Содержание
- Introduction
- 1. Relevance of the topic
- 2. The purpose and objectives of the study
- 3. The types and categories of plastic waste
- 4. Overview of research and development
- 4.1 Overview of international sources
- 4.2 Overview of national sources
- Conclusions
- List of sources
Introduction
Currently, the production of plastic products has a tendency to constant growth and at a rough estimate, up to 200–270 million tons with a growth rate of 7 % annually.
Along with the improvement of technology of synthesis and plastics processing more and more attention paid to the development of processes and methods of disposal or disposal of plastic waste. At the same time the following main areas are[1]:
- re–use or recycling them in various compositions;
- thermal decomposition to give the desired product;
- thermal neutralization with regeneration of heat released.
One of the important methods of disposal of a thermolysis of polymer raw materials.
Thermolysis — thermal decomposition (destruction) of waste. As a result of processing of the organic part of MSW, as well as any industrial organic waste, both solid and liquid (waste oil, transformer fluids and pr.) are received useful combined cycle, liquid and solid carbonaceous products: synthesized high–calorie gas, coke carbon content of about 70 %, or fraction of liquid pyrolysis oil.
1. Relevance of the topic
Recycling of waste polymeric materials is becoming increasingly important. Today, plastics occupy space in many areas of human life, and that now there is no alternative. Given that, the average household each year sends to the landfill about 300 kg. of household waste. This bottle, label them, corks and other packaging products in a solid household trash up to 50 kg. per person per year[2].
Burning or rolling
into the land of the waste,
we are doing great harm to the environment,
but also lose valuable products Polymer processing.
Therefore, processing of plastic waste in particular
such as PET–bottles, PE–stopper, polypropylene label
is a very important issue and requires more consideration
of the application process of thermal decomposition of
a more ecological and sustainable use of methods and
disposal of waste plastics.
2. The purpose and objectives of the study, expected results
The aim of this study is to study the effect of thermolysis process waste polymeric raw material, the production process and its rational use.
The main objectives of the study:
- explore the process of thermal decomposition of plastics and to develop efficient and environmentally friendly methods of influence on thermolysis plastics from municipal solid waste, followed by the capture and separation of thermolysis products;
- conduct research and determine the possibility of further use of thermolysis products, for example, as a basis for the production of liquid fuel, the creation of new composite materials based on solid products of thermal decomposition of plastic;
- The work out mathematical model of the process of thermolysis of polymer waste.
3. The types and categories of plastic waste
There are many different types of waste plastics, for simplicity, they are divided into four categories based on processing methods:
• the same grade as waste plastics and scrap which can be added to the process by which they were originally derived;
• the same grade contaminated plastics that must undergo further processing and can be directly incorporated into the process of their production;
• mixed waste plastics to the known composition, mostly do not contain impurities;
• various grades of plastics contained in municipal solid waste contaminated with foreign matter.
By referring plastics can be divided into:
- Polyethyleneterephthalate — one of the most commonly used for packaging purposes are materials based on polyethylene terephthalate (PET, PET). This polymer is used, in particular, for bottles and bottles for water, soft drinks, fluids, etc.;
- Polyethylene and polypropylene (PP, PE) — these polymers are used in the manufacture of packages, labels, stoppers for bottles, etc. To date, polyethylene, polypropylene and multi-layer film is packed about 80 % of all goods;
- Polyvinylchloride (PVC) — is used for electric wire and cable, production sheets, pipes (especially chlorinated polyvinyl chloride) films, films for suspended ceilings, artificial leather, polyvinyl chloride fiber, penopolivinilhlorida, linoleum, coir mats, shoe plastic compounds, furniture edges, and so on. d. It is also used for the production of
vinyl
records, profiles for windows and doors[3].
4. Overview of Research and Development
4.1 Overview of international sources
In the French been registered
patent Thermolysis of organic waste in the furnace with balls
author Gerard Pullen.
The invention relates to the treatment of organic waste of industrial, agricultural and domestic origin. It concerns their treatment by thermolysis carried out, in particular, to set up, equipped with fixed or rotary kiln.
The patent is based on the heat treatment method comprises heating the organic waste in their stationary or rotary kiln – furnace for thermolysis when used as a means of heating the preheated pellets. The heat treatment is performed in an atmosphere without oxygen, and as the use of said granules fed into the furnace together with the waste and mix them with steel balls, and the steel balls are introduced into an oven at 600–1100 °C and the output temperature from 500–850 °C. Characterized installation options for carrying out the method. Technical result: simplification of the method of heat treatment of organic waste, security processing, providing the possibility to use the on–site installation of waste generation[5].
General design thermolysis group according to the invention is shown schematically in figure 1:
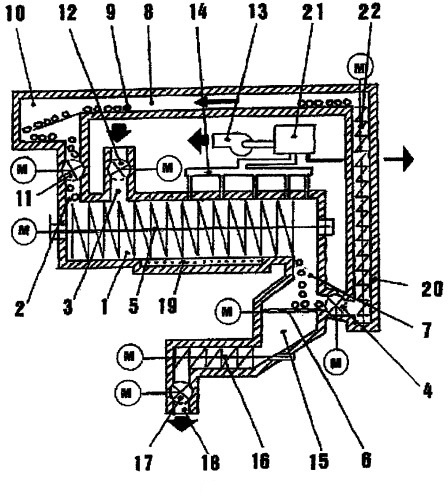
Figure 1 — General design thermolysis group
1 — furnace for thermolysis; 2 — an inlet pipe for the heated at a high temperature of balls; 3 — an inlet pipe for the waste to be thermolysis; 4 — drum or a gateway to release the balls, gave their thermal energy; 5 — screw conveyor; 6 — crashing to separate the balls from thermolysis residue; 7 — the pipeline for discharging a mixture of balls and residue after thermolysis; 8 — a conduit for recirculating steel balls; 9 — steel balls; 10 — a furnace for heating the steel balls; 11 — drum or the gateway to load steel balls; 12 — drum or the gateway to download the processed material; 13 — exhaust fan or a vacuum pump for sucking gas generated during the thermolysis, and to maintain a slightly reduced pressure in the furnace; 14 — collector (formed during the thermolysis gas for energy recovery; pair for condensing and recovering the condensable components are not to be incinerated); 15 — tank for collecting residues thermolysis; 16 — screw for transporting residues thermolysis; 17 — drum or the gateway to remove residues after thermolysis; 18 — the pipeline for removal of residues after thermolysis; 19 — for the additional heating device to compensate for the heat losses of the furnace or to provide energy for the launch phase; 20 — insulation of the whole complex, consisting of a furnace, piping, bins, etc.; 21 — condensing unit depressurized, trapping condensable thermolysis products; 22 — lift the heating mass (screw, belt conveyor and so on.); M — engines.
Figure 2 shows a special unit for thermolysis, complementary elements 1 shown in the total figure.
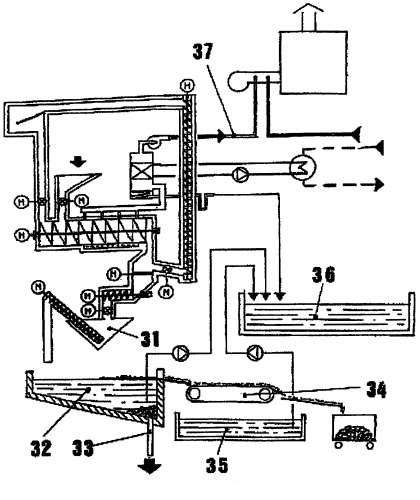
Figure 2 — Special unit for thermolysis
31 — tank for storage after thermolysis residues; 32 — bath wash residue after thermolysis; 33 — pipeline for removing solid residues; 34 — conveyor for the swelling with water of coke; 35 — a bath for storage and selection of water, dripped–off with the coke; 36 — Bath to store all liquid effluents, condensates, water dripped-off with the coke–contaminated water from the bath for washing and separation residue after thermolysis; 37 — direction of gas flow after thermolysis recycling.
Figure 3 shows a schematic of loaded waste from a different, more or less considerable humidity and comprising in series a drying oven and the unit for thermolysis. Here it is shown the elements marked with reference to the previous figures and positioned around.
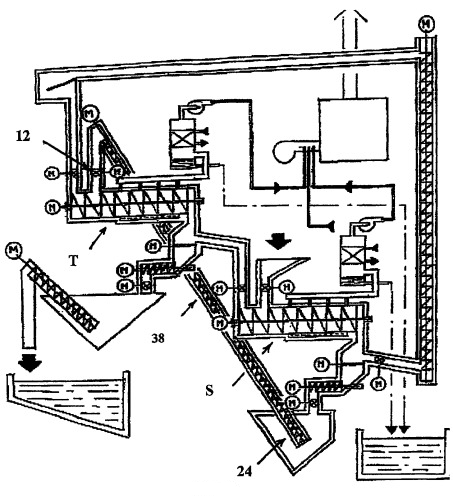
Figure 3 — Apparatus for waste with a humidity
S — drying furnace; T — furnace for thermolysis; 24 — a buffer hopper for storage of dry waste; 38 — hoist located between the hopper 24 — and the intake manifold; 3 — thermolysis furnace.
4.2 Overview of national sources
Being designed for installation FORTAN recycling allows to obtain high–quality heating oil from previously used tires, waste rubber (rubber products), household waste, wood waste, straw, waste oil refining, construction waste.
Figure 4 shows a schematic of FORTAN.
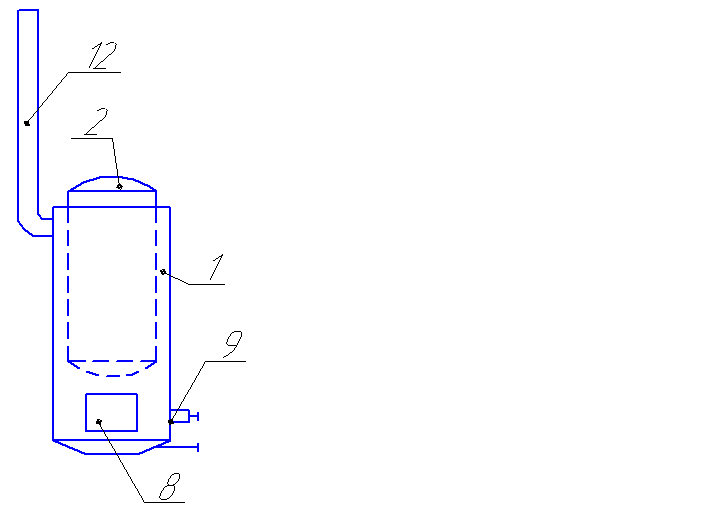
Figure 4 — Installation scheme FORTAN for recycling
1 — battery retort furnaces; 2 — stainless steel retort; 3 — bellows; 4 — magistral pyrolysis vapor gas; 5 — capacitors–refrigerators; 6 — various artists–separator; 7 — gas–liquid separator; 8 — furnace; 9 — burner; 10 — injector; 11 — blower; 12 — chimney; 13 — retort on loading and unloading; 14 — cover of the retort; ПГС — gas–vapor mixture; ГЖС — gas–liquid mixture; ГП — pyrolysis gas; МП — pyrolysis oil; В — air; ОГ — gas extraction; ОМ — selection of oil; РО — loading of waste (raw material); ПК — unloading char.
Description of the technological process of processing of rubber products on FORTAN installations.
Recycling of rubber products is carried out with a view to their disposal and to obtain valuable products–liquid fuels, combustible gas, carbon residue (char), metal.
Raw material (waste rubber products) is loaded into the vessel of the heat–resistant material (retort). The retort is placed in the oven. The raw material is heated by heat transfer through the walls of the retort and is thermally decomposed (pyrolysed) to form a gas mixture of carbon residue and—char. Gas–vapor mixture output from the retort through the pipeline is cooled, and the resulting vapors are condensed liquid is separated from non–condensable gases. Fluid accumulates in the liquid product collection, gas is used to partially or completely maintain process (burnt in the furnace). After the retort process, pyrolysis char is removed from the oven and placed in a retort furnace feedstock[4].
Conclusions
Recycling of household plastic is an actual problem. The use of thermal processing method has great potential in terms of efficient use and recycling of waste plastics. In the future, must to experimentally investigate the possibility of an optimal thermal decomposition of waste plastics with a maximum output of chemical products.
In writing this essay master's work is not yet complete. The full text of work and materials on the topic can be obtained from the author or his manager after that date.
Список источников
- Быстров Г. А., Гальперин В. М., Титов Б. П. Обезвреживание и утилизация отходов в производстве пластмасс. Л.: Химия, 1982. С. 178 — 214.
- Пилунов Г. А. Переработка отходов полиэтилентерефталата / Г. А. Пилунов, З. А. Михитарова, Г. М. Цейтлин // Химическая промышленность. — 2001, № 6. — С. 22 — 26.
- Википедия. Режим доступа: https://ru.wikipedia.org/wiki/%D0%9F%D0%BE%D0%BB%D0%B8%D0%B2%D0%B8%D0%BD%D0%B8%D0%BB%D1%85%D0%BB%D0%BE%D1%80%D0%B8%D0%B4
- Сайт разработки установки FORTAN. Режим доступа: http://biodizel.at.ua/
- Поисковик патентов. Режим доступа: http://www.findpatent.ru/patent/238/2381081.html
- Митрофанов Р. Ю., Чистякова Ю. С., Севодин В. П. Переработка отходов полиэтилентерефталата // Твердые бытовые отходы. — 2006. — № 6.