Abstract
Contents
- Introduction
- 1. Analytical review of the technical means to increase water intake interval water wells.
- 2. The purpose and objectives of research
- 3. Driving and technical implementation of the new and expanded jetting telya
- 3.1. Schematic diagram of the hydraulic expander
- 3.2. Technology washout cavity for installing gravel
- Findings
- List of sources
Introduction
The problem of drinking water in the world is becoming more acute. This is due to the fact that almost all sources of fresh water have become more or less contaminated by human activity. This problem is particularly acute in the organization of economic–drinking water supply. Never before has the problem of drinking water is not facing humanity as acute as in recent years. To mark the official recognition of the importance of water issues, the General Assembly proclaimed the period 2005–2015 as the International Decade "Water for Life". [3]
One of the main sources of water are water wells.
The boreholes water movement is performed in the forward direction (from the wells) direction. For the whole period of operation of the well wall it within the reservoir must be sustainable. This is achieved by installing a filter in the well, the purpose of which is the prevention of the collapse of the walls of the well and clean up the water coming to the surface of solids.
Depending on the particle size of the rock producing formation, the filter structure can be used from the very simple–with the tubular perforations or frame–rod, to the most complex–gravel.
Among the selected filter, especially when the producing formation is represented by sands of different particle size distribution, it is recommended the use of gravel filters. Such filters are successfully prevent sanding. Lower hydraulic resistance allow to obtain higher than the other filters, flow rates. The velocity of the water as it passes through a gravel mixture gradually increases as you move to the frame. This fact is the reason for the slower clogging of the filter due to deposits of salts, iron hydroxide, and others. Therefore, filters with gravel package, even under adverse conditions, hydrochemical work for a long time without a significant reduction in the specific flow rates [1], [2], [6].
Currently, filters with gravel package are of limited use. For their water supply is used 5–8% and hydrogeological studies–only 3–5%[1], [4]. This situation is due to several reasons, among which are the lack of effectiveness of engineering and technology facilities such filters, which in some cases is due to the complexity of the s, Originating in the formation of cavities in the area prifiltrovoy well to contain a sufficient amount of sorted and c tions Therefore further development and perfection of technique and technology expansion slot water intake water wells in places gravel construction is an important task.
1. Analytical review of the technical means to increase water intake interval water wells.
Borehole expanders used to create cavities in the range of the producing formation may have retractable cutters bodies (reamer) or do not have them (nerazdvizhnye expanders).
Nerazdvizhnye expanders have fixed dimensions in transport and operating position, providing an unobstructed descent (ascent) of the instrument in the hole in a predetermined interval above the producing formation. When operating expanders nerazdvizhnyh slaughter develops along the productive interval in the interior of the reservoir from the well bore.
Sliding dilators of different sizes and in the transport position. In the transport position, the diameter of the housing provides a smooth slope instrument at a predetermined interval of the well with the diameter of the casing and drill pilot trunk. After launching the tool in a predetermined interval from the case put forward cutters organs that are removed after the extension back. When the reamer after collaring ring culling develops along the productive formation from the lower to the upper limit, or vice versa.
By the nature of driving from transport to working position reamer is divided into mechanical, hydraulic and inertia.
Hydraulic reamer are in the operating position the pressure developing in the pump discharge line and the tool body when flushing. Cutters authorities closed, usually at the expense of the return force of the springs when you stop washing.
Inertia reamer are in the working position by centrifugal forces acting on the cutters bodies under the instrument. Closing the blade is under the influence of their weight.
The jetting expanders used to break the rock energy of the jet wash liquid flowing out of the nozzles. Such ext-solvent and are in working condition after the descent at a predetermined interval by washing with a given flow rate and the creation of the design pressure drop across the nozzles. After descending into the hole of the expander at a predetermined interval start the washing liquid to be fed either concurrently with rotation or no rotation of the tool. The flow of fluid flowing from the nozzles jetting expander goes to slaughter and destroy the rock. Destruction of rocks under the influence of jetting the jet is due to the creation at the bottom of the axial pressure, leading to the destruction of the structural links and erosion of rocks (Figure 1a).
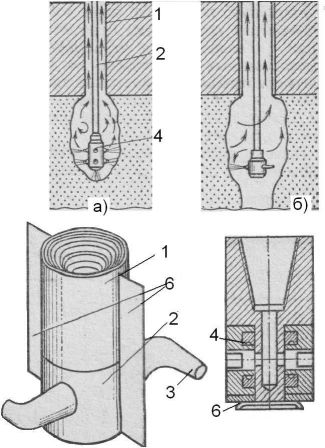
Figure 1–Jetting extenders: a–circuit hydraulic expander: 1–clearance; 2–drill pipe; 4–expander; б–diagram of the hydraulic turbine expander: 1–coupling to the shaft; 2–impeller housing; 3–nozzle; 4–the self-cuff th schiesya; 5–locking washer; 6–Brake plate
Jetting effect of the destruction of rocks used in hydraulic turbine expanders (Fig. 1б). The advantage of the dilator and prior to jetting s lies in the fact that the drilling of the cavity in the desired interval of the wellbore can be accomplished without rotation of the body of the expander through the drill pipe. Due to the reactive forces through directed nozzles 3 high-pressure jets of washing liquid breaks down the wall of the well. The casing of the rotating impeller 2 m smiling on the coupling to the shaft 7 through which the washing liquid is fed to the nozzle 3. The impeller housing is held on the shaft by means of a locking washer 5. To reduce the RPM of the turbine installed brake plate 6. These extenders found comment tion for e expansion borehole in weak or unstable sands under gravel package, the extension can be done simultaneously with the descent of the filter. Expanders are also used for development of wells to clean filters by clay particles and destruction of the filter cake on the borehole wall.
Although the resulting effectiveness of the provision of schemes jetting method for producing cavities, use th s alozhenn kinematics and work expander straight scheme wash well does not exclude the uncontrolled erosion of its walls above l Formation uyuscheysya prifiltrovoy cavity, especially if wall folded easily washed rocks [2].
According to some researchers highlighted the impact of the lack of jetting expanders can be significantly reduced due to the removal of technical support through the use of sludge feedback circuit's circulation of fluid in the well. At the same time, practical proposals for implementation, type of parameters and the justification of this type of expanders to date enough.
And activities of the master's work is to use a jetting effect of the destruction of the state of aggregation of sand and clay rocks in drillable cavity with simultaneous removal of sludge and kolmatata through the implementation of the scheme reverse circulation of fluid in the well.
The subject of the research master's work is technology and machinery equipment water intake of the water wells gravel filters.
The object of research the technical means and the technology expansion jetting water intake interval water wells in places construction gravel.
2. The purpose and objectives of research
Purpose–improving the efficiency and reliability of education development for the equipment of the water intake hole gravel packs by using the universal expander implementing jetting effect of the destruction of the wall rocks drillable cavity and stem cuttings scheme reverse circulation fluid.
To achieve the goal formulated the following main targets research:
- Justify the scheme to perform the calculation and design district azrabotat universal expander.
- Identify the basic regularities of the influence of design parameters of generators of the expander to ensure effective e e side breaking rocks and their removal from the drillable cavity.
The basis of the decision of tasks on the findings obtained in the result of On the review of analytical concepts and designs of expanders, forming cavities and to accommodate the construction of graded gravel gravel filters. It is noted that for the most difficult conditions when a producing formation is represented by sands of different particle size distribution, especially in the presence of layers of clay rocks, are the most effective development made through the use of jetting effect of the destruction of the wall rocks coupled feedback circuit circulation of the liquid in the removal of sand and clay emulsions on the surface.
3. Driving and technical implementation of the new and expanded jetting telya
3.1. Schematic diagram of the hydraulic expander
Schematic diagram of the developed expander is shown in Figure 2. The expander is lowered to the bottom hole on the drill string 1, performing the role of water-lifting columns consisting of a set of drill pipes TBS-70r complex KSSK–76, in which the concentric tubes placed vozruhopodayuschie 2 (LBTN–24), providing a job airlift pump.
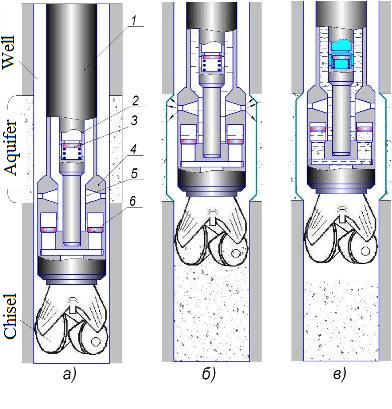
Figure 2–Schematic diagram of the jetting Extender: a–the initial state of the elements of the expander in the well; б–the process of erosion of the cavity; в–cleanout process.
Directly extender consists of two hydraulically and Cons t ruktivno s interconnected knots: knots and breaking rocks jetting assembly and cleanout.
The nozzle body 4 placed 5 relating to node jetting fracture rocks and impassable supporting rod 7, relating to the purification unit that connects to an air supply pipe string 2 and provided with a valve used PATH 3.
The camera body is made periodically overlapping section and tive valves 6. In this closed position of the valve corresponds to the erosion of rocks (Figure 2, б) feeding liquid through the pipes to the reamer 1. At an air lift hole cleaning, feeding air tr y bang 2, release valve opened, connecting the well cavity (via flushing bit windows) with cameras and half a spreader of water riser (Figure 2, в).
An air supply pipe in the bottom of the mixer are in the form of apertures provided above the housing with the possibility of escape of air in the pump string.
3.2. Technology washout cavity for installing gravel
Prior to the final depth of the well is drilled in the usual, conventional ones x nology. Then, the drill is removed and the well down to expand and Tel.
After descending into the well of the expander technology discussed in Section 3.1, included the drilling pump. From the nozzle the wash liquid exits under pressure. The check valve does not allow water to fill the air supply pipe. Jet energy during rotation of the expander housing destroyed rock cavern in producing the desired range. Collaring begins at the lower end of the range of expansion followed by expansion of the well from the bottom to the upper boundary of the aquifer.
Enhanced well done discretely. After drilling the wellbore interval length of 0.2–0.5 m the drill is stopped.
After completion of the expansion phase of wellbore drilling pump is switched off. Compressor for air supply pipe is supplied with compressed air. The check valve opens and air pressure of the compressed air is supplied to the mixer airlift. Passing through the openings in the air passes into the mixer drill string TBS-70r where it is mixed with the water, filling the hole and forming the pulp. Pressure drops in the mixer, the separating valve is opened and the cuttings sucked in to about Lonna drill pipe and outputted to the sump.
After the hose fixed on the nozzle gland being input cuttings, the air supply is stopped and transferred to the next drilling wellbore. After his drilling operation is repeated cleanout air–lift pump. At the same time the drill string is rotating drilling machine at minimum speed and IU d ately moves down. Chisel mixes rock at the bottom, but a surcharge s crushing it.

Figure–6 Technology washout cavity for installing gravel
(23 cycle, 10 reps, 223 kilobytes)
Findings
1. In the master's work on the basis of the analysis and synthesis of n roduktivnosti engineering and technology facilities gravel filters, pointed out that the limited application of these filters during the development of water wells is largely determined by the complexities involved in the formation of cavities in the zone of the well prifiltrovoy serving to contain a sufficient amount of sorted gravel, and inadequate efficacy oh yu cleaning wells drilled from rocks. Therefore further development and perfection of technique and technology expansion slot water intake water wells in places gravel construction is an important task.
2. The limited technical level created a broad class of stents, in terms of their application for the construction of gravel packs, it was the main prerequisite for the development of a new formulation of the problem of the expander to form cavities within the boundaries of the interval should be as well bubbled with increased levels of quality cleaning wells, and adapted, primarily for conditions when borehole complex and unstable sands sandy-clay deposits.
3. The parameters and developed, and a new jetting first extender, made on the basis of the technical association of nodes that implement the jetting th e wall rocks fracture expandable cavity, and back th circuit in the circulation of fluid in the well with the removal of sand and clay emulsions to the surface. Thus replaceable jet nozzle may be used for different breeds of hardness at a constant fluid supply pump power ground.
4. Calculation airlift using selected column with water-lifting arrangement of concentric tubes TBS–70r and the air supply pipes made based LBTN–24 for extracting broken rock from the well showed that the depth of fluid level 300 m and a depth of the hole to 600–700 m You can use the widespread compressors with s giving pressure 1–1.2 MPa.
5. Increased use of indicators developed device makes possible to expand well at different lengths, while ensuring the reliability of cleaning wells drilled from a long dy.
List of sources
- Арестов Б. В. Усовершенствование технологии сооружения гравийно–намывных фильтров способом обратной промывки / Б. В. Арестов, С. Н. Бузинов, А. Е. Корнилов, М. А. Цайгер. // Техника и технология сооружения газовых и газоконденсатных скважин.–М.: ВНИИгаз, 1984.С. 104–107.
- Башкатов А.Д. Прогрессивные технологии сооружения скважин /А.Д. Башкатов.–М.: Недра, 2003.–554 с.
- Башкатов Д. Н. Бурение скважин на воду / Д. Н. Башкатов,В.Л. Роговой.–М.: Колос, 1976.–206 с.
- Гаврилко В.М. Фильтры буровых скважин / В. М. Гаврилко, В. С. Алексеев.–М.: Недра, 1985. – 334 с.
- Ганджумян Р.А. Расчеты в бурении / Р. А. Ганджумян, А. Г Калинин, Н.И. Сердюк.–М.: Недра, 2007.–660 с.
- Дубровский В. В. Справочник по бурению и оборудованию скважин на воду / В. В. Дубровский, М. М. Керченский, В. И. Плохов, Я. А. Сиднев.–М.: Недра, 1964.–516 с.
- Никонов Г. П. Разрушение горных пород струями воды высокого давления / Г. П. Никонов, И. А. Кузьмич, Ю. А. Гольдин.–М.: Недра, 1986.