Аннотация
Черенков Н. С., Семёнов А. С. Модернизация и оптимизация автоматизированных конвейеров в гнорной промышленности В данной статье описана суть автоматизации и модернизации конвейеров (преимущественно ленточных) в горной промышлености и их механизмов. Проведен анализ автоматизации конвейеров, описаны основные требования к их надежной работе и производительности после проведенной над ними модернизации, а именно: оптимизация работы линий и сокращение простоев; управление пуском, остановкой, режимом работы и скоростью конвейерных линий дистанционно; автоматизация подачи компонентов; удаленный контроль состояния конвейера; предупредительное извещение о запуске или остановке транспортеров; повышение уровня безопасности на предприятии; синхронизация работы нескольких участков конвейерной линии; автоматическое определение брака продукции на линии и остановка конвейера; автоматизированный учёт готовой продукции и её компонентов. Также осуществлён анализ практического применения модернизации систем автоматизированной работы конвейеров и перспективы их дальнейшего усовершенствования.
Ключевые слова: ленточные конвейеры, автоматизация, модернизация, горное дело, фабрика, перспективы дальнейшего усовершенствования.
Введение
Автоматизация конвейера заключается в его модернизации (модификации), а также в систему его электропривода. В настоящее время многие компании предлагают такие услуги: модификацию конвейеров посредством снабжения их современными датчиками и компьютерами с необходимым ПО. Все это делается для ускорения производительности производственных и перерабатывающих фабрик, повышения дохода от производства, а также для увеличения безопасности на предприятии: ведь благодаря датчикам и ПО контролирующего конвейерное производство компьютера, повышается не только производительность, но и надежность работы конвейера и его безопасность, поскольку при аварийных ситуациях работа на фабрике (например, горноперерабатывающей) связанна с определенным риском для жизни и здоровья сотрудников, работающих на предприятии.
Автоматизация транспортеров и конвейерных линий
С момента изобретения современные конвейерные линии ушли далеко вперед. На многих предприятиях, тем ни менее, используются такие конвейеры, которые произведены достаточно давно. И такие линии могут не отвечать современным требованиям, как безопасности производства, так и производственного процесса. Вместо покупки полного комплекса оборудования имеется и такое решение проблем, как модернизация уже установленных на предприятии конвейеров.
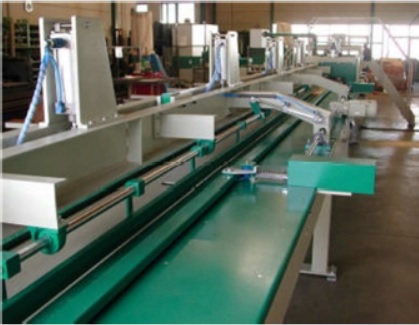
Рисунок 1 – Конвейерная линия фабрики по сбору механизмов
Автоматизация транспортеров и конвейерных линий позволяет:
- оптимизировать работу линий и сократить простои;
- управлять пуском, остановкой, режимом работы и скоростью конвейерных линий дистанционно;
- автоматизировать подачу компонентов;
- удаленно контролировать состояние конвейера;
- предупредительно извещать о запуске или остановке транспортеров;
- повысить уровень безопасности на предприятии;
- синхронизировать работу нескольких участков конвейерной линии;
- определять автоматически на линии брак продукции и останавливать конвейер;
- автоматизировать учёт готовой продукции и её компонентов;
В итоге автоматизация транспортеров/конвейеров повышает производительность предприятия, оптимизирует расход энергии, сокращает износ оборудования. Удалённое управление позволяет контролировать производственный процесс более эффективно. Повышается прибыльность производства в целом.
При автоматизации конвейерных линий выполняется следующие виды работ:
- разработка и внедрение для конвейерной ленты систем управления скоростью движения;
- для предотвращения на производстве несчастных случаев – установка систем безопасности и аварийного отключения оборудования;
- разработка и внедрение системы мониторинга и удаленного управления конвейером;
- установка счетных систем и модернизация систем автоматической сортировки и отборки;
Автоматизация отдельных конвейеров и конвейерных линий производится по двум основным схемам: дистанционное управление, при котором автоматизируются только пуск и остановка конвейера; автоматизированный контроль за работой конвейера и его элементов, при котором приводные двигатели автоматически отключаются при нарушении режима работы конвейера или его отдельных элементов. Согласно правилам безопасной эксплуатации к аппаратуре автоматизированного или дистанционного управления отдельными конвейерами или конвейерными линиями предъявляются следующие основные требования: обеспечение подачи предпускового предупредительного сигнала длительностью не менее 5 с; включение конвейеров в линию в последовательности, обратной направлению грузопотока, и обеспечение пуска последующего конвейера (против грузопотока) после разгона предыдущего; автоматическое одновременное отключение всех конвейеров в линии, транспортирующих груз на вышедший из строя конвейер; невозможность повторного включения неисправного конвейера при срабатывании электрических защит электродвигателя механической части конвейера и др.; отключение провода из любой точки по длине конвейера и наличие местной блокировки, предотвращающей пуск данного конвейера с пульта управления; возможность перехода на местное ручное управление приводами отдельных конвейеров при ремонте, осмотре и регулировании. Аварийное отключение привода конвейера должно осуществляться при обрыве ленты, затянувшемся пуске, снижении скорости ленты до 75% от номинальной, завале перегрузочного пункта и т.д. Между пультом управления, местом расположения приводов конвейера и пунктами загрузки конвейерной линии должна быть двухсторонняя телефонная связь или кодовая сигнализация. Для шахтных ленточных конвейеров применяют комплекс АУК.1М, обеспечивающий выполнение основных технических требований к автоматизации конвейерных установок и предназначенный для автоматизированного управления конвейерами и контроля работы стационарных и полустационарных неразветвленных конвейерных линий с числом конвейеров до 10. Комплекс обеспечивает централизованное управление из пункта оператора, расположенного в шахте или на поверхности, и включает в себя пульт управления и блоки управления, в которые входят датчики скорости, датчики контроля схода ленты, кабель-тросовые выключатели, сирена и др. Для контроля скорости ленты применяют тахогенераторные датчики, устанавливаемые у приводной станции между холостой и рабочей ветвями ленты. Ролик датчика прижимается пружиной к ленте. При вращении ролика тахогенератор вырабатывает ток с определенными параметрами, которые изменяются при изменении скорости ленты. Это фиксируется приборами, подающими команду на электропривод конвейера. Датчик контроля схода ленты контролирует ее положение и при аварийном сходе ленты в сторону подает сигнал в систему дистанционного или автоматизированного управления. Для экстренного прекращения пуска и экстренной остановки конвейеров с любого места технологической линии используют кабель-тросовые выключатели, состоящие из гибких тяг (тросов), протянутых вдоль става конвейера, и конечных выключателей. Для контроля состояния тросовой основы резинотросовых лент применяют устройства, обеспечивающие обнаружение поврежденных тросов в поперечном сечении ленты при ее движении, автоматическое суммирование повреждений тросовой основы по длине ленты и выдачу команды на отключение конвейера при обнаружении недопустимых повреждений. Применяют также датчики контроля работы перегрузочных пунктов (контроля заполнения бункеров и течек в местах перегрузок горной массы с конвейера на конвейер), аппаратуру автоматизации орошения на перегрузках, предназначенную для автоматического включения и отключения системы орошения в местах перегрузки на конвейерах и др.
Практика автоматизации горных предприятий
ООО «Компания ДЭП» создала автоматизированную систему управления конвейерами дорожно-эксплуатационного предприятия (АСУК-ДЭП) – подсистема горного предприятия и конвейерного транспорта, которая была создана для проведения модернизации морально устаревших систем управления конвейерами, таких как АУК рудника. К этому времени на горных предприятиях уже был опыт внедрения систем автоматики: управление технологическими процессами на обогатительных фабриках, управление поточно- транспортными линиями на поверхности и т.п. Однако такая модернизация означала полную замену системы управления, что в свою очередь являлось остановкой конвейера на неопределенный срок. Поэтому было принято решение создавать систему с максимальным сохранением функциональной части оборудования, которая не противоречила внедряемой новой технологии и могла работать совместно с модернизируемой аппаратурой. Такой подход позволил внедрять новое оборудование последовательно, «от конвейера к конвейеру», не останавливая всю цепочку конвейеров, и сокращал затраты на инвестиции такой модернизации.
Внедрение системы автоматизации конвейеров должно было позволить:
- перевести управление конвейерным транспортом на поверхность;
- разместить центральный диспетчерский пульт управления в диспетчерской рудника;
- повысить безопасность работы конвейеров путем получения адресной оперативной информации о состоянии датчиков защиты и систем пожаротушения;
- оперативно устранять аварии;
- своевременно распределять грузопоток, обеспечивая равномерную выдачу руды;
- проводить постоянный контроль работы и простоев конвейерных линий;
- настраивать систему управления конвейерным транспортом в зависимости от изменения технологии грузопотоков.
Диспетчерский пункт управления представлял РС-компьютер в индустриальном исполнении с бесперебойным источником питания и операционной системой не ниже Windows 2000. Блок управления конвейером разместили в непосредственной близости от приводного механизма. Органы управления и индикации расположили на дверце шкафа (с возможностью размещения их на отдельном пульте). Монтаж блока управления спроектировали с максимальным использованием существующих кабелей и схем обвязки. Контрольные датчики в шлейфе безопасности, при контроле ленты, ограждения, датчики скорости ленты и барабана потребовали только ревизии. Для определения номера сработавшего в шлейфе датчика был разработан малогабаритный адресный модуль, который легко устанавливается в цепи датчика, типа КТВ и КСЛ, и при его размыкании генерирует в шлейф запрограммированный адрес. На верхнем уровне установили специализированное программное обеспечение АРМ-ЦПУ.
Данная система автоматизации конвейерного транспорта прошла опытную эксплуатацию в 2003 году в руднике ОАО «Уралкалий» и в 2004-м получила разрешение на применение в шахтах и рудниках, опасных по газу и пыли. Система получила название «автоматизированная система управления конвейерным транспортом АСУК-ДЭП». За семь лет АСУК-ДЭП получила «прописку» на многих предприятиях горной и угольной промышленности. В частности, ее используют все рудники ОАО «Уралкалий» и ОАО «Сильвинит», все шахты ОАО «Воркутауголь». В Кузбассе первыми АСУК-ДЭП стала использовать шахта «Березовская», а в настоящее время системой заинтересовались и другие угольные предприятия региона.
За это время система АСУК-ДЭП получила немало положительных отзывов. Система постоянно совершенствуется, добавились новые функции: измерение температуры на двигателе и редукторе, измерение объема транспортируемого материала, управление орошением и пр. Появилась аппаратура управления вспомогательным оборудованием конвейерного транспорта — например, пересыпными устройствами, бункерами, питателями, катучими конвейерами, реверсивными конвейерами и многое другое.
Результаты исследований
Дальнейшее качественное совершенствование автоматизации конвейерных линий должно развиваться в направлении повышения централизации управления на базе использования специализированных ЭВМ и микроконтроллеров, что позволит повысить оперативность управления за счет обработки большого объема информации о работе конвейеров, причинах аварийных ситуаций, вести работу конвейеров в оптимальных режимах, увязанных с работой очистных забоев или других источников грузопотока.
Автоматизация конвейерного транспорта предусматривает оснащение средствами автоматического контроля и зашиты каждого конвейера и управление, как отдельными конвейерами, так и всей линией.
Повышение эффективности технологических процессов путем применения компьютерно-интегрируемых систем автоматизированного управления является перспективой дальнейшего развития рудодобывающей промышлености, которые позволяют организовать технологические процессы на качественно новом уровне, исключая непроизводительные затраты времени и энергоресурсов при изменении динамических параметров объекта. Если рассматривать транспортный комплекс шахты, который осуществляет доставку полезного ископаемого от очистных забоев на поверхность шахты и включает в себя конвейерный транспорт с аккумулирующими емкостями и скиповой подъем, то в процессе работы конвейерной линии должно обеспечиваться наиболее выгодное (по условиям экономии электроэнергии) соотношение параметров – «уровень загрузки ленты – величина скорости ленты», не ограничивая при этом производительность забоя. При отсутствии твердого материала на ленте конвейер должен быть остановлен. Это позволит снизить потребление электрической энергии за счет уменьшения времени работы конвейеров вхолостую, а также повысит срок их службы. Существующие в настоящее время системы управления шахтными конвейерными установками не позволяют достаточно эффективно регулировать скорость движения ленты. Поэтому единственным вариантом регулирования её скорости при производительной работе является остановка конвейеров на период времени, продолжительность которого определяется аккумулирующей способностью конвейерного состава. Автоматическое поддержание в процессе разгрузки аккумулирующего бункера рационального соотношения параметров – «уровень загрузки бункера – уровень загрузки ленты – скорость движения ленты» обеспечит дополнительную экономию электроэнергии.
Перечень ссылок
1. Семёнов А. С., Шипулин В. С. Использование газоаналитических систем нового поколения для защиты рудника // Фундаментальные исследования. 2014. № 6–3. – С. 480–484;
2. Рушкин Е. И., Бондарев В. А., Семёнов А. С. Применение автоматической газовой защиты на подземном руднике по добыче алмазосодержащих пород // Современные наукоемкие технологии. 2014. № 5–1. – С. 229–231;
3. Семёнов А.С. Применение системы электропривода с преобразователем частоты и автономным инвертором напряжения на проходческом комбайне // Технические науки – от теории к практике. 2013. № 18. – С. 71–77;
4. Семёнов А. С., Пак А. Л., Шипулин В. С. Моделирование режима пуска электродвигателя
погрузочно-доставочных машин применительно к рудникам по добыче алмазосодержащих
пород // Приволжский научный вестник. – 2012. № 11 (15). – С. 17–23.