Abstract
Content
- Introduction
- 1 Relevancy
- 2 Setting the task
- 3 Review of the papers on this topic
- Conclusion
- Source List
Introduction
Waste heaps is an inevitable part of most coal mines, also of coal-preparation plants, strip-pits, open pits. In Donetsk region there are a lot of enterprises of given branch because of presence of coal. In total there are about 1260 waste heaps in Donbass, which accept rock from a certain mine, coal-preparation plant or from a group of coal enterprises. The most of the damage is done by making conical and herringbone heaps, which at times reach 110–120 m at height. The size and the shape of waste heaps influence the intensity of heat exchange at deep zones, define filtering capacities of a heap and help or cut the generation and accumulation of heat. The most intensive processes take place at the peaks of conical heaps and at the crest of plain ones. But in the same time spotty rock fire take place on surfaces of the heaps of different configuration. The heaps of height of less than 30 m usually don’t catch fire, those of under 50 m — 60 % fires, under 90 m — 87 %, over 90 % — almost all the heaps [1–2].
The specifics of coal mining include the fact that for every 1000 tons of extracted coal up to 12 kg of coal and rock dust is thrown out on the Earth surface, apart from that 50 000–570 000 m3 of methane; 1500–9000 m3 of mine waters; about 5500 m3 of oxides which are generated during the explosion works; 210–300 (up to 800 in Donbass) tons of waste rock. And the waste after coal preparation reaches up to 3 tons per each 1 ton of coal [5]. The total of rock waste situated in our region right now goes above 2 b m3. Moreover, a waste heap, especially when it’s burning, is a source of constant emission of polluting elements, and the changes in earth composition have negative consequences on its biological, erosional and esthetical characteristics [3].
1 Relevancy
Right now in Donbass 5526.3 ha are occupied by waste heaps, and the areas meant for waste get larger every year because of continuous arrival of rock to the heaps at disposal of working enterprises. Besides of taking the place for cropping, waste heaps also significantly change natural landscape. And as a result of spontaneous combustion of waste heaps, of wind and water erosion air and water pits get polluted, as well as the soil and the sources of water service. A burning waste heap of medium size emits annually about 15 000 tons of carbon oxide and large quantity of dust [1].
So the topic of this thesis is relevant, because the problem of presence of waste heaps, many of which are burning, is calling in Donbass. The results of sulfur burning, various oxides and coal and rock dust negatively influence human respiratory system, central nervous system and other organs. Waste rock must be considered as a raw material, not as waste. Deforming even one waste heap will produce such results as freeing the territory occupied by it, making the quality of air better, shrinking the negative influence on local residents. Moreover, in case of using the waste rock for making building materials, this act will help acquire cheap raw material.
2 Setting the task
This question was studied on the example of The Mine n. a. M. I. Kalinin, the waste heap of which has conical shape with a cut peak. During the time of its exploitation, 1 282 000 m3 of rock was put there. As this waste heap is classified as burning, it must go under procedure of putting out the fire according to The Instruction On Prevention of Spontaneous Combustion, Fire Extinction And Deforming The Waste Heaps
. As a result of putting out fire, negative influence on the environment will shrink, general enlightening in the condition of the environment in the area of situation of the enterprise will take place.
The Research of MakNII found that rocks in the given waste heap can be classified as follows: the lower zone contains large rock pieces (90 %), in the middle zone the percentage of big pieces goes down to 20–35 %. The peak generally contains small rock. Also the important parameters for our research are: humidity of rock in the waste heaps (from 7.6 % to 16.3 %), ash content (88.9–98.1 %) [2].
The aim of my paper is getting rid of negative influence of the waste heap in the area of its situation.
The tasks set:
- Studying all possible options for using extracted rock.
- Studying composition and properties of rock from the waste heap of The Mine n. a. M. I. Kalinin.
- Choosing the most appropriate option for usage of the rock from the waste heap of The Mine n. a. M. I. Kalinin, taking into consideration the characteristics of the rock.
- Composing the process scheme for usage of the rock with calculating all the details.
Object of the research: extracted rock.
Subject of the research: technologies and methods of recycling extracted rock.
3 Review of the papers on this topic
One of the priority directions of usage of extracted rock is to backfill with it the worked-out area. However, for many mines this option is not applicable, because rock is stored on the surface in such amounts that its removal back underground is technically inconvenient and economically insufficient. It needs to be said that the rock which is extracted during mining shouldn’t be on the earth surface in the open at all. Leaving rock in the worked-out area will allow zero expenses on its transportation and no addition to the existing waste heaps. In the same time the rock on the waste heaps, especially killas, is a new kind of anthropogenic mineral raw material which can be effectively used (both economically and environmentally) for making building blocks, ceramics, walling material, concrete filling etc. The most popular across the world is the burnt rock containing minimal percentage (less than 5 %) of coal contaminant and mineral clayey-sandy part that gets baked more or less. Old and fully burnt waste heaps often contain rock of fine quality that formed as a result of self-baking in the high temperatures (up to 1000 °С). Organic impurities partly burn away. The specialty of burned rock is its microporosity and, as a result, appearance of microcracks during self-baking. Besides, they possess quite high adsorption activity [4]. From the point of possible use all rock from waste heaps can be sorted into 3 groups:
- сontaining elements needed for nutrition of plants and usable for producing fertilizers;
- containing toxic elements and by using corresponding technologies usable for producing building materials;
- containing valuable microelements, usable in separation and industrial extraction of elements.
Nowadays the main directions for use rock from waste heaps are: filling the worked-out space (94.4 %), production of building materials.
Let’s look at one possible option of using rock from waste heaps in agriculture. Scientists from Lugansk have introduced an investment project on recycling waste from mining, with adding to it waste from poultry industry in order to use them later in agriculture as bioorganic mineral fertilizer.
This production consists of 3 main stages:
- on the first stage the waste containing carbon gets fermented in a methane-tank, as a result biogas and decontaminated sludge are produced. Produced biogas gives energy for production, and also in its liquefied form it can serve as gas for automobiles, agriculture machines and as a tool for local residents;
- on the second stage the sludge is mixed with crashed rock. The mixture is put into the machine that produces artificial humus with productivity 1 ton/hour;
- on the third stage mixed sludge and rock or the humus serve as food for California worms, which leads to getting biohumus.
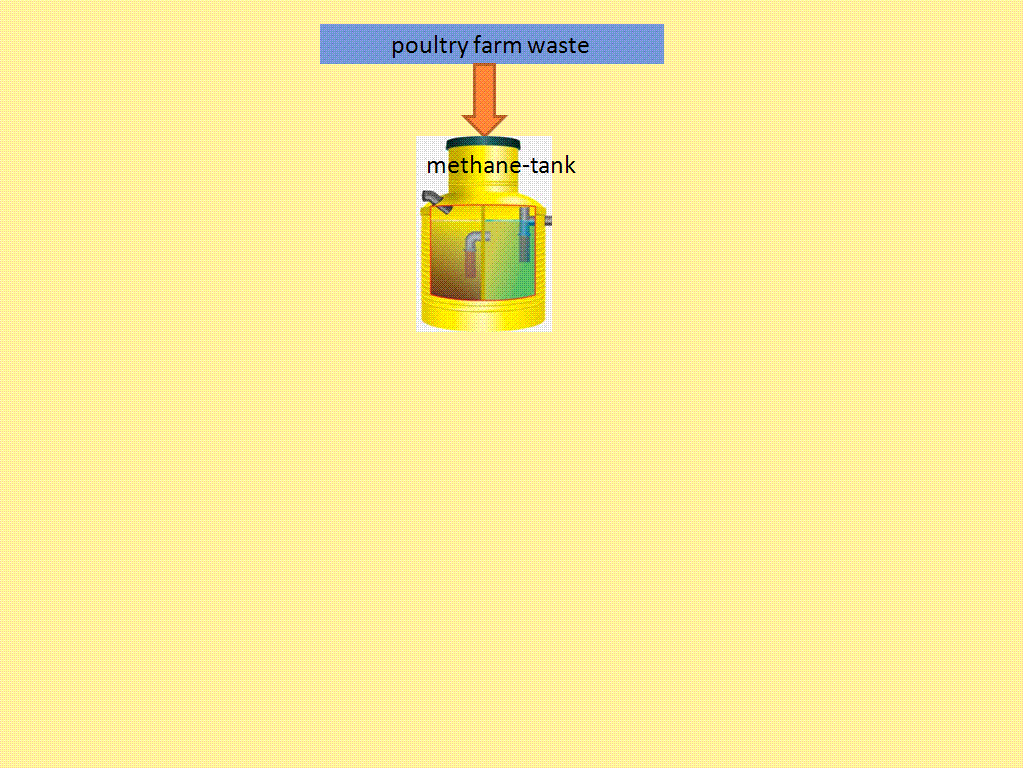
Picture 1 — The table for production of fertilizers by use of mine rock
(The picture is animated. Quantity of slides: 5. Quantity of repetitions: 7. Size: 200 kB. )
Biohumus that is produced with organic waste and mine rock as a foundation, contains a lot of microelements which are necessary for nutrition of plants. It is a highly effective complex fertilizer. Local injection of biohumus in such quantity as 2–5 tons/ha can raise cropping capacity by 40–80 %. In the same time the task of restoring chernozem layer, boosting soil fertility and reducing waste is solved [3].
The other direction for putting in use rock is production of building materials.
Burned rock by its chemical and physical characteristics, radiation and hygiene rate and other exponents can replace by 30–40 % natural raw materials for building industry. Innovative research also showed that, apart from binder based on burned rock, cement-free solid and celled autoclave and out-of-autoclave concrete (good for producing many items: external wall blocks, internal wall blocks, partitions, floor panels, footing) can be produced. A special place in production of things made out of burned rock takes fixing concrete — they are blocks of concrete of different length and width, special shape which are used in coal industry for fixing underground excavations. The addition (20–30 %) of floured mine rock gives concrete durability against sulfate water. At the department of extractable resources and eco-geology at DonNTU integrated research on waste heaps of Donbass has taken place to resurface possible ways to use rock from these waste heaps. The results show that the rock can be used to produce keramzit, building blocks, fill-up ground and as fertilizers [4].
From clay-slate from waste heaps of the mine n. a. Kalinin, adding clay, was made building block No. 75, certified by Experimental and Industrial Lab of geological expedition Ukrgeolstroy
(Kiev). This brick is lighter than a clay one and has better heat-insulating properties [4].
Burned mine rock of waste heaps after mechanical recycling at place can be used as large and small filler in concrete blocks and for producing wall items (bricks, stones, blocks), roof tile, decorative shell plates, pavers. Burned rock raw material when mixed with lime, cement or activating supplements makes a highly effective building material of controlled quality.
There are specific regimes, technologies and nomenclature of building produce that is made with burned rock: [3]:
- cement-free colored binder that has breaking strength of 20–30 mPa when squeezed for building, including brickwork, plasterwork, decoration work and preparation of solutions and different kinds of concrete;
- small filler for concrete and solutions;
- solid rock concrete of medium density (1400–1600 kg/m3);
- celled concrete of medium density (450–750 kg/m3).
Based on local and world experience of making use of industry induced resources a conclusion can be made that recycling of them may appear an additional source of obtaining non-ferrous and precious metals, also it may help reduce negative toxic influence on the environment and return the lands given to waste heaps to its original agricultural use. Among the waste of mining industry were located ferrous (iron, manganese, chrome), alloying (titanium, vanadium, nickel, cobalt, molybdenum and wolfram), non-ferrous (copper, zinc, lead, mercury, antimony and bismuth), noble (silver), rare (lithium, beryllium, strontium, yttrium, lanthanum, niobium, cadmium, scandium, gallium and germanium) metals as well as non-metals (porcelain) [3], and other useful components.
Study of chemical characteristics of rock from waste heaps gives evidence that burned rock from waste heaps is enriched by Fe2O3, K2O, P2O5, S. The most changes underwent argillites which are presented by sintered rock that contains leftovers of metal ware. The specific feature of this kind of rock is high content of Fe2O3 (67.7 %). Nowadays special attention deserves the opportunity to use clay-slate, tailings and other kinds of clayish rock for producing alumina (AI2O3), from which aluminum is made. Traditional alumina and aluminum are produced from bauxites, meaning rock with content of alumina more than 26–28 %. High content of AI2O3 is typical for rock of waste heaps of Donbass as well (up to 28 % in argillites and to 44 % in tonsteins). On the average in Donetsk-Makeevka area of Donbass content of AI2O3 s: in current waste of mining — 23.1 %, in waste heaps of coal-preparation plants — 20.2 %, in waste from flotation — 25.8 %, in waste heaps — 21.7 % (the highest rate of content is located in waste heaps of mines: mine n. a. Gorkiy — 26.75 %, mine No. 3 18
— 25.58 %, mine No. 8 Vetka
— 26.62 %, mine Krasnogvardeyskaya
— 26 %). This shows that rock from waste heaps of mines and coal-preparation plants can be used for producing alumina, from which aluminum is made. And that it should be seen as new non-conventional kind of mineral raw material. In some countries of the world technologies of producing alumina from mining waste have already been introduced. For instance, in France there was successfully tried a new diacid method of recycling mining waste for extracting alumina; technologists of Poland have proved the possibility of industrious produce of alumina from clayish rock which contains about 25 % AI2O3. In these and other countries reasonability of producing alumina from tailings of coal preparation and from other technogenic mineral raw materials has been proved.
In case when rock doesn’t meet regulations, a spoil tip should be greened: trees and shrubs should be planted. This will reduce the quantity of dust and gases that go to the atmosphere. The trees planted on a spoil tip also prevent its erosion.
Conclusion
At the time of writing this paper the thesis is not finished. Mentioned ways to use solid waste of the mine n. a. M. I. Kalinin are to be further studied in the master’s thesis in order to find the most effective one, taking into account the conditions at the enterprise and qualitative characteristics of the rock. Completed paper may be received from the author or his research advisor after June 30, 2017.
Source List
- Костенко В. К., Шафоростова М. Н. Решение экологических и социально-экономических проблем угледобывающей отрасли на основе комплексного использования недр // Сборник трудов V международной конференции
Социально-экономические и экологические проблемы горной промышленности, строительства и энергетики
(28–30 октября 2009). — Тула: ТулГУ, 2009, Т 1. — С. 438–446. - Васильев С., Шафоростова М. Н. Перспективы использования горелых пород шахтных отвалов // Сборник трудов V региональной конференции
Комплексное использование природных ресурсов
. — Донецк, ДонНТУ, 2012. — С. 16–19. - Колесникова В. В. Основные направления комплексного использования отвальной массы горнодобывающих предприятий // Сборник трудов II региональной конференции аспирантов и студентов
Комплексное и рациональное использование природных ресурсов
. — Донецк, ДонHТУ, 2009. - Панов Б. С., Проскурная Ю. А. Новые виды минерального сырья Донбасса // Сборник трудов I научно-практической конференции
Донбасс–2020: перспективы развития глазами молодых учeнных
. — Донецк, ДонНТУ, 2002. [Electronic resource] Access: http://ea.donntu.ru. - Соколов Э. М., Качурин Н. М., Мелехова Н. И. Рекультивация отвалов отработанных шахт Подмосковного бассейна. Известия ТулГУ. Науки о Земле, 2010. [Electronic resource] Access: http://cyberleninka.ru.
- Дворкин Л. И., Дворкин О. Л.
Строительные материалы из отходов промышленности
// Учебно-справочное пособие. — Феникс, 2007. - Закон
Об охране окружающей природной среды
от 30 апреля 2015 года. - Закон
Об отходах производства-потребеления
от 09 октября 2015 года. - Курденко С. С., Шафоростова М. Н.
Направления использования шахтной породы на примере шахты им. М. И. Калинина
// Сборник научных трудов VII региональной конференцииКомплексное использование природных ресурсов
. — Донецк: ДонНТУ, 10 декабря 2015. [Electronic resource] Access: http://ea.donntu.ru. - Снижение вредного воздействия породных отвалов угольных шахт на окружающую природную среду / Д. А. Козырь, Н. И. Артюхова, В. Н. Артамонов, В. Г. Ефимов // сб. науч. работ по материалам IX Всеукраинской научной конференции студентов, магистров и аспирантов
Экологические проблемы регионов Украины
.