Реферат за темою випускної роботи
Зміст
- Вступ
- 1. Актуальність теми
- 2. Мета і задачі дослідження
- 3. Огляд дослідження
- Висновки
- Перелік посилань
Вступ
Дослідження процесів, що відбуваються під час продування сталеразливочного ковша інертним газом є дуже актуальною темою в сучасній металургії. Завдання отримання високоякісної сталі або сплаву, придатних для виготовлення відповідальних виробів, зводиться до розробки такої технології виплавки, розкислення і заключного етапу обробки, які можуть забезпечити мінімальне залишковий вміст шкідливих домішок, газів і неметалевих включень.
1. Актуальність теми
Завдяки дослідженням в цій області ми можемо з'ясувати: оптимальне розташування продувних отворів; необхідний витрата вдуваемого газу; визначити ймовірний знос футеровки, в залежності від розташування продувочного отвори і інтенсивності продувки. Дані дослідження дозволять оптимізувати витрати газу, збільшити термін експлуатації футерування сталеразливочного ковша. На сучасному етапі розвитку сталеплавильного виробництва обов'язковою операцією позапічної обробки стали є перемішування розплаву в ковші. Відомо, що в поєднанні з перемішуванням швидкість рафінування металу істотно зростає, стає можливим реалізація ефективного дугового нагріву і вакуумної обробки раскисленной стали. Більш того, шляхом перемішування досягаються необхідні за умовами розливання ступінь однорідності металу по температурі і хімічним складом, які в значній мірі визначають техніко-економічні показники процесу виробництва.
2. Мета і задачі дослідження
Ми провели дослідження за існуючою математичної моделі, яка виконана в прикладному пакеті Ansys. Дана модель повною мірою дозволяє оцінити гідродинамічний і тепловий стан розплаву.
Основні завдання дослідження завдяки отриманню векторних картин швидкостей руху розплаву на двомірної моделі, що дозволяє кількісно оцінити характер переміщення рідини. У даній моделі використовувався метод кінцевих елементів. Розвиток технологічних систем позапічної доведення сталі в ковші обумовлює необхідність оптимізації умов перемішування металу в ковші, яке, як правило, здійснюється шляхом вдування в розплав деякої кількості інертного газу (аргону). Особливо, це питання раціонального перемішування металу в ковші при продувці аргоном, є актуальним при роботі установок ківш-піч. Це пояснюється тим фактом, що в ковшах, використовуваних на УКП, передбачається, як правило, один - два (рідше три) продувних вузла, розташування яких регламентується певними технологічними міркуваннями. По-перше, продувні вузли необхідно розташовувати таким чином, щоб повітря, що вдихається в метал аргон не потрапляв в зону роботи електродів, що використовуються для підігріву металу і шлаку. По-друге, один з продувних вузлів повинен розташовуватися в зоні подачі феросплавів, що забезпечить високу ступінь їх засвоєння. По-третє, продувний вузол не може розташовуватися в зоні падіння струменя металу під час наповнення ковша. По-четверте, продувний вузол не може розташовуватися поблизу стінки ковша, оскільки в цьому випадку буде відбуватися підвищений знос вогнетривів в області поширення висхідного потоку. По-п'яте, в залежності від технологічної послідовності операцій, що виконуються на агрегаті ковша, інтенсивність продувки металу аргоном може змінюватись в значних межах. Тому основним завданням даного дослідження є встановлення оптимальних режимів перемішування розплаву в процесі обробки його на УКП, які б дозволили вирішувати такі проблеми:
- визначення оптимальної кількості продувних вузлів і їх положення в днище ковша.
- запобігання виникненню застійних зон у ванні рідкого металу в ковші.
- визначення умов, відповідних раціональної інтенсивності перемішування відповідно до технології обробки металу в ковші.
- оптимізація умов взаємодії (перемішування) металу і шлаку в процесі продувки.
Процес перемішування рідини в замкнутому просторі є складним фізичним явищем. Для того, щоб проаналізувати це явище відносно конкретної технологічної задачі представляється доцільним використання певних критеріїв, які дозволяють виконати порівняльні оцінки на макро- і мікрорівнях. В рамках оцінки ефективності перемішування певного об'єму рідини найбільш часто використовуються інтегрований показник «інтенсивність перемішування» (час перемішування). Інтенсивність перемішування металу в ковші представляється дуже важливим технологічним показником при обробці стали на УКП. По-перше, інтенсивність перемішування металу визначає тривалість деяких етапів обробки, в тому числі гомогенізації металу по хімічному складу і температурі або процесу рафінування металу шлаком. По-друге, процес перемішування металу газом відбувається досить складно, і в рідкій ванні утворюються як зони інтенсивної циркуляції, так і «застійні області», прояв яких може негативно відбиватися на кінцевих показниках обробки в цілому. По-третє, використання аргону як субстанція, яка забезпечує процес перемішування, допускає додаткові витрати на обробку і відповідно зменшення кількості аргону їх, що використовується, знижує. З урахуванням всіх цих особливостей, було прийнято рішення, що дослідження будуть проводитися на «холодної» водної моделі. Основні завдання фізичного моделювання щодо справжньої роботи можна сформулювати таким чином:
- вивчення особливостей перемішування рідини в ковші при її продування газом через пористі блоки, встановлені в днищі.
- вивчення можливості оптимізації основних робочих параметрів вдування газу (інтенсивність, кількість продувних блоків, розташування продувних блоків і т.п.) для забезпечення процесу перемішування раціональної інтенсивності.
- вивчення особливостей перемішування металу з шлаком в процесі продування металу газом.
3. Огляд дослідження
Фізичне моделювання процесів перемішування рідини найбільш переважно при збереженні однакових геометричних розмірів досліджуваного агрегату і моделі. З огляду на той факт, що при вдування газу в рідину вельми важливими представляються процеси, що відбуваються під дією сил тяжіння, які визначають спливання бульбашок газу, і сил інерції, які визначають розвиток системи циркуляційних потоків в рідкій ванні ковша, в даній роботі як базові критерії подібності був прийнятий критерій Фруда і критерій гомохронності. Фізичне моделювання процесу перемішування розплаву інертним газом в ковші виконане на прозорій моделі, що дозволяє візуалізувати всі основні процеси, які відбуваються під час продування рідини. Геометричні розміри місткості, яка імітує сталерозливних ківш, були обрані наступними: діаметр (верхній) - 0,6 м, діаметр (нижній) - 0,55 м висота - 0,75 м. При цьому передбачалася, що вибрана місткість забезпечить моделювання процесів перемішування для ковшів різної конструкції (в першу чергу, відносини висоти наливання металу до діаметру ковша). При цьому як моделює рідина використовували воду при температурі 18-25 °С і при відповідній в'язкості силіконового масла. Вибір води як моделює рідина пояснюється тим фактом, що значення в'язкості води і стали в області температур позапічної обробки достатньо близькі один до одного. Перемішування рідини здійснювали стислим повітрям. Для імітації шлаку, розташованого на поверхні металу, використовували масло силікону, яке, як відомо, має високі значення поверхневого натягу, а в'язкість може варіюватися в досить широких межах залежно від його температури. Щільність обраного масла силікону склала 965 кг/м3. Як критерій ефективності перемішування рідини в ковші був прийнятий показник інтенсивності перемішування, який визначається як час гомогенізації об'єму рідини в ковші. Час гомогенізації визначалося як період, необхідний для досягнення відповідної високої однорідності системи, необхідної з технологічної точки зору. Найбільш точним методом вимірювання часу перемішування є електрохімічний метод з введенням в перемішувати рідину (воду) невеликої кількості розчину солі і вимірюванням електропровідності в одній або декількох точках обсягу ковша. При цьому значення часу перемішування є найвищими, в порівнянні з іншими методами, а точність вимірювань складає ~ 5%. Електрохімічний метод вимірювання часу перемішування був реалізований наступним чином. Геометричний масштаб фізичних моделей визначався з урахуванням критеріїв подібності Фруда і гомохронності і склав 1: 6 по відношенню до вибраного модельованого об'єкту - установка ківш-піч місткістю 160т. Для візуального спостереження газорідинних потоків стінки моделей виконували з прозорого скла, а масла силікону підфарбовували спеціальним індикатором для колірного відмінності від води. Спостережувані картини перемішування фіксували за допомогою цифрової відеокамери. Експериментальні установки дозволили регулювати витрату газу і змінювати положення продувних пристроїв щодо вертикальної осі судини. У процесі дослідження було знято близько 250 фотографій процесу перемішування для різних значень витрат і швидкостей вдуваемого газу, які змінюються в інтервалі 0,5-2 л / хв. В якості електроліту, що вводиться в воду, застосовувався насичений розчин кухонної солі. Електропровідність вимірювалася двома датчиками, кожен з яких представляв собою два платинових електрода, між якими пропускався електричний струм. Електроди, виготовлені з платинового дроту діаметром 0,3-0,5 мм, закріплені в ізоляторі, герметично зчленування в пустотілому тримачі, всередині якого пропущені з'єднувальні дроти, припаяні до електродів. Датчики розташовувалися в діаметрально протилежних точках під стінами моделі ковша на висоті 0,2 і 0,8 висоти наливу води в моделі. Перевагою такої схеми є те, що вихідний сигнал являє собою різницю між показниками датчиків, а, отже, дозволяє більш точно судити про те, в якому ступені здійснилася гомогенізації електроліту в об'ємі ковша. Застосування платинових електродів обумовлювалося необхідністю запобігання окислення поверхні електродів в сольовому розчині, що значно знизило б точність вимірів. Була розроблена єдина для всіх експериментів методика вимірів часу перемішування, яка полягала в наступному. Електроди поміщаються в різні точки моделі і закріплюються. При необхідності виконується балансування моста, в результаті якої сигнал надходить з АЦП повинен знаходиться приблизно на одному рівні, що дає нам «майданчик» (зазвичай це 3,5 - 4 мВ) від якої можна відмірювати максимальне відхилення при введенні електроліту. Вводиться індикатор (розчин кухонної солі) під електрод, розташований на висоті 0,2 висоти наливу води. Це пов'язано з тим, що існує зона застою, де перемішування майже не відбувається. Ця зона знаходиться під довгим датчиком, а розчин кухонної солі ми вводили на короткий електрод. При введенні індикатора на графіку спостерігається різкий стрибок до значень в середньому 15 - 20 мВ. Це свідчить про те що опір «плеча» до якого підключений довгий електрод, різко зменшується, що викликає розбалансування моста, з цього моменту можна почати відлік часу усереднення і розчинення цієї добавки в обсязі ковша. У міру розподілу концентрації розчин значення мВ починає знижуватися до вихідних 3,5 - 4 мВ. Як тільки воно стабілізується, можна говорити про повне розчинення індикатора, що свідчить про закінчення виміру часу перемішування. Таким чином, за час перемішування рідини приймається відрізок часу, протягом якого амплітуда записуваного сигналу знижувалася зі свого пікового значення до мінімуму. А оскільки графік по лінії абсцис розбитий на рівні проміжки, завмер часу перемішування не складає особливих труднощів. Запис проводився за допомогою мостової схеми з підсилювачем, підключеним до аналогового цифрового перетворювача (далі АЦП), а з нього вихід на комп'ютер. За допомогою спеціальної програми будується графік, який потім зберігається у вигляді зображення. Вимірювальна схема для контролю часу перемішування рідини повинна включати міст, два плеча якого утворені однаковими безиндукціонность опорами R1 іR2 по 3 кОм кожне, а до двох інших плечах приєднані електроди R3 і R4. Змінний опір R5 служить для балансування моста перед початком вимірювань. Мостова схема повинна харчуватися змінним струмом, оскільки напруга постійного струму викликає помітну велектролітичні реакцію, що призводить до зменшення струму між електродами. Найчастіше застосовується змінна напруга 4В, що прикладається до однієї з діагоналей моста. Напруга, що знімається з іншої діагоналі моста, подається на випрямляч, до якого підключений самописець для реєстрації електричного сигналу. Вхідний в схему мікроамперметр необхідний для балансування моста і поточного запису сигналу. Посилаючись на експериментальні дані і результати регресії, представлені досі, можна відзначити, що явище потоку при газовому перемішуванні є невід'ємно перехідним. Тому, умова тривалий і короткострокове блукання струменя, безперервно відхиляється, роблять потік перехідним, що впливає на вимірювання. Ситуацію посилює два барботують устрою застосовувані замість одного. В рівній мірі важлива траєкторія вводиться індикатора, яка істотно відрізняється в ковшах різних розмірів. Траєкторія індикатора не була виразно відтворена і істотно залежала від блукає струменя. Це ймовірно включає деяку помилку у вимірах і невизначеність в кінцевих висновках. Відхилення лінії проведеної через експериментальні точки можна віднести до притаманному характеристикам газового перемішування і процедури експерименту.
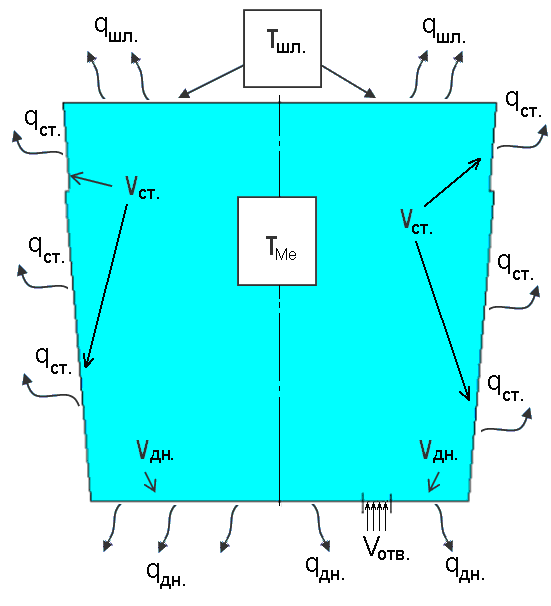
Рисунок 1 – Схема внутрішньої порожнини ковша з початковими і граничними умовами
Висновки
Після аналізу отриманих даних ми можемо зробити висновок про характер руху потоків металу. Найбільші швидкості розплаву спостерігаються в висхідній області потоку, в близькості від продувних отворів, далі потік металу розвивається, залучає великі шари металу в рух, і формуються циркуляційні зони. Процес стабілізується. Найбільш повне перемішування розплаву спостерігалося при продувці через два продувних отвори зі зміщенням продувних отворів rn/Rн = 0,6...0,95, тобто ближче до стінок ковша. В цьому випадку спостерігався рух потоків металу уздовж футерування ковша, що є сприятливим фактором, так як найгарячіші верхні шари металу попадали в осьову зону рідкої ванни. При такому розташуванні продувних отворів спостерігалася невелика частка малоскоростной потоків, які розташовувалися в придонному частини і в зоні шлакового пояса. Завдяки всім цим факторам спостерігався менший знос футеровки шлакового пояса і мінімізація залучення шлаку в глиб розплаву. Так само дослідження показали, що зміна інтенсивності продувки практично не вплинуло на характер перемішування розплаву. А найбільш інтенсивному впливу потоків металу схильна робоча футерування ковша трохи нижче шлакового пояса. Однак, не дивлячись на це, дане розташування продувних отворів є найбільш оптимальним.
При написанні даного реферату магістерська робота ще не завершена. Остаточне завершення: травень 2017 року. Повний текст роботи і матеріали по темі можуть бути отримані у автора або його керівника після зазначеної дати.
Перелік посилань
- А.Н. Смирнов, Е.В. Ошовская, И.Н. Салмаш, В.М. Сафонов, К.Е. Писмарев Некоторые вопросы оценки интенсивности перемешивания при продувке металла в ковше инертным газом // «Металл и литье» - № 3 – 4, - 2007. – с. 44 - 49
- D.Mazumdar, H.B.Kim, R.I.L.Guthrie. Критерии моделирования потока при обработке металла в сталеразливочном ковше с газовой продувкой: экспериментальное исследование // - Ironmaking and Steelmaking. 2000 - Vol.27. No4. - P.302-308
- M.Iguchi, K.Takanashi, H.Kawabata. Модельное изучение свойств жидкостного потока в резервуарах с донной продувкой при возникновении обратного эмульгирования // - ISIJ International. - Vol.38 (1998). No.10 - pp.1080-1085
- M.Iguchi, K.Takanashi, O.Ilegbusi Влияние физических свойств верхнего масляного слоя на характеристики газожидкостного потока в резервуарах с донной подачей газа //- ISIJ International. Vol.38 (1998). - No.9. - pp.1032-1034