Abstract
- Introduction
- 1. The urgency of the theme
- 2. The purpose and objectives of the study
- 3. Expected outcomes
- 4. Conclusions
- list of references
Introduction
From the experience of inspection systems of heat supply of cities and districts of the region in recent years, the trend of the specific consumption of fuel and electricity consumption growth in the production and transfer of thermal energy and coolant. Efforts disharmony in performance-heating systems heating and non-heating periods, resulting in a high difference of the same specific indices of fuel and electricity consumption. Summer thermal power boilers involved sometimes 30 times or more greater than the calculated power required for heat load, ie, the boiler operates in an invalid mode, indicating that it overestimated the installed capacity or the absence in the scheme of the boiler boiler for the summer heat mode.
Automated burner with a wide range of regulation is not always able to provide adequate heat output mode. This implies to heat loss on the source expressed in excessive costs for their own needs or low-efficiency units, and heat networks. In this case, on the production and transport of heat in the summer electric power involved much more than in the winter, in the proportion: the unit cost of electricity increased by 3-6 times, mostly consumed in the coolant circulation.
Existing resources of the accounting system and reporting to allow heating plants to reflect quite acceptable indicators of fuel consumption for the production and supply of heat to consumers, but overlook the analysis of the electric component. The structures of the heat rating of enterprises and billing are made on a specific fuel flow rates, and unit costs of electricity and power indicators are not standardized and practically not monitored. This fact is significant flaw regulatory framework and methods of energy audits, while the specific indicators of energy consumption and electric power can serve as significant indicators of heat supply systems, reduction of which will be the determining criterion for evaluating the efficiency of power supply systems.
The absence of a real picture of the boiler power supply systems, the discrepancy and lack of information about existing facilities under actual loads often does not allow to optimize the same systems in place, and the administrations of cities and regions and different levels of managers to take the right decisions and favorable development plans for district heating systems.
Ånergy audits accumulated at the Department of DonNTU industrial power system material allows to ascertain such facts and draw such conclusions and requires in-depth analysis of the situation, and in each case individually, as a good energy audit - it's not only saving energy, can crop up various interesting conclusions and decisions.
Most of the heat and electricity produced by thermal power plants (TPP) as a public and industry, as well as in centralized boilers. The remainder of the thermal energy produced in the autonomous sources of heat.
Energy efficiency of such enterprises is the ability to carry out the production process with minimum consumption of energy resources. One of the key instruments for achieving the required level of the enterprise is the energy audit of the company - an energy audit. Energy audit is carried out to improve the reliability of power supply companies with a minimum consumption of energy.
Energy audit - an energy survey of facilities in order to establish the efficiency of use of energy resources and the development of economically feasible measures to reduce the costs of energy savings for the enterprise or group of consumers, allowing to make quantitative estimates of the savings of energy and costs, as well as assisting the company in carrying out activities providing practical energy savings.
As a result of surveys determine the real state of the energy department of the object, energy balances, evaluate sources of energy losses, determine the direction of reducing energy costs and payments for energy. Mandatory energy audit result object is to issue recommendations for the optimization of production technologies and energy consumption.
In the process of enterprise energy audit assessed its potential energy or energy conservation, the state of its IT systems and accounting systems, the energy balance is compiled, modeling standards system. As a result, energy audits compiled "Report on the energy survey," developed an energy passport is given a list of activities to be implemented in order to eliminate provisions efficiency and improve work efficiency.
Energy audit is aimed at solving the following tasks:
-assessment actual state of energy use in the enterprise, identifying the causes and defining the values of energy resources losses;
-development plan of measures aimed at reducing the loss of energy resources;
-identification and estimation of reserves of fuel and energy savings;
-Define the size of rational energy use in manufacturing processes and facilities;
-Define requirements for improving the organization of accounting and control energy consumption.
As a result of the energy audit the company's management received:
-estimate current energy consumption with reliable data on the volume of consumption of resources and the amount of money spent on them, the whole enterprise, section by section, and their specific values for each type of product;
-The program of energy conservation measures aimed at continuous and systematic reduction of costs.
energy auditors are ready to solve most of the tasks that are put before them. At the same time a real energy auditor will warn the customer about his doubts to achieve the efficiency of a particular solution.
The basic rules of the audit:
There are three ways to reduce energy consumption:
-Exclude inefficient use;
-ustranit loss;
-povysit efficiency.
In these areas and in the following auditors have to work, because unwise to invest in improving the efficiency of operating equipment is useless.
The smaller the share of energy in total energy consumption, the less time (money the client) should be spent to determine the effectiveness of its use in the enterprise.
Often, a small saving for large consumers, it is more significant and achievable than a big savings in small consumer.
Energy audit can be divided into four main stages:
1.Oznakomlenie now, collecting and analyzing the necessary information, compiling a survey program.
2.Obsledovanie Company:
-Development of detailed balance sheets for all resources, the identification of the major consumers of resources and places to save.
-To perform this task, it is often necessary to carry out measurements and tests.
3. Development of energy saving projects and combining them into a single program improve efficiency.
4.Otchet and presentation of the results.
1. Background
Established recently the demographic situation and the pace of the world's energy consumption threaten the exhaustion of the existing stockpiles of fossil fuels. If before 1980 there 210 billion of fossil fuels were produced in the world, it is only in the last 20 years of the last century, this figure was exceeded. Of course, the forecast energy consumption in the XXI century, shown above includes not only the energy produced on the basis of fossil fuels, but also obtained from all possible sources (nuclear, thermonuclear, from renewable sources, etc.). Today, however, fossil fuels provide the lion's share of energy resources and their consumption shock, which causes the energy, or more correctly speaking, the fuel, the problem.
The data on reserves of fossil fuels are markedly different in different sources, which can be explained, first of all, the difficulty of obtaining reliable geological estimates, the constant improvement of evaluation methods and the ongoing exploration, as well as border mobility in the classification of energy: installed (explored) and undiscovered ( theoretically supposed); traditional (the development of which the present state of technology and economically feasible) and non-traditional (the development of which is now the technical difficulties or is not economically profitable).
How important is this factor (depletion of fossil fuels), provides insight into the comparison of values traditional reserves of fossil fuels and the current level of consumption (Table 1). Thus, while maintaining the resources of fossil fuels in consumption at the level of 2000 conventional oil reserves will be exhausted in 41 years, natural gas - 62 years, coal - 230 years.
Fuel | Traditional | General | 2000 consumption, at Mtoe |
---|---|---|---|
Oil, billion t | 140 (120-155) | 320 | 3430 |
Natural gas, trillion m³ | 146 | 270 | 2220 |
Coal bituminous and brown, then bn | 690 td> | 10125 | 2240 |
Uranus -. 235, kt | 3200 (reserves) | 5100 |
There is no doubt the global solution of the energy problem is connected with the search for new forms of energy is practically inexhaustible and clean, but they appear to the use of traditional sources should be accompanied by well thought-out energy-saving policies. It is well known: to save a ton of raw materials, fuel and materials, you need to spend 3-4 times less money than getting the same tonne of primary resources.
The main energy-saving components are:
-restructuring of the economy; shift to less energy-intensive manufacturing, high-tech products;
-specialization and cooperation of production within the industry and between industries;
-transition to a new energy-efficient technologies and equipment in all sectors of the economy;
-improvement in the fuel and energy balance structure;
-highly energy management (energy audits).
In the issues of improving the methods of energy audits and make recommendations to reduce the specific fuel consumption is invited to consider the example of the analysis of the company PE "Volnovahamezhrayteploset". "Donetskteplokommunenergo" The company is located in g.Volnovaha and a production unit (PU) utility. Direction of activity - supply of steam and hot water. PE is composed of 6 production sites: Volnovaha - 10 U n Olginka - 1 units, item Novotroitskoye - 2 units, n Vladimirovka - 1 units, item Mangush - 4 units, Dokuchaevsk - 4 units, ie, all on the balance sheet is 22 boiler.
2. The purpose and objectives of the study
To determine the effectiveness of the use of energy consumed, the choice of ways to reduce wasteful energy consumption information for an objective assessment of energy consumption both in volume and in value terms, is necessary to conduct energy inspections (energy audits). These survey by independent expert groups allow to objectively evaluate the level of efficiency of use of energy resources in the enterprise and to identify appropriate measures for energy efficiency.
The main purpose of the audit is a comprehensive analysis of all facility power systems to determine potential energy savings and to identify the main directions of its implementation, as well as to develop measures and technical solutions that reduce energy consumption and, as a consequence, the financial costs to pay for the fuel - energy resources.
Energy Auditing is required for all companies, organizations and enterprises regardless of their organizational-legal forms and forms of ownership at least once every 5 years, and on the results compiled and updated energy performance certificate.
Energy audit suggests the following methodological steps:
Primary overview static, documentary and technical information on all types of energy of the company and making the energy audit program;
metrology (instrumental) and thermographic inspection of all consumers of thermal and electrical energy;
Study of the heat balance of the enterprise;
treatment received or collected information and analytical review of all types of energy-related activities of the enterprise;
energy efficiency rating of heating, thermal power and thermal technological equipment, heat-generating plants, heating and ventilation systems, hot water supply, steam supply, condensate collection and return, cooling, power supply, the use of secondary energy resources;
Development of the main recommendations and actions on energy efficiency, fuel accounting, water, electricity and thermal energy;
report design and preparation of energy certificates.
One of the terms of the effects achieved for the modernization or improvement of operation of boiler is potential savings of fuel or thermal energy. Performance and commissioning works in the boiler room allows to identify deficiencies in the condition and operation of boilers, to identify and implement a set of measures to increase efficiency: to optimize the levels of excess air in different parts of the gas system, flue gas temperature, set the water treatment regime, which provides a minimum formation of scale on the internal heating surfaces , et al.
In most types of boilers gas path is under vacuum. In the upper part of the furnace, it is about 20-30 N / m² (3.2 mm of water column) and increases with the resistance heating aerodynamic surfaces placed after firing. Since the design of the boiler leaks are present at the interface with the individual elements lined, when its operation take place always cups cold air into the combustion chamber and other parts of the gas path. Influence of the suction stronger than they are closer to the furnace.
The thermal performance of boilers significantly depend on the level of excess air in the furnace. If the excess exceeds the norm (as established on complete combustion conditions), then reduced the temperature in the furnace, reducing heat absorption of the radiation heating surfaces, increasing the enthalpy and volume of gas in front of convective heating surfaces. As the excess air in the furnace due to the increase in their relative suction increasing heat absorption behind enthalpy increase, resulting in higher flue gas temperature, i.e. reduce boiler efficiency. At the same time increase the cost of electricity on Forced draft installation due to the increase in volumes of gas to be allocated.
If the level of air suction into the furnace is 10-20%, the flue gas temperature rises by 3-8 °C. The same level of air suction in the duct tail heating surfaces does not affect the operation of the furnace, but it lowers the temperature of the exhaust gases at 8-14 °C and increases their volume.
The increase in excess air in the combustion chamber during combustion of solid fuels as a result of lowering the temperature in the furnace also leads to an increase in losses due to mechanical incomplete combustion (q³).
Power boiler with cold water leads to damage to the heating surfaces, it promotes the formation of scale. By reducing the feed water temperature against the calculated values and the constant flow of steam from the boiler is always required to increase fuel consumption, even though the gross efficiency of the boiler practically does not change. By reducing the feed water temperature and flow rate constant gross fuel boiler efficiency increases while reducing steam. Reducing the feed water temperature leads to water in economizers underheating nekipyaschego type economizer section and increased screen surfaces. So, for the sake of high efficiency and reliability of boiler plants Boiler feed water must be pre-heated. For steam boilers always effective is the use of the condensate return from the consumers. In addition, hot water or steam spent flue gases allows to keep another part of the heat that would be lost.
feed water supply with a high temperature in the economizer leads to a decrease in its heat removal and increase exhaust gas temperature. Therefore, there are various ways of lowering the water temperature after atmospheric deaerators to 70-80 °C, and the practice of application of vacuum deaerators in which water boils at a temperature of 54-70 °C.
For steam boilers equipped with economizers, it is important to maintain the operating pressure of steam at the level calculated. Many enterprises boilers rated operating pressure of 9-13 atm operate at reduced pressure, which leads to a waste of fuel and limits the ability to preheat the feed water economizer nekipyaschego type using heat of exhaust gases. There is an optimum value of the difference between the temperature of saturated steam in the boiler drum and the water temperature at the outlet of the water economizer. By reducing the operating pressure in the boiler to 5 am instead of 13 at the nominal value of fuel losses reach 6%.
When throttling steam to the pressure conditions necessary for consumers, reduction plants are losing place. However, they are substantially less than those discussed above. Furthermore, when reducing its vapor temperature almost constant, which allows it to produce the superheated state.
In order to improve the efficiency of boilers, in which the operating pressure exceeds the desired boiler to consumers, reduction-cooling equipment (DOC) is replaced by low-power turbines. The introduction of such turbines is useful when loading existing customers and allows heat to provide a combined power output of heat-consumption with high efficiency.
For each of the sizes of boilers exist characteristic depending on the efficiency of the load. Usually its maximum value occurs in the region of 80-90% of the nominal load. By reducing the load it is reduced by increasing the relative flue losses, increasing the excess air in the furnace, and others. For boilers have technical limitations of minimum load on the circulation conditions. Boiler operation in the forced mode is also accompanied by an increase of heat losses and decrease efficiency. Individual characteristics change boiler efficiency of the load used in the boilers in the distribution of load between the boilers and the choice of their working staff. When selecting staff operating boilers are taken into account the feasibility of their stop and start, and other limiting factors.
3. Expected results
As one of the options to improve methods of energy audits and processing of the results it is advisable to each inspected object be calculated for heating depending on the fuel consumption (heating) of buildings in graphical and tabular form. For their construction materials can use the energy source projects and buildings, or normative and methodological materials, for example, [2], where the technique of determining the amount of heat energy required for the planning period:
Q = a · V · q · (tb - th) - (1 + Kip), kcal / h (1)
where Q - design hourly heat the building heating load (buildings), kcal / h; a - correction factor of 0.95; V - volume of the building (object) on the outer measurements, m³; q - the specific characteristics of the building heating, kcal / (m ³ · hr · °C) (for the lower of the case q = 0,45 kcal / (m ³ · hr · °C)); TV - indoor air temperature, °C; ti - ambient air temperature, °C; Cyrus - current infiltration coefficient determined by the formula:
Cyrus = 10-2 · {2g · L · [1 - (273 + ti) / (273 + ti)] + W³} °C, 5 (2)
where g - acceleration of gravity, m / s²; L - building height, m; W - the estimated wind speed for the area during the heating period, m / s (take 3 m / s).
Given that the settlements of the heat conducted by prescription, for example, the natural gas flow meter on the calorific value (Qnr) which are regularly informed consumers of thermal energy in the fuel consumption of express terms, m³ / h:
A = Q / Qnr - bp, (3)
where ηbp - Gross efficiency of boilers according to the regime maps.
The results of calculations are shown in the figure. In the range of outdoor temperature changes by about -12 ° been uprated fuel consumption for heating, an average of 24-26%.
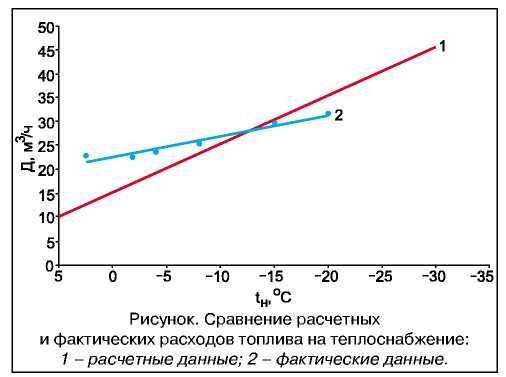
The data documenting the survey work on the boiler actual fuel consumption in a lowest possible temperature graph of heating system 62-60° in a straight line and 56° in reverse (for boilers working conditions with quality regulation) show that a temperature schedule is quite admissible only at ambient temperatures from -12 to -20°.
Therefore, it can be shown experimentally that when outside air temperatures up to -10-12°C; necessary to organize the combined or quantitative regulation of heat network operation [1-4], which will save at least 25% of fuel consumption. Such schemes are widely tested in practice [9].
In order to calculate the cost of heat and electricity is proposed to use several techniques: with aggregate and detailed calculations, including the hourly schedule of consumption of heat and electricity and the average daily temperature fluctuations.
Any district heating is divided into 3 main components:
- the source of heat (boiler);
- the transportation of thermal energy (heat networks);
- heat system.
Each of the above components has a characteristic unproductive losses reduction which is the main energy-saving function.
Based on the data obtained in the course of instrumental measurements in the stage heat and power audit for boilers, heat transfer equipment, thermal and electrical networks, as well as data documenting the boiler operation Survey calculates the indicators characterizing the boiler operation.
During normal operation the heat source, there are always three types of major losses:
- with unburnt fuel and exhaust gases (usually bolee18%), loss of energy through boilers setting (no more than 4%) and the loss to the blowing and boiler auxiliaries (about 3-8%). These figures are close to the heat losses of about normal for no new domestic boiler (with an efficiency of about 75%). More sophisticated modern boilers have a reasonable efficiency of about 85-90%, and the standard for these losses are lower.
Increase efficiency of operation of an existing boiler by reducing heat loss in the general case can be represented as a series of specific actions and general recommendations to reduce the specific fuel consumption (in order of effectiveness):
¹ | Name of event | Limits of annual savings,% |
---|---|---|
1 | Conducting regime commissioning of boilers with the inventory of emissions. Working regime of the boiler card at various loads and actions that will ensure job boilers only in economy mode. | 5 - 10% of the fuel consumed |
2 | Maintaining an optimal air-fuel ratio and good mixing it with the fuel conversion burner nozzles under real load | 1 -3% |
3 | Installation of surface water economizer for boiler | 1 - 3% |
4 | Conducting comprehensive examination of boilers, including combustion gas analysis products. The use of heat recovery boilers deep installations, installations use latent heat of vaporization of exhaust flue gases (contact heat exchanger) | 15% |
5 | Increase feed water temperature at the inlet to the boiler drum. | 2% for every 10 ° C |
6 | feedwater heating in a water economizer | 1% to 6 ° C |
7 | Contents clean exterior and interior of the boiler heating surfaces | 10% |
8 | Use of thermal emissions from the boiler through the fence of warm air from the upper zone of the boiler room and feeding it into the suction blowing fan line | 1 - 2% |
9 | Thermal insulation of external and internal surfaces of boilers and heating pipes, seal valves and boilers tract (the surface temperature of lining should not exceed 55 ° C) | 10% |
10 | Translation boilers to gas | the cost of 1 Gcal 2 - 3 times reduced |
11 | Installation of modern systems of accounting for fuel costs, elec-tricity, water and heat supply | 20% |
12 | Equipment boiler work control and regulation devices, the optimal setting of boiler automation. | 30% |
13 | Equipment boiler efficient and economical pumping equipment, reliable pipeline shut-off and regulating valves. The use of frequency drive to control pump speed, fans and smoke exhausters. | 30% of the electricity they consume |
The heat energy transferred to the heat carrier in the boiler flows into the heating main and should be on the consumer objects. The value of the efficiency in the area of heating networks are usually defined as follows:
- network efficiency pumps for the propulsion of the coolant for the heating pipes;
- heat losses along the length of heating related to the process of laying and pipe insulation;
- the thermal energy losses associated with the correct distribution of heat between objects-users, the so-called mood hydraulics of a heating;
- recurring during emergency and abnormal situations coolant leaks.
When intelligently designed and hydraulically adjusted of heating system, the removal of the end-user from the site of energy production is rarely more than 1.5-2 km and the total amount of loss usually does not exceed 5-7%.
The reduction of heat loss and improve the efficiency of the heating duct in general, can also be represented as a series of specific actions:
1. Conducting a comprehensive survey of heating from the boiler to heat the objects and identifying the main channels appear in their thermal losses.
2. Carrying out hydraulic adjustment of heating with shaybirovaniem consumers actually consumed their thermal load.
3. Restoring or strengthening the thermal insulation of a heating or feasibility relining existing pipeline used to replace the pre-insulated pipes.
4. For domestic hot water systems to ensure the circulation of the circuit. If possible, equip consumers Heat points Heat plate heat exchangers for domestic hot water needs.
5. Replacing inefficient domestic network pumps for modern higher-efficiency. If the economic feasibility (high power pump motors) must use the frequency control device asynchronous motor speed.
6. Replacement of valves on the track, using modern reliable butterfly valves that significantly reduce heat loss in abnormal and emergency situations, as well as eliminate the options of visiting leaks coolant through the valve seals.
The most significant components of the heat loss in the heating system are loss-consuming installations. The presence of such is not transparent and can be determined only after the consumers of heat heat meters.
In general, the improvement of the situation of energy consumption at the site of the consumer, taking into account the real possibilities of their implementation, as follows:
¹ | Name of event | The limits of the expected decline in the total heat loss,% |
---|---|---|
1 | Troubleshooting ventilation losses by eliminating excessive infiltration. | from 28% to 9,8% |
2 | Reduced heat loss through the filling of windows and doors. | from 15% to 4,5% |
3 | Thermal insulation of the basement. | 9% to 3,6% |
4 | Warming of the attic. | from 6% to 2,4% |
5 | Setting an automatic flow control system for heating the coolant, depending on weather conditions. Using the "weather" regulation can reduce heat consumption while increasing comfort in the buildings. | Reduction of 10-15% |
6 | If possible, heaters equipment radiator controls room temperature, which makes it possible to reduce building heat load. | Up to 10 - 20% |
7 | Ensuring reliable operation of DHW circulation inside the facility, which will save thermal energy spent on heating water. | Up to 25% |
8 | Ensuring efficient operation of the temperature control to hot water boilers. | Up to 15% |
This list can be expanded to:
1. Installations of thermal energy meters for heat consumption objects. The appearance of the heat consumption pattern over time will make it possible to analyze the situation and choose the most efficient way to heat energy use.
2. Flush the heating system.
3. Settings "hydraulics" internal heating system using shaybirovaniya or balancing valves, circulation pumps. If necessary - amend the scheme of connection of heating appliances and possible - the use of more efficient radiators.
4. Equipment substation reliable and modern stop and control valves.
5. Audits of existing boilers and hot water, if necessary - replacing them with highly efficient plate heat exchangers.
6. Locations where necessary complex of works on exterior insulation walling buildings.
For the realization of this potential energy saving is needed, distributed multi-level system of regulation of heat buildings. A comprehensive energy audit and specification of the heat balance of buildings in the balance sheet of the boiler, have revealed differences of real power with the contractual values, to propose a set of measures reducing energy consumption, an extensive system of regulation. Buildings with the data values of thermal resistance of the walls (1,15-1,5 m²;K / W) hold quite acceptable heat, leading in some cases to "melt down"; during energoobsledovany revealed significant values of "melt down" buildings within 13-15%.
More research communication modes of heat and humidity in areas with features heating operation were carried out in order to clarify these issues in buildings. The experimental results generally confirmed the assumptions about the correction of the specific characteristics of heating adopted earlier calculations of heat balances of buildings in almost the entire range of the outdoor temperature. The values of the specific costs of heating of buildings with different thermal resistances fences are virtually identical because determined exclusively modes of functioning of the heating system, the mixing units work at the entrance to the building and hydraulic characteristics of specific objects. Significant variation in the obtained values of specific energy consumption per heating season is once again evidence of an unbalanced system of work in separate houses, and all the consumers in general.
is supposed to clarify the structure of the criteria, specific parameters describing the heat and power supply systems of buildings (thermal density, specific length, specific losses during transportation, etc..) To determine the maximum energy losses and, accordingly, the energy saving potential based on the analysis of survey data of some objects.
All of these factors lead to the need for correction of energy certificates of buildings. Correction of energy passport of the building is suitable to detect the direction of the functional efficiency of the building and its engineering systems components. Certification of buildings as a result of energy audits should provide a clear understanding of the effectiveness of the building in terms of the degree of achievement of optimal parameters. At the same time the concept of "optimal" building a thermal power multilevel system also requires additional theoretical and methodological study.
5. Conclusion
The growth of the economy should not be constrained by energy deficiency, therefore saving today only and non-alternative instrument that in a much shorter time and the least expensive way (in comparison with the construction of generating capacity) can allow to reduce power consumption without reducing the rate of growth of the industry and construction, and to achieve reduction of energy intensity of GDP.
The economic effect of the introduction of energy saving measures, and the other, it is possible to increase the methods of quality systems based on the analysis, through planning and cost management, the moment and the timing of implementation and other techniques. For example, you can evaluate the effectiveness of the use of the boiler room for the heat output rental 1 Gcal of heat given to the area of 1m²; and 1m³; volume space, and efficient use of fuel boilers.
Based on the experience of implementation and operation of modern automated boilers, reconstruction separately selected boiler with their translation in class boilers, having the same dimensions, but with higher heating efficiency and fuel utilization factor would improve the provision of thermal capacity of the existing boiler and further to take the load, freeing up obsolete boilers in the power reserve or eliminating them.
An analysis of the boiler room layouts, teplopunkt or other object types and dimensions and weights of equipment can significantly reduce the occupied area of objects that allows you to optimize costs and get the greatest benefit in the operation and in the new construction of real estate, especially in large cities.
If you consider that over the decades has changed the heat consumption of the structure and composition of consumers, load themselves, it is advisable to revise the scheme of heat supply of cities and regions in the whole complex of energy audits, especially since this sector is diverse and has a high investment attractiveness.
list of references
- Ganja VL Basics of energy efficiency: theory and practice energy conservation / VL Ganja. - Minsk: Belarusian. Science, 2007. - 451 p. - ISBN 978-985-08-0810-3.
- Energy audits - the way the real energy savings and more profit: Manual (standard documents, information - reference materials) / ed. THOSE. Trinity-Markov et al. M .: Sport and Culture, 2002. 209 p.
- Basics of energy conservation: the textbook / NI Danilov, JM Liquors, ed. NI Danilova. Yekaterinburg: SEI HPE Ural State Technical University, 2006. 564 p.
- Fokin VM Basics of energy conservation and energy audits. M: "Publisher Engineering 1", 2006. 256 p.
- Thermal Engineering Handbook / Ed. VN Yureneva and PD. Lebedev. T. 1.m .: Energy, 1975. 744 p.
- Transfiguration NI Control over the efficient use of gas. L .: Nedra, 1983. 368 p.
- Kachan AD Modes of operation and maintenance of thermal power plants. Mn .: Executive. School 1978. 288.
- Thermal design of boiler units (Normative method) / Ed. NV Kuznetsova. M .: Energia, 1973. 296s.
- Roddatis KF Boilers. M .: Energy, 1977.432 with.
- ESCO ESCO Electronic Journal "Ecological Systems» ¹ 5, May 2005.