Abstract
Contents
- Introduction
- 1. Analysis of the object of research
- 2. The purpose and objectives of research
- 3. The results of the research
- Conclusion
- References
Introduction
Two-speed induction motor refers to the basic electric machine of conveyors. Its use allows the start of the conveyor with a short step of reduced speed and implement delivering operation at a lower speed.
Operating experience of a two-speed induction motor has revealed the presence of voltage in the disconnected stator windings, in the absence of the control circuit leak in power connection its creates a potential electrocution hazard and require additional special investigations.
The experimental oscillograms of changing the electromotive force of the induction motor type EKVF – 355L12 / 4 when the power supply is other evidence that the work of the asynchronous motor with a nominal angular velocity in the low speed winding generated three-phase electromotive force.
Preliminary analysis of the oscillograms allows you to draw conclusions about the significant difference in shape and its frequency from nominal voltage and of a set of high-frequency and low-frequency components, which makes its specificity in the formation of the current and the amount of electricity in the circuit earth leakage [1].
It is logical to assume that the formation of the electromotive force of the stator winding is substantially determined by the structural features and dynamic characteristics of electromagnetic “stator – rotor” induction motor.
To determine the functionality of the devices of protection against leakage current to the ground in relation to the identification of electrical parameters in the connection of the disconnected stator windings, scientific and practical interest is the problem of modeling the electromotive force of said winding with the real parameters of the engine and the electrical supply network.
Investigation of the formation of the transformer voltage in the disconnected stator winding is rational conduct by computer simulation.
This approach allows for the study of processes in systems where full-scale experiment difficult. Also, a preliminary mathematical modeling allows to avoid errors during the experiments on real objects, and keep working capacity of the used equipment.
1. Analysis of the object of research
The object of the study is two-speed induction motor, designed for simple and reliable systems of automated electric scraper conveyor, allowing steps to change the rotor speed and to receive long-term lowered speed actuator for the implementation of haul operations [2].
The specifics of the operation of the engine as a basic element of the electric mining scraper conveyors gives grounds to consider that it is a functional component of mine local electrotechnical complex. Therefore, apply to him all the requirements for electrical operation and, above all, of State Standard Specifications 22929–78 [3].
Two-speed induction motors comprise a magnetic circuit on two three-phase stator windings (each compound wye 1 and 2 with four poles and twelve receive and allow simultaneous angular velocity of the rotor, respectively with 1500 rev/min and 500 rev/min. This greatly enhances security conveyor operation: Start the conveyor with a degree of short-term reduction (3 times) speed traction body; auxiliary operations for the delivery of equipment and materials in the stope at a slower speed. In Figures 1 and 2 you can see schemes of stator winding two-speed motor and its structure.
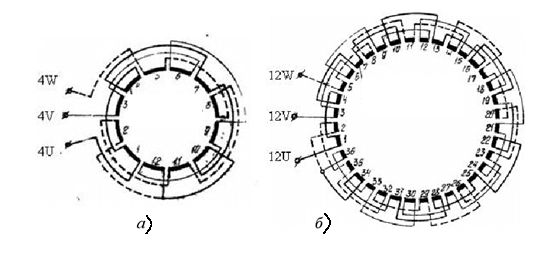
Figure 1 – Schemes of motor stator EDKVF series:
a) winding the nominal speed (pole number 2р = 4);
b) winding a reduced speed (pole number 2р = 12)
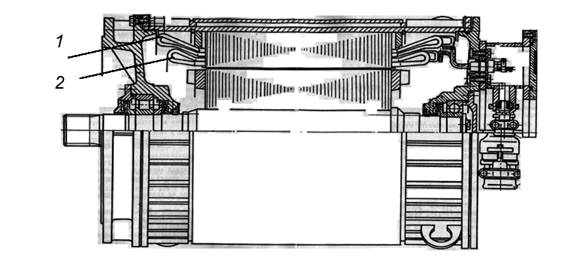
Figure 2 – The construction of a two-speed asynchronous motor series EDKVF manufacturing Pervomaisky Electromechanical Plant named after Karl Marks (Ukraine)
The use of two-speed motors can also solve the problem to reduce the dynamic loads in the traction organ by performing a certain switching sequence motor head and tail actuator for the first and second speed. The work of speed motor by special plan allows to reduce the dynamic loads in the traction body during starting, thereby enabling carry out ripping off conveyor on the low speed by static moment, i. e. without impact, and reduce the inrush current at low speed, without reducing the value of torque. The scheme of two-speed induction motor is shown in Figure 3.
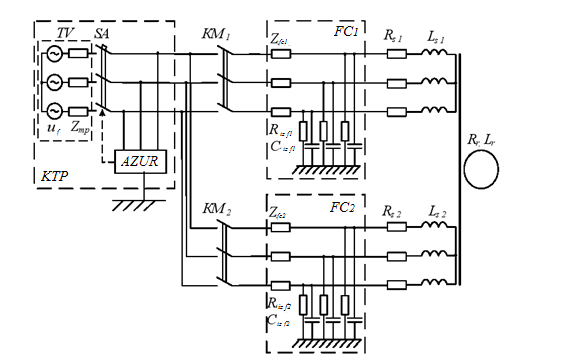
Figure 3 – Scheme of a two-speed induction motor
In the illustration: a three-phase power supply TV (transformer substation with automatic switch SA); AZUR – apparatus of protection against leakage; switching devices KM1–KM2; flexible cables FC1–FC2; Rs1, Rs2, Ls1, Ls2 – active resistance and inductance of the stator; Zтр1, Zfc1, Zfc2 – the impedances of the transformer and flexible cables FC1 and FC2; Riz f1, Riz f2, Liz f1, Liz f2 – insulation resistance and capacitance of the cable network.
For remote switching of the engine is supposed existence of a special starter, equipped with two distinct contactors, the outputs of which are joined by means of flexible cables with the corresponding stator windings.
Operation of the two-speed induction motor in a mine site is different of certain characteristics that must be considered in order to ensure the safety of personnel from electrocution. In particular, the presence of two separate windings on the same magnetic conductor produces effect when the one of the windings, which could cause a dangerous condition such as electrocution in case human touch phase of disconnected stator coil. This hazard occurs despite the presence in mine local electrical protection against current leaks to the ground, because the action of these means does not extend to monitoring of the disconnected stator winding two-speed motor due to lack of electrical connection between the stator windings.
2. The purpose and objectives of research
The aim of the study is to analyze the nature of changes in the parameters of transformer electromotive forces from the various operating conditions and parameters of the equipment and software, at the expense of science-based options, to protect people from electrocution when touching power connections of the two-speed motor.
To achieve this goal it is necessary to solve several problems:
3. The results of the research
The initial data for the model should be considered shape and geometry magnetic circuit of the stator slots, features of distribution in these slots stator windings, the air gap between the yoke of the stator and rotor, shape and geometry the magnetic circuit of the rotor and the angular velocity of its rotation, as a parameter which specifies the frequency of overlapping the stator slots by magnetically conductive material fragments of the magnetic system of the rotor.
In the generalized form of the processes occurring in the two-speed motor, the model can be represented by a single-phase transformer when it alternately overlapping the yoke of the magnetic system, the rate of overlap can be varied, which corresponds to the processes during engine operation [5].
Consider the simplest case – processes during alternately overlapping U-shaped magnetic circuit single-phase transformer magnetically environment. The equivalent circuit of the magnetic circuit of the transformer is shown in Figure 4, where indicated: F1, F2 – the magnetomotive force of the primary and secondary windings; Ф1, Ф2 – magnetic fluxes; Фs – leakage flux; UM1, UM2 – magnetic voltage drop in the primary and secondary magnetic cores; Uzaz1 – Voltage magnetic air gap between the primary core and the yoke, Uzaz2 – voltage at the magnetic air gap between the secondary shaft and yoke; Uz1, Uz2 – magnetic pull to the left and right halves of the yoke.
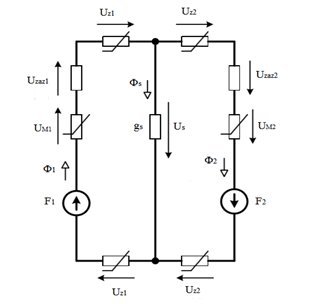
Figure 4 – The equivalent circuit of the magnetic circuit of the transformer
For the above equivalent circuit satisfy the following dependence [4]:
Magnetomotive force of the primary winding:

Magnetomotive force the secondary winding:

The magnetic flux in the chain:

The magnetic flux of the primary winding is determined from the expression:

where: Ψ = ∫Edl – magnetic flux linkage of the winding, w1 – the number of turns.
The required voltage on the secondary side:
where I2 = F2 / w2 – secondary current.
By implementing the given function in software package MatLab, were obtained waveform voltage in the secondary winding of the transformer under different conditions.
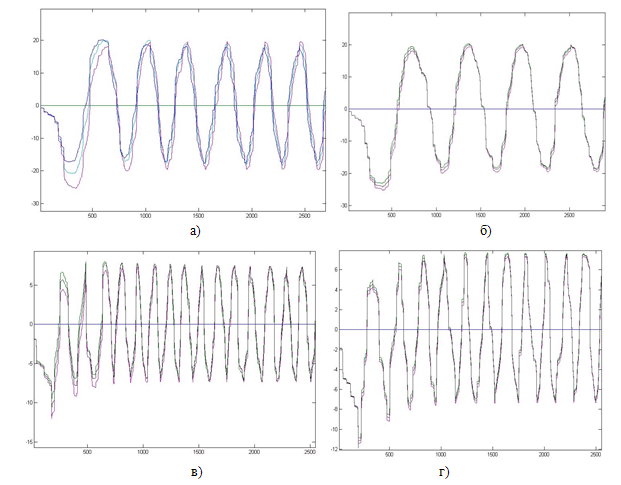
Figure 5 – Oscillograms of the voltage on the secondary winding of the transformer:
a) the amplitude of 100 V, frequency 70π рад/с, 50х25х50, k = 1, Δ = 0.01;
б) the amplitude of 100 V, frequency 70π рад/с, 50х25х50, k = 1, Δ = 0.09;
в) the amplitude of 100 V, frequency 200π рад/с, 50х25х50, k = 1, Δ = 0.01;
г) the amplitude of 100 V, frequency 200π рад/с, 50х25х50, k = 1, Δ = 0.09
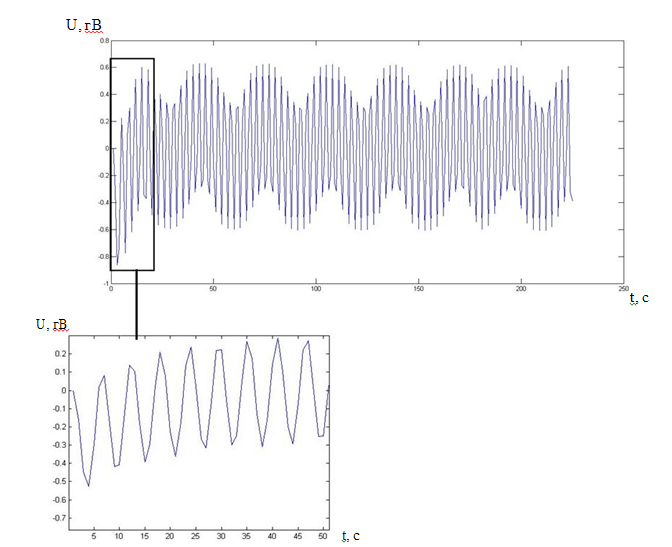
Figure 6 – Oscillograms of the voltage on the secondary winding of the transformer 50 at the amplitude, frequency 100π рад/с, 25х12х25, k = 1, Δ = 0.1
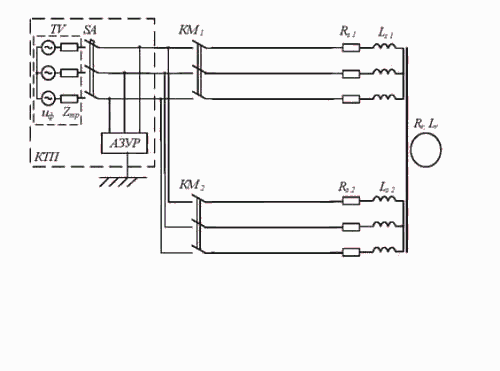
Figure 7 – Danger of the electrocution in a case when a person touches a winding phase of an induction motor (animation: 15 frames, 7 cycles of repeating, 145 kilobytes)
Conclusion
Substantiated the existence of electric power in affecting the properties of accessions disconnected stator winding of working two-speed induction motor. Disconnected coil system generates a three-phase electromotive forces, the amplitude and frequency parameters are sufficient to create a dangerous factor of electrocution in the earth leakage circuit.
Based on the research of the developed model, we can conclude that the job in the frequency and sequence of overlapping clearances magnetically conductive material allowed us to obtain the form of electromotive forces with distortions close to the actually existing. Therefore, this approach can be applied to further study the adjusted two-speed asynchronous motor model by representing it as a set of components of the transformer.
This master's work is not completed yet. Final completion: January 2016. The full text of the work and materials on the topic can be obtained from the author or his head after this date.
The text of the abstract is intellectual property that is forbidden to use or copy without an agreement with the author.
References
- Маренич К. М. Анализ параметров эксплуатационной безопасности двухскоростного асинхронного двигателя шахтного скребкового конвейера / К. М. Маренич // Наукові праці Донецького державного технічного університету. Серія гірничо-електромеханічна. Вип. 35. – Донецьк, ДонДТУ, 2001. – С. 127–131.
- Правила технічної експлуатації електроустановок споживачів. Затв. 25.07.2006 № 258 / Міністерство палива та енергетики України. Х. Індустрія, 2007. – 272 с.
- Маренич К. М. Автоматичний захист електроустаткування шахт від аварійних станів і небезпек / К. М. Маренич, І. В. Ковальова // Навч. посіб. для вищ. навч. закл. – Донецьк: ДВНЗ «ДонНТУ», 2013. – 199 с.
- Кацман М. М. Электрические машины / М. М. Кацман // Учебник для студентов вузов. – М.:
Академия
, 2001. – 463 с. - Дубинка Е. С., Маренич К. Н. Принцип моделирования процесса формирования ЭДС отключенной обмотки статора двухскоростного асинхронного двигателя / Е. С. Дубинка, К. Н. Маренич // ХV международная научно-техническая конференция
Автоматизация технологических объектов и процессов. Поиск молодых
. – Донецк: ДонНТУ, 2015.