Abstract
Content
- Introduction
- 1. Actuality of theme and the problem statement
- 2. Review of research and development
- 3. Methods of solving the problem and the current results
- Conclusion
- References
Introduction
Today automation of industrial processes and robotics operations reduce a person’s job, in essence, to the setting and monitoring of production automation. This reduces the dependence of production on the human factor, which ensures a more efficient and effective work throughout the production process. Automation of technological processes gives the opportunity to all mankind to the next level of development and achievements in media and directions before seemingly inaccessible. All of the above applies to all industries, particularly chemical, which is widely used heat exchange processes.
Processes of heat transfer through the heat exchangers the coolant from one to another, are very widely used in industry and the public sector, the household sector. Often we just use the result of heat, without attaching any importance to it, without seeing the process.
Heat exchangers are high intensity mixing devices, as they heat transfer occurs through direct contact heat transfer, i. e. in mixing heat exchangers, thermal resistance of the wall. These heat exchangers are used in cases where it is permitted mixing coolants or when mixing is determined by technological conditions.
The most commonly used mixing exchangers to condense water vapor, the heating and cooling water and gas (air).
1. Actuality of theme and the problem statement
Heat exchangers are an integral part of most manufacturing processes, so the task automation mixing heat exchangers is very important due to the significant energy consumption of heat exchangers and their prevalence in industrial practice.
Regulation of the mixing heat exchangers is to maintain temperature setpoint by changing the output flow rate of a heat carrier on the condition that is the main source of disturbances and the temperature of the second fuel flow and the temperature of the first flow and the specific heat of substances constant. To create the desired temperature in chemical apparatus used in the transfer of energy by mixing two or more substances with different enthalpy. As a basic object management for the research system of automatic control of the temperature at the outlet of the heat exchanger is technological process (TP) cooling of hydrogen sulfide gas from 750 °C to 450 °C, by mixing them with air [1].
Analysis of the cooling process of hydrogen sulfide gas as a control object, showed that hydrogen sulfide gas flow G2 and gas temperature are the main source of disturbances and air supply G1 – the control action, the temperature is assumed constant [2].
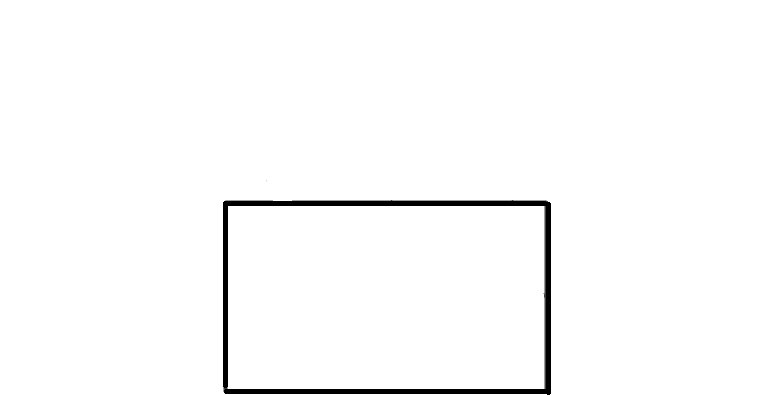
Figurre 1 – The scheme of the analysis of the cooling process, hydrogen sulfide gas in the heat exchanger
(animation: 8 frames, interval 500 ms, 26 kilobytes)
The purpose of is to enhance the quality indicators of temperature stabilization of the total flow at the outlet of the mixing heat exchanger. Specifically to maintain a given accuracy mode, knot security automation, reducing energy consumption by improving the automation system of the object.
2. Review of research and development
Presently known such heat exchangers mixing automation solutions.
Application of single-closed-loop control system.
In a mixing tank, the coolant is supplied through the pipe at a flow rate G1, the temperature of which is maintained by the regulator. Through a second tube is fed to the second coolant flow rate G2. In these two coolant tank mix and the output is a mixture of the desired temperature Q [9 - 10].
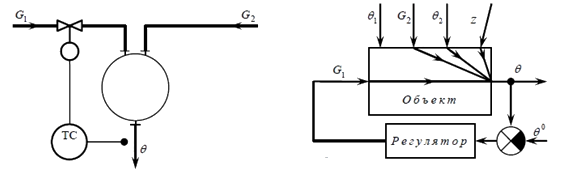
Figure 2 – Functional and structural schemes closed single-automatic temperature control system in the heat exchanger mixing
Stabilization of the output temperature of the mixture is achieved by using Q single-closed-loop control system, wherein the controlling influence of the water flow is G1, in our case the cooling gas. Maintaining setpoint Q ( temperature of total flow at the outlet of the mixing chamber) in the steady state is achieved by using a regulator with integral component of the law and regulation (PI or PID) ensures the maintenance of the set temperature in the steady state, but the quality of the transition process may be unsatisfactory at high inertia of the control channel and strong perturbations.
Another embodiment includes a system for controlling the ratio of water flow G1 and G2. This open-loop control system, the ability to control invariance of the temperature of the mixture to perturbations flow G2, but if there is any disturbance temperature is not equal to the reference.
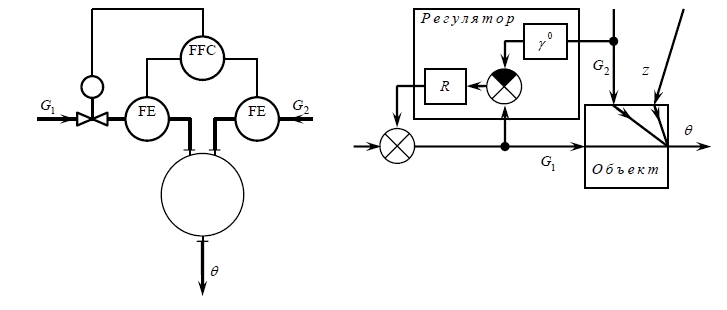
Figure 3 – Functional and structural schemes open loop single-automatic temperature control system in the heat exchanger mixing
Coefficient g° is the ratio of costs heat carriers (g° = G1/G2).
But these methods do not achieve the desired quality of temperature control the total flow.
3. Methods of solving the problem and the current results
Experience and practice have shown that for these classes of objects worked well combined automatic control system in order to ensure payment of basic disturbances and input feedback controlled coordinate.
Fig. 4 shows a functional and structural schemes control system costs and coefficient corrected temperature output stream. It is a two-stage automatic control system. Main (external) controller is a temperature controller 1, and auxiliary (internal) – 2 ratio control flows, which compensates for the perturbation flow (in this case, the gas flow). If there are other perturbations, such as change of heat loss into the environment, this structure will maintain the temperature of the effluent within the specified limits.
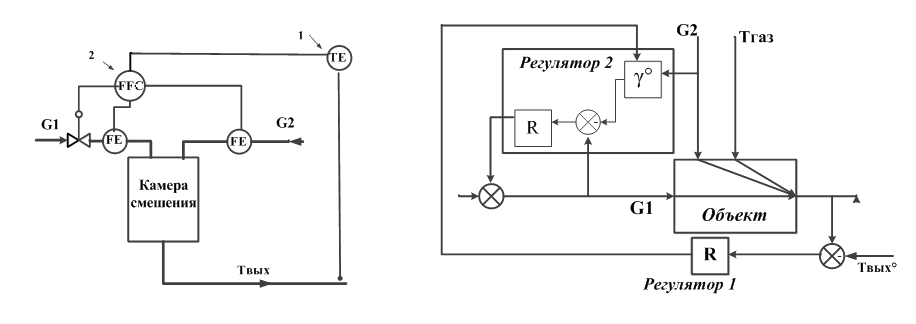
Figure 4 – Functional and structural schemes ACS of the outlet temperature with the correction factor for the temperature of the total flow
The main objective of this work is to study the dynamics represented by ACS analysis of quality indicators when changing disturbances.
Analysis of the cooling process of hydrogen sulfide gas as a control object, showed that hydrogen sulfide gas flow and gas temperature are the main source of disturbances and air supply – the control action, the temperature is assumed constant [2]. Authors in [2] analyzed the mathematical model of the object. The analysis showed that under normal perturbations observed in practice, as a result of linearization error can be significant. By increasing the gas flow by 30% compared with a predetermined gain ratio control action can be changed by 5–20%, while the perturbing 25–40% of the calculated depending on the flow ratio G1 and G2. It has also been shown that stabilization of flow ratio G1/G2 = g° allows to reduce the influence of the nonlinearity in the mathematical model, since no other disturbance except G2 constancy is ensured outlet temperature. Availability of other sources of disturbance than the gas flow rate will require the introduction of correction g° [2].
Consider the work of ACS temperature output stream. As actuator choose DC motor (DCM). This mechanism allows the flap to open only within limits.
Let the ratio of gas and air flow such that gases exiting the heat exchanger has a temperature of 450 C°. Then the output of the rectifier – zero volts DCM does not rotate and the flap is in a fixed position. With increasing perturbation (increase in fuel hydrogen sulfide gas), as a result of the gas output temperature begins to increase. This leads to the fact that the mismatch error will start to increase, which in turn causes an increase in controller output signal ratio as well as the output voltage of the controlled rectifier. The motor starts turning in the direction of opening the flap that will produce an increase in the air into the mixing chamber. This will result in some reduction in temperature of the output stream. If the supply of hydrogen sulfide gas will continue to increase linearly, as a result of the transition process control error is stabilized, the damper will open more and more, at a constant speed. To achieve the air supply a constant value, the engine will choke to a situation in which the error becomes zero, the engine will stop and the temperature at the outlet of the heat exchanger will be equal to 450 C°.
Sudden changes in feed hydrogen sulfide gas into the mixing chamber appears inertial vibrational properties of ACS and for a while the transition process can make the temperature oscillation. In order to avoid such a regime, when stabilization error may exceed the allowable values, technology-smoking increase the feed rate of hydrogen sulfide gas in the furnace-boiler more than 1500 m3/hr [1].
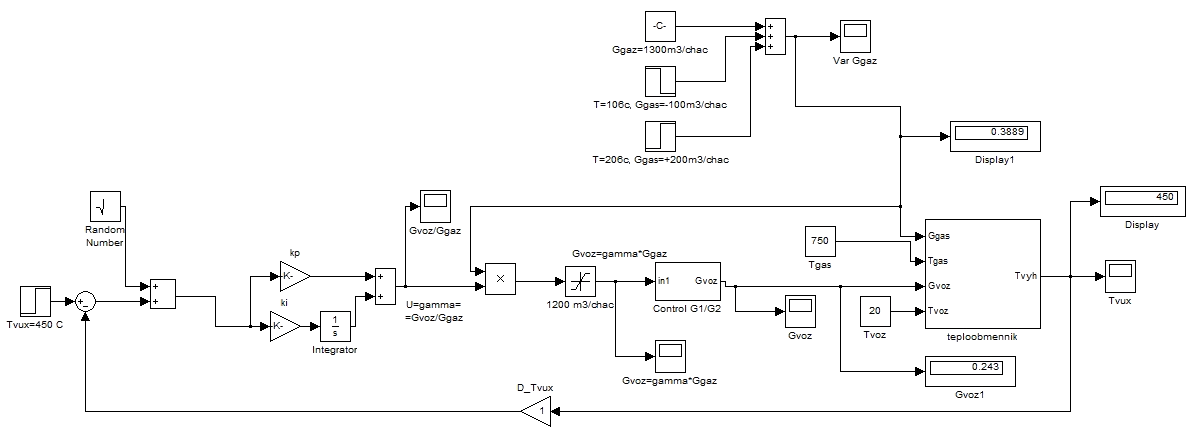
Figure 5 – Modeling scheme ACS temperature hydrogen sulfide gas at the outlet of the heat exchanger
The main problem of the synthesis of ATS is to select control law and determining the tuning parameters of the controller. From the practice of regulators flow ratio [5] accept PI-control law:
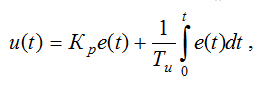
Setting values which are close to optimal, derived from a study of the dynamics of a closed system. As a method of finding the parameters of the controller tuning method is selected auto-tuning PID-control unit simulation package Matlab, because of automatic optimization techniques are a powerful tool of modern industrial controllers. Automatic tuning method is based on three stages: identification of the object model, the definition of the controller parameters and settings. Selecting the above method due to the fact that the controller parameters are defined by existing and widespread method of Ziegler and Nichols then adjusted manually or automatically in the process of analyzing the dynamics of ACS [3].
Figure 6 shows plots of the transient response of the temperature at the outlet of the heat exchanger when the controller parameters calculated by the above named methods and optimized through automatic configuration. The variation of hydrogen sulfide gas is as follows: 150 seconds – is a reduction of the feed rate of 100 m3/hr and 300 seconds – increase feed rate of 200 m3/hr from the nominal value. Nominal air flow is 1200 m3/hr.
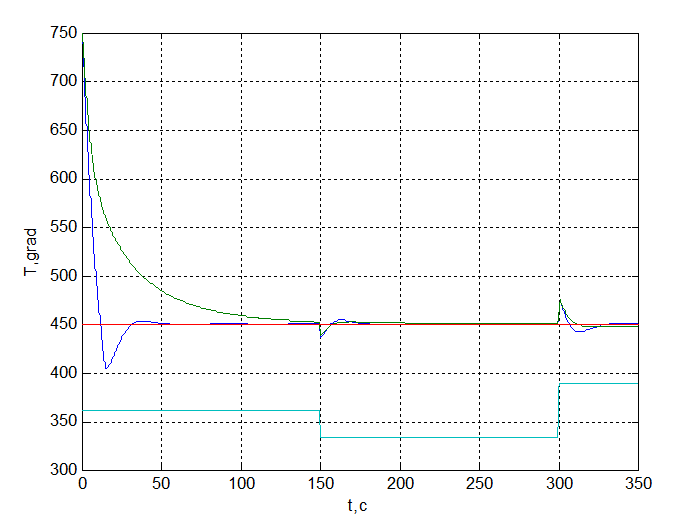
Figure 6 – Transient response output stream temperature when the gas supply
Figure 6 shows that the transient response of temperature controller, configured manually is aperiodic, control time is tp = 150 sec. Transient temperature with optimal parameters is faster: control time is tp = 50 sec, overshoot h = 10%. Time mining disturbing effect on the supply of gas is in both cases approximately 30 seconds. These indicators are satisfactory.
In the studied ACS analysis of the increased susceptibility to the presence of noise in the input to the temperature controller error signal. For this purpose, the main output of the adder feedback signal is a white Gaussian noise generator. Asked broadband Gaussian noise with standard deviation equal to
10 C°. As can be seen from Figure 6. ACS easily copes with its task.
Thus, the simulation results showed the operation cascade of ACS and the possibility of applying the developed systems, which are key indicators of quality are:
- No static error.
- Regulation time – about 100 seconds.
- Aperiodic transient overshoot with valid up to 10%.
- Satisfactory setting time of processing signals and disturbances about 30 sec.
- Compensation as controlled and uncontrolled disturbances selected by the principle of management by exception with a subordinate regulation.
In writing essay of this master’s work is not yet complete. Final completion: December 2013. Full text of the work and materials on the topic can be obtained from the author or his manager after that date.
Conclusions
- Considered technological process cooling hydrogen sulfide gas as a control object. The main source of the perturbation is the gas flow and temperature, and the temperature and specific heat of substances constant. As a basic research for the object management system of automatic control of the temperature at the outlet of heat exchanger cooling the selected technological process gases to hydrogen sulfide to 750 °C to 450 °C.
- It is shown that the stabilization of relations expenses G1/G2 = g° to reduce the influence of nonlinearity in the mathematical model. Analysis of structural schemes of automatic control systems objects of this class has shown that well-proven combination of automatic control system in order to ensure payment of basic disturbances and input feedback controlled coordinate.
- The simulation results cascade ACS different kinds of options PI controllers showed good performance quality system.
- In the future, research will be conducted taking into account the dynamics of ACS heat loss to the environment and nonlinearity of the initial conditions.
References
- Production instructions of the operator of sulfuric acid production Avdiivka coke. – Avdeevka 2013. – 57 p.
- Zhukova N., Kravchenko A. The automatic temperature control of the output stream from the heat exchanger mixing. Materials of ÕVI International youth scientific conference «Severgeoteh-2014»: materials of conference (26-28 March 2014): 1 part. – Uhta, UGTU, 2014.
- Denisenko V. PID controllers: implementation issues (part two). S_Pb., 2004. – 723 p.
- Kuzmenko N. V. Automation of technological processes and productions: Textbook. The allowance. – Angarsk 2005, AGT. – 78 p.
- Dorf R., Bishop R. Modern control systems. Translation from English B. I. Kopylov. – M:Laboratory of basic knowledge, S_Pb, 2002. – 832 p.
- Kim D. P. Theory of automatic control. Vol.2. Multi-dimensional, nonlinear, optimal and adaptive systems: Textbook. – M: FIZMATLIT, 2004. – 464 p.
- Klimachev N. C. Theory of automatic control systems and management: Training–methodical complex. – Chelyabinsk, 2005. – 652 p.
- Chernuh I. B. «Simulation of electro-technical devices in Matlab, SimPowerSystems and Simulink». – 2008.
- Lapchenkov G. I., Polotsk L. M. Automation of production processes in the chemical industry. – M.: Khimiya, 1982. – 377 p.
- Mankovsky O. N. Heat exchange equipment for chemical production. – Leningrad: Khimiya, 1976. – 348 p.