Abstract
Contents
- Introduction
- 1. Topicality
- 2. Research object and purpose of the qualifying work
- 3. Physical and chemical bases of rubber products
- 4. An experimental research methods and their results
- 4.1 Of experimental research methods
- 4.2 The results of experimentation
- 4.3 Discussion experimentation
- Conclusions
- Source List
Introduction
Currently available large number of articles made of composite materials based on elastomers. The only structural material, with a unique feature – the ability to large reversible deformation (elasticity) is rubber. Another advantage of the rubber as the the material of construction is the possibility to change widely not only its plastoelasticheskih properties, but also parameters such as: temperature saving interval elasticity; abrasion resistance; crack propagation, atmospheric aging; resistance to motor fuels, lubricants, water, corrosive liquids, and so on. At the present time it is impossible to find the branches of material production, which did not apply to rubber products. The term «rubber» – and collectively refers to a class of materials based on one kind of high molecular compounds  rubber (elastomer). Also rubber tires comprising a number of the various components (ingredients).
All the expanding needs of modern industry in the elastic material, the composite nature of their relationship and complex technical and technological determine the properties of one of the problems of modern rubber technology – the development of rubber with a certain level of technical and economic indicators. The complexity of the problem is that of a plurality of ingredients, the number of which is currently several thousand items, rezinschikov technologist must select 10-15 such components which when mixed rubber compound is obtained with the desired technical parameters, easily recyclable in standard industrial equipment. In developing the recipe of the rubber composition and the choice of the required technological process it into products technologist must remember that the material, energy and labor costs should be minimal, that is being developed by a complex pattern of technical and economic indicators should be on the level of international standards.
1. Relevance of the topic
The work was performed on the base production department DonNTU DKZHI and chemical technology of fuel. Actual work is that used rubber products, in snaryazhatelnom production and utilization in the process, have limited resource efficiency. The reason for this is an active influence on rizinotehnicheskie melt TNT products and mixtures thereof. Lack of engineering methods of forecasting performance rubber products makes this work to date.
2. Research object and purpose of the qualifying work
The object of study – the rubber mixtures used when working with vzrіvchatіm substance.
The purpose of qualifying work – to determine the effect of TNT on the performance properties of rubber compounds.
3. Physical and chemical bases of rubber products
Rubber is a complex multicomponent system, in addition to the rubber composition which contains up to 10-15, and sometimes and a variety of substances (ingredients) [ 1 ]. Its valuable technical properties of the tire gets in the final cycle of its production – in the process of vulcanization. A rubber in its turn – is the reactive component which is under the influence of mechanical stress, corrosive liquids and gases, low and high temperatures may undergo various structural changes that lead to a deterioration of the physical, chemical and mechanical properties of rubbers. Consequently, the correct choice of polymer depends on the duration of the operational capabilities of the rubber products. As rubber determines elasticity and a number of technical, technological properties and the cost of rubber products [ 7 ].
The specific properties of rubber high flexibility, the ability to large reversible deformations under static and dynamic loads, resistance to active chemicals, low water, gas tightness, good dielectric and other properties- caused its widespread use in various areas of the use of technology.
Manufacture of rubber products the largest industries, whose products are used in all areas of the economy. The main consumer of rubber products (tires, brakes, sponge products and a variety of parts) is a modern ransport – road, air, rail. How valuable insulation material combines with the dielectric properties of elasticity and resistance to various atmospheric influences, rubber is widely used in the electrical industry (in the production of cable, various electrical devices and so forth). Widely used in the national economy various rubber products – conveyor tape loading and unloading, flexible rubber hoses, shock absorbers, hoses. It is well known the value of rubber products consumer such as – shoes, clothing, sanitation and hygiene, and others. The main raw material for the manufacture of rubber are natural and synthetic rubbers.
At present, the domestic rubber industry has a large range of synthetic rubbers with different properties. Research in the synthesis of rubber continues [ 3 ]. Technical properties of rubbers mainly depend on the type of rubber from which they made [ 2 ]. Because of the wide variety of operating conditions rubber products used for their manufacture various types of rubbers. For example, oil resistant rubber products made from synthetic nitrile butadiene or chloroprene rubber. For the production of articles that have high temperatures are used, heat- resistant silicone rubbers and fluorinated polymers. High resistance to dynamic strain and wear tire is achieved using natural or synthetic stereoregular butadiene and isoprene rubbers, or combinations thereof, and styrene butadiene rubber. Such polymers are so many.
The article [ 4 ] and [ 5 ] given (about rubbers).
However, the properties of rubber products depend not only on the type of rubber and the ingredients used for the manufacture of rubber (vulcanizing agents, activators, accelerators of vulcanization, fillers, plasticizers, antioxidants, special substances). The most important ingredients used in rubber, should include soot (filler). When introducing it into the rubber mixture, its hardness, abrasion resistance.
The expansion of applications of rubber products, and the increasing demands on their technical properties led to the need for broad research on the study of the mechanism of processes of rubber from the rubber properties of the rubber under deformation, the fracture behavior of rubber in different operating conditions and other phenomena [ 5 ]. On the basis of these studies were developed ideas about the structure of rubber, vulcanized rubber structure, chemical nature transformations occurring during curing, aging and fatigue rubber. Created physicochemical principles rubber technology.
4. An experimental research methods and their results
The foundation of any rubber is rubber, natural or synthetic, which defines the basic properties of the rubber material. In this study, we conducted research rubber compounds based on urethane, ethylene-propylene, butadiene- nitrile, chloroprene rubbers, also a vacuum on natural rubber and isoprene rubber, on silicone rubber, Nairit rubber and fluorine rubber mixture on. Rubber compounds were selected from among used in the recycling of old ammunition, as well as new developing the rubber industry. When choosing a brand of rubber aim was to explore the different rubber compounds on the rubber, which would determine the future guidelines for the production of [ 8 ].
4.1 An experimental research methods
The process of mechanical mastication giving increased plastic properties of rubbers facilitates the processes of rubber compounding and adhesives, improves the quality of rubber mixes and convenience foods. When plasticizing observed not only increase ductility, but also drop in elasticity, an increase in viscosity, the solubility and the adhesive properties of the rubber.
Kneading was performed at laboratory rubber mill, it is carried out as a certain time mode, the clock set mode is set rollers and include the start mastication. The batch of rubber rollers into the gap produced by the large gear, separate pieces and gradually sank to the pan roller rubber returning to gap and repeats this process 5-6 times. Increases clearance of 1-2 mm, the rubber was allowed to wrap the front shaft, it happens plasticizing rubber. The homogeneous kneading achieved by repeated stirring. Kneading was carried out by rubber knife trimming the left and right sides of the roll, and further dimmed with a sliced pieces of rubber the opposite side of the roll. During mastication were doing 10-15 scores. Mixing is also achieved clotting on the front roll, fully trimmed rubber and feed roll into the nip rolls its end face [ 9 ]. Mechanical mastication process completed plastic cooling air. Mechanical kneading in laboratory conducted on laboratory valtsahkotorye shown in figure 1 [9].
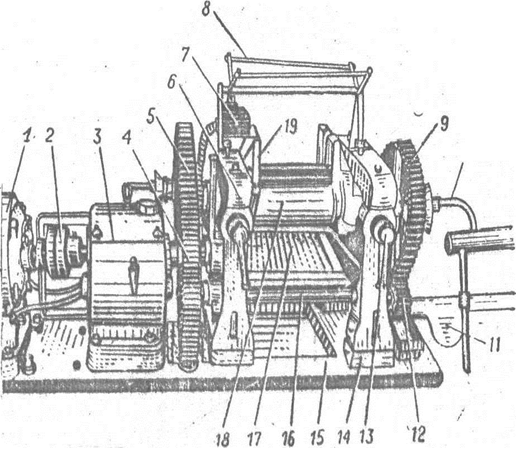
Figure 1 - rolls of laboratory
Laboratory mills are used for the mechanical mastication of rubber. Before you begin, include push-button starter, to test the machine without downloading and uploading. For this purpose the rolls applied chalk four lines that divide its circumference into equal parts. When you hit the rocker switch emergency loaded rollers should not rotate more than 1/4 turn under load rollers must stop immediately. Convinced of the good working rolls, including starting the device, set the desired temperature roll smoothly, gradually opening the valve in the pipeline, falling steam. In the future, control the temperature of cooling water fed into the rotating rollers. The temperature of the rolls check thermocouple at a stop rollers. The gap between the rolls is set at the beginning of the plasticizing minimum 0.2-0.3 millimeters shifting the rolls by means of adjusting screws, at the same time turning them clockwise. The gap between the rolls to control the left and right sides [9].
The vulcanization in the laboratory – is carried out in a hydraulic press used in the laboratory floor vulcanizing presses with plate 400x400 mm. The rise of the press platens and the formation of products is carried out by the action of the oil pump pressure according to 1.5-3 MPa [ 10 ]. These sheets or profiles mixture is cut by a knife for the cutting. Before vulcanization preform was controlled by weight up to 1 gram. The vulcanization was carried out at a predetermined temperature of 135- 180 ° C, and the press plate form a pre-heated for 20-30 minutes. The duration of curing at a certain optimum curing mixture, respectively equal to six preforms 10, 20, 30, 40, 50 and 60 minutes.
The vulcanization presses consists of the following:
- loading blanks into the form;
- press plate lifting hydraulic fluid at low pressure;
- preform blanks low pressure;
- formation and vulcanization products under high pressure;
- lowering of the press platens;
- unloading press plates and forms;
- vypressovok rubber trimming and cooling products;
- cleaning shape.
The forms are selected for a given configuration and size of the product, taking into account shrinkage of preforms [10].
Cutting- produced on a press for punching (figure 2), which is designed for manual cutting of rubber samples with special plates for the cutting knives [ 9 ]. The press consists of a frame (1) carrying on top of resistance (2) and the bottom of the lever system (3) and (4). Recent pivotally connected to the lever (5) via the rod (7) and the roller (6) crank. By turning the handle rod (7) causes erectile levers (3) and (4), thereby raises the vertical support (8) with a movable table (9) making it easy installation punching knife and removing a sample of the finished table is made retractable. Progress in the table is equal to 15 millimeters. Urging the wedge is located in a support, may vary the distance between the support (2) and the table (9) ± 10 mm. To work on the press need to find a table (9) and put on a sheet of paronite, thickness of 4-5 mm. On Paranit set punching knife. Next table rubber and is moving knife to the initial position, it is desirable for the cutting blade with is centered on the support (2). Pressing the lever handle (5) The table rises with the knife pressed into the rubber and cut the sample [ 9 ]. Turn the knob to its original vertical position, the table is lowered and removed carved pattern double sided blade, which is shown in figure 3 [9].
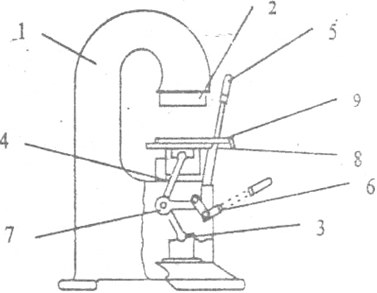
Figure 2 - Press for punching samples
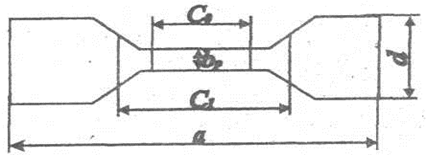
Figure 3 - Two-way blade
To study the process of swelling of rubber in an environment of molten TNT. In the process of filling and disposal of ammunition comes in direct contact with the melt rubber and TNT observed their mutual influence on each other. One measure of the stability of the RTI is the degree of swelling. The experience of previous work, it follows that the study of the process of swelling rubbers in an environment of molten TNT is essential and is one of the primary experiments in determining the compatibility of BB- polymer and polymer fitness material for use in contact with molten TNT [11].
The breaking machine as has been said above, the test sample is stretched at a constant rate to the gap and determining a conditional extension for a given voltage, tensile strength, and the relative residual elongation (figure 4) [9].
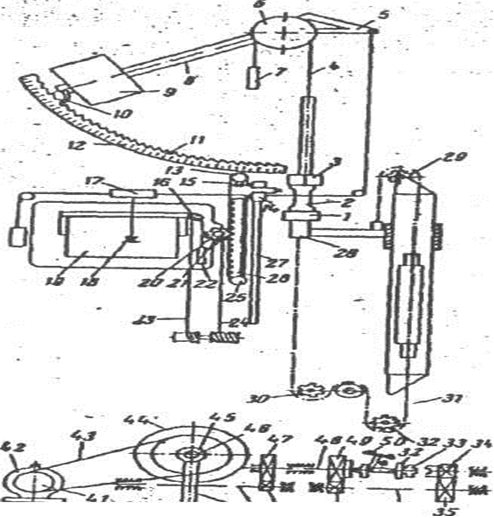
Figure 4 - Breaking Machine
The device testing machine consists of the following components:
- terminals and anchorages samples;
- the mechanism that produces the deformation of the sample (the drive and transmission-transforming nodes) force-measuring part or dynamometer;
- node strain measurement.
The disadvantage of the power pendulum-meter is the effect of inertia and the presence of friction in pendulum axis. Pendulum force-measuring instruments are extremely simple to operate, however, except as indicated deficiencies–uncomfortable because of their complexity and require strict vertical installation of the machine. A sample is placed in the upper and lower jaws. Clamp the actuator moves progressively down at a predetermined rate, the sample being stretched. The resulting force is balanced by the sample is measured and the power-measuring unit connected to the upper terminal (in this case, balancing is performed lifting force pendulum 8-meter). The deformation of the sample is determined by the change in length on its labels [9].
Stand for static tests of creep of rubber for long term static tests (Figure 5). The design of the stand can be varied and depends on the strength properties of the material, type of deformation, temperature conditions and testing medium used. This stand can be obtained by partial rekonstruktsieysuschestvuyuschih stands for stretching-compression [ 12 ]. Experimental data were obtained on the stand the following construction. In a welded frame with a table stand. On a table mounted speakers upper plate 3 which is mounted on the lamp 5 and 6. The emphasis between the table and the upper plate is ur type, udalennvy from the attachment (not rigid) arm at such a distance, as well as thrust 7 and the locking movement of the lever 8 [9].
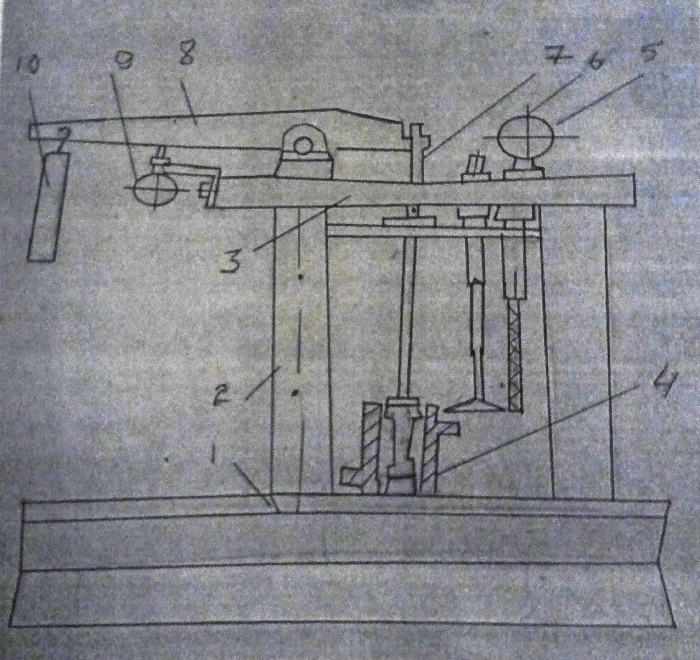
Figure 5 - Stand for static testing of rubber creep
4.2 The results of experimentation
9 was investigated various structural grades of rubber. In an environment in which thermostatted rubber used TNT. According to the degree of swelling of the rubber exposed to melt TNT at 100 °C for 100 hours can be reduced in the overall range in which rubber stamps can be arranged in the following order (from high to low swelling degree). In view of the fact that the main component of every rubber mixture is a rubber, of interest to consider the swelling of rubber depending on the brand content of rubber in the molten medium TNT at a temperature of 100 °C. Most susceptible to swelling rubber urethane rubber, nitrile–butadiene and hloropryanovom on isoprene and chloroprene rubber, rubber to vacuum Natural, fluoro rubber on. Several smaller swell silicone rubber to rubber. Slightly lose weight rubber in the isoprene and butadiene rubbers, rubber-based Nairit on EPDM dramatically lose weight. The results of studies of the effect of TNT on the performance properties of rubber products are shown in figure 6.
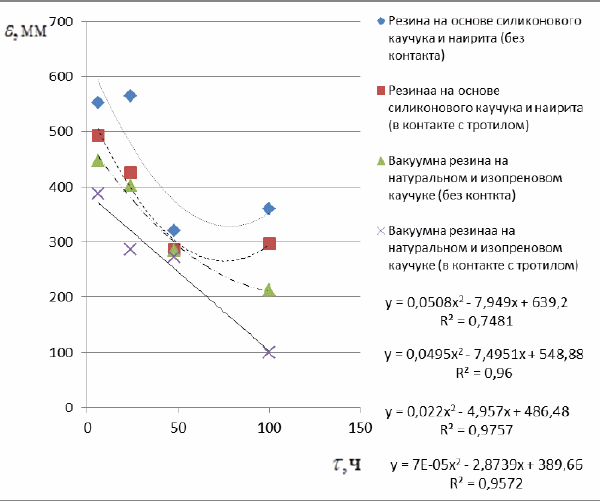
Figure 6 - Diagrams study of the effect of TNT on the performance characteristics of rubber products, and changes depending on the study of strength characteristics of rubbers in time
(animation: 6 frames, 7 cycles of repetition, 128 KB)
When testing the strength behavior of rubber – fatigue in corrosive liquids as well as in the air depends on the load conditions. With an increase in their resistance to swelling rubbers destruction increases, which leads to reduction of stresses. Under constant stress fracture occurs more intensively. Thus there may be no correlation between the creep and swelling, as well as between the behavior of rubber in statistical and dynamic conditions [13].
4.3 Discussion experimentation
Analyzing the results, it should be noted that most rubbers are subjected to incubation for 100 hours at a temperature of 100 °C, lose weight. In other words, there is a "shrinkage" rubber, i.e. evaporation of the volatile components of its composition. Vacuum tires «solidified» as a result of incubation, another significant holds this process, when it is in environment and superheated molten TNT. This phenomenon is typical of rubber, which tend to swell in mind crystallization of TNT in the pores of the rubber. For vacuum rubber in the first period termostatuvaniya there is a reduction in weight, as in air, and then over time, it begins to swell. Severe swelling of the data environment of nine brands of rubber seen in a vacuum based on natural rubber rubber (up to 70 % after 100 hours of incubation). Severe swelling is common to all the vacuum rubbers which differ from each other component composition. Less prone to swelling medium in TNT on EPDM rubber, NBR and chloroprene rubber, as well as natural rubber and isoprene. At the same time used in ammunition disposal rubber swell environment TNT at operating temperatures. Among these brands include rubber on rubber urethane rubber. Miscellaneous swelling of rubber stamps on urethane rubber that after six hours of contact swell 110 and 67 %, respectively, further intensive swelling continues, reaching 48-mi hours incubation 260 and 240 %. For the bulk of the rubber, a characteristic pattern, up to 100 hours of incubation they swell to a degree of saturation and continuation of contact does not lead to- that significant changes. In terms of the strength of the best proven rubber on urethane rubber, Nitrile rubbers and hloropryanovom. One measure of the stability of rubber products is the degree of swelling. The experience of previous work, it follows that the study of the process of swelling rubber in a medium of molten explosive is imperative and is one of the primary experiments in determining compatibility of explosive and polymer, and the polymeric material for use in contact with the explosive material [14].
The comparative analysis of rubber samples were investigated the effect of four different technical rubber grades with widely used explosive- trotilom. Under the influence of aggressive environment TNT interact chemically active substance with a rubber leads to various processes (structuring degradation, oxidation and the like), which causes a change in the structure of the rubber and deterioration Physico – mechanical properties of the rubber. A kind of picture of the destruction observed in samples of rubber on the isoprene rubber. Failure occurs gradually, alternating with jumps due to the gradual separation of fibers. For this rubber stamps in an environment characterized by TNT fiber break. Rubber – based urethane and NBR watched the gradual destruction and the picture in place breakage identical. According rubber stamps is not peculiar to high elasticity and the pattern of destruction in the air picture is identical to the destruction of the environment in melt TNT. Impact melt TNT leads generally to a decrease of the strength characteristics of rubbers. A synthetic rubber, urethane, nitrile rubbers, isoprene and more resistant to explosive which allows their use in the manufacture and provides greater strength parts made from these types of rubber. Samples were involved in the experiment, are compatible with the explosive, due to the fact that these rubber stamps having low power characteristics are approved for use in industry. Study of durability of rubber in these conditions is of great practical significance in these circumstances to assess the performance properties of rubber products.
Conclusions
1. In the Master's qualification was determined the effect of molten TNT in the performance properties of rubber compounds.
2. It was the selection of research subjects. It was selected rubber mixture used in the baseline and the new plant development DKZHI rubber industry. In view of the fact that the main component of the rubber composition a rubber mixture were chosen in different rubbers: on urethane, nitrile- butadiene, chloroprene, natural, isoprene and siloxane.
3. Research methods were selected rubber mixture. By long incubation determined the effect of an explosive stoykostnye parameters rubbers. The high degree of swelling up to 240 % for rubbers urethane, natural, NBR, and helps the ingredients to 15% rubber based on butadiene rubber and rubber at Nairit.
4. A mathematical model that establishes a connection between the phenomena of swelling and changes in the strength characteristics of the studied brands rubbers nahodyaschihsyaposle prolonged incubation in aggressive delirium molten explosives- TNT.
5. The research on the stand which determines the time of destruction and deformation of rubber, while the impact load, temperature and melt the explosive. It is found that the range of the destruction rubbers at loadings of 1.4 to 10.6 MPa and temperatures of 110 and 85–100 °C to melt TNT varies from one second to several hours.
6. As a result, studies have shown that, used at DKZHI rubber mixture based on NBR has limited capacity and resources are recommended for rubber compounds based on isoprene and silicone rubbers.
On the basis of previous work, I have made were sent on mission:
Article IV of the International scientific and practical conference «Donbass-2020»: Prospects rozvitku ochima molodih vchenih on the topic – «Rational use of rubber products at the disposal of ammunition» [15].
With Article IX International scientific conference of graduate students and students «Environment protection and rational use of natural resources» the topic – «Studies of the effect of TNT on the performance properties of rubber products» [16].
Article from the VII Regional Conference «Integrated use of natural resources», on the topic – «Assessment of compatibility with TNT rubbers methods spektraskopii» [17].
Source List
- Захаров Н. Л. Основные свойства резин и методы их определения. Учебное пособие к лабораторному практикуму / Н. Л. Захаров, З. В. Черных // Ярославль. – 1976г. – с. 60
- Баргштейн Л. А. Лабораторный практикум по технологии резины / Л. А. Баргштейн // Л. – 1979. – с. 219
- Материалы студенческой научной конференции за 2010 год К 80-летию ВГТА / Воронеж: Воронежская государственная технологическая академия. – 2010. –с. 108-109
- Грибанова М. А., Лынова А. С. Материалы студенческой научной конференции за 2010 год К 80-летию ВГТА / Воронеж: Воронежская государственная технологическая академия. – 2010. – с. 108-109
- Праздникова Т. Н. Рациональное использование конструкционных материалов в процессе переработки нитросоединений / Праздникова Т. Н., Полевик Н. В. // Охорона навколишнього середовища та раціональне використання природних ресурсів / Збірка доповідей VII міжнародної наукової конференції аспірантів і студентів. Том 1. – Донецк: ДонНТУ, ДонНУ. – 1997. – с. 131-132.
- Чалдаева Д. А., Хусаинов А. Д. Применение натурального и синтетического каучука в шинной промышленности / Вестник казанского технологическкого университета выпуск – № 11. – Том 16. – 2013
- Махлис Ф. А. Термодинамический справочник по резине / Ф. А. Махлис, Д. Л. Федюкин / М. – 1989. – с. 157
- Лебедев Л. М. Машины и приборы для испытания полимеров / Л. М. Лебедев / М. – 1967. – с. 253
- Праздникова Т. Н. Методическое пособие по теории деформации твердых веществ / Т. Н. Праздникова, Ф. Н. Галиакберова // Донецк: ДонНТУ. – 2010. – с. 28
- Галиакберова Ф. Н. Альбом оборудования для производства ЭНМ / Ф. Н. Галиакберова, Т. Н. Праздникова // Донецк: ДонНТУ. – 2012. – с. 48
- Бартенев Г. М. Прочность и разрушение высокоэластических материалов / Бартенев Г. М., Зуев Ю. С. / М.: Химия. – 1964. – с. 298
- Шур А. М. Высокомолекулярные соединения. Учебник для вузов- 3-е издание, перераб. и дополн / Шур А. М. // М.: Высшая школа. – 1981. – с. 656
- Кнунянца И. Л. Химическая энциклопедия в пяти томах, том 4. / М.: Советская энциклопедия. – 1990. – с. 641
- Материалы студенческой научной конференции за 2010 год К 80-летию ВГТА / Воронеж: Воронежская государственная технологическая академия. – 2010. – с. 108-109
- Праздникова Т. Н. Рациональное использование резино-технических изделий при утилизации боеприпасов / Праздникова Т. Н., Самохина А. С. // Охрана окружающей среды и рациональное использование природных ресурсов/ Сборник докладов IV международной научно-практической конференции "Донбас-2020": Перспективи розвитку очима молодих вчених. Т. 1. – Донецк: ДонНТУ, ДонНУ. – 2015. – с. 264-267.
- Праздникова Т. Н. Исследования влияния тротила на эксплуатационные свойства резинотехнических изделий / Праздникова Т. Н., Казаренко Д. С., Самохина А. С./ Охрана окружающей среды и рациональное использование природных ресурсов / Сборник докладов IХ международной научной конференции аспирантов и студентов. Т. 1. – Донецк: ДонНТУ, ДонНУ. – 2015. – с. 462-465.
- Праздникова Т. Н. Оценка совместимости тротила с резинами, методами ИК и ЯМР спектраскопии / Праздникова Т. Н., Самохина А. С. / Комплексное использование природных ресурсов, техногенная безопасность и энергосберегающие технологии / Cборник докладов VII региональной конференции «Комплексное использование природных ресурсов». Т. 1. – Донецк: ДонНТУ. – 2015. – с. 136-140.