Abstract
Contents
- Introduction
- 1. The relevance of the topic
- 2. The purpose and the objectives of the work
- 3. The significance and the use of production
- 4. The
physicо-chemical production bases - 5. The description of technological scheme and production technology
- Conclusion
- References
Introduction
Enamelling principle is known from very early times. Industrial enamelling, as we understand it now for technical purposes, is still young compared with metallurgy, manufacturing of glass and ceramics.
The technical essence of enamelling — a connection of enamel and metal — is still largely unchangeable, although since ancient times the number of metals and enamels has increased greatly.
Enamel coatings have got several advantages above other
Simultaneously, enamelling of metal products can solve problems of design of products for domestic and industrial use.
1. The relevance of the topic
In this work we have researched the synthesis of optimal composition and the technology of
2. The purpose and the objectives of the work
The main purpose is to study the structure and technology of
The objectives are:
- The study of the optimum composition and the technology of
glass-enamel coating for the protection of copper from high temperature corrosion and gas one. - The synthesis of
lead-free protectiveglass-enamel coatings. - The use of new materials in enameling.
3. The significance and the use of production
Enamelling of copper and
In artistic purposes various decorative household objects such as vases, pictures, cigarette cases, bowls, jewelry, badges are made from copper and
In connection with the introduction of individual heating trends there is a need to use water heaters, in which electric heaters formed on metal enamelled substrates are widely used. Since copper possesses good thermal conductivity, it is expedient to use it as the material for manufacturing heat exchangers. These products must have high strength, heat conductivity, heat resistance, corrosion and thermostable [2]. Copper inductors are used in the hardening of complex products with
4. The physicо-chemical production bases
As it is known [4], monolayered vitreous coating for copper are relatively
The
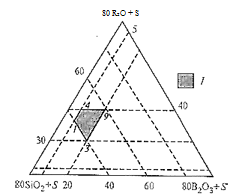
I — optimum region for obtaining enamel glass, S = 7Al2О3 + 5CaO + BaO
Image 4.1 — Region of vitrification in the system R2О — CaO — BaO — B2О3 — Al2О3 — SiО2 (mass %)
The additives Co2О3, Fe3О4 and MnО2 that were being added during grinding in the process of preparation of slurry were used to increase the heat resistance and the adhesion strength. It was discovered that the enamels with the additives Co2О3, Fe3О4 and MnО2 in amounts 0.51–1.98; 0–4.5; 3.3–9.3 mass %, respectively, formulations of which are in the region indicated on image 4.2 possess the optimal properties [4]. During introducing these additives into the enamel slurry maximum values of the adhesion strength and the heat resistance are 98 % and 72 cycles (20–400 °C) respectively [4].
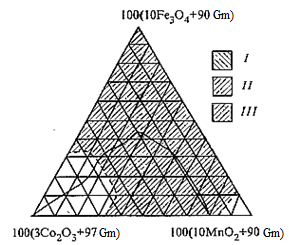
I — heat resistance, amount of cycles (41–72);
II — adhesion strength (96.5–98.0 %);
III — region of optimal values of properties;
Gm — glass matrix
Image 4.2 — Diagram of optimal values of properties
In developing of the technology of protecting copper inductors with using
When enamel is used without additives Co2О3, Fe3О4, MnО2 (image 4.3) until the melting of frit particles under the temperature of 580 °C atmospheric oxygen penetrating through the porous layer oxidizes copper in the temperature range of 200–375 °C to СuО [5].
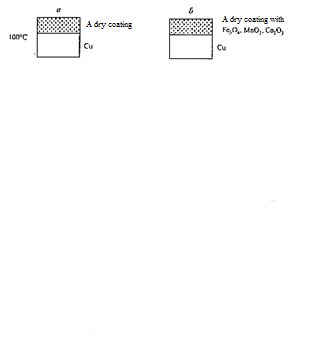
а — no additives Co2О3, Fe3О4, MnО2; b — with additives
Image 4.3 — Scheme of formation of
(animation: 6 shots, 6 cycles of repeat, 133 kilobytes)
At higher temperatures in the contact layer between copper and
As a result of the firing of the enamel coating it was established that the enamel coating is enriched with copper in an oxidized, preferably in the ferrous (monovalent) state [6]. Enamel melts during firing are a kind of protective coatings, although the processes of interaction here are pretty intense (image 4.4).
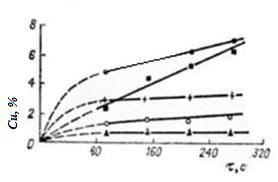
Image 4.4 — The dependence of the oxidation of copper under the cover upon the firing time
Thus, we can consider that under high temperatures
The research of the microstructure of copper coated samples after oxidation under temperatures below the softening point (image 4.5) has shown that the copper oxide layer, which hardly dissolves in the coating and does not destroy its continuity is formed between the coating and the copper strip.
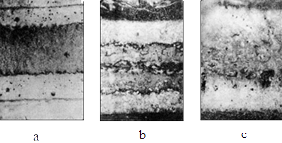
а — original sample; b, c — after soaking for 116 and 150 hours at 700 °C
Image 4.5 — The microstructure of copper coated samples
In case of slow maintaining the copper strip can be completely oxidized, after the experiment the copper oxide layer remains enclosed in a shell of constant unchangeable coating (image 4.5, с). In this case the integrity of the coating is not disturbed because the molar volumes of copper and oxides of copper are close enough. On the image 4.5 it is shown that the oxides of copper form a layer of equal thickness between the copper strip and the coating [6].
In case of introduction of additives Co2О3, Fe3О4, MnО2 during grinding the process of coating forming on copper is a different matter. The presence of activators of clutch in the contact zone enhances the chemical activity of the interacting phases and promotes the following electrochemical reactions [5]:
Fe2О3 + 2Cu = 2FeO + Cu2О,
Fe2О3 + Cu = 2FeO + CuO,
Fe2О3 + Cu2О = 2FeO + 2CuO,
MnО2 + 2Cu = MnO + Cu2О,
MnО2 + Cu = MnO + CuO,
MnО2 + Cu2О = MnO + 2CuO,
Co2О3 + 2Cu = 2CoO + Cu2О,
Co2О3 + Cu = 2CoO + CuO,
Co2О3 + Cu2О = 2CoO + 2CuO.
CoO, FeO, MnO, CuО interacting with a formation of solid solutions (Cu, Fe)О2, (Cu, Mn)О2 and (Cu, Co)О2 appear. They interact with the silicate melt, in particular with the anions [SiО4]4−, and form the corresponding silicates
This is confirmed by electron microscopic studies of the transition layer. Unlike coating without additives, coating with additives Co2О3, Fe3О4, MnО2 has got a distinct transition layer between the coating and copper. In addition, the metal surface is more fluffed in the result of past electrochemical reactions. Therefore, in the presence of additives Co2О3, Fe3О4, MnО2 bonding strength, provided with an intermediate oxide layer Cu2О and СuО associated with
5. The description of technological scheme and production technology
The
Tests were carried out by melting mixture in refractory crucibles for
The most important prerequisite for strong coupling of enamel with copper is irreproachable condition of the metal foundation. Surface preparation of the copper samples was carried out by treatment in the etching solution (the method «brilliant etching») [1, 7]. Applying the enamel coating was made with the wet method, initially a layer of enamel slurry without refractory filler was applied. After fixing of at layer on the surface of copper samples by annealing under the temperature of 800 °С, a second layer with a refractory filler (Al2О3) was applied. This layer was fixed again by calcining under the temperature of 870 °С. To prolong the period of the product employment the number of applied layers of enamel coatings with refractory filler (two and more) can be increased. Firing of the enamel coating was carried out in the laboratory electric muffle furnace (image 5.1).
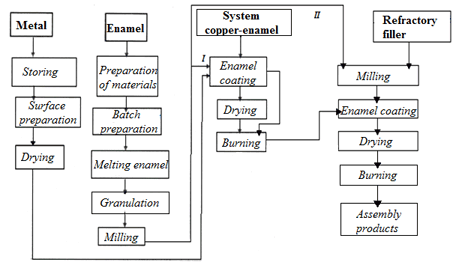
I — getting the first layer of enamel coating;
II — getting the second layer of enamel coating
Image 5.1 — Scheme of production of
During firing of obtained enamels
Conclusion
Analyzing the material contained in the work, we can make the following conclusions:
- The most effective way to protect products from corrosion is to use
glass-enamel coatings with increaced thermal stability. - Copper products with
glass-enamel coatings are used for a long time as the protection of metals from oxidation and destruction in gaseous environments under the temperatures up to 600 °C and above. - Both lead R2О — PbO — B2О3 — SiО2 and
lead-free R2О — CaO — BaO — B2О3 — Al2О3 — SiО2 systems were put into the basis of the development of glass matrix srtucture for the protectiveheat-resistant glass-enamel coating. - For better secure of the
glass-enamel coating on copper products it is recommended to use small amount of oxides Co2О3, Fe3О4, MnО2 0.5–5 % as an additive during grinding of enamel frit. - The most important prerequisite for strong adhesion of enamel with copper is irreproachable condition of the metal foundation. The main stage is surface treatment of copper by the «brilliant etching» method.
- To raise the use temperature of copper products with
glass-enamel coatings refractory material such as quartz sand, alumina, mullite, and others are introduced into mixture during the grinding of enamel frit. - Firing temperature of
glass-enamel coatings for copper products is in the range 720–800 °C for lead enamels, and 800–880 °C forlead-free ones.
References
- Технология эмали и защитных покрытий / Л. Л. Брагина, А. П. Зубехин, И. Я. Белый и др. — Харьков: НТУ
ХПИ
, 2003. — 483 с. - Аппен, А. А. Температуроустойчивые неорганические покрытия / А. А. Аппен. — Л.: Химия. Ленингр. отд-ние, 1967. — 238 с.
- Эмалированние металлических изделий / Под ред. В. В. Варгина. — Л.: Машиностроение, 1972. — 494 с.
- Яценко, Е. А. Новое стеклоэмалевое бессвинцовое покрытие для меди, модифицированное добавками Fe3О4, MnО2 и Co2О3 / Е. А. Яценко, А. А. Непомящев, А. П. Зубехин // Журнал прикладной химии. — 2000. — Т. 73. Вып. 3. — С. 443–445.
- Яценко, Е. А. Защита меди от высокотемпературной коррозии / Е. А. Яценко, А. П. Зубехин, А. А. Непомящев // Стекло и керамика. — 1999. — № 9. — С. 28–30.
- Журавлев, Г. И. Химия и технология термостойких неорганических покрытий / Г. И. Журавлев. — Л.: Химия. Ленингр. отд-ние, 1975. — 199 с.
- Пат. 2149842 Рос. Федерация: МКИ C 03 C 8/02. Защитное покрытие для меди / А. П. Зубехин, Е. А. Яценко, А. А. Непомнящев; Заявл. 16.11.1998; Опубл. 27.05.2000. Бюл. № 15. — 5 с.