Реферат за темою випускної роботи
Зміст
- Вступ
- 1. Завдання технічного діагностування
- 2. Функції та параметри діагностування
- 3. Методи діагностування
- 3.1 Органолептичний метод діагностування
- 3.2 Вібраційний метод діагностування
- 3.3 Акустичний метод діагностування
- 3.4 Тепловий метод
- 3.5 Трібодіагностіческій метод
- 3.6 Діагностика на основі аналізу продуктів зносу в продуктах згоряння
- 3.7 Метод акустичної емісії
- 3.8 Радіографічний метод
- 3.9 Магнітопорошковий метод контролю
- 3.10 Вихрострумовий метод діагностування
- 3.11 Ультразвуковий метод діагностування
- 3.12 Капілярний метод діагностування
- 4. Діагностика стану електрообладнання електростанцій і підстанцій за допомогою засобів інфрачервоної техніки на практиці
- 5. Проблеми технічної діагностики
- Висновки
- Перелік джерел
Вступ
Діагностика електрообладнання займає все більш важливе місце в сучасній електроенергетичної галузі України та Росії, що диктується, насамперед, необхідністю продовження терміну служби або інтервалу часу безаварійної роботи силового електрообладнання. Знос основних фондів електроенергетики давно вже перевалив за 50%. В даний час галузь не має ні фінансовими, ані технічними можливостями в найкоротші терміни замінити обладнання, яке вичерпало свій нормативний ресурс. Щорічний приріст парку електрообладнання з наднормативним терміном служби значно перевищує приріст знову вводиться обладнання, зважаючи на це використання системи планово-попереджувальних ремонтів для підтримки необхідної експлуатаційної готовності обладнання стає все більш складним. До переходу до ремонту в залежності від фактичного стану підштовхує бурхливий розвиток засобів і методів технічної діагностики.
В електроенергетичної галузі назріла проблема створення системи технічної діагностики, яка дозволила б вирішити проблему організації ремонтів електрообладнання відповідно до його станом. Крім того, необхідність підвищення експлуатаційної безвідмовності працюючого електроустаткування, в умовах, що склалися, за рахунок виявлення дефектів, прогнозування їх розвитку, представляється актуальним завданням [1].
В якості фундаменту для побудови ефективної системи діагностування повинні застосовуватися такі засоби і методи діагностики, які мають досить високою інформативністю, технічним і нормативним забезпеченням, а також мають гнучку методологічну базу прийняття рішень. Поряд з традиційними методами контролю, за останнє десятиліття, знайшли застосування сучасні високоефективні способи діагностики, що забезпечують виявлення дефектів електрообладнання на ранній стадії їх розвитку і дозволяють контролювати досить широкий перелік параметрів.
1. Завдання технічного діагностування
В даний час на сучасних вітчизняних і зарубіжних електростанціях, підстанціях і в електричних мережах експлуатується значна кількість зношеного електрообладнання. Наприклад, в США за станом на 1997р. близько 65% силових трансформаторів відпрацювали більше 25 років, в Росії знос основних фондів електроенергетики становить близько 50%[2,3]. Станом на кінець 2005 р. середній термін експлуатації електрообладнання Україні вже перевищує половину проектного, що призводить до зниження надійності його функціонування, зростанню аварійності.
Існуюча у вітчизняній електроенергетиці система планово-попереджувальних ремонтів електрообладнання [2,3] не завжди виправдана, оскільки вона не враховує його реальне техніческоеьсостояніе, і часто вимагає виведення з роботи працездатного обладнання.
Тому виникає необхідність розробки нових технологій і практичних методів, що забезпечують ефективне технічне обслуговування та ремонт електрообладнання за технічним станом. Це в свою чергу зумовлює розвиток існуючих методів і засобів контролю для отримання діагностичної інформації, розробки математичних моделей і алгоритмів оцінки технічного стану електрообладнання, що становлять основу експертної системи прийняття рішень [2,4].
У загальному випадку експертна система оцінки технічного стану електрообладнання визначає наступне: чи знаходиться обладнання в нормальному стані, що не вимагає будь-якого втручання; чи потрібно додаткову увагу з боку персоналу або прискорений контроль параметрів обладнання; чи необхідно виконання додаткових вимірювань, випробувань та інших профілактичних заходів з відключенням і без відключення; чи потрібно проведення ремонтів, модернізації, полегшення режимів роботи або висновок електрообладнання з роботи.
Для оцінки технічного стану електрообладнання можна використовувати автоматичний класифікатор, побудований на основі нечітких алгоритмів і дозволяє на основі параметрів стану віднести об'єкт діагностування до одного з класів технічного стану [4].
Стан силового електрообладнання характеризується великою кількістю параметрів стану (ознак), значення яких можна отримати використовуючи штатні засоби вимірювання або ж шляхом проведення додаткових випробувань на працюючому або відключеному обладнанні. При великому числі параметрів стану, побудова нечіткої бази знань експертної системи стає важкоздійснюваним завданням.
2. Функції та параметри діагностування
Діагностика технічного стану електрообладнання може здійснюватися як спеціальними приладами, якими виробляються прямі вимірювання електричних параметрів контрольованих об'єктів традиційними методами, так і приладами для вимірювання непрямих характеристик електрообладнання, наприклад температури поверхні, на безконтактному вимірюванні який заснований теплової неруйнівний контроль – тепловизионная діагностика, але всі процеси діагностування технічних об'єктів включає в себе наступні функції:
- оцінка технічного стану об'єкта;
- виявлення і визначення місця локалізації несправностей;
- прогнозування залишкового ресурсу об'єкта;
- моніторинг технічного стану об'єкта.
Під діагностичними параметрами розуміють репрезентативні параметри, за якими можна судити про стан об'єкта Розрізняють прямі і непрямі діагностичні параметри. Перші безпосередньо характеризують стан об'єкта, а другі пов'язані з прямими параметрами функціональною залежністю [4].
При функціональної діагностики об'єкта в процесі його роботи – поряд з окремо розглянутими параметрами – можуть використовуватися також як ознака стану функціональні зв'язки (функціональні залежності) параметрів.
3. Методи діагностування
Залежно від технічних засобів і діагностичних параметрів, які використовують при проведенні діагностування, можна скласти наступний неповний список методів діагностування:
- органолептичні методи діагностування;
- вібраційні методи діагностування;
- акустичні методи діагностування;
- теплові методи;
- трібодіагностіка;
- діагностика на основі аналізу продуктів зносу в продуктах згоряння;
- метод акустичної емісії;
- радіографія;
- магнітопорошковий метод;
- вихрострумовий метод;
- ультразвуковий контроль;
- капілярний контроль;
- методи параметричної діагностики;
- електродіагностичний контроль. Сфера застосування – електродвигуни, електромагнітні клапани, котушки, кабелі, трансформатори. Розрізняють статичні і динамічні випробування електроагрегатів;
- специфічні методи для кожної з областей техніки (наприклад, при діагностуванні гідроприводу широко застосовується статопараметріческій метод, заснований на аналізі задросселірованного потоку рідини; в електротехніці застосовують методи, засновані на аналізі параметрів електричних сигналів, в складних багатокомпонентних системах застосовують методи діагностування по стохастичним відхилень параметрів від їх усереднених значень і т. д.).
Розглянемо більш докладно всі методи діагностування.
3.1 Органолептичний метод діагностування
Органолептичні методи діагностування засновані на використанні органів чуття людини.
pВізуальний огляд, контроль температури і візуалізація механічних коливань входять в список органолептичних методів діагностування та контролю роботи обладнання. Вони є досить ефективними і не вимагають матеріальних витрат, так як в ролі діагностичного «приладу» в даному випадку виступає людина.
Контроль температури є важливим аспектом оцінки технічного стану механічного обладнання. До 95% всіх форм енергії, створюваної і переданої машинами прямо або частково, перетворюється на теплову енергію. Параметром теплового діагностування є температура, що відображає перебіг робочого процесу і розвиток цілого ряду несправностей.
Температура нагріву корпусів механізмів як діагностичний параметр має дві особливості: поява деяких видів несправностей викликає підвищення температури корпусу механізму; інерційність нагріву металевих деталей, корпусів і опор не дозволяє використовувати даний параметр для визначення раптових відмов і зароджуються пошкоджень. Правила технічної експлуатації регламентують граничну температуру корпусів підшипників, яка не повинна перевищувати температуру навколишнього середовища більше ніж на 40°С і бути не вище 60-80°С. Для деяких механізмів, що мають циркуляційних систем мастила або охолодження, оцінюють різницю температур масла або води на виході і вході. Це дозволяє контролювати теплові процеси, загальний стан обладнання, а також ступінь його погіршення. Зазвичай різниця температур на виході і вході не повинна перевищувати 5-10°С.
3.2 Вібраційний метод діагностування
Вібраційні методи діагностування засновані на аналізі параметрів вібрацій технічних об'єктів.
Вібраційна діагностика – метод діагностування технічних систем і устаткування, заснований на аналізі параметрів вібрації, або створюваної працюючим обладнанням, або є вторинною вібрацією, зумовленої структурою досліджуваного об'єкта.
Вібраційна діагностика, як і інші методи технічної діагностики, вирішує завдання пошуку несправностей та оцінки технічного стану досліджуваного об'єкта.
При вібраційної діагностиці як правило досліджуються тимчасової сигнал або спектр вібрації того чи іншого обладнання. Також застосовується кепстральних аналіз (кепстра – анаграма слова спектр).
При вібраційної діагностиці аналізуються віброшвидкість, вібропереміщення, віброприскорення [6].
В якості діагностичних параметрів можуть виступати наступні:
- ПІК – максимальне значення сигналу на даному інтервалі часу;
- СКЗ – середнє квадратичне значення (діюче значення) сигналу для розглянутої смуги частот;
- ПІК-фактор – ставлення параметра ПІК до СКЗ;
- ПІК-ПІК – (Розмах) різниця між максимальним і мінімальним значенням сигналу на даному інтервалі часу;
- SPM – метод ударних імпульсів, заснований на використанні спеціального датчика з резонансною частотою 32 кГц і алгоритму обробки ударних хвиль малої енергії, що генеруються підшипниками кочення внаслідок зіткнень і змін тиску в зоні кочення цих підшипників (Едвін Сёхль, SPM Instrument, Швеція, 1968р .);
- EVAM – Абревіатура EVAM є скороченням від "Evaluated Vibration Analysis Method", що в перекладі означає "Метод аналізу вібрації з оцінкою стану". Метод EVAM® об'єднує в собі різні загальновизнані методики аналізу вібросигналів разом з програмними засобами практичної оцінки стану обладнання на основі результатів такого аналізу. Підтримується програмно і апаратно, як і метод SPM, обладнанням і ПО виробництва фірми SPM Instrument AB (Швеція);
- SPM-M: пік-фактор на резонансній частоті акселерометра (ТОВ біфорії) (1980р.);
- RPF: пік-фактор вищих частот вібрації механізмів (1982р.);
- VСС – контроль ступеня кондиції мастила (1995р.);
- ARP: розподіл амплітуд імпульсів сухого тертя у вузлах машин (2001р.);
- Entropy – вібраційно-ентропійна оцінка стану вузлів машин (2002р.).
З датчиків вібрації найбільш часто застосовуються акселерометри (віброперетворювачі прискорення) п'єзоелектричні датчики.
Найбільшого розвитку метод отримав при діагностуванні підшипників кочення. Також вібраційний метод успішно застосовується при вібровипробування виробів та діагностиці колісно-редукторних блоків на залізничному транспорті.
Заслуговують на увагу віброакустичні методи пошуку витоків газу і в гідрообладнанні. Суть цих методів полягає в наступному. Рідина або газ, дросселіруя через щілини і зазори, створює турбулентність, що супроводжується пульсаціями тиску, і, як наслідок, в спектрі вібрацій і шуму з'являються гармоніки відповідних частот. Аналізуючи амплітуду цих гармонік, можна судити про наявність (відсутність) течей [7].
Інтенсивний розвиток методу в останні роки пов'язано із здешевленням електронних обчислювальних засобів і спрощенням аналізу вібраційних сигналів [8].
Переваги методу:
- метод дозволяє знаходити приховані дефекти;
- метод, як правило, не вимагає складання-розбирання обладнання;
- малий час діагностування;
- можливість виявлення несправностей на етапі їх зародження;
- зниження очікуваного ризику виникнення аварійної ситуації при експлуатації обладнання.
Недоліки:
- особливі вимоги до способу кріплення датчика вібрації;
- залежність параметрів вібрації від великої кількості факторів і складність виділення вібраційного сигналу обумовленого наявністю несправності, що вимагає глибокого застосування методів кореляційного і регресійного аналізу;
- точність діагностування в більшості випадків залежить від числа згладжених (усереднених) параметрів, наприклад, числа оцінок SPM.
3.3 Акустичний метод діагностування
З датчиків сигналів (часткових розрядів) ЧР (електричні, електромагнітні, акустичні) велике застосування отримали акустичні. Акустичний метод діагностування, заснований на аналізі параметрів звукових хвиль, що генеруються технічними об'єктами та їх складовими частинами.
Електричні датчики здатні дати наближену локалізацію джерела сигналів ЧР, засновану тільки на порівнянні інтенсивностей сигналів в різних точках обладнання (трансформатора). Для локалізації дефекту зазвичай використовують акустичні датчики, які хоч і мають значно меншу чутливість, але, завдяки порівняно низькій швидкості поширення акустичних сигналів (час проходження звукової хвилі значно більше, ніж тривалість електричного імпульсу), дозволяють провести досить точну локалізацію джерела сигналів усередині трансформатора (в просторі). Акустичні датчики практично не схильні зовнішніх перешкод на підстанції. Вимірювання сигналів ЧР в реальних умовах експлуатації хоча і стикається з певними труднощами, але є цілком розв'язуваної завданням. В даний час успішно випробувана на силовому обладнанні підстанцій практично всіх класів напруг і потужностей система СКІ-2. Вона використовувалася як при одноразових вимірюваннях, так і в режимі безперервного автоматичного моніторингу. Апаратура надійно реєструє сигнали ЧР з рівнями 50-500 пКл навіть в умовах дуже сильних перешкод високої інтенсивності з амплітудою, що досягає 15 пКл. У Росії освоєний комплект для акустичного визначення рівня часткових розрядів на базі акустичного приймача LDA 5 / S компанії «Intereng Messtechnik». За допомогою його визначаються місця часткових розрядів в трансформаторах, вимикачах, перетворювачах струму і напруги. Кращі результати діагностування можна отримати при використанні методу ЧР і дефектоскопа «Філін-6».
3.4 Тепловий метод
Метод інфрачервоної термографії. Втрати електричної енергії на нагрів елементів і вузлів електрообладнання в процесі експлуатації залежать від їх технічного стану. До теплового методу так само відноситься метод діагностування, заснований на використанні тепловізорів.
Вимірюючи інфрачервоне випромінювання, обумовлене нагріванням, можна зробити висновки про технічний стан електрообладнання. Невидиме інфрачервоне випромінювання за допомогою тепловізорів перетвориться у видиме людиною сигнал. Даний метод дистанційний, чутливий, що дозволяє реєструвати зміни температури в частки градуса. Тому його показання сильно схильні впливає факторам, наприклад, відбиває здатності об'єкта вимірювання, температурі і станом навколишнього середовища, так як запиленість і вологість поглинають інфрачервоне випромінювання, та інші.
3.5 Трібодіагностіческій метод
Трібодіагностіка – аналіз складу масла (продуктів зносу, окислення і забруднення сторонніми речовинами). Це один з найефективніших методів діагностики стану тертьових деталей механізмів. Трібодіагностіка стосовно до машинного обладнання являє собою оцінку його технічного стану за складом і концентрації продуктів зносу в робочому маслі за допомогою спеціальних приладів та обладнання (аналізаторів масла, атомно-емісійних та ІЧ спектрометрів, рентгено-флюорісцентних аналізаторів і т.д.). Аналіз проб масла на даному обладнанні дозволяє визначити концентрацію в ньому того чи іншого елемента, з якого зроблені деталі механізму, що піддаються тертю. Знаючи цю величину, визначають усереднений знос відповідної деталі і роблять висновок про необхідність проведення ремонтних робіт.
Трібодіагностіка – це перспективний превентивний метод оцінки стану машинного обладнання, що дає достовірні дані про його робочому стані і ступеня зносу. Однак на сьогоднішній день даний метод не отримав широкого розповсюдження у промисловості. Трібодіагностіка в якості повсякденної практики поки використовується тільки для обслуговування газотурбінних двигунів. Але перспективно її застосування для оцінки працездатності підшипників кочення і інших вузлів машин.
3.6 Діагностика на основі аналізу продуктів зносу в продуктах згоряння
Відомо, що руйнування деталей проточної частини ГПА, що викликається перегрівом, газовою корозією, абразивним зносом, супроводжується виносом з ГПА разом з газовим потоком найдрібніших частинок металу. Початок руйнування і його характер, можна визначити, реєструючи наявність продуктів зносу та їх склад. Звідси розглянутий метод аналогічний методу діагностики з аналізу продуктів зносу в маслі. Вирішення цього завдання базується на застосуванні імпульсного методу з лазерним джерелом для визначення концентрації в газовому турбулентному потоці. Експериментально показано, що метод дозволяє проводити миттєві (протягом 10-14 с) і одночасні вимірювання локальних концентрацій у сумішах в багатоатомних газах. Визначення складу та концентрації продуктів зносу проводять в процесі аналізу складу проб продуктів згоряння, взятих з вихлопного тракту ГПА. Недолік даного методу пов'язаний з його трудомісткістю і дискретністю контролю технічного стану. Перспективність ж його пов'язана з тим, що цей метод є досить ефективним для діагностування такого важливого вузла, як камера згоряння ГПА, в даний час найменш охопленого діагностуванням.
3.7 Метод акустичної емісії
Для контролю широко застосовуються всі види і діапазони випромінювання. Метод акустичної емісії працює в звуковому діапазоні. Відомий метод контролю оптичного випромінювання ПР за допомогою електронно-оптичного дефектоскопа. Він заснований на реєстрації просторово часового розподілу яскравості світіння і визначенні за її характером дефектних ізоляторів. Для цих же цілей з різною ефективністю застосовують радіотехнічний і ультразвуковий методи, а також метод контролю ультрафіолетового випромінювання за допомогою електронно-оптичного дефектоскопа «Філін».
3.8 Радіографічний метод
Контроль заснований на проникненні гамма і рентгенівських променів крізь матеріали, метод широко застосовується в неруйнівному контролі. Використовується для визначення внутрішніх дефектів в металі і обладнанні.
За допомогою радіографічних методів перевірки розподільного пристрою на наявність зносу і дефектів компанія ABB заощадила американському замовнику 38 діб простою, потрібних на профілактичне обслуговування 26 автоматичних вимикачів, причому витрати на цю перевірку склали менше половини звичайної вартості подібного техобслуговування. Наприклад, при перевірці автоматів на напругу 35-145 кВ звичайним методом потрібно два дні, а радиографическая дефектоскопія дозволяє виконати цю роботу за дві години. Якщо ж взяти автоматичний вимикач на 550 кВ, то буде потрібно відповідно п'ять діб і чотири години. Основною перевагою радіографії є можливість залишити елегаз в розподільчому пристрої, а не відкачувати його, як це має місце при звичайній перевірці.
3.9 Магнітопорошковий метод контролю
Магнітопорошковий метод – один з найпоширеніших, надійних і продуктивних методів неруйнівного контролю поверхонь виробів з феромагнітних матеріалів в їх виробництві та експлуатації.
МПК – один з чотирьох класичних методів неруйнівного контролю, а також один з найбільш старих методів НК, пов'язаних із застосуванням приладів і дефектоскопічних матеріалів для НК. Перші досліди описали феномен полів магнітного розсіювання і пояснили їх значення. Згодом були зроблені спроби знайти застосування цьому явищу і ввести його в технічну практику. У 1868 році англієць Саксбі застосував компас для визначення дефектів в гарматних стовбурах. У 1917 році американець Хок застосував залізні ошурки для виявлення тріщин в сталевих деталях.
Суть методу така: магнітний потік в бездефектной частини виробу не змінює свого напрямку; якщо ж на шляху його зустрічаються ділянки зі зниженою магнітною проникністю, наприклад, дефекти у вигляді розриву суцільності металу (тріщини, неметалеві включення і т.д.), то частина силових ліній магнітного поля виходить з деталі назовні і входить в неї назад, при цьому виникають місцеві магнітні полюси (N і S) і, як наслідок, магнітне поле над дефектом. Так як магнітне поле над дефектом неоднорідне, то на магнітні частинки, що потрапили в це поле, діє сила, яка прагне затягнути частинки в місце найбільшої концентрації магнітних силових ліній, тобто до дефекту. Частинки в області поля дефекту намагнічуються і притягуються один до одного як магнітні диполі під дією сили так, що утворюють ланцюгові структури, орієнтовані по магнітним силовим лініям поля.
Метод магнітопорошкового контролю призначений для виявлення тонких поверхневих і підповерхневих порушень суцільності металу – дефектів, що поширюються вглиб виробів. Такими дефектами можуть бути тріщини, волосовини надриви, флок, непровари, пори. Найбільша вірогідність виявлення дефектів досягається у випадку, коли площина дефекту становить кут 90 з напрямком намагнічує поле (магнітного потоку). Зі зменшенням цього кута чутливість знижується і при кутах, істотно менших 90° дефекти можуть бути не виявлені.
3.10 Вихрострумовий метод діагностування
Вихрострумовий метод заснований на аналізі взаємодії зовнішнього електромагнітного поля з електромагнітним полем вихрових струмів, що наводяться збудливою котушкою в електропровідному об'єкті контролю. Вихрострумовий метод дозволяє виявляти дефекти типу несплошностей, що виходять на поверхню або залягають на невеликій глибині, а також тріщини, розшарування, неметалеві включення і т.д.
Вихрострумовий контроль знаходить застосування для аналізу електропровідних матеріалів: метали, напівпровідники, графіт, сплави, а також неферромагнетікі. Застосовується, в основному, для пошуку тріщин і корозійного розтріскування під напругою (КРН) на газонафтопроводів.
3.11 Ультразвуковий метод діагностування
Ультразвуковий контроль також найбільш поширений метод, цей метод можна розділити на ультразвукову дефектоскопію (УЗД) та ультразвукове товщинометрії (УЗТ). Ультразвукова дефектоскопія використовується, як правило, для контролю зварних швів і основного металу обладнання з метою пошуку різних дефектів як підповерхневих, так і внутрішніх. Використовувана частота 2,5 або 5 МГц. Ультразвукова товщинометрія використовується для вимірювання товщини феромагнітних матеріалів за допомогою ультразвукових хвиль. Існує також метод довгохвильової хвилі, але він діє на обмеженій дистанції і широкого застосування не має.
3.12 Капілярний метод діагностування
Капілярні методи контролю призначені для виявлення поверхневих дефектів в об'єктах контролю. Вони засновані на капілярному проникненні індикаторних рідин (пенетрантів) в порожнині дефектів матеріалу об'єкта контролю та реєстрації утворюються індикаторних малюнків.
Капілярний метод заснований на штучному підвищенні світло-і кольороконтрастної дефектів щодо неушкодженого ділянки. Методи капілярної дефектоскопії дозволяють виявляти неозброєним оком тонкі поверхневі тріщини та інші несплошності матеріалу, що утворюються при виготовленні та експлуатації різних об'єктів.
4. Діагностика стану електрообладнання електростанцій і підстанцій за допомогою засобів інфрачервоної техніки на практиці
Оцінка фактичного стану силового електрообладнання за результатами діагностичних вимірів – дуже складна і актуальне завдання. Значна частина електричного обладнання станцій, підстанцій, системи передачі і розподілу електроенергії виробила свій ресурс, але продовжує експлуатуватися, оскільки на його заміну потрібні великі фінансові кошти. У зв'язку з цим з кожним роком зростають витрати на проведення комплексних обстежень та діагностики.
В останні десятиліття великого поширення отримують методи контролю параметрів силових трансформаторів під робочою напругою. До методів безперервного контролю і вимірюваним «on-line» параметрам силових трансформаторів, які можуть бути реалізовані в системах моніторингу, можна віднести контроль величини tgδ ізоляції вводів; вимірювання температури верхніх шарів масла, струму навантаження, напруги з ПІН вводів, тиску масла у введенні, вологовмісту масла, вмісту розчинених у маслі газів за допомогою спеціальних датчиків; вимір рівня ві Брацило з метою оцінки стану запресовування обмоток, стану муздрамтеатру, системи охолодження; моніторинг рівня часткових розрядів (ЧР) в ізоляції вводів і обмоток та ін. Перераховані вище методи мають різну ступінь достовірності та інформативності.
Метод тепловізійного контролю за допомогою засобів інфрачервоної діагностики та хроматографический аналіз газів, розчинених у трансформаторному маслі (ХАРГ), що виконуються у відповідності з керівними документами «Обсяг і норми випробувань електроустаткування» (ОНІЕ), дозволяють виявити цілий ряд різних дефектів високовольтного електроустаткування (ЕО). Про тепловидения і його застосуванні для контролю стану електрообладнання відомо кілька десятків років [11,12]. Тепловізійний контроль є одним з основних напрямків розвитку високоефективної системи технічної діагностики, яка забезпечує можливість контролю теплового стану обладнання та споруд без виведення їх з роботи, виявлення дефектів на ранній стадії розвитку, скорочення витрат на технічне обстеження за рахунок прогнозування термінів і обсягу ремонтних робіт [13]. Тепловізійний контроль проводиться для з'ясування теплового стану роз'єднувачів, трансформаторів струму (ТС) і напруги (ТН), розрядників і обмежувачів перенапруги (ОПН), конденсаторів зв'язку, масляних і повітряних вимикачів, ошиновки розподільних пристроїв (РУ), якості пайки обмоток статора турбогенераторів при ремонтних роботах, високовольтних вводів силових трансформаторів, систем охолодження трансформаторів, електродвигунів, генераторів тощо. Ведеться також контроль стану димових труб і газоходів на теплових електростанціях, виявлення місць присосов холодного повітря і т.д. В енергосистемі «Самараенерго» тепловізійний контроль проводився за допомогою засобів інфрачервоної техніки типу «INFRAMETRIKS-740» і «ІРТІС». В [13] торкнулися питання застосування тепловізійних приймачів для виявлення дефектних пайок з'єднувальних голівок стрижнів обмотки статора турбогенераторів (ТГ) в процесі експлуатації. В даному розділі розглянуті питання використання тепловізійних приймачів як засоби контролю якості пайки з'єднувальних голівок стрижнів статорних обмоток ТГ із застосуванням твердих припоїв при їх ремонтах. Тепловізійний контроль проводиться при відкритих лобових частинах обмотки статора з виведеним ротором і попереднім нагріванням від джерела постійного струму (наприклад, резервного збудника) струмом величиною порядку 1000 А. При цьому, необхідною умовою ефективності обстеження головок стрижнів обмотки статора є наявність перевищення температури обмотки генератора над температурою довкілля турбінного цеху.
Слід зазначити наступний важливий момент: для забезпечення можливості зіставлення результатів вимірювань величини надлишкової температури T, виконаних на ТГ різних типів і потужностей, необхідно виконання вимоги щодо забезпечення однакової щільності струму в прогрівається обмотці. Однак у розглянутих у статті випадках ремонту ТГ цей параметр не контролювався. При подальших ремонтах ТГ це передбачається робити. Крім тепловізійного контролю, існує і застосовується для контролю пайок гідрогенераторів (сотні головок) струмовихровий метод, але в даній статті він не розглядається.
Максимальна відміну величини опору постійному струму між гілками обмотки статора ТГ не повинно перевищувати 5%, а відхилення від паспортного значення не більше 2% [11]. Турбогенератор ТГ-6 Тольяттінськой ТЕЦ типу ТВФ-60-2, (рік випуску 1967, капремонт з повною перемоткою обмоток 1991) перебував у тривалому резерві. Результати вимірювання опору постійному струму обмоток статора показали, що максимальне відміну ΔRmax междуветвямі склало 6,8% (між гілками А1 і А2 фази А). Таким чином, ΔRmax між гілками А1 і А2 фази А перевищував допустимий ОНІЕ рівень в 5%. Тепловізійне обстеження лобових частин обмотки статора 17.03.2000 р показало підвищений нагрів місць пайок в семи точках з надмірною температурою ΔT в діапазоні від 4,1 до 6,6°С в порівнянні з сусідніми «холодними» (реперними) точками (рис. 1, 2). Із семи точок дві точки припадають на гілку А2 фази А, яка має підвищений омічний опір ΔRmax = 6,8% (між гілками) (рис. 1).
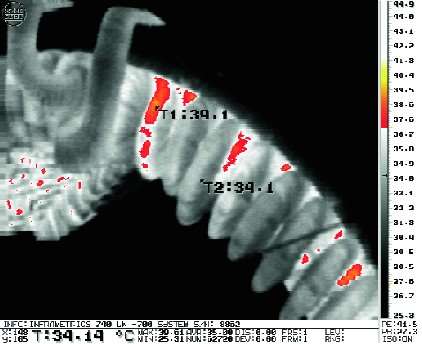
Рисунок 1 – Термограма 17.03.2000 р. Генератора 6 ГТ Те ТЕЦ. Вид з боку збудника в районі 1-ї години (до 1-й перепайки), ΔT = 5°С (ΔRmax = 6,8% між гілками А1 і А2 фази А)
На підставі цих результатів проведена перепайка стрижнів гілки А2 фази А обмотки статора ТГ в точках, зазначених на рис. 1 і 2. ΔRmax між гілками А1 і А2 фази А склало 5,07%. Після 1-й перепайки відзначено зниження омічного опоруΔR на фазі А на 1,8%. ΔRmax між гілками А1 і А2 фази А раніше перевищував допустимий ОНІЕ рівень в 5%.
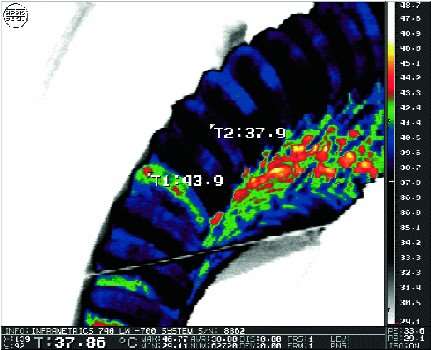
Рисунок 2 – Термограма 17.03.2000 р. Генератора 6 ГТ Те ТЕЦ. Вид з боку турбіни в районі 11-ти годин (до 1-й перепайки), ΔT = 6 оС (ΔRmax = 6,8% між гілками А1 і А2 фази А)
Повторне тепловізійне обстеження 30.03.2000 р. показало підвищений нагрів двох головок в гілці А2, що має максимальне відхилення ΔRmax. Надлишкова температура ΔT в районі цих двох точок склала від 5 до 7,6°С (рис. 3, 4). Тобто, було виявлено, що тепловий стан головки гілки А2 на рис. 3 (до 1-й пайки на рис. 1), а відповідно і якість її пайки, погіршився.
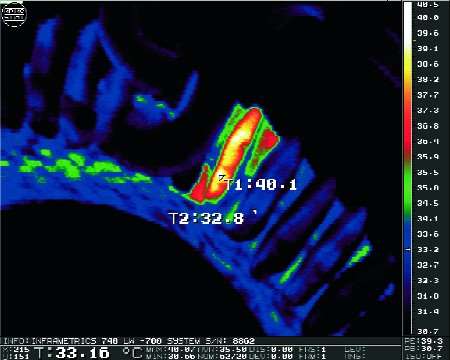
Рисунок 3 – Термограма 30.03.2000 р. Генератора 6 ГТ Те ТЕЦ. Вид з боку збудника в районі 1-ї години (після 1-й перепайки), ΔT = 7,6°С (ΔRmax = 5,07% між гілками А1 і А2 фази А)
Тому 3.04.2000 р. проведена перепайка двох з'єднувальних головок в гілці А2 фази А (див. Рис. 3, 4). Виявлений дефект пайки головки гілки А2 (див. Рис. 3). Далі ΔRmax між гілками А1 і А2 зменшилася і склала 4,4%, що відповідає допустимим нормам по ОНІЕ [11].
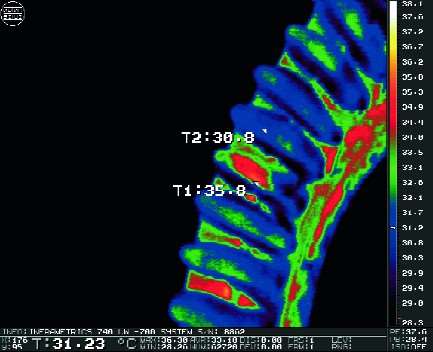
Рисунок 4 – Термограма 30.03.2000 р. Генератора 6 ГТ Те ТЕЦ. Вид з боку турбіни в районі 10-ти годин (після 1-й перепайки), ΔT = 5°С ( ΔRmax = 5,07% між гілками А1 і А2 фази А)
Турбогенератор ТГ-4 ТЕЦ ВАЗ типу ТВФ-120-2 (рік випуску 1970) відключився від мережі дією поперечної диференціальної захисту генератора. Причиною спрацювання захисту стало порушення пайки сполучної голівки гілки С2 фази С обмотки статора (обрив гілки). Попереднє вимірювання опору постійному струму обмоток статора показало, що максимальне відміну ΔRmax між гілками становить 3,49%. Максимальне відхилення від заводських даних становило 2,2% на гілки С2. Після перепайки обмотки статора 3.03.2000 р було проведено тепловізійне обстеження стану якості пайок головок стрижнів обмотки статора. Результати вимірювань вказали на підвищений нагрів місць пайок на гілки С2 в точках зΔT в діапазоні від 3,6 до 3,9°С (рис. 5, 6). Після перепайки максимальне відмінуΔRmax між гілками склало 3,1%, від заводських даних – 1,8% на гілки С1, що відповідає допустимим нормам по ОНІЕ [11]. За результатами тепловізійного обстеження ТГ6 ТоТЕЦ, ТГ-4 ТЕЦ ВАЗ і ТГ-2 Сизранський ТЕЦ була побудована залежність максимального відмінності по опору постійному струму обмоток статораΔRmax (між гілками у%) від величини надлишкової температуриΔT (рис. 7) . На рис. 7 виділена також порогова межа в 5% для відхиленняΔRmax по ОНІЕ. Розгляд цієї залежностіΔRmax відΔT дозволило зробити висновок про величину порогового значенняΔT = 4-5°С, при перевищенні якого можлива наявність дефекту в пайку сполучних головок стрижнів обмотки статора турбогенераторів (ТГ) в процесі експлуатаціі.Однако цей графік носить приблизний характер і потребує подальшого уточнення в міру нагромадження досвіду тепловізійного контролю та статистичних даних вимірювань. Пороговий критерійΔT = 4-5°С не є остаточним і буде уточнюватися.
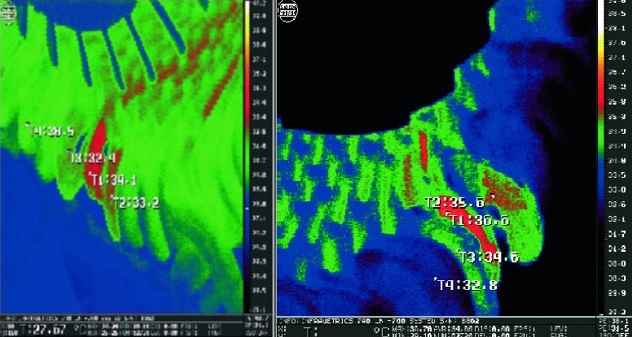
Рисунок 5, 6 – Термограми 3.03.2000 р. генератора ТГ-4 ТЕЦ ВАЗа. Лобова частина з боку збудника T = 3,6-3,9°С (ΔRmax = 3,1% між гілками)
Турбогенератор ТГ2-25-2 Сизранський ТЕЦ (рік випуску 1956) обстежувався під час капітального ремонту за допомогою тепловізійного контролю при відкритих лобових частинах обмотки статора з виведеним ротором і попереднім нагріванням від резервного збудника постійним струмом величиною порядку 600 А. У ході капітального ремонту проводилася повна перемотування обмотки статора турбогенератора; перепайка дефектних з'єднувальних голівок стрижнів проводилася з використанням цирконієвого припою марки ПМФОЦр 6-4-0,03.
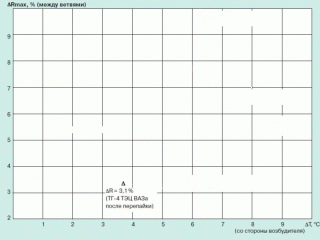
Рисунок 7 – Залежність максимального відмінності по опору постійному струму обмоток статора ΔRmax (між гілками, у%) від величини надлишкової температури T (у порівнянні з сусідніми «холодними» (реперними) точками. Вид з боку збудника, ТГ ТЕЦ ВАЗа, ТоТЕЦ, СТЕЦ)(анімація: 6 кадрів, 8 циклів повторення, 351 кілобайт)
При первинному тепловізійному обстеженні 27.10.2004 р. на термограмме з боку збудника виявлено перевищення температури дефектних головок стрижнів (точки №№ 1-7, 10) над температурою сусідніх "холодних" точок ΔT = від 3,1°С до 6,2°С при різниці величини омічного опору ΔRmax = 15% між фазами, що значно перевищує норму, зазначену в ОНІЕ (рис. 8). Після серії послідовних перепайок дефектних головок стрижнів обмотки статора турбогенератора 27.10, 28.10 і 29.10.2004 р. різниця величин провідникові ΔRоміч. між фазами знизилася спочатку з ΔRmax = 15% до 7,6%, а потім до 4,2%.
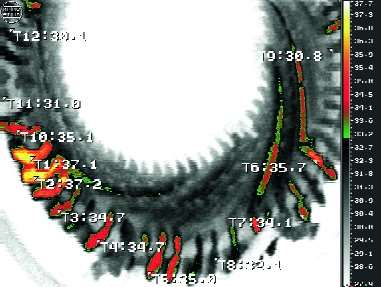
Рисунок 8 – Термограма 27.10.2004 р. турбогенератора типу ТГ2-25-2 Сизранський ТЕЦ, рік випуску 1956. Вид з боку збудника, дефектні пайки головок стрижнів – точки № 1, № 2, № 3, № 4, № 5, №6, № 7, №10 (ΔT від 3,1°С до 6,2°С, ΔRоміч. = 15%)
Електрична схема розташування фаз в обмотці статора турбогенератора (вид з боку збудника) показана на рис. 9.
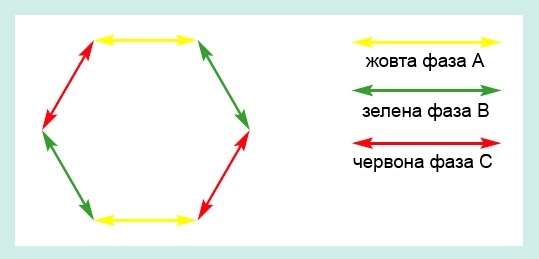
Рисунок 9 – Розташування фаз в обмотці статора
Тепловізійне обстеження 29.10.2004 р після чергової перепайки показало, що на термограмме, вид з боку збудника, кількість дефектних пайок головок стрижнів зменшилася з 8 до 2 – точки № 1, № 5 і ΔT склала від 3,3°С до 5,5°С при ΔRоміч. = 3,2% (рис. 10). Це демонструє ефективність застосування тепловізійного контролю якості пайки з'єднувальних голівок стрижнів статорних обмоток турбогенераторів як інструмент послідовної оцінки якості пайок [14-16].
Теплобачення дозволяє виявляти аварійні дефекти технічного електрообладнання (ЕО) підстанцій з сильному нагріванні і значними перепадами температур у порівнянні з температурою навколишнього середовища (максимальна в даній статті ΔT = 116°С). Крім аварійних, в ході тепловізійного обстеження виявляються нагріви болтових з'єднань шинних і лінійних роз'єднувачів, які можуть усуватися по мірі можливості відключень.
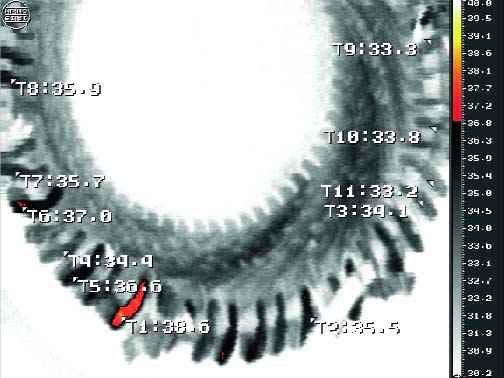
Рисунок 10 – Термограмма 29.10.04 г. турбогенератора типа ТГ2-25-2 Сызранской ТЭЦ, год выпуска 1956. Вид со стороны возбудителя, дефектные пайки головок стержней – точки № 1, № 5 (ΔT от 3,3°С до 5,5°С, ΔRомич.= 3,2 %)
На рис. 11 представлена термограмма опорного ізолятора роз'єднувача 110 кВ підстанції «Новоспаська-1». Можлива причина нагріву – зволоження внутрішньої поверхні порцеляни, збільшення струму витоку по внутрішній поверхні (ΔT = 1,4°С). На рис. 12 – нагрів болтового з'єднання апаратного затиску роз'єднувача 220 кВ у бік лінії «Просвіт-2» підстанція «Томиловская» (губки ножа роз'єднувача, фаза «В» (ΔT = 48°С)). На рис. 13 – нагрів болтового з'єднання гнучкого зв'язку шинного роз'єднувача 110 кВ в сторону масляного вимикача підстанції «Чапаєвська» (фаза «С» (ΔT = 116°С)).
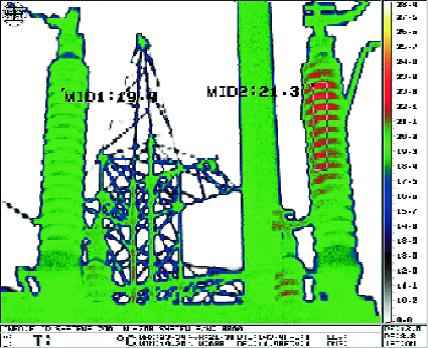
Рисунок 11 – Опорний ізолятор роз'єднувача ШР-110 кВ підстанції «Новоспаська-1» в сторону ЛР. Фаза «А». Імовірно зволоження внутрішньої поверхні порцеляни, збільшення струму витоку по внутрішній поверхні (ΔT = 1,4°С)
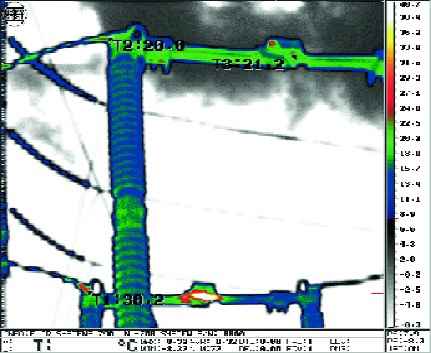
Рисунок 12 – ЛР-220 кВ лінії «Просвіт-2» підстанція «Томиловская». Нагрівання болтового з'єднання апаратного затиску роз'єднувача в сторону ЛЕП. Губки ножа роз'єднувача, фаза «В» (ΔT = 48°С)
Дефекти болтових з'єднань роз'єднувачів не єдині виявляються тепловізорами. Можливо також виявлення локальних нагревов на стінках бака високовольтного маслонаповненого ЕО, пов'язаних з дефектами обмоток вбудованих ТТ або поганими контактами всередині масляного вимикача, які приховані товщею масла і важко піддаються інтерпретації. На рис. 14 добре видно нагрів фази «А» вбудованого трансформатора струму 110 кВ (ΔT = 5,1°С) підстанція «ЗІМ 110/35/6 кВ». Імовірно можливі дві причини: раскорачіваніе вторинних затискачів ТТ або виткове замикання в обмотці ТТ. На рис. 15 зображений локальний нагрів на стінці бака масляного вимикача ВМ-35 кВ «Т1Т» типу МКП-35 підстанції «М. Ішуткіна 35/10 кВ », фаза« А »(ΔT = 3,7°С), який може бути пов'язаний з поганим контактом в гнучкого зв'язку до струмоведучих стрижня або в контактній групі (розетка дугогасного пристрої) [14-16].
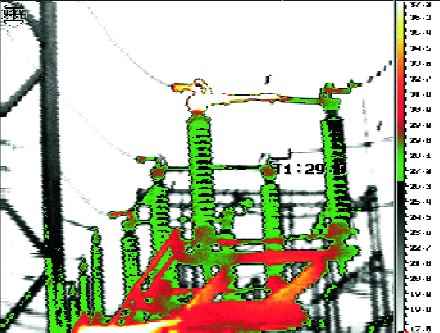
Рисунок 13 – ШР-1-110 кВ лінії «Громадянська» підстанції «Чапаєвська». Нагрівання болтового з'єднання гнучкого зв'язку в сторону МВ, фаза «С» (ΔT = 116°С)
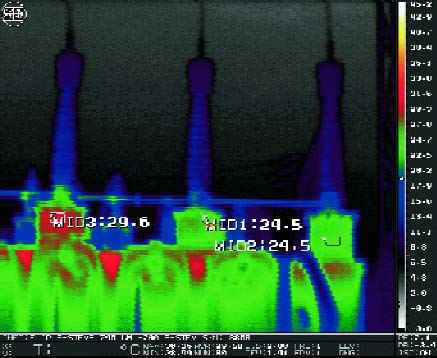
Рисунок 14 – Підстанція «ЗІМ 110/35/6 кВ», трансформатор С1Т. Нагрівання фази «А» вбудованого трансформатора струму 110кВ (ΔT = 5,1°С)
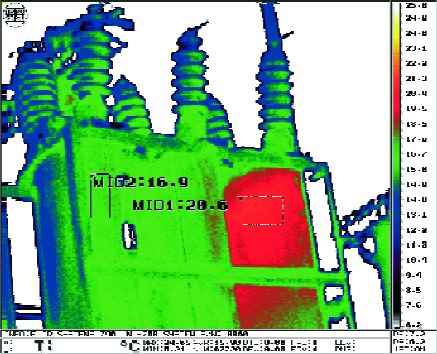
Рисунок 15 – Підстанція «М. Ішуткіна 35/10 кВ »ВМ-35 кВ« Т1Т »типу МКП-35. Локальний нагрів на стінці бака масляного вимикача, фаза «А». (ΔT = 3,7°С)
5. Проблеми технічної діагностики
Загальною проблемою технічної діагностики є досягнення адекватної оцінки розпізнавання істинного стану об'єкта та класифікації цього стану (нормального або аномального).
При проведенні технічного діагностування для підтвердження нормального стану об'єкта виділяють два основні завдання:
- забезпечення отримання достовірної інформації;
- забезпечення прийнятною оперативності отримання інформації.
При проведенні технічного діагностування для виявлення аномалій виділяють дві основні проблеми:
- ймовірність пропуску несправності;
- вірогідність «помилкової тривоги», то є ймовірність помилкового сигналу про наявність несправності.
Чим вища ймовірність «помилкової тривоги», тим менше ймовірність пропуску несправності, і навпаки. Завдання технічної діагностики несправностей полягає в знаходженні «золотої середини» між цими двома проблемами.
Висновки
Діагностика технічного стану електрообладнання може здійснюватися як спеціальними приладами, якими виробляються прямі вимірювання електричних параметрів контрольованих об'єктів традиційними методами, так і приладами для вимірювання непрямих характеристик електрообладнання, наприклад, температури поверхні, на безконтактному вимірюванні який заснований теплової неруйнівний контроль – тепловизионная діагностика. Метод дозволяє здійснювати високопродуктивний безконтактний контроль електрообладнання в процесі роботи без знеструмлення об'єкту і виявляти багато дефекти на ранній стадії їх розвитку, попереджаючи виникнення аварій та надзвичайних ситуацій в системах енергопостачання.
Розроблена методика в даний час успішно застосована при натурних обстеженнях більше 50 об'єктів на практиці.
Тепловізійний контроль став важливим інструментом для обстеження стану різного електротехнічного обладнання енергосистеми: трансформаторів струму і напруги, роз'єднувачів, вентильних розрядників, високовольтних вводів, силових трансформаторів, масляних вимикачів, якості пайки обмоток статора турбогенераторів при ремонтних роботах електродвигунів, димових труб і газоходів та інші.
Проблема забезпечення використовуваними технологіями якості пайки з'єднувальних голівок статорних обмоток ТГ при проведенні ремонтних робіт на сьогоднішній день досить актуальна. Необхідна перевірка якості пайки за допомогою послідовного тепловізійного контролю та вимірювання опору постійному струму обмоток статора ТГ.
Для об'єктивного визначення технічного стану обладнання електротехнічних комплексів пропонується використовувати програмно-інформаційну діагностичну систему, яка дозволяє здійснювати збір та обробку первинної інформації на працюючому електрообладнанні за допомогою сучасних, високоефективних діагностичних засобів, видачу результатів обробки цієї інформації в зручній формі, передачу цієї інформації в архів; звернення до довідково-інформаційний масив; постановку попереднього діагнозу; прийняття рішення про подальші діагностичних операціях. Діагностична система включає переліки контрольованих вузлів різних типів електроустановок, що виявляються дефектів, методи контролю та параметри, що характеризують експлуатаційний стан. Враховано метрологічна забезпеченість, необхідний рівень автоматизації і сумісність засобів вимірювання з ПЕОМ, зручність і наочність вихідної інформації.
Діагностична система показала високу ефективність при вирішенні завдань раннього виявлення дефектів високовольтного обладнання; прогнозування розвитку дефектів, оцінки їх небезпеки; визначення обсягу ремонтно-відновлювальних робіт; оптимізації ремонтно-технічного обслуговування обладнання.
*При написанні даного реферату магістерська робота ще не завершена. Повний текст роботи і матеріали по темі можуть бути отримані у автора або його керівника в січні 2016 року.
Перелік джерел
- Косолапов А.Б. Система технической диагностики электротехнических комплексов // Успехи современного естествознания. – 2005. – № 2
- Алексеев Б.Л. Контроль состояния крупных силовых трансформаторов. – М.: Издательство НЦ ЭНАС, 2002. – 216с.
- Назарычев А.Н. Основные принципы системы технического обслуживания и ремонта электрооборудования по техническому состоянию // Надежность либерализованых систем энергетики / Под ред. Н.И. Воропая, А.Д. Тевяшева. – Новосибирск: Наука, 2004. – с.173-189.
- Структура экспертно-диагностической и информационной системы оценки состояния высоковольтного оборудования /Давиденко И.В., Голубев В.П., Комаров В.И., Осотов В.Н. // Электрические станции. 1997. №6. – с.25-27.
- Ротштейн А.П. Медицинская диагностика на нечеткой логике. – Винница: Континент-ПРИМ, 1996. – 132с.
- Пархоменко П. П. О технической диагностике. М: Знание, 1969 – 90 с.
- Приборы и системы для измерения вибрации шума и удара. Справ. в 2 кн. под ред. В.В. Клюева. М: машиностроение, 1978 – 844 с.
- Вибрации в технике. Т. 5. Ред. совет: В. Н. Челомей и др. М: Машиностроение, 1981 – 496 с.
- Технические средства диагностирования: Справочник / В.В.Клюев, П.П.Пархоменко, В.Е.Абрамчук и др.; под общ. Ред. В.В.Клюева. – М.: Машиностроение, 1989. – 672 с.
- Костюков А. В., Костюков В. Н. Повышение операционной эффективности предприятий на основе мониторинга в реальном времени. – М.: Машиностроение, 2009. – 192 с.
- Обьeм и нормы испытаний электрооборудования РД 34.45-51.300 – 97 с.
- Поляков В.С. Применение тепловизионных приемников для выявления дефектов высоковольтного оборудования. – Л.: 1990.
- Бажанов С.А. Инфракрасная диагностика электрооборудования распределительных устройств. ИТФ
Энергопрогресс
, Приложение к журналуЭнергетик
. – М.: 2000. - Григорьев А.В., Осотов В.Н. О совершенствовании и расширении методов контроля теплового состояния турбогенераторов. – Электpические станции, 1999, № 11.
- Хренников А.Ю., Еганов А.Ф., Смолин А.Ю., Щербаков В.В., Языков С.А. Тепловизионный контроль генераторов и импульсное дефектографирование силовых трансформаторов. – Электрические станции, № 8, 2001.
- Хренников А.Ю., Петров А.С., Цыгикало Г.В., ЩербаковтВ.В., Языков С.А. Cистемы мониторинга и опыт диагностики состояния электротехнического оборудования в ОАО
САМАРАЭНЕРГО
. – ЭЛЕКТРО. Электротехника, электроэнергетика.