Abstract
Сontent
- Introduction
- 1. Theme urgency
- 2. Goal and tasks of the research
- 3. Review of research and developments
- 3.1 Decrease in emissions in coal preparation department
- 3.2 Decrease in emissions at batch coke of ovens
- 3.3 Decrease in emissions at the coke drawing
- 3.4 Decrease in emissions at the coke quenching
- Conclusion
- References
Introduction
Today on modern coke-chemical plant take root new advanced without waste the technics allowing not only to raise quality of fabricated coke, but also to lower consumption of not renewed natural resources (coal, natural gas) to lower formation of emissions, dumps and a waste on a runout. However in Ukraine almost all equipment of the operations coke-chemical plant is physically obsolete, it is bundled first of all by that to Ukraine there are no big financial investments on reconstruction of production plants. And as consequence of the operation do not presume to fix to itself more modern of the equipment for opening-up of coal mix material, manufacture of more quality coke, its refrigeration, and also highly effective treatment facilities for scrubbing action of the polluted waste gases, and neutralisation of a waste.
Toughening of ecological requirements to coke-chemical to the operations, the basic units and the equipment, began to demand from coke-chemists efforts for reconstruction and technical re-equipment of the operations under the decision of questions of protection of the air and water environment.
1. Theme urgency
The operations the coke-chemical industries are one of the basic sources of receipt of polluting substances in environment (OS). Now in Ukraine functions 13 coke-chemical plants, 7 from which are concentrated in Donetsk area. Environmental problems are aggravated also with that these operations are located in regions with considerable concentration of industrial production and a dense population. The extremely adverse ecological conditions which have been stacked last years in the large metallurgical centres, in certain degree are caused by low rates of modernisation coke-chemical industries, slow introduction in practice of new master schedules, modern units and the equipment.
Coke-chemical plants take a leading place on emissions of harmful substances among the iron and steel industry operations. To them carry a dust, nitrogen oxides, a sulphur dioxide, carbon oxide, ammonia, phenol, benzene, naphthalene, hydrogen sulphide, cyanic hydrogen and graphite. Therefore the major social problem facing to the coke-chemical operations, increase of ecological safety of manufacture, technical re-equipment the coke-chemical operations, realisation of the large-scale program of building of nature protection objects, introduction of modern ecologically safe master schedules is.
On modern production plants introduce the high technologies, allowing to lower emissions of polluting substances in atmosphere. To the cores from them carry machine for smokeless charging of coke ovens with coal charge, machine for unloading coke from coke ovens. However, recently the increasing urgency is got by perfection of master schedules at all stages of manufacture of coke (opening-up, batch, coking of coals, distribution, refrigeration and coke sorting). To these stages of manufacture of coke belongs now more than 70 % emissions.
2. Goal and tasks of the research
The goal is working out and introduction of rational "know-how" of the coke, allowing to raise quality of coke and simultaneously to reduce harmful emissions.
Main tasks of the research:
- To study основне environmental contamination sources at all production phases of coke;
- To study modern domestic and foreign "know-how" of coke: opening-ups of coal mix material, its batch in коксовую the oven, process cokings, an unloading of coke from coke’s ovens and it’s refrigeration;
- To consider possible ways of decrease in emissions of polluting substances at all production phases of coke;
- To give the characteristic to the factors, influencing the basic characteristics of metallurgical coke, and to develop offers on improvement of quality of coke;
- Search of optimum ways of perfection of master schedules of manufacture of coke;
- To Calculate economic and ecological effect from introduction of technics reducing harmful emissions and raising quality of coke.
Object of exploration: : Makeevskiy coke-chemical plant PJSC «MAKIYIVCOKE»
Object of research : master schedules of opening-up of coal mix material, its batch in the coke oven, process cokings, an unloading of coke from coke ovens and its refrigeration.
3. eview of research and developments
Presently on cokers next classification of coke workshops is used in an ecological relation:
- Industrial departments where no events are on defence of atmospheric air.
- Industrial departments where there is a batch without dust of coal mix material, scrubbing action of heating gas from hydrogen sulphide to the residual contents 3,0 g/m3 and a biochemical effluent treatment before their use on a coke quenching;
- Industrial departments where besides the actions specified in item 2 there is an machine for without dust coke drawings.
3.1 Decrease in emissions in coal preparation department
In coal preparation departments from the coals intended for coking, coal mix material of the set quality prepares. Thus according to a flow diagramme following operations are carried out: reception, unloading and storing of coals, dispensing, crushing, separation and melting pot mix materials. All these operations, and also transportation of coals and mix material are accompanied by stressing in the finely pulverised coal air which quantity depends on humidity of coal.
Radical action for decrease in emissions at storing of coals is the construction of the folded store room with effective vacuum cleaner systems and dust collections: the Dust content of air of a working zone can be reduced by following actions: hermetic sealing dust the equipment; constructions the vacuum cleaner systems intended for disposal of dusty air; systems with the effective dust removal equipment; the forced ventilation device; blocking of the process equipment with constructions the vacuum cleaner systems; regular cleaning of premises and the equipment from the settled dust; the regular control over a condition of air of industrial premises. One of the factors influencing a dust content of air of industrial premises, cleaning of the settled dust from surfaces of floors, walls and the equipment is. On coke-chemical plant the greatest spreading was received by wet cleaning that is caused by explosive properties of finely pulverised coal. However experience of a dry dust collection on a number of the operations shows that basically it is possible to fabricate and dry cleaning. In this case it is expedient to use centralised constructions the vacuum cleaner systems with water ring vacuum pumps. It will allow to get rid from vodno - a refuse pumping system, to simplify system operation, but will demand the device of the branched out network of communications, air scrubbing action before a venting and decisions of questions of recycling of the caught dry dust.
Till now in the basic way of catching of finely pulverised coal remains wet. In this connection at the operations centrifugal scrubbers, cyclones with a water film are most extended; in some cases the original designs developed by the operations are applied. The dry collectors used as the first step of scrubbing action, in most cases equip with devices for giving and water dispersion. Efficiency of catching of finely pulverised coal in wet devices is rather various that is bundled, apparently, as to density of an irrigation and quality of dispersion of a liquid, and with dispersion of caught particles. Necessity of the complex decision of nature protection problems causes perspectivity of dry methods at a dedusting of gases and air. It confirms long-term operating experience of dry dust traps on a number of the operations (Open Society "Severstal", joint-stock company "Ispat-Karmet", Open Society «Magnitogorsk metallurgical industrial complex»). In particular, cyclones are successfully maintained on the Gubahinsky production plant more than 25 years for a dedusting constructions the vacuum cleaner air at opening-up and coal upgrading. Scrubbing action degree makes 70-84 % that at an actual initial dust content <200 mg/m3 are quite enough for achievement of a sanitary code on a venting. In cyclones in diameter of 4000 mm after slime concentrate dryers in joint-stock company «Western-Siberian metallurgical industrial complex» scrubbing action degree reaches on the average 88,5 % at fluctuations of an initial dust content from 10 to 130 g/m3 and the expense of refined gases from 43,2 to 61,3 thousand m3/h.
It is necessary to carry application of electrofilters to perspective methods. As it is known, in the coal industry and on thermal power stations electrofilters UVP (coal, vertical, lamellar) are widely applied. Recently instead of these electrofilters devices UVV (unified, vertical, explosion-proof) are tapped. Electrofilters UVV are intended for catching of finely pulverised coal with concentration to 60 g/m3 at temperature of gas to 130 °С.
Application of such rather expensive devices as electrofilters, it is economically justified at the big scales of scrubbing action. Blanket productivity of enough bulky installation ~ 1500 thousand m3/h. At initial concentration coke and agglomeration dust of an order 1,42 g/m3 the residual dust content makes 40-60 mg/m3 (i.e. average degree of scrubbing action ~ 96,5 %).
Comprehensible results are received VUHIN at tests of conic cyclones. Superfluous gas-heat-carrier diluted with air to the contents of oxygen of 3-7 % (volumes.), warmed up to 450-550 °С, subjected cotalitic to scrubbing action from organic bridgings in the fluidized bed reactor, and then directed to a cyclone on scrubbing action from a dust. Catching degree a dust with concentration 4,8-6,9 g/m3 sostavila apprx. 90 %.
In joint-stock company "NLMK" also there is an experience of application of cyclones for a dedusting аспирационного air in the folded store room of coal. Degree of catching of finely pulverised coal in groups of three cyclones in diameter of 1,2 m makes 96,8-97,0 %.
Thus, the most effective technical decisions of a problem of catching of finely pulverised coal - application of highly effective dry cyclones, and at designing of the new operations of the decentralised systems with use of electrofilters.
3.2 Decrease in emissions at batch coke of ovens
At batch of damp coal mix material in the heated oven chamber it is formed ~5 m3 of gases on each ton of the loaded mix material. These gases contain 10-60 g/m3 the weighed particles coal and half-coke dust. In recalculation on 1 т fabricated coke dust stressing at batch of ovens reaches 150-400 g/т, thus the quantity of an allocated dust sharply increases with reduction of humidity of mix material <7 %.
Serious difficulties arise at thermobeneficiated burden batch. For batch of the mix material which have passed thermoopening-up, application of traditional ways batches without dust with an exhaust of gases of batch in collector it is absolutely impossible because of increase in entrainment of a dust in collector and the deterioration of coal pitch bundled to it and a carbon loam. Thermal opening-up of mix material for coking consists in its heating to temperature 150-200 °С for the purpose of decrease in humidity and increase of bulk density. Now use in the basic two methods of heating of mix material: the gas heat-carrier (in dryers of a fluidized bed and in tube driers) and mix material heating by hot lumpy coke (the combined process of thermoopening-up of mix material and a coke dry cooling).
For example, in installation of a heat treatment of mix material on коксовой to the battery №7 joint-stock companies "ZSMK" as the first step of scrubbing action of the heat-carrier after a tube drier it is fixed cyclone with 100 elements in diameter of 229 mm. On the second steps the wet dust collector is used. Bulkiness, unreliability and insufficient efficiency of a multicyclone (degree of scrubbing action of 88 %) demand at following stages of test to add the scheme with a conic cyclone. Settlement degree of scrubbing action of an additional cyclone of 76,5 %, concentration of a dust decreases from 26-47 to 5,1 g/m3 that allows to lower a residual dust content on a venting to 0,15 m3/h.
The combined process of thermal opening-up of mix material and the coke dry cooling, developed VUHIN, has essential advantages both from the point of view of technics and heat recycling, and on the ecological indicators. The essence of this technics (drawing 1) consists in mixing of the crushed damp mix material with the heated lumpy coke with the subsequent compartment to heat up mix materials from the extinguished coke.
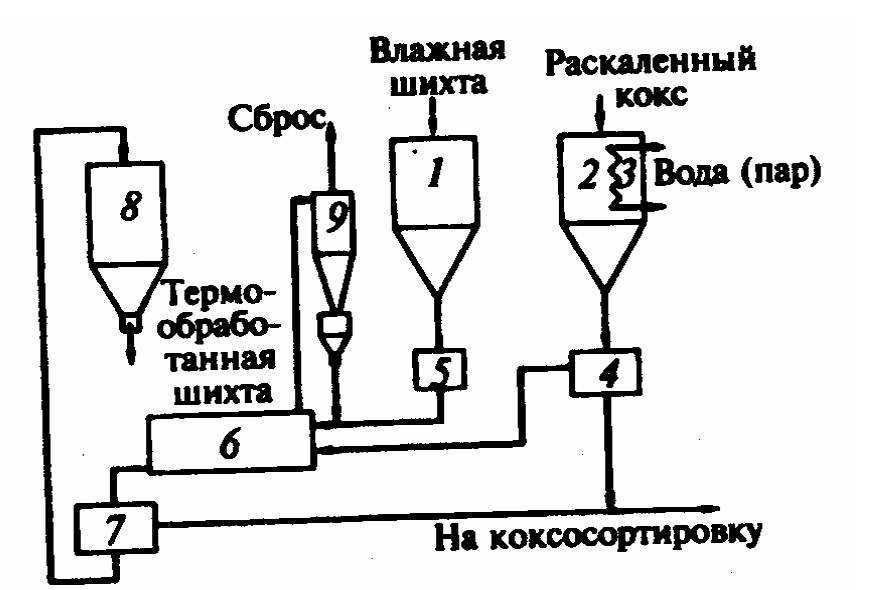
The 1-bunker of initial mix material; the hot coal 2-storage hopper; a 3-recuperator of superfluous heat of coke; 4-rassev a hot coal; the 5-loader of initial mix material; 6-teploobmennyj the device; 7-rassev coal-coke mixes; the 8-storage hopper thermally a beneficiated burden; a finely pulverised coal 9-separator
Drawing 1 - The Scheme of the combined process of thermoopening-up of mix material and a coke quenching
Application of systems of the combined exhaust formed at batch of mix material of gases in collector of coke dust and a stationary exhaust gas pipeline widely practises Japan. Batches without dust of this kind are equipped by systems almost all batteries. Machine for smokeless charging is carried out by an exhaust of a part of dusty gases in collector ovens at the expense of ammoniacal liquor injection in a pouring gate, and other quantity of gases after burning - in the exhaust stationary gas pipeline passing lengthways coke the batteries (drawing 2). Capacity of an injection spraying apparatus an exhaust in collektor almost half of gases formed at batch usually choose so that to provide.
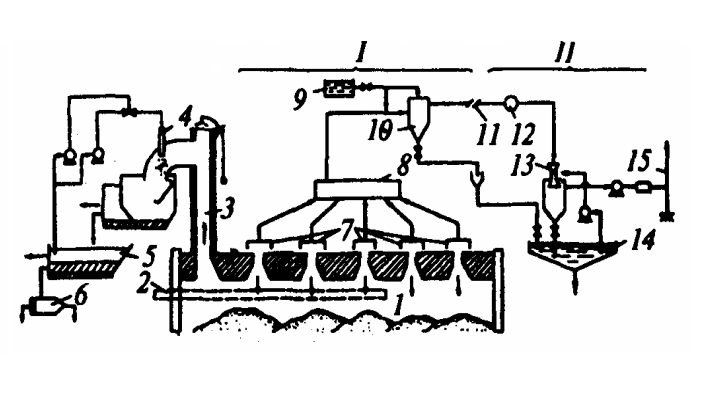
1- the coking chamber; 2-planirnaja a bar; 3-pouring gate; a 4-spraying apparatus for injection Ammoniacal liquor; 5-smolootstojnik; a 6-centrifugal separator; 7-fume hoods; the 8-chamber of burning of dusty gases; 9-capacity with water; 10-pyleosaditel; the 11-connecting valve; a 12-stationary exhaust gas pipeline; a 13-scrubber of Venturi; 14-thickener; a 15-draught stack;
The I-equipment mounted the car of coal-smokeless; the II-equipment, Mounted on the earth
Drawing 2 - System for smokeless charging of coke ovens with coal charge
The Japanese system machine for smokeless charging of coke battery № 1 (60 ovens in height 6,1) on a firm metallurgical plant «LТВ Steel» in Chicago (USA), located in industrial region with high level of pollution of atmosphere, and on коксовой to the battery of a metallurgical plant of firm "Sollak" in Seremanzhe (France). The car of a welded portal design which is mounted on four traction mechanism bogies is applied To mix material batch coal-smokeless. Four storage hoppers of the car are executed from a rust-resisting steel, equipped by feeders and mechanically adjustable measuring gears for the control of level of filling-up. Gases are sucked away in collector batteries by injection in pouring gates of an ammoniacal liquor under the pressure of 4,2 МПа, partially incinerated and through ring space of telescopes and a modular collector on coal-smokeless to the car arrive in the stationary exhaust gas pipeline bridged to system of gas purification. This system is located in the end coke batteries and, a dividing box and an exhaust fan. The system works on a cyclic diagramme, blanket duration of a running cycle of 7 mines 25 with.
Last years for scrubbing action of the gases formed at batch along with wet methods of scrubbing action, receive application fabric filters. The way of a dry cleaning of such gases is applied for the first time in the Netherlands at upgrading c departments №1 on firm "Hoogovens" production plant in Ejmejdene. For maintenance without smoke mix material batches four-bunker углезагрузочная the car with rotating plates is equipped by system of gazo-wires and the devices providing offtake of gases in a stationary exhaust gas pipeline.
On coke-chemical plant of our country mix material load also coal-smokeless cars. The uglezagruzochnyj car with 3 or 4 storage hoppers is fixed over hatches to subject batch of the chamber, final fitting pipes of storage hoppers with the help a body-skopicheskih of devices join loading chutes then mix material expulsion is fabricated. With out smoke batches, as a rule, provide with a way отcoca all gases of batch in collectors. The method of evacuation of gases of batch through pouring gates by means of steam injectors is Most extended. Thus efficiency of an exhaust depends on pressure of steam upon spraying apparatuses (0,7-0,9 МPа).
By the basic lack of a method of steam injection from the point of view are sewn up environment the increase in quantity of an ammoniacal liquor as a result of condensation of steam spent for an exhaust of gases of batch is. In this connection recently primary spreading is received by hydroinjection with use of an ammoniacal liquor of a cycle газосборников. For realisation of this method pressure to 2-3 МПа (drawing 3) and tubings of a high pressure the pump is necessary for water delivery to spraying apparatuses.
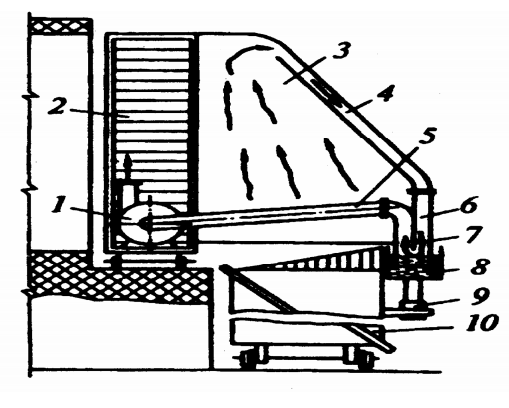
The 1-fan; 3-roof hood; a 4-hot gas duct; a 5-cold gas duct; 6-tee; a 7-partition; 8-capacity with water; the 9-pneumocylinder; 10-tushilnyj the car.
Drawing 3 - Machine for unloading coke from coke ovens
Experience of application of hydroinjection has shown that systems work steadily and at pressure of water> 2 МПа, almost completely providing an exhaust of gases. A lack of this method is necessity of regular cleaning of the pouring gates which elbows grow with adjournment during 7-10 days; at non-observance of the diagramme of cleaning the moulding box of streams owing to what efficiency of injection sharply decreases changes.
3.3 Decrease in emissions at the coke drawing
Struggle against emissions at pushing out of coke from oven chambers - one of most challenges. Over a hot coal getting in the car for coke transportation, there is an intensive ascending current heated air which involves considerable weights of surrounding atmospheric air in movement. As a result there is a painted dust cloud of the considerable sizes in which except a dust can contain and the gaseous harmful substances allocated from coke; the volume of these gases is rather insignificant and usually does not exceed several tens cubic metre.
Formation of a dust cloud at distribution occurs rather quickly, and this unorganized emission can be carried to troop landing. At a coke drawing of insufficient readiness formation of dense clouds dense black or black-green a thought is observed. Such phenomena are observed at incompleteness of process of coking in the centre of coal batch or the non-uniform heating of ovens leading to formation in batch of cold zones.
The greatest recognition was received by systems with the device of roof hoods, an exhaust and scrubbing action of gases of distribution. Thus sucking away and dust removal equipment project both in mobile, and in stationary execution. In practice systems with a mobile roof hood and stationary system of a dust collection more often are used. As dust traps apply scrubbers of Venturi, wet electric precipitation plants, fabric filters. Recently the transition tendency only on dry dust traps, as a rule, bag hoses is abroad observed.
In 1983г. On Kommunarsky coke-chemical plant a production plant the first machine for unloading coke from coke ovens with stationary system of an exhaust and scrubbing action of gases (drawing 4) has been started up. The next years similar installations have been mounted on a number of production plants. Existing tendencies still are based on increase in volume of sucked away gases to 150-180 thousand m3/h with corresponding increase in the sizes and design a roof hood.
Concentration of a dust in gas sucked away from under a roof hood reaches 18-22/m3 Fixing at the first step of scrubbing action of group of cyclones, reach total degree of scrubbing action of 99,1-99,2 % at residual concentration of a dust in gases of distribution 0,11-0,22/m3 Easy to see that having increased volume of sucked away gases, we receive the raised dust content which reduction to demanded norms demands increase of degree of scrubbing action.
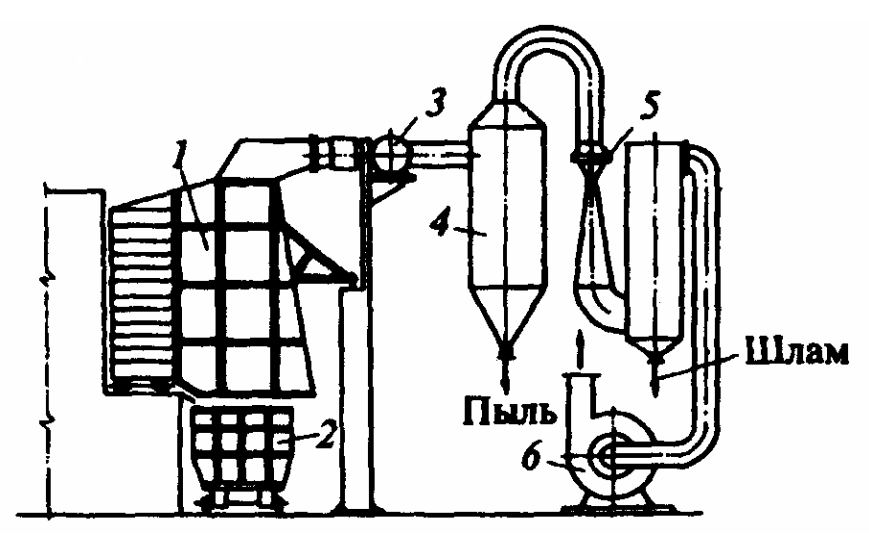
Drawing 4 - The machine for unloading coke from coke oven with stationary system Scrubbing actions
From all systems applied now abroad coke without dust drawings (overlapping over all coke the battery party; an exhaust and scrubbing action of allocated gases in stationary system of scrubbers; dust removal roof hoods over the car for a coke quenching with collector the equipment on the car for a coke quenching or the ramp bridged to it; dust removal roof hoods over directing coke car for a coke quenching with stationary an exhaust gas pipeline and gas purification system) the most effective are recognised systems of last type. In Japan by such systems are equipped practically all coke batteries.
The scheme of one of such systems is shown in drawing 5. The width of a dust removal roof hood is equal to width the car, the length fluctuates from 6 до 10 m depending on coking chamber volume. Capacity of an induced-draught fan in system without dust distribution at 40°С makes 2500-4500 m3/m depending on coking chamber volume. To scrubbing action of gases are applied both wet, and dry methods of scrubbing action.
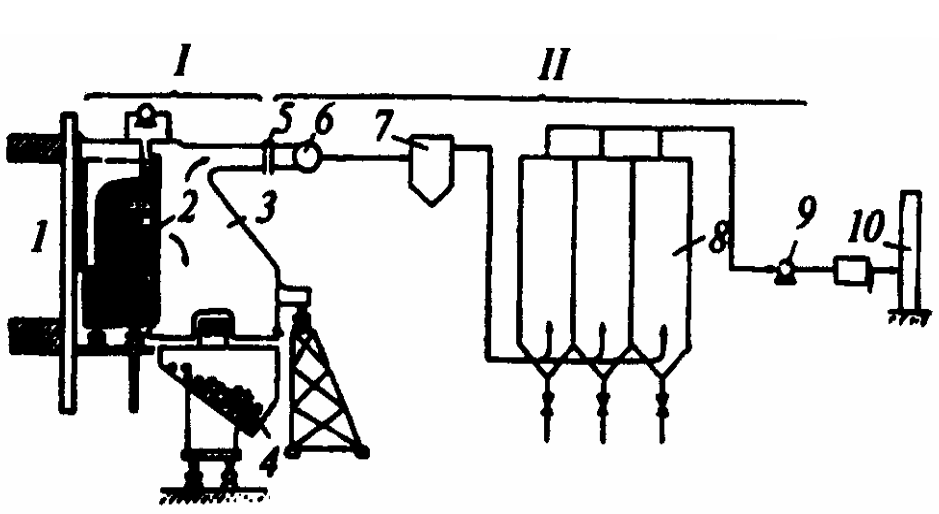
The coking 1-chamber; 2-directing coke; a 3-dust removal roof hood; 4- car for coke acceptance; the 5-connecting valve; the 6-stationary exhaust Gas pipeline; 7-pyleosaditel; a 8-fabric filter; a 9-induced-draught fan; a 10-draught stack;
The I-equipment mounted on directing coke; the II-equipment mounted On the earth
Drawing 5 - System unloading coke from coke oven
The system unloading coke from coke oven of type "Minister Stein" last years is introduced on new coke batteries in Germany, Great Britain, the Netherlands, the USA.
During perfection of the specified system by firm «Hartung, Kun ynd To» razrabo-tana a design new directing coke the car executed as a unit with a dust removal roof hood. Coke drawings in Germany are equipped by such systems all new coke batteries on a number of production plants.
3.4 Decrease in emissions at the coke quenching
Process of a wet quenching of coke in its usual hardware registration is extremely stacked from the point of view of scrubbing action thrown out steam-gas mixes. During 1-2 mines from the coke-quenching station modern coke-chemical plant it is thrown out in atmosphere about 20 thousand m3 of the water steam which volume increases because of air. Use of the polluted water for a coke quenching leads to increase in emissions of harmful substances. So, at use at its finest the quantity of firm particles thrown out in atmosphere makes 0,23-1,13 kg/t of coke, and at application of sewage of coke of 0,68 2,26 kg/t. The specific flue-dust blowout on 1 т coke increases on 0,4 g at increase in the dry rest in circulating water on 0,1 g/h. Shrinking of emissions of firm particles in the course of a wet quenching at usual hardware registration is reached by the device of special entrainment separators or additional circles of dispersion of water through spraying apparatuses.
Introduction of a dry cooling of coke on domestic coke-chemical plant is necessary, first of all it allows to improve quality of coke in the conditions of continuously worsening raw-material base of coking. However in modern execution of a dry coke quenching installation throw out in atmosphere большее quantity of harmful substances, than coke-quenching stations at a coke wet quenching the refined sewage.
However, one of advantages of a way of a dry cooling of coke in the ecological relation is that emissions on these installations carry organised character and can be subjected scrubbing action thanks to what blanket shrinking of specific ventings by coke manufacture is reached.
The temperature of coke after the car of a dry cooling of coke reaches 150-200 °С. At transportation, overburdenings, a screen separation of such coke occurs intensive dust, therefore the process equipment stock air with installations. Appointment vacuum cleaner systems - creation of favorable working conditions under the contents of harmful substances in air of industrial premises by prevention from process equipment thinnesses. Aspiratsionnye systems have according to flow diagramme car of a dry cooling of coke and dry-quenched coke sortings (drawing 6).
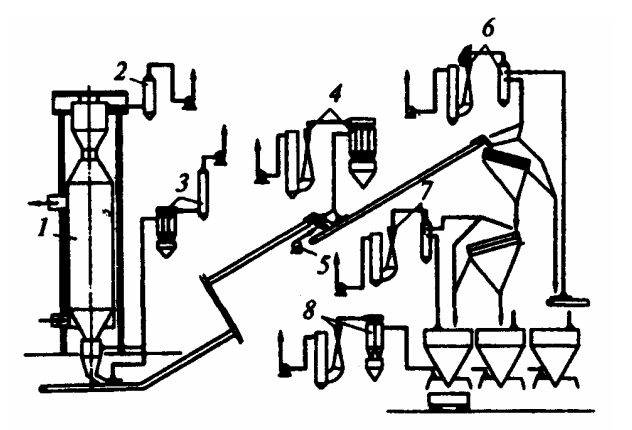
1-chamber USTK; 2 with. Knot of batch USTK; 3 - Knot of unloading USTK; 4 - Reloading knot; 5-dutevoj the fan of station of a dedusting of coke; 6 -. A rotating grizzly; 7- An inertial roar; 8 - Knot of loading of coke in cars
Drawing 6 - The scheme vacuum cleaner systems of car of a dry cooling of coke and coke-screening stations
In makeup vacuum cleaner systems plug dry and wet dust collectors. At an unloading of hot coke from chambers USTK a lot of dust is allocated, therefore usually apply the two-level scheme of scrubbing action. As the first degree use groups of cyclones of type ZN-15, having high enough dust-catching efficiency (87-97 %) at moderated hydraulic a clod resistance (0,35-1,15 кПа). At the second step of a dust collection fix scrubbers TSS-VTI. Actual degree of a dust recovery in them - from 60 to 90 % also is defined in grounds by the expense of an irrigating liquid and quality dispersion.
Conclusion
Preminenie systems without dust batches of coal mix material in a coking chamber and installations without dust coke drawings allows to lower ventings on 90 %.
Priminenie dry coke quenching installations provides:
- To lower expenses for manufacture of coke from 143 927 thousand grn/year to 143 755 thousand grn/year;
- In a consequence decrease in ventings ecological deductions will shrink in 3,5 times;
- The effect from use of steam of installation makes 26 million grn/year;
- The effect of manufacture of the electric power makes 11,4 million grn/year;
- The project time of recovery of outlay (considering payments under the credit with the rate in 25 %) makes 2,3 years
References
- БольшинаЕ.П. Экология металлургического производства: Курс лекций. – Новотроицк: НФ НИТУ «МИСиС», 2012. – 155 с.
- Кауфман А.А., Харлампович Г.Д. Технология коксохимического производства: Учебное пособие. – Екатерингбург: ВУХИН-НКА, 2005. – 288 с.
- Кауфман А.А. Мастер коксового производства. – Екатеринбург: ВУХИН, 2002. – 228 с.
- Иванов Е.Б. Технология производства кокса / Е.Б. Иванов, Д.А. Мучник. – Издательское объединение «Вища школа», 1976. – 232 с.
- Мищенко И.М. Черная металургия и охрана окружающей среды: учебное пособие. – Донецк: ГВУЗ «ДонНТУ», 2013. – 452 с.
- Успенский С. К. и др. Совершенствование технического уровня и повышение эффективности установок сухого тушения кокса // Кокс и химия. 1988, с. 38 – 41.
- Родькин С. П. и др. Комплексная оценка эффективности сухого тушения кокса // Кокс и химия. 1988. № 4, с. 48 – 51.
- Кокс. Коксохимическое производство [Электронный ресурс]. – Режим доступа: http://www.metaljournal.com.ua/coke.
- Сухоруков В.И. Научные основы совершенствования техники и технологи производства кокса. – Екатеринбург: ВУХИН-НКА, 1999. – 393 с.
- Пыриков А.Н. Защита окружающей среды на коксохимических предприятиях / А.Н. Пыриков, С.К. Васнин, Б.Н. Баранбаев. – М.: Интермет – инжиниринг, 2000. – 176 с.
- Родионов А.И. Техника защиты окружающей среды / А.И. Родионов, Н.С. Торочешников. – М.: Химия, 1989. – 325 с.
- Лейбович Р.Е. Технология коксохимических производств / Р.Е. Лейбович, Я.М.Обуховский, С.Я. Сатановский, П.М. Кутовой. – М.: Металлургия, 1974. – 420 с.
- Браун Н.В., Глущенко И.М. Перспективные направления развития коксохимического производства. – М.: Металлургия, 1989 г. – 272 с.
- Рудыка В.И. Коксовая батарея с печными камерами объемом 51 м3 и боковым подводом смешанного газа / В.И. Рудыка, Н.Ю. Чеботарев, О.Н. Суренский, В.В. Деревич // Кокс и химия, - 2009. - № 7. – С. 25-27.
- Власов Г.О. Системный анализ коксохимического производства / Г.О. Власов, В.И. Саранчук, В.М. Чуищєв, В.В. Ошовський. – Д.: ДонГТУ «Східний видавничий дім», 2002. – 296 с.
- Ярошенко Ю.Г. Энергоэффективные и ресурсосберегающие технологи черной металлургии: учебное пособие / Ю.Г. Ярошенко, Я.М. Гордон, И.Ю. Ходоровская. Под ред. Ю.Г. Ярошенко. – Екатеринбург: ООО «УИПЦ», 2012. – 670 с.
- Зингерман Ю.Е. Внедрение установки беспылевой выдачи кокса / Ю.Е. Зингерман, В.Б. Каменюка, Т.Ф. Трембач // Кокс и химия, – 2004. – № 7. – С. 34
- Лейбович Р.Е. Технология коксохимического производства: Учебник для техникумов, изд. 3-е, доп. и перераб / Р.Е. Лейбович, Е.И. Яковлева. – М.: Металлургия, 1982. – 360 с.
- Зингерман Ю.Е. Внедрение новых технологий и разработок / Ю.Е. Зингерман, В.И. Рудыка, В.В. Кривонос, В.В. Гураль // Кокс и химия. - 2009. – № 9. – С. 51
- Общая схема коксохимического производства [Электронный ресурс]. – Режим доступа: http://opeaulay.ucoz.ru/news/obshhaja....
- Углеподготовительный цех коксохимического производства [Электронный ресурс]. – Режим доступа: http://www.borpak.ru/ugolnaya....
- Зашквара В.Т. Подготовка углей к коксованию / В.Т. Зашквара, А.Г. Дюканов. – М.: Металлургия, 1981. – 260 с.
- Жидко А.С. Совершенствование и оптимизация технологи подготовки углей для коксавания. – Челябинск: Металлургия, 1989. – 189 с.
- Посохов М.Ю. Первая установка избирательного измельчения углей с пневмосепарацией в Китае/ М.Ю. Посохов, В.И. Сухоруков, Чэнь Кай // Кокс и химия, - 2006. - № 7. – С. 5-9.
- Иванов Е.Б. Технология производства кокса / Е.Б. Иванов, Д.А. Мучник. – Издательское объединение «Вища школа», 1976. – 232 с.
- Пыриков А.Н. Защита окружающей среды на коксохимических предприятиях / А.Н. Пыриков, С.К. Васнин, Б.Н. Баранбаев. – М.: Интермет – инжиниринг, 2000. – 176 с.
- Родионов А.И. Техника защиты окружающей среды / А.И. Родионов, Н.С. Торочешников. – М.: Химия, 1989. – 325 с.
- Браун Н.В., Глущенко И.М. Перспективные направления развития коксохимического производства. – М.: Металлургия, 1989 г. – 272 с.
- Рудыка В.И. Коксовая батарея с печными камерами объемом 51 м3 и боковым подводом смешанного газа / В.И. Рудыка, Н.Ю. Чеботарев, О.Н. Суренский, В.В. Деревич // Кокс и химия, - 2009. - № 7. – С. 25-27.
- Власов Г.О. Системный анализ коксохимического производства / Г.О. Власов, В.И. Саранчук, В.М. Чуищєв, В.В. Ошовський. – Д.: ДонГТУ «Східний видавничий дім», 2002. – 296 с.
- Зингерман Ю.Е. Внедрение установки беспылевой выдачи кокса / Ю.Е. Зингерман, В.Б. Каменюка, Т.Ф. Трембач // Кокс и химия, – 2004. – № 7. – С. 34
- Бородин М.В. Энергоресурсы коксохимической промышленности Украины. Направления их использования / М. В. Бородин, В. Ю. Попов, Э. В. Старченко // Кокс и химия – 2000. - № 7 – С. 45 – 47.
- Зингерман Ю.Е. Внедрение новых технологий и разработок / Ю.Е. Зингерман, В.И. Рудыка, В.В. Кривонос, В.В. Гураль // Кокс и химия. - 2009. – № 9. – С. 51
- Газоочистные аппараты и установки в металлургическом производстве. Учебник для вузов/ С.Б. Старк. Изд. 2-е, перераб. и доп. – М.: Металлургия, 1990. –400 с.
- Инженерная защита окружающей среды. Учебное пособие / под ред. Воробьева О.Г. –СПб.: изд. Лань, 2002. –288 с.
- Курс инженерной экологии. Учебник для вузов/ Под ред. Мазура И.И. – М., Высшая школа, 1999. – 447 с.
- Мазур, И.И. Курс инженерной экологии. Учебник для вузов /И.И. Мазур, О.И. Молдаванов / под ред. И.И. Мазура –М.: Высшая школа, 1999. –447 с.
- Воскобойников В.Г. Общая металлургия. Учебник для вузов/В.Г. Воскобойников, В.А. Кудрин, А.М. Якушев. 6-изд., перераб. и доп. – М.: ИКЦ «Академкнига», 2002. –768 с.
- Цветков, Ю.В. О создании экологически чистого энергометаллургического комплекса /Ю.В. Цветков//Экология и промышленность России, № 5, 1999, с.11-15.
- Денисенко, Г.Ф. Охрана окружающей среды в черной металлургии. Учебное пособие / Г.Ф. Денисенко, З.И. Губонина. –М.: Металлургия, 1989. –120 с.