, data to estimate the cost, efficiency and real-world problems, the industrial exploitation of this type of PSU.
Financial support and scientific and technical partnership between the government and industry is necessary for drawing up and implementation of such a program.
References
1.Скафа П.В. Подземная газификация углей//Государственное научно-техническое издательство литературы по горному делу.-М.-1960.-316с.
2. Разработка временных рекомендаций на подбор угольных месторождений для проектирования станций подземной газификации углей // ИГД им. А.А. Скочинского.-М.-1998.-63 с.
3. Каталог участков (месторождений), пригодных для подземной газификации углей // Донгипрошахт. – Донецк, 1993. – 81 с.
4. Кулешов В.М., Корчемагин А.В., Панасенко В.М. Повышение эффективности подземной газификации угля // Уголь Украины. – 1990. – № 2. – С. 18-20.
5. Крейнин Е.В. Экологическое и технико-экономическое обоснование строительства промышленных предприятий подземной газификации углей // Уголь. – 1997. – № 2 – С. 46-48.
6. Подземная газификация углей в СССР / Антонова Р.И., Бежанишвили А.Г., Блиндерман М.С. и др. – М, ЦНИЭИуголь. – 1990. – 98 с.
7. Лавров Н.В. Физико-химические основы горения и газификации топлива//Металлургиздат.-1957.
8. Ревва М.К. Основные итоги работы станции Подземгаз. Бюллетень «Подземная газификация углей».-1957.-№2
9. Цейтлин Д.Г. Критический обзор методов подземной газификации углей. «Подземная газификация углей».-1954.-№3
10. Шишаков И.В. Основы производства горючих газов//Госэнергоиздат.-1958.