Abstract
This master's work is not completed yet. Final completion: January 2015. Full text of the work and materials on the topic can be obtained from the author or his adviser after that date.
Content
- Relevance of the topic
- 1. Research goals and objectives
- 2. Analysis of the modern state of the research question
- 3. Methods and principles of application of function-oriented coating roller mills
- Conclusions
- References
Relevance of the topic
Currently in the world focuses on the challenges of increase the wear resistance and corrosion protection of machinery parts. Topical issues of durability sufficiently illustrated by the fact that in some industries the production of spare parts equal to the production of parts for the assembly of new machines. [1]. Wear brings losses in all sectors of industry and all over the world. The amount of damages - billions of dollars. Wear eats not only the money that goes to purchase replacement parts. Because when stops equipment associated with its repair, output at the company reduced losses increase significantly. Downtime - well as loss of profits. Besides all this, wear a global problem concerns — depletion of natural resources of the planet.
In conjunction rolls-rolled strip only the roll surface wear is studied.
Wear of rolls is primarily connected with sliding metal rolled strip with respect to the rolls in the areas of advancing and defending. This effect leads to the fact that the work roll surface undergoes alternating stresses, tangential to the surface of the roll body. Repetition of these force effects and large normal pressures cause a sharp mechanical abrasion of the roll, gap of the metal particles and chipping on their surface. [2].
One way to improve the functional characteristics of roller mills is a method of coating. Currently there are many coating technologies. The choice of method depends primarily on the requirements of the product and perform their functions.
Typically the same technological impact is used for all products, it is often economically unprofitable and it leads to uneven loss of the properties of different areas of surfaces of the rollers. Such conditions promote a more thorough development of specific technologies. In this case, perhaps we can use the technology which based on function-oriented approach [3].
1. Research goals and objectives
The purpose of this work is to improve the wear resistance of the rollers rolling mills by using special coatings on the basis of application of function-oriented technologies.
Accordingly, the following problems are generated:
- To perform analysis of the application features of function-oriented coating roller mills.
- To develop methodology and application of the principles of function-oriented coating roller mills.
- To perform structural synthesis of functional studies and analysis of special coating roller mills.
- To explore the design features and the synthesis of equipment for application of function-oriented coating roller mills.
- To carry out pilot studies special coating roller mills.
- To develop recommendations for the application of technological protection of function-oriented coating roller mills.
2. Analysis of the modern state of the research question
Depending on the requirements in terms of performance parts, there are three types of coatings [4]:
- protective coatings whose purpose is to protect against corrosion of parts in various aggressive environments, including high temperatures;
- protective and decorative coatings, serving for decorative details with protecting them from corrosion;
- special coatings, which are applied to impart special properties to the surface (wear resistance, hardness, electrical and magnetic properties, etc.) and restoration worn components.
Quite a lot of companies working in this direction. In particular, the JSC «Ilyich Iron and Steel works» uses the installation of mechanized arc welding.
Annual economic effect of the development was more than 250 thousand UAH. The cost of restoring worn the roll are on average 15% of the cost of a new one. Wear resistance weld rolls is more than 2.5 times higher than the rate of new rolls [5].Working mill rolls should provide a secure capture, be sufficiently strong and wearproof, have a high resistance to impact loads, will inevitably arise in the initial moment of capture.
Quality of work rolls and their resistance significantly extent determine the technical and economic performance of the mills.
Wear mills depends on: the chemical composition and structure of the roll, the rolling temperature and the cooling conditions of the rolls, adopted calibration system and regime compresses, state roller fittings and mill setup.
Usually temperature of the roll surface outside the deformation zone is above the ambient temperature not more than 50 ° C.. In the deformation temperature on the surface of the roll is close to the temperature of the rolled metal. As a result of temperature fluctuations on the roll surface cracking mesh appears where intensive oxidation of the metal occurs, promotes the further development of the formed cracks.
The service life of caliber significantly increase, when rolls is cooled with water . Water abundantly supplied on the outlet side of the strip. Wear gauges is also influenced by the chemical composition of rolled steel. When rolled steels with high carbon wear calibers is larger than usual steels during rolling. Especially wear out quickly during rolling calibers many alloy steels.
Between the amount of roll wear and hardness, there is a direct correlation [7].
Fig. 3 shows diagrams of wear caliber medium-section mill 350 JSC "Severstal", which was built according to wear every 5 mm along the perimeter caliber with fixing the amount of rolled metal in this caliber.
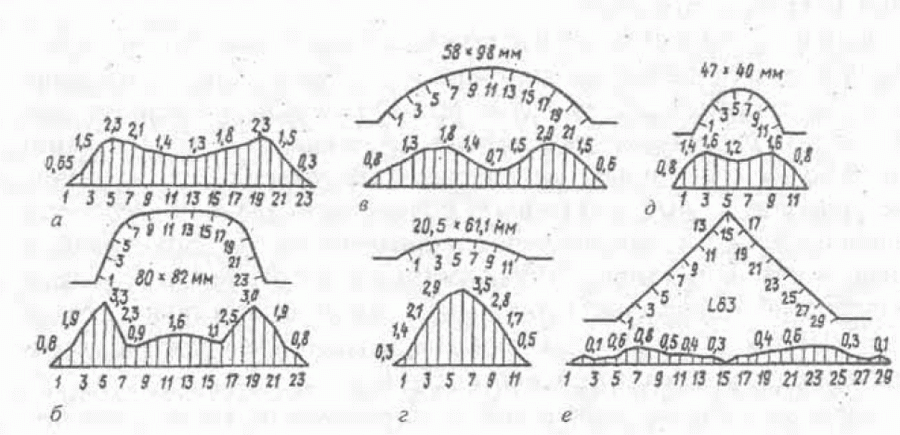
Fig. 3 Diagrams 350 mill roll wear [2]
The figure shows that when rolling on a smooth barrel there are two areas of maximum wear, the location of which corresponds to the corners defined by the strip, which has a lower temperature, and hence increased resistance to deformation (Fig. 3a)
Maximum wear of box calibers (Fig. 3b) is observed on their walls. At the bottom of the wear is almost twice smaller. The surface condition of worn caliber indicates a metal sliding on the wall surface of caliber caused by flow of metal under the force of limiting broadening, and the difference of rotational speeds at the wall of the caliber.
Oval calibers (Fig. 3c), which is set in the blank square are two symmetrically located areas of maximum wear, given by the respective corners of a square.
Maximum wear oval caliber preceded oval rib (Fig. 3d), occurs at an average of the caliber, caliber wear to edges decreases smoothly.
Wear caliber rib oval (Fig. 3e) occurs more uniformly than wear oval caliber. Maximum wear portions are arranged symmetrically at a certain distance from each other.
Minimal wear of the angular roll caliber VI, VIII, IX and X stands observed in their top corner. Wear gradually increases to the rim.
Finishing calibers rolls XII and XIV stands have the same wear pattern as the angular calibers (Fig. 3, e).This is explained by the fact that the rib stand XI caliber rolls observed increased wear wall caliber [2].
3. Methods and principles of application of function-oriented coating roller mills
Given the characteristics of the various wear rollers rolling mills, we can establish that a promising approach to the development of coating technology is functionally-oriented technologies.
Function-oriented manufacturing technology engineering products — a special technology, which is based on the exact topologically oriented realization of a variety of algorithms the necessary technological exposure of tools and means processing necessary micro, macro zones and areas articles which functionally correspond to the conditions of operation in each individual zone thereof. Using functional-oriented technologies engineering products maximizes their general operating parameters through local enhanced technological capabilities and properties of the individual elements, surfaces, and / or areas of product depending on the local functional characteristics of their operation. In this case engineering products maximally adapt in their properties to the features of their operation and show their full potential opportunities in the machine. It should be noted that this new class of techniques complicates the manufacturing process of products, but generally provides a qualitatively a new set of properties and measure of the usefulness engineering products in using. This enables a substantial increase technical and economic indicators operation and using of machines and technical systems [3].
The main features of functionally-oriented technologies are that the technological impact of tools for processing products and the process ensure the specified and the desired properties of products is performed at the following levels: at the level of the articles; at the site level; level components; at the zone level; at the level of macro zones; at the level of micro-watersheds; at the level of nanozon.
In this case specified, the required limits and properties of the products provided by the orientation of technological influences flows of matter, power and information based on the principles of eight special principles [3,8].
Based on developed principles the synthesis of functionally oriented technologies and manufacturing of products is performed.
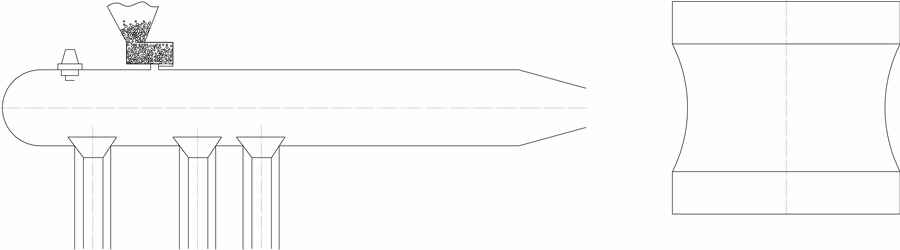
Fig. 5 Functional-oriented detonation coating
So, exploring the range of functions, which is performed by the working surface of the roller mill, we can break it up into several zones. Breaking occurs depending on the effects of non-uniform along the length of the roller surface. So requires an individual approach to each roller to which a functionally-oriented technology. In this case we study the uneven wear and temperature effect on the surface of the roller. For performance we can use the principle of concentration and intensification of the process and reducing downtimes.
Conclusions
Functional-oriented technologies are promising for many applications, including roller mills. The main feature of this approach - better adaptation of products to the operating conditions. This, in turn, significantly improves the durability of the rollers because and the process is reduced and becomes uniform wear along the length of the roller barrels, increases time between reloading, and as a result, productivity is increased of the rolling mill.
Positive trend in improving the wear resistance can be noted by studying the experience of companies, which is developing technologies hardfacing roller mills.
In adverse events we can note the increasing complexity of technology development for the treatment of products in general. Also the technology and equipment are complicated , it leads to increasing cost the product, but the economic effect is achieved by increasing the lifetime of the roller mill and improving the performance of the rolling equipment.
References
- Бартенев С.С., Федько Ю.П., Григоров А.И. Детонационные покрытия в машиностроении.—Л.: Машиностроение, Ленингр. отд-ние, 1982.—215с.
- Яковлев Р.А. Расчет на износ узлов трения прокатных станов. Учебное пособие по курсу «Основы динамики и надежности прокатных станов». — Под ред. А.Г. Колесникова. — М.: Изд-во МГТУ им. Н.Э. Баумана, 2004. — 52с.
- Михайлов А.Н. Основы синтеза функционально-ориентированных технологий.—Донецк: ДонНТУ, 2009. — 346 с.
- Зборщик А.М. Конспект лекций по дисциплине «Новые материалы в металлургии». — Донецк: ГВУЗ «ДонНТУ», 2008.–253с.
- Портал Приазовского государственного технического университета [электронный ресурс]. — Режим доступа: http://www.pstu.edu...
- Сайт предприятия РУП «Технопарк БНТУ «Метолит» [электронный ресурс]. — Режим доступа: http://www.otnp.metolit.by...
- Чекмарев А.П., Гречко В.П., Гетманец В.В., Ховрин Б.В. Прокатка на мелкосортных станах. — М.: Изд-во «Металлургия», 1966. -363с.
- Михайлов А.Н. Общие особенности функционально-ориентированных технологий и принципы ориентации их технологических воздействий и свойств изделий. // Машиностроение и техносфера XXI века. Сборник трудов XIV международной научно-технической конференции в г. Севастополе 17-22 сентября 2007 г. В 5-ти томах.–Донецк: ДонНТУ, 2007. Т. 3. С. 38-52.