СИСТЕМЫ ТЕХНИЧЕСКОГО КОНТРОЛЯ И ДИАГНОСТИКИ ПОДВИЖНОГО СОСТАВА
1 Диагностика технического состояния грузового поезда
В основе функционирования транзитного пункта ТО (ПТО) сетевого значения лежит кардинальное изменение технологии дефектоскопирования технического состояния грузовых вагонов. Работа осмотрщиков вагонов заменяется использованием автоматизированных систем неразрушающего контроля, осуществляющих определение дефектов вагонов на ходу поезда при подходе к станции. При этом отбраковка узла или детали вагона производиться автоматически без участия оператора. Это накладывает жёсткие требования к надёжности, быстродействию и условиям эксплуатации используемых диагностических средств. На центральный пункт управления ПТО должны передаваться данные от каждой диагностической системы. Далее по ним принимается решение о необходимости ремонта или отцепки забракованного вагона. Данные о параметрах каждого проконтролированного поезда регистрируются для последующего хранения, часть из них передаётся на следующий СПТО, так как их наличие увеличивает достоверность диагностирования многих дефектов.
Автоматизированные диагностические комплексы контроля технического состояния вагона на ходу поезда должны выявлять следующие неисправности вагонов:
- контроль температуры буксового узла и заторможенных колёс;
- контроль волочения;
- контроль габаритных размеров вагонов;
- контроль дефектов колеса по кругу катания;
- контроль геометрических параметров колеса;
- контроль параметров ударно тягового механизма;
- контроль неравномерности загрузки вагонов;
- контроль сползания буксы с шейки оси.
2 Классификация диагностических систем контроля параметров грузовых вагонов
2.1 Комплекс технических средств многофункциональный
Комплекс технических средств многофункциональный КТСМ-02 представляет собой систему автоматического контроля, включающая в себя одну или несколько подсистем для обнаружения дефектных узлов и деталей подвижного состава (например: букс, колес, тормозов, габарита и т. д.). Основное назначение КТСМ-02 заключается в контроле параметров подвижного состава, привязанных к конкретным осям, или подвижным единицам, а также координации работы подключенных к нему подсистем и обеспечении информационного взаимодействия через систему централизации с системами контроля и управления верхнего уровня (АСК ПС, ДНЦ, ДГП).
2.2 Система комплексного контроля технического состояния подвижного состава на ходу поезда ДИСК-2
Автоматизированная система комплексного контроля второго поколения ДИСК-2 предназначена для оснащения станций с целью наиболее полного охвата контролем неисправностей подвижного состава. В состав системы входят подсистемы для обнаружения перегретых букс (ДИСК-Б); заторможенных колес (ДИСК-Т); волочащихся деталей (ДИСК-В); неровностей колес по кругу катания (ДИСК-К); отклонений верхнего габарита подвижного состава (ДИСК-Г); перегруза или неравномерной загрузки груза (ДИСК-3).
2.3 Автоматизированный бесконтактный комплекс контроля колесных пар подвижного состава
Автоматизированный бесконтактный комплекс контроля колесных пар подвижного состава предназначен для бесконтактного контроля и анализ параметров колесных пар подвижного состава.
Параметры диагностики: толщина гребня колеса, разность и сумма толщин гребней на колесной паре, равномерный прокат, расстояние между внутренними гранями ободов колес, разность расстояний между внутренними гранями ободов, толщина обода, ширина обода, диаметр колеса, разность диаметров колес в одной колесной паре и в тележке, счет количества осей, определение типа подвижного состава, определение количества вагонов в составе, регистрация скорости движения поезда, регистрация времени контроля, направление движения состава.
2.4 Система автоматизированного контроля механизма автосцепки «САКМА»
Данная подсистема применяется для контроля наличия неисправностей автосцепных устройств, по причине которых может произойти саморасцеп автосцепок грузовых вагонов на ходу поезда. Она контролирует:
- износ замков;
- излом направляющего зуба;
- излом предохранителя от саморасцепа;
- износ замков, поверхностей контура зацепления, перемычки между направляющим зубом и сигнальным отростком;
- полуутопленное состояния замков;
- трещины в большом и малом зубе, приводящие в режиме тяги поезда к уширению зуба;
- уширение зева.
В состав системы САКМА входят напольная камера; блок лазерных излучателей; стойка сопряжения; компьютер для обработки информации в помещении диагностического пункта; блок бесперебойного питания и модем.
2.5. Автоматизированная система контроля открытых, незафиксированных и деформированных люков и дверей вагонов
Система предназначена для контроля технического и коммерческого состояния грузовых вагонов в прибывающих на станцию поездах. Система автоматизированного анализа и обработки информации обеспечивает автоматизированное выявление деформаций, открытых люков, качки и других неисправностей на основе обработки и суммирования данных, поступающих от камер и датчиков.
Система осуществляет отображение данных и сигналов тревоги в прибывающих на станцию поездах на АРМ оператора, а так же предоставляет возможность оператору осуществлять анализ технического и коммерческого состояния грузовых вагонов по видеозаписи.
2.6. Детектор дефектных колес ДДК
Аппаратура ДЦК относится к напольным средствам автоматической диагностики технического состояния вагонов на ходу поезда и предназначена для выявления колёсных пар с дефектами на поверхности катания колёс, вызывающих недопустимые динамические перегрузки неподрессоренных элементов вагонов и пути.
Принцип действия аппаратуры ДЦК основан на измерении специальными тензометрическими схемами вертикальных сил, действующих между колесом и рельсом при их динамическом взаимодействии, и сравнении измеренных значений с допустимыми нормируемыми уровнями сил. Превышение нормируемого уровня означает, что на поверхности катания колеса имеется неровность (или несколько неровностей), вызывающая недопустимые динамические перегрузки колёс и рельсов.
Сведения о наличии в составе поезда вагонов с колёсными парами, подлежащими осмотру и браковке, передаются по линии связи на ПТО, перед которым установлена аппаратура ДЦК, в виде текстового файла с выходов специализированного компьютера, установленного на посту диагностики.
Аппаратура ДЦК включает перегонное и станционное оборудование, связанные между собой линией связи.
Напольное оборудование аппаратуры ДДК размещается в непосредственной близости от помещения постового оборудования. При этом сигналы от напольного оборудования по кабелю передаются к постовому оборудованию.
Постовое оборудование аппаратуры ДДК состоит из двух электронных блоков: тензометрического усилителя типа «Sрider-8» и контроллера (специализированного компьютера).
Станционное (приёмное) оборудование аппаратуры ДДК устанавливается непосредственно на ПТО станции прибытия. При этом возможны два варианта станционного оборудования. Первый вариант предусматривает конечный компьютер ДДК на ПТО с устройством печати результатов контроля и звуковыми сигналами тревоги при обнаружении колёсных пар с дефектами. По второму варианту вывод результатов контроля с аппаратуры ДДК производится через локальную связь в систему централизации информации от различных устройств диагностики с выдачей оператору ПТО единого документа – смотрового листа.
2.7. Автоматизированный диагностический комплекс для измерения колесных пар вагонов на подходах к станции
Данный комплекс предназначен для измерения геометрический параметров поверхности катания, а также выявления износа и дефектов цельнокатаных колес на ходу поезда, регистрации неисправностей колесных пар и оперативной передачи полученной информации на ближайший ПТО. Он контролирует параметры поверхности катания колесных пар грузовых вагонов: толщину и высоту гребня, толщину и ширину обода, диаметр по поверхности катания.
2.8. Устройство контроля сползания буксы с шейки оси
Автоматическое устройство контроля сползания буксы с шейки оси предназначено для выявления на ходу поезда роликовых букс, имеющих сползание корпуса с шейки оси, вследствие разрушения торцевого крепления, регистрации таких букс и оперативной передачи полученной информации на ближайший ПТО.
2.9. Устройство контроля тормозов поезда УКТП
Устройство УКТП предназначено для ускоренной зарядки и опробования тормозов поездов на ПТО. Устройство производит автоматическую регистрацию хода опробования тормозов и расчет параметров тормозной системы состава и локомотива с выводом данных в реальном времени на монитор, в сеть АСУ ПТО и на бумажный носитель в виде графиков и по форме ВУ-45.
Устройство позволяет автоматизировать процессы подготовки тормозов подвижного состава в парках отправления, осуществлять контроль над качеством подготовки тормозов и соблюдением технологической дисциплины в парке отправления.
Устройство обеспечивает:
- обработку тормозов при подключении тормозной сети состава и локомотива к питательным стационарным напольным колонкам, располагаемым в междупутье парка отправления;
- обработку тормозов состава;
- контроль пневматической части тормозов локомотива;
- непрерывный контроль на мониторе ПК за изменением утечки и давления воздуха в тормозной магистрали состава;
- регистрацию процессов подготовки тормозов;
- выдачу на основе измеренных параметров рекомендаций по ведению обработанного на маршруте с учетом местных инструкций и состояний автотормозов состава;
- создание пакета документов о работе ПТО (ВУ-45 и др.);
- зарядку и опробование тормозов в полуавтоматическом режиме с дистанционным управлением процессами при использовании радиостанций.
Устройство включает в себя:
- пульт оператора парка ПОП, имеющий в составе: персональный компьютер ПК; принтер ПУ; блок связи БС; радиостанцию оператора РС;
- пульт дистанционного управления ПДУ, подключенный к радиостанции осмотрщика;
- блок БС;
- электрические коммуникации, предназначенные для обмена информацией между блоками устройства и подачи питающего напряжения на БПК;
- блок питательной напольной колонки БПК;
- пневматические коммутации, предназначенные для подвода воздуха от напорной сети парка к БПК;
- блок хвостового вагона БХВ, предназначенный для контроля давления в тормозной магистрали хвостового вагона.
2.10. Комплексная информационно-измерительная система технического диагностирования подвижного состава
В качестве примера разрядности комплексной системы технической диагностики рассмотрим комплексную информационно-измерительную систему ТО и ремонта колесных пар депо. Анализ порч и неисправностей колесных пар подвижного состава на железнодорожном транспорте показывает, что они существенно влияют на безопасность движения. Именно поэтому техническое диагностирование и предупреждение отказов в пути следования колесных пар является одним из важнейших факторов обеспечения безопасности движения поездов.
Комплексная информационно-измерительная ТО и ремонта депо имеет иерархическую структуру, содержащую три уровня (см. рис. 1).
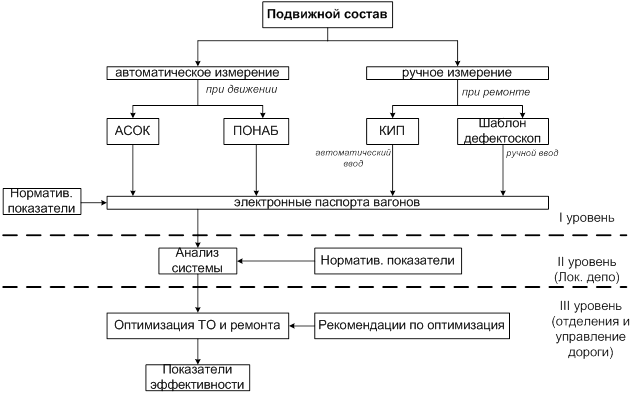
Рисунок 1 – Комплексная система диагностики подвижного состава
Первый уровень структуры включает систему контроля параметров колесных пар, выполняющую автоматическое измерение параметров при движении подвижного состава, ручное измерение параметров колесных пар при ремонте и ТО. Автоматическое измерение параметров комплексных пар выполняется с помощью двух подсистем: автоматической системы обмера колесных пар (АСОК) и автоматической системы обнаружения трещин и дефектов поверхности катания колесных пар. Ручное измерение параметров колесных пар проводится с помощью комплексного переносного измерителя параметров колесных пар (КИП), шаблонов и дефектоскопии. Все подсистемы автоматического и ручного измерения параметров колесных пар сопровождаются метрологическим обеспечением. Выходная информация с указанных подсистем поступает на программный комплекс контроля над нормативными параметрами колесных пар и ведением электронных паспортов колесных пар. Причем информация с подсистем ручного измерения вводится в программный комплекс через устройства автоматического и ручного ввода данных. Также в программный комплекс вводятся нормативные показатели.
Программный комплекс обрабатывает информацию, поступающую с подсистемы измерения параметров колесных пар, формирует электронные паспорта на каждую колесную пару соответствующий единицы подвижного состава, сравнивает результаты измерений с нормативными показателями, систематизирует информационный поток и организует базу данных для передачи на следующий уровень комплексной системы. Кроме этого, программный комплекс через устройства аварийного предупреждения о выводах параметров колесных пар за пределы допуска подает соответствующие сигналы в подсистемы измерения, а также формирует фразу текущих данных обследования колесных пар для последующего использования при обработке и прогнозировании в службах депо.
Второй уровень структуры (см. рис. 1) АРМ по колесным парам, которое включает программный комплекс анализа состояния колесного парка депо. В данный программный комплекс обязательно вводится нормативные технические параметры обслуживания колесных пар. Программный комплекс также организует БД для передачи на следующий уровень структуры комплексной системы ТД, выдает информацию для составления отчетных форм и через подсистему планирования обслуживания колесных пар формирует соответствующие данные.
АРМ по колесным парам должно удовлетворять общим требованиям: анализировать диагностическую информацию, используемую для выполнения технико-экономических расчетов; оценивать качество диагностирования для периодической корректировки методики диагностирования с выработкой рекомендаций по срокам и объемам ТО и текущего ремонта каждой единицы подвижного состава, по срокам очередного контроля составления элементов соответствующей единицы подвижного состава и др.
Третий уровень структуры состоит из программного комплекса оптимизации ТО и ремонта колесных пар по критериям экономической эффективности подсистемы контроля и управления ремонта колесных пар.
3. Автоматизированная система контроля подвижного состава
Автоматизированная система контроля подвижного состава (АСК ПС) предназначена для автоматизации процесса сбора, передачи и обработки показаний аппаратуры контроля перегретых букс типа ПОНАБ, ДИСК и КТСМ с целью обеспечения централизованного контроля технического состояния поездов на участках движения. Контроль за показаниями аппаратуры контроля перегрева буксовых узлов вагонов осуществляется оператором центрального поста контроля АСК ПС регионального ЦУП. При обнаружении в составе поезда вагона (локомотива) с повышенным уровнем нагрева буксового узла на экране монитора появляется информационное окно и раздается звуковой сигнал. В информационном окне выводятся данные о показании установки ПОНАБ, КТСМ, ДИСК, которые содержат: название пункта контроля, зафиксировавшего повышенный нагрев буксового узла с указанием направления (четное, нечетное), порядкового номера вагона в поезде, начиная с головы, порядкового номера оси вагона, стороны вагона и уровня нагрева буксового узла с каждой стороны вагона.
Комплекс технических средств АСК ПС представляет собой распределенную структуру специализированных аппаратно-программных комплексов, объединенных единой СПД. По своему функциональному назначению технические средства АСК ПС подразделяются на технические средства линейных пунктов контроля (ЛПК) и оборудование центрального поста контроля (ЦПК).
В состав технических средств ЛПК входит: один или более периферийных контроллеров ПК, предназначенных для сбора и передачи показаний аппаратуры контроля ПОНАБ и ДИСК-Б в АРМы ЛПК и ЦПК соответственно. Каждый ПК может осуществлять ввод информации от 4-х приемных (станционных) стоек аппаратуры контроля типа ПОНАБ-3 или ДИСК-Б.
Примерная структурная схема комплекса технических средств АСК ПС приведена на рис. 2.
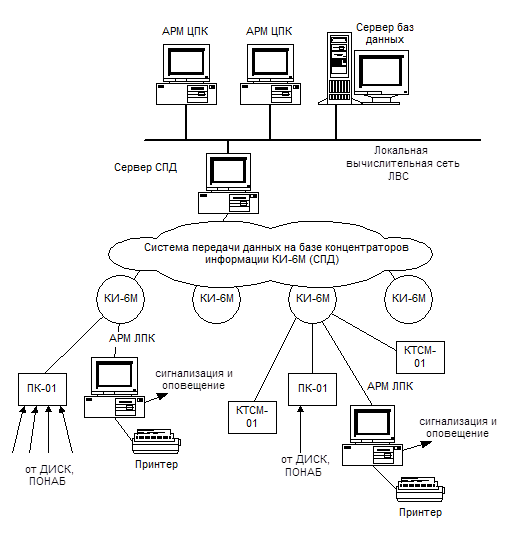
Рисунок 2 – Структурная схема АСК ПС
Оборудование АСК ПС центрального поста контроля представляет собой локальную вычислительную сеть (ЛВС), содержащую:
1) сервер БД – ЭВМ, функционирующую под управлением сетевой операционной системы (ОС) и системой управления базами данных (СУБД);
2) сервер СПД – ЭВМ, обеспечивающую информационный обмен между сетью передачи данных и сервером ЛС , а также осуществляющую контроль работы концентраторов СПД, периферийных контроллеров и каналов информационной связи между ними;
3) рабочие станции (АРМы) – ЭВМ, на которых выполняется прикладная программа АРМ ЦПК
и использующие информацию, содержащуюся на сервере БД.
Сервер СПД принимает, осуществляет обработку и помещает в файлы информационных баз показаний аппаратуры контроля, размещенные на файловом сервере ЛВС. Прикладные системы (АРМы ЦПК), включенные в локальную вычислительную сеть диспетчерского центра, осуществляют чтение информации из файлов баз показаний аппаратуры контроля для выполнения различных задач формирования оперативных и статистических данных. Программное обеспечение АРМов ЛПК дополнительно к прикладным задачам содержит функции сервера СПД по управлению и диагностике устройств.
4. Функции информационно-управляющего комплекса АСУ СПТО
Автоматизация функций оперативного управления техническим обслуживанием и ремонтом грузовых вагонов и функций взаимодействия с пользователями линейного уровня включает в себя:
1. контроль за поездами, находящимися на линии;
2. планирование ТО и текущего ремонта;
3. информационная поддержка ТО и текущего ремонта;
4. автоматизация ведения учета и анализа производственной деятельности;
5. автоматизация ведения учета запасных частей и материалов;
6. ведение технологической, нормативной и организационной документации;
7. организация взаимодействия причастных работников линейных предприятий.
5. Информационное взаимодействие АСУ СПТО с системами технической диагностики технического состояния вагонов
АСУ ПТО функционирует, как одна из подсистем АСУ опорной станции, работа которой осуществляется на единой БД и не требует специального обмена информацией между смежными подсистемами. Взаимодействие с АСУ дорожного и сетевого уровней обеспечивается по единым правилам обмена:
- на уровне прикладных задач на основе ведомственного протокола информационного взаимодействия систем АСУЖТ (протокол обмена сообщениями);
- на транспортном уровне на основе протокола НТТР, являющегося основным протоколом взаимодействия подсистем АСУ ОЦ.
Рассмотрим транспортный протокол взаимодействия АСУ опорной станции (АСУ ОЦ) с системами технической диагностики.
Он обеспечивает вызов, запуск на выполнение, передачу и прием данных от сервера приложений АСУ ОЦ. Обращение к серверу приложений, оформление данных выполняется в соответствии со спецификацией протокола НТТР.
В общем виде к серверу приложений формируется в следующем виде: http:/serverd.pvrr.mps:88/Cart?par1=val1, где serverd – имя хоста, на котором находится сервер приложений; pvrr.mps – имя интернет-домена, на котором находится требуемый хост; 88 – номер порта, на который настроен лисенер сервера приложений; Cart – название картриджа (прикладной задачи сервера приложений).
Адресация абонентов в АСУ ОЦ основана на применении идентификационных кодов (обозначений) называемых логическими номерами.
Структура логического номера имеет вид – DD.LL.ХХХХ, где
DD – номер дороги в соответствии с единой сетевой разметкой,
LL – номер линейного района,
ХХХХ – уникальный номер рабочего места в данном линейном районе.
Идентификацию по логическим номерам имеют: АРМы; серверы разных уровней АСУЛР; внешние системы (АСОУП, КГМ, и т.д.). Формат входных сообщений с контрольно-диагностических устройств аппаратуры ДИСК-2 и системы КТСМ состоит из служебной фразы, содержащей информацию о поезде, и несколько информационных фраз, содержащих данные о тревожных вагонах.
Структура служебной фразы имеет следующий вид:
:XXXX – код сообщения;
4 знака – адрес устройства;
1–4 знака – номер поезда;
1–4 знака – число осей в поезде;
1–3 знака – число вагонов в поезде;
ччмм – время захода поезда;
ччмм – время схода поезда.
Структура информационной фразы определяется номером Ю. Однотипных фраз может быть несколько по разным вагонам, осям.
Структура фразы Ю1 (износ колеса) состоит из: 2 знака – тип фразы; 1–3 знака – порядковый номер вагона (без учета головного локомотива); 1 знак – тип вагона (1 – холодный локомотив, 2 – пассажирский вагон, 3 – грузовой вагон); 1–2 знака – количество осей в вагоне; 1–2 знака – номер оси (в пределах вагона); 1–2 знака – длина неровности (в мм); 1–2 знака – глубина неровности (в мм); 1–2 знака – уклон неровности (в мм); 1 знак – тип износа (1 – ползун, 2 – навар, 3 – неравномерный прокат, 4 – тонкий гребень, 5 – тонкий обод); 1 знак – уровень тревоги (1 – Т0, 2 – Т1, 3 – Т2).
Структура фразы Ю2 (уровень нагрева буксы, ступицы) включает в себя: 2 знака – тип фразы; 1–3 знака – порядковый номер вагона; 1 знак – тип вагона; 1–2 знака – количество осей в вагоне; 1–2 знака – номер оси; 1 знак – нагрев левой буксы; 1 знак – нагрев правой буксы; 1 знак – нагрев левой ступицы; 1 знак – нагрев правой ступицы; 1 знак – уровень тревоги левой буксы; 1 знак – уровень тревоги правой буксы; 1 знак – уровень тревоги левой ступицы; 1 знак – уровень тревоги правой ступицы.
Структура фразы Ю3 (нарушение габаритов) содержит следующую информацию:
2 знака – тип фразы; 1–3 знака – порядковый номер вагона; 1 знак – тип вагона; 1–2 знака – количество осей в вагоне; 1 знак – верхний габарит; 1 знак – левый габарит; 1 знак – правый габарит; 1 знак – волочение (левый наружный); 1 знак – волочение (левый внутренний); 1 знак – волочение (правый внутренний); 1 знак – волочение (правый наружный).
Структура фразы Ю4 (неравномерность загрузки вагона) имеет:
2 знака – тип фразы; 1–3 знака – порядковый номер вагона; 1 знак – тип вагона; 1–2 знака – количество осей в вагоне; 3 знака – вес вагона в тоннах; 3 знака – процент неравномерности по тележкам; 3 знака – процент неравномерности по сторонам; 1 знак – уровень тревоги.
Структура фразы Ю5 (уровень тревоги по тормозам) состоит из:
2 знака (Ю4) – тип фразы; 1–3 знака – порядковый номер вагона; 1 знак (1) – тип вагона; 1–2 знака – количество осей в вагоне; 1 знак (1) – уровень тревоги по тормозам.
Структура фразы Ю6 (уровень бальности вагона) имеет:
2 знака – тип фразы; 1–3 знака – порядковый номер вагона; 1–5 знаков – уровень бальности.
Структура фразы Ю7 (уровень сползания буксы с оси колеса) состоит: 2 знака – тип фразы; 1–3 знака – порядковый номер вагона; 1–2 знака – номер оси; 1 знак – сторона вагона;1 знак или 1знак, 1знак (через запятую) – размер сползания.
6. Заключение
Применение комплексных систем ТД подвижного состава позволяет повысить безопасность движения за счет выработки рекомендаций об индивидуальных объемах ремонта каждой единицы подвижного состава с учетом действительного технического состояния. Экономический эффект от внедрения указанной системы можно представить в виде трех составляющих. Первая составляющая – экономический эффект, реализуемый на сетевом уровне. Он связан с безопасностью движения, с уменьшением затрат энергии и топлива на тяговое усилие локомотивов, уменьшение числа повреждений стрелочных переводов и динамических нагрузок на путь. Вторая составляющая – экономический эффект, реализуемый в дело и обусловленный снижением затрат на ТО. Третья составляющая – экономический эффект, реализуемый в дело и связанный с повышением срока службы подвижного состава. Например, по данным опыта эксплуатации систем контроля и паспортизации колесных пар в США при профилактике достижения 50%-ного износа гребня бандажей колес срок службы или пробег колесной пары повышается на 20%.
Наиболее сложным этапом при построении комплексных систем ТД является выделение групп элементов, подлежащих диагностированию, и недиагностируемых. Для такой классификации целесообразно использовать технико-экономические критерии. В число диагностируемых включаются те элементы подвижного состава, исправность которых в наибольшей степени обеспечивает безопасность движения и работоспособность каждой единицы подвижного состава.
К недиагностируемым элементам каждой единицы подвижного состава относится оборудование, диагностирование которого экономически нецелесообразно или технически невозможно. Недиагностируемые элементы должны иметь высокий уровень безопасности, несущественное влияние отказов на работоспособность подвижного состава, небольшие материальные затраты на устранение отказов.