Abstract
Content
- Introduction
- 1. Theme urgency
- 2. Goal and tasks of the research
- 3. Review of existing frequency converters
- 3.1. Frequency converters with direct connection
- 3.2. Frequency converters with DC current
- Conclusion
- References
Introduction
The problem of rational use of electricity was and remains urgent especially in industry. The main consumers of electricity in the production are three-phase AC motors, namely asynchronous motors with squirrel-cage rotor (AM). The massive use of this type of engine due to reliability, cheapness and ease of operation. The disadvantage of these motors is that their speed depends on the design of the motor and the mains frequency. Before induction motors were used, as a rule, in the unregulated electric drives, the start of which was carried out by direct inclusion in the network. Direct start (DS), AM is not effective, since at start-up creates a large inrush current, which has a significant load on the supply network causing a significant voltage drop and increasing energy loss, and also accompanied by electrodynamic and thermal overload of windings, which reduces long-term engine operation. Partly to address the shortcomings of DS can limit the starting current for this series with the stator windings include a series resistor or inductance. Also used the auto transformer start and start with switching the stator winding from star to triangle. These methods allow you to limit inrush current, but does not provide smooth starting and speed control, AM. The solution of these problems is the use of soft start devices, which allow to improve the transients during the start-up and provide the ability to generate the required smoothness of acceleration and deceleration or frequency converters (FC) for regulating not only the smoothness of the acceleration and speed of the motor [1].
1. Theme urgency
One of the main objectives of process improvement in industry is to minimize energy consumption and security, in both equipment and technical staff.
The use of frequency converters systems adjustable speed drive, allows you to automate the entire operation of the electric motor: start, braking, reverse and change speed automatically smoothly including the starting resistance, which provide current regulation within the required limits. The feature of using converters in drives with AM is that they control the motor speed in accordance with the nature of the load, this reduces the sharp voltage change in the power supply and increase the economy of energy consumption, and also reliability of the drive [2]. Most modern FC's have a simple interface and input and output unified signals, which enable connect to external management systems a higher level of remote control devices and information display. The possibility of modulating the speed allows you to refuse the majority of gears used in the drives, this further increases the reliability and reduces system cost.
The development of technologies in the field of semiconductor devices and microprocessor technology allows currently to build frequency converters, which are low cost, high reliability and wide functionality. The majority of industrial enterprises located on the territory of the CIS, require either replacement of the obsolete automation and control, or even a transition to automated production, so this problem is relevant [3].
2. Goal and tasks of the research
The aim is to increase the efficiency of operation of the frequency Converter drives of mining machines by establishment and scheme design and optimization of control algorithms.
The main objectives of the study:
- Analytical review of well-known schemes, identify their advantages and disadvantages.
- The choice of optimal designs.
- Development of a mathematical model of the Converter.
- Research of operation modes of the inverter model to determine the required control algorithms.
3. Review of existing frequency converters
3.1 Frequency converters with direct connection
Historically, first came the converters with direct connection. They output voltage is formed of sections of sine waves of the mains voltage supply, with the engine in the process of operation of the Converter using the public keys in each moment of time is connected directly to the power source. This allows the use of additional devices to provide two-way exchange of energy between AM and the mains supply, which in turn creates the possibility of engine operation in two quadrants of mechanical characteristics. NFC can in principle be based on partially or fully-managed keys. In the first case, as keys use thyristors (triacs) with natural commutation (NC); in the second or fully-controlled thyristors or thyristors with artificial switching, or transistors. The use of artificial switching allows you to adjust the output frequency in the area below and above the network frequency. However, a switching device thyristor keys significantly impair the weight and overall dimensions. The use of transistor switches eliminates this disadvantage, but the principle of operation of NFC requires the use of at least triple the number of key elements compared to the inverter with the inverter. In addition, for some tasks in NHR use input or output transformers, which further reduces their competitiveness. Therefore, in converters of this type are most often used natural commutation and apply them in drives where the apparent advantages of the thyristor key in the drives of large capacity [5]. A functional diagram of a frequency Converter with direct coupling is shown in figure 1
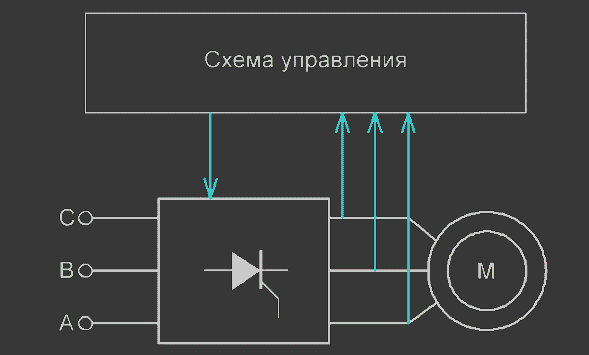
Figure 1 – Functional diagram of the frequency Converter with direct connection [4]
With the help of three phase-three phase NC NFC is possible to form the phase currents of hell with a distortion factor of the order of 0.99-0,9999, i.e. currents, contains almost only the basic harmonic. However, with the increase in the frequency of the main harmonic distortions increase when the power supply of 50 Hz limits the output frequency with a satisfactory range of current is considered to be 20 Hz. The increase of this frequency in 1,5-2 times is possible via the input transformers and extra keys, but this solution will greatly reduce the weight and overall dimensions. In any case, the use of NPL for the current management of AM enables in-depth control of rotation speed up to work at close range with a nominal overload capacity, and ensure engine starting in difficult conditions.
The presence of relatively large number of keys is a drawback of NFC, but the reliability and power of thyristor switches has identified the area in which the NFC are applied almost exclusively NC. This large-power drives with heavy starting conditions such as the traction drive for transport, propeller shafts of ships, cement mills, etc
3.2 Frequency converters with DC link
Currently more common with the inverter DC link. At the entrance of these energy-channel drive installed controlled or uncontrolled rectifier. After conversion by the rectifier AC energy with constant voltage and frequency into a DC power, it is fed to the input of the inverter (I) And is then converted into energy three-phase alternating current, but with adjustable parameters. Thus, in the inverter of this type is a dual power conversion, which reduces its efficiency, but other significant advantages of these transducers provide them a dominant position in modern automated drive.
For power decoupling rectifier and inverter between them are required to establish the energy storage. Depending on the kind of storage – capacitor or inductor– inverter operates in either the voltage source (VS) or current source (CS).A functional diagram is shown in figure 2(a) – voltage source and 2(b) – current source.
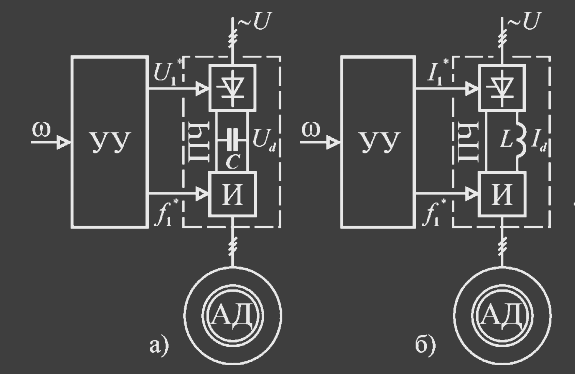
Figure 2 – Functional diagram of the Converter with a controlled rectifier
Energy storage is necessary because the DC power purely resistive, and for the formation of magnetic fields in the motor the desired exchange of reactive power from the power source, which provides the drive. When moving the AM in the generator mode changes the sign of the active current component of the stator, i.e., its direction relative to the voltage. This current and voltage correspond approximately to the values at the inlet And, therefore, when you change AM mode should be a change in relative direction of current and voltage in the DC link. But FCVS to change the direction can only be voltage and FCVS – current. The change in direction of tension in FCCS while maintaining the current direction will lead to the fact that the SW switches to invert and the excess energy will be returned to the network. In PCIN transition AM in the generator mode will change the direction of the current in the inverter. In this case, the excess energy cannot be returned to the mains through the rectifier, because its keys possess a unilateral conductivity. It can either be and often are recovered by the slave network inverter, included counter-parallel with controlled rectifier (СR), or to be dissipated in a braking resistor that is included with this purpose at the input of the inverter. Thus, FCCS provides two-way direction of energy exchange between the AM and the network without the use of additional devices and therefore engine operation in the two quadrants of mechanical characteristics, while FCVS in only one quadrant. However, more common in practice are FCVS. This is because most of the tasks the drive does not require asynchronous motor in the generator mode, and short-term outputs in this area are associated with a moderate amount of energy produced, which can dissipate the braking resistor. In addition, the throttle has a much worse size / weight parameters.
Concluions
- After the analysis of main advantages and drawbacks of the existing frequency converters, we can conclude that in most cases more appropriate to use frequency converters with DC link.
- Frequency converters with DC link optimization algorithms manipulated.
- The efficiency of the frequency converters will reduce energy consumption and increase reliability and performance of technological process.
At the time of writing this abstract master's work is not yet complete. The estimated completion date of master's work: June 2018. Full text works and materials on the subject can be obtained from author or his supervisor after the specified date.
Список источников
- Преобразователи частоты преимущества использования [Электронный ресурс]. – Режим доступа: http://elpriv...,свободный.
- Преимущества частотного регулирования электродвигателя [Электронный ресурс]. – Режим доступа: http://priv...,свободный.
- Частотно-регулируемый привод экономит и повышает надежность производства энергии [Электронный ресурс]. – Режим доступа: http://driv...,свободный.
- Виды частотных преобразователей [Электронный ресурс]. – Режим доступа: http://electric...,свободный.
- Основные типы преобразователей [Электронный ресурс]. – Режим доступа: http://ets.ifm...,свободный.
- Усольцев А. А.Частотное управление асинхронными двигателеми: учебное пособие. – Санкт-Петербург: Изд-во ИТМО, 2006. – 94 с., ил.
- Чернышев А. Ю., Деменьтьев Ю. Н., Чернышев И. А. Электропривод переменного тока: учебное пособие. – Томск: Изд-во Томского политехнического университета, 2011. – 213 с.