Реферат по теме выпускной работы
Содержание
- Введение
- 1. Актуальность темы
- 2. Цели, задачи исследования и планируемая новизна
- 3. Основные характеристики исходных техногенных материалов
- 4. Описание практической части
- 4.1 Подготовка смеси
- 4.2 Приготовление смеси
- 4.3 Пресование образцов
- 4.4 Пропарка готовых образцов
- 5. Исследование образцов на свойства
- Выводы
- Список источников
Введение
Условия существования и развития жизни на земле определяются экологическими факторами, то есть элементами среды, значительно влияющими на организмы. В настоящее время мировым сообществом в полной мере осознается масштаб угрозы экологического загрязнения земли и атмосферы техногенными отходами. Выход золошлаковых отходов и отходов угледобычи в год составляет примерно 1 млрд. т. Накапливаясь в районах функционирования предприятий, техногенные материалы существенно осложняют экологическую ситуацию в регионах. Создается опасность для здоровья населения, потерь вторичных ресурсов. [1]
Техногенные месторождения – это скопления минеральных веществ на поверхности земли или в горных выработках, представляющие собой отходы горного, обогатительного, металлургического и других производств и пригодные по количеству и качеству для промышленного использования, которое становится возможным по мере развития технологии его переработки и изменения экономических условий [2].
Общая масса накопленных промышленных отходов составляет около 30 млрд. т. Отвалы, терриконы, и шламонакопители размещёны на площади 160 -180 тыс. га, которая увеличивается со скоростью 3 - 6 тыс. га/год. Низкий объём переработки отходов (10 - 15 %) обуславливает рост техногенного загрязнения всех компонентов ОПС. Проблема отходов имеет ряд серьезных экологических и экономических аспектов и требует принятия неотложных мер по её решению. Одним из перспективных и эффективных путей ее решения является использование промышленных отходов для создания новых технических материалов. Из общего количества ежегодно образующихся промышленных отходов к повторному использованию пригодно около 120 -150 млн. т. В настоящее время используется только около 30 % этого количества [3].
1. Актуальность темы
Использование доломитовой пыли в качестве компонента вяжущего позволяет утилизировать накопленные в отвалах шлаки, являющиеся техногенными полезными ископаемыми, сэкономить природные и энергетические ресурсы, улучшить экологическую обстановку и существенно расширить сырьевую базу производства строительных материалов. Изготовление строительных материалов из доломитовой пыли будет более дешевым по сравнению с применением традиционных материалов.
В связи с этим, актуальное значение приобретает проблема осуществления мер, направленных на комплексное использование минеральных ресурсов.
2. Цели, задачи исследования и планируемая новизна
Целью данной работы является использование техногенных побочных продуктов промышленности в качестве сырья для производства строительных материалов.
Для достижения цели решаются следующие задачи:
- Анализ возможности использования доломитовой пыли, гранулированного доменного шлака и других техногенных отходов в качестве основы для производства строительных материалов.
- Разработка технологии производства строительных материалов из побочных техногенных отходов.
- Изготовление образцов строительных материалов.
- Исследование прочностных и других свойств.
Планируемая научная новизна: разработанная технология использования доломитовой пыли и гранулированного доменного шлака в качестве сырья для производства строительных материалов, а также методика проведения исследования свойств полученных образцов.
Использование техногенного сырья позволит получить практический эффект:
- Изготовлять дешевые строительные материалы.
- Повысить производительность труда, за счет рентабельной переработки раннее добытого сырья, которое является готовым полупродуктом и находящегося рядом с действующими предприятиями.
- Освободить занимаемые участки земли, рекультивировать их и ликвидировать источники загрязнения окружающей среды, улучшая тем самым экологическую обстановку вокруг действующих предприятий.
Методы исследований: изготовление образцов и исследование их свойств на реальном оборудовании кафедры.
Результаты отдельных этапов работы были доложены на научной конференции и опубликованы в сборнике.
3. Основные характеристики исходных техногенных материалов
Доломит — это уникальный минерал, который относится к группе карбонатов. Доломит в строительстве применяется весьма широко, поскольку этот материал достаточно крепок. Этот минерал применяют в строительстве вместо менее прочного известняка или же вместе с известняком для строительства малоэтажных зданий. Это кристаллическое соединение белого или желтого цвета использовалось раньше для производства гипсовых смесей, цемента, резины и стекла.
Доломитовая пыль - это отход металлургической промышленности, получаемый при обжиге доломита в вагранках. Свежая доломитовая пыль состоит в основном из СаО и МgO, которые при хранении постепенно переходят в СаСO3 и МgСO3. По нейтрализующей способности 1 т доломитовой пыли соответствует 1,5 т СаСO3 [4].
Химический и гранулометрический составы доломита и доломитной пыли представлены в таблице 1 и 2 [5].
Вид сырья | CaO | MgO | SiO2 | Al2O3 | Fe2O3 | П.П.П. |
---|---|---|---|---|---|---|
Доломитовая пыль | 12,14% | 24,66% | 12,00% | 10,00% | 12,00% | 29,17% |
Сырой доломит | 29,83% | 20,53% | 2,15% | 0,52% | 0,60% | 45,95% |
Остаток на сите | 0,315 | 0,071 | -0,071 |
---|---|---|---|
Массовая доля,% | 3,15 | 31,5 | 65 |
Размер сита,мм | Остаток на сите,% |
---|---|
10,0 | 2,2 |
5,0 | 40,0 |
3,0 | 45,0 |
1,0 | 66,0 |
0,63 | 67,0 |
менее 0,63 | 33,0 |
В процессе измельчения сырого доломита до нужных фракций ежегодно образовывалось порядка 250000 – 260000 тонн, а отходов в виде доломитовой пыли 10000 – 12000 т/год, результаты предоставил ОАО «Докучаевский флюсо - доломитный комбинат» [5]. При обжиге доломита во вращающихся печах основным видом отходов является пыль. Часть пыли из печи в виде полуобоженного доломита с крупностью 0-1 мм уносится с отходящими дымовыми газами и продуктами декарбонизации доломита и улавливается на двухступенчатой очистке отходящих газов камерах осаждения, циклонах и электрофильтрах. Уловленная на газоочистных установках пыль системой винтовых конвейеров и камерными насосами транспортируется в отгрузочные бункеры или отвалы.Доломитовый отсев имеет все преимущества доломитового щебня, отличающие его от других минеральных наполнителей, но при этом он намного дешевле щебня или крошки.
Доломитовая пыль не требует размола, однако при высеве сеялкой необходимо отсеивать крупные и твердые частицы. Объемов его добычи на сегодняшний день вполне хватает для полного удовлетворения потребностей государства [6].
Шлак — побочный продукт или отход от производства металла, после очистки от остатков ценных компонентов отправляемый в отвал. Однако в некоторых случаях основным продуктом плавки, содержащим наиболее ценный компонент сырья, является именно шлак (титановые шлаки, получаемые при плавке ильменитовых концентратов; ванадиевые шлаки, образующиеся при конвертировании ванадийсодержащего чугуна). Химический состав доменных шлаков зависит от состава руды, плавней, используемого топлива, условий охлаждения шлакового расплава [7].
CaO | MgO | SiO2 | Al2O3 | Fe2O3 | MnO | SO3 | П.П.П. |
---|---|---|---|---|---|---|---|
38,0% | 7,2% | 36,4% | 15,0% | 1,8% | 0,7% | 1,0% | 0,12% |
Высокое содержание MnО в составе шлака является неблагоприяным, т.к. в этом случае происходит частичное замещение CaO в активных минералах и образование менее активных минералов. При содержании MnО в шлаке более 3 - 4% снижается его гидравлическая активность, ухудшаются свойства и структура шлакового стекла.
Микроструктура шлаков влияет на важнейшие свойства изготавливаемого из них строительного материала – механическую прочность, химическую стойкость и долговечность.
Пористость шлака имеет неоднородное значение по его массе. Так, пористость различных фракций быстроохлажденного шлака не совпадает и изменяется в интервале от 15 до 80% [8].
Одной из особенностей шлакового заполнителя является увеличение пористости зерен по мере увеличения их размера. Высокая пористость доменных шлаков, прежде всего, вызвана их дегазацией при охлаждении шлакового расплава. Т.к. процесс газообразования не является регулируемым, влиять на степень пористости гранулированного шлака можно с помощью таких величин как вязкость шлаков, температура, а также скорость охлаждения шлакового расплава.
Водопотребность гранулированного доменного шлака, ввиду его высокой пористости и пустотности, выше водопотребности природного песка и может достигать 30%. Также возможно уменьшить водопотребность доменного шлака путем его частичного или полного измельчения [9].
Гранулированный шлак получают в результате быстрого охлаждения жидкого шлака при помощи воды и воздуха в специальных установках. При охлаждении воздухом шлак содержит большое количество алюмосиликатных минералов. При получении расплавленного шлака, его температура может достигать 1480 °С. В зависимости от способа получения шлак может иметь различные свойства. Вес, структура и размер шлака тоже зависит от выбранного метода обработки.
Шлак – это зернистый материал с частицами размером меньше10 мм, от темно-бурого до светло-желтого цвета, преимущественно стекловидной структуры. После его тонкого помола получают вяжущее, обладающее гидравлической активностью, т.е. свойством твердеть в воде. Гранулированные основные доменные шлаки могут использоваться для получения активированного вяжущего, на базе которого изготавливают активированный бетон [10].
Самое выгодное направление сейчас – это использование шлака, как компонент для различных строительных материалов. Оно также имеет большие перспективы, а ещё приводит к сбережению ресурсов, так как шлак является отходом производства. А используя отходы в дело, принесет большую выгоду.
4. Описание практической части
4.1 Подготовка смеси
4.1 Подготовка смеси
Технология получения прессованного кирпича на основе техногенных продуктов в лабораторных условиях начинается с написания рецептуры. Далее следует взвешивание и смешивание компонентов. Для качественной и достоверной проверки свойств нами были использованы 3 образца, разные по процентному содержанию исходного сырья. Для получения пластичной массы все компоненты должны быть строго дозированы согласно рецептуре. Для этого используются весы с допустимой погрешностью измерений 0,5 %. В таблице 5 представлена рецептура трех образцов.
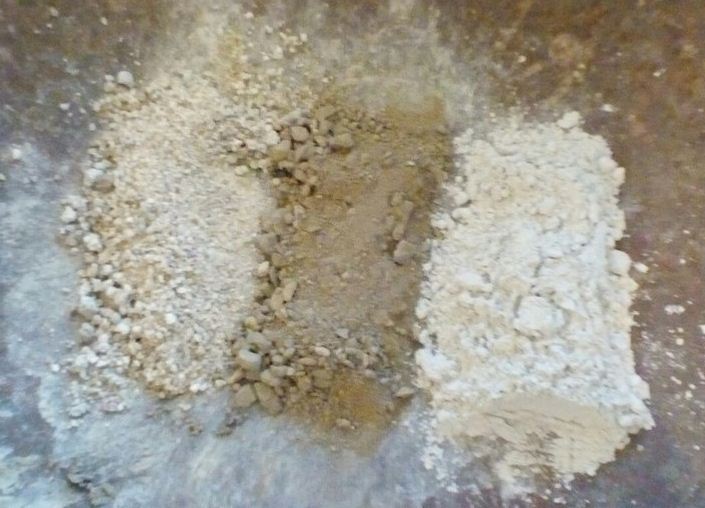
Рисунок 1 — Исходное сырье
Образец | Молотый граншлак | Граншлак | Доломитовый отсев | Вода + ЛСТ |
---|---|---|---|---|
1 | 30% | 30% | 40% | 5 мл |
2 | 40% | 20% | 40% | 5 мл |
3 | 50% | 10% | 40% | 5 мл |
4.2 Приготовление смеси
Дозированная смесь подвергалась измельчению, при помощи мельницы с мелющими телами, где также происходило тщательное перемешивание всех компонентов для их активация. Добавлялось строго необходимое по рецептуре количество воды (если количество воды не будет соответствовать рецепту, то на этом технологическом этапе раствор не будет соответствовать определенным стандартам, готовые изделия не обретут нужных свойств). Для получения гомогенной массы необходимо непрерывно перемешивать смесь.
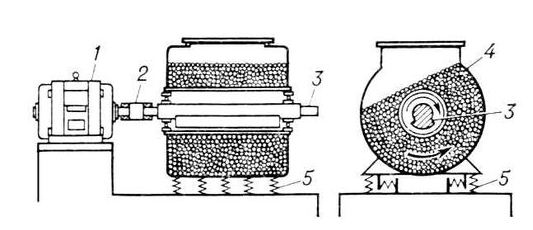
Рисунок 2 — Мельница ( 1 - электродвигатель, 2 - муфта, 3 - вал, 4 - барабан, 5 - пружина)
4.3 Прессование образцов
На современных предприятиях используется автоматизированные прессы, а в лабораторных условиях был использован ручной пресс. Для удобоукладываемости смеси, пресс-форму смазывали ЛСТ. Готовой смесью с нужной консистенцией заполняли пресс-форму и начали процесс прессования. Манипуляцию повторяли для трех разных образцов. После того как образцы были отпрессованы их оставляли на 24 часа на стелаже.
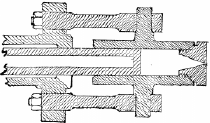
Рисунок 3 – Пресс
(анимация: 8 кадров, 11 циклов повторения, 136 килобайт)
4.4 Пропарка готовых образцов
Изготовление кирпича далее заключается в пропаривании полученного после прессования сырца. В процессе пропаривания готовые изделия набирают до 70 % своей марочной прочности. На этой стадии была использована специальная пропарочная камера, куда на поддонах отправлялись сформованные образцы. Нами были выбраны разные промежутки времени: 2, 4 и 6 часов. Выдерживались при температуре 70 – 75 °С. После пропаренные изделия были отпралены на допарку для постепенного снижения температуры, в течении 1 часа при температуре 45 °С. По завершении стадии допаривания изделия отстаивались при комнатной температуре 3 дня.
5. Исследование образцов на свойства
Практическая часть еще не окончена, изготовлено достаточное количество образцов для проведения опытов. На данном этапе магистерской работы исследуются прочностные свойства образцов. Далее образцы будут подвеграться испытаниям на сжатие, истираемость, морозостойкость и водопоглащение.
Можно отметить, что в зависимости от процентного содержания исходных компонентов с увеличением молотого граншлака в образце, улучшается прессуемость, образцы более прочные, с четкими ребрами и гладкой поверхностью.
Выводы
Первый этап исследований показал возможность использования техногенных продуктов (пыль, отсев, шлак) для получения строительных материалов и изделий.
При написании данного реферата магистерская работа еще не завершена. Полный текст работы и материалы по теме могут быть получены у автора или его руководителя после защиты магистерской работы.
Список источников
- Техногенные отходы в производстве строительных материалов [Электронный ресурс]. — Режим доступа: http://www.concrete-union.ru/articles/index.php?ELEMENT_ID=5206.
- Трубецкой К.Н., Уманец В.Н., Никитин Н.Б. // Комплексное использование минерального сырья. – Екатеринбург. 1987. №12. 18-23 с.
- Касимов А.М. Промышленные отходы. Проблемы и решения. Технологии и оборудование: учебное пособие / А.М. Касимов, В.Т. Семёнов, А.А. Романовский; под ред. А.М. Касимова. – Харьков: ХНАМГ, 2007. – 411 с.
- Известковые отходы промышленности [Электронный ресурс]. — Режим доступа: http://agro-portal24.ru/agrohimiya/686-belitovaya-muka.html.
- Инвентаризация отходов производства «Докучаевского флюсо-доломитного комбината». Форма ОТ – 4 от 06.09.95 г. № 208.
- Доломиты [Электронный ресурс]. — Режим доступа: https://ru-ecology.info/term/42993/.
- Строительные материалы: Справочник / Болдырев А.С., Золотов П.П., Люсов А.Н. и др.; Под ред. А.С. Болдырева, П.П. Золотова. - М.: Стройиздат, 1989. - 567 с.
- Попов Л.Н. Строительные материалы и детали. – М.: Стройиздат, 1986. - 335 с.
- Паращенко О.Д., Шульга А.С., Валешко К.А. Контроль качества строительных материалов. - К.: Будівельник, 1985. - 96 с.
- Пальгунов П.П., Сумарохов М.В. Утилизация отходов / П.П. Пальгунов. - М.: Стройиздат, 1990. - 352 с.