Abstract
Content
- Introduction
- 1. Theme urgency
- 2. Goal and tasks of the research
- 3. A review of research
- Conclusion
- References
Introduction
Products with the gears are the most common security mechanisms because gear is the most common mode of transmission in modern engineering. They are very reliable in operation, provide consistency ratio, compact, have high efficiency, easy to operate, durable and can transmit any power. The main working part of gears is a crown gear, which works in difficult operating conditions, comprising: high bending and contact stresses, the uneven distribution of the load in contact, edge contact, etc. While the main performance characteristics and quality parameters gears are formed in the final technological operations, including: operation of finishing machining to ensure the required accuracy and quality of surfaces; and operations hardening treatment performed with the aim of increasing the physico-mechanical properties of base material of the part or working of the surface layers.
Among the requirements that determine the operational properties of gears, the most important are requirements on the wear resistance of teeth and improve the quality of working surfaces with special coatings, without prejudice to the cost of manufacturing of gear wheels.
1. Theme urgency
In gears the most labor-intensive to manufacture and are accurate elements of the ring gear, to the greatest extent determine the health and performance properties. Where required the parameters of accuracy, surface quality, and physico-mechanical properties of elements of the ring gear are formed on the stages finishing and finishing. Therefore, the development of a rational structure of these transactions is of paramount importance to improve the quality of gears.
To achieve the required physico-mechanical properties of HCC, most frequently used methods of heat treatment and surface plastic deformation. These methods allow to provide properties for a sufficiently long plots of, and usually require a significant amount of subsequent machining. During the subsequent operation of gears is often observed some distortion of the tooth profile caused by the uneven wear on the tooth height. Special coating on the elements of gears, not widespread, however, have advantages, as evidenced by their use for other machinery [1-4.].
Based on the foregoing, this work is relevant, and in matters of improving the quality of gears based on the application of special coatings and methods of combined treatment in the stages of finishing processing of the teeth.
2. Goal and tasks of the research
Objective: improve the quality of the working surface of the LC by the application of vacuum ion-plasmonic coatings and increasing the efficiency of finishing treatment
Main tasks of the research:
- To analyze the causes of wear of the working surfaces of the teeth.
- To perform the analysis of methods to ensure physical-mechanical properties of working surfaces of the teeth.
- To offer a method of increasing the performance of the process of coating the working surfaces of the teeth.
- To perform the kinematic structure of the movement of gear wheels in a vacuum chamber. to offer the most rational structure of the movement of the gear wheels relative to the plasma flow.
Expected scientific novelty:
- It is established that the process of dividing the HCC into functional elements must be performed in accordance with the performed operational functions, and the properties of these elements to provide, depending on the features and operation.
- It is established that providing the changing properties of the working surface of the tooth, depending on the velocity of mutual slip profile is achieved a more uniform wear on the tooth height, and the rational use of resources gears.
The alleged practical benefit:
- The recommendations were developed, which allow to create a technological support and to form a rational structure of the technological process of finishing processing on the basis of coating on the basis of the working conditions of the LC; and to determine the required parameters of surface layer quality on the stages of surface preparation to apply coatings.
- The results of the work implemented in production on Sejnenska engineering plant, JSC
Motor-Sich
, in the Donetsk machine-building plant ODOBuran
, and also in educational process of chairTechnology of mechanical engineering
DonNTU.
3. A review of research.
Gears are widely used in mechanical equipment for the transmission and transformation of the parameters of rotational motion. The lifetime determines the reliability of the mechanism and is one of the critical parts of the fault tree. Mechanical failures due to wear or destruction of the gears leads to a more lengthy downtime and costly recovery. Alert the emergency destruction of the teeth and increase the service life of the transmission allow timely repair actions informed by the results of visual wear.
On the performance of gears is influenced both by external factors, which determine the transmitted torque, and the rotation of the gear wheels and internal, depending on the technical condition of the mechanism. The interaction of external and internal factors creates a variety of possible damage to gears. Despite the constancy in the process of operation of the gear ratio of the gear, these factors change, leading to the predominance of a certain type of wear or damage. In determining the causes of damage is necessary to consider the gear as a part having a Seating surface, the bearing elements and the contact, the interacting surface.
On the performance of gears is influenced by the following external factors:
- The value of the actual power supplied of the load as the nominal load does not change the shape of the tooth and does not leave significant traces of deformation on the working surface of the gearing.
- The presence of abrasive particles that contribute to abrasive wear or chemical substances causing corrosion of the surfaces of the teeth, contributing to the emergence of a gas or liquid erosion. The main reason for corrosion is the presence of water in the lubricant is manifested in the form of uniform or non-uniform rust layer on the surface of the teeth. The degree of corrosion can be different.
- The degree of mutual displacement of gear wheels relative to the shaft. The immobility of the Seating surfaces of the toothed wheels and the shaft meets the design requirements in that case, if the mating parts remains stationary during load application. The emergence of small displacements of the mating parts leads to fretting corrosion, which is manifested in the form of dark spots on the landing surface.
- The nature of the interaction between contacting surfaces, which determines the friction on the contact surfaces. If the prevailing fluid friction, ensuring minimum friction coefficient, and there is a complete separation of the contacting surfaces with a layer of oil, the condition was evaluated as good. In this case, is predominantly oxidative wear. The appearance of boundary friction leads to the contact of the two parts, appearing in the polishing of the working surfaces of the teeth. Most often, boundary friction is evident at the initial stage of running-in of new gears.
To eliminate premature failure and prolong the time of operation of gears and introduces various operations additional hardening of the surface layers of teeth, to improve the physico-mechanical properties of working surfaces of the teeth. This is achieved by using methods of thermal and chemical-thermal treatment, application of special coatings, the use of compositions of several materials of different properties in a single product. One such method is the application of vacuum ion-plasma coatings. Such coatings are widely used, and provide the required properties of the individual items details.
Based on the characteristics of the process of deposition of vacuum ion-plasma coatings described previously [10], it was found that the functionally-oriented technological process of treatment of teeth, improves the physico-mechanical properties of gears.
This kind of hardening gears is the most efficient in the moment. For maximum performance of the coating process when the established technological parameters it is necessary to efficiently use the volume of the working chamber for deposition of vacuum ion-plasma coatings.
The unit is ННВ6.6-I1 for coating using plasma sputtering rotating table is provided with a planetary mechanism providing rotation of the workpiece around its axis and around the axis of the camera. For a more complete use of the working space of the vacuum chamber proposed various options for the location of blanks of the type gear
(Fig 1).
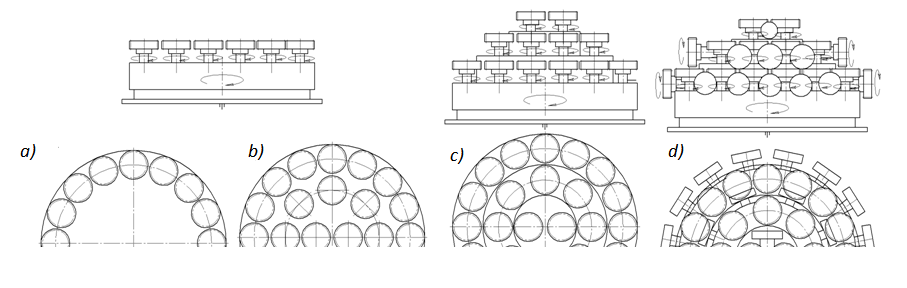
Figure 1 – Accommodation billet in the process of coating[6]
According to the method of placement of workpieces, the planetary gear can be the following options:
- a sibling of filling blanks on the periphery of the table in single row (Fig. 1, a),
- single-level multi-row, with the placement of workpieces on the entire area of the circumference of the table (Fig. 1, b);
- tiered, with placement of pieces on each level, and parallel vertical position of the axes of rotation of the workpiece (permitting the crossing at small angles when the message of the precession of the swing) (Fig. 1, c);
- layered, with intersecting axes of additional blanks located between workpieces with a vertical axis of rotation (Fig.1, d).
Under certain technological parameters, the cyclic performance of the installation depends on the number of simultaneously processed products.
In multi-level placement with additional workpieces between the workpieces with a vertical axis of rotation, the total number of workpieces of the same level in the chamber is doubled and the parameter limiting the working space of the camera is the thickness of the outermost workpiece.
In Fig.2 shows the options for construction of the turntable of the vacuum chamber, allowing to implement the schemes of placement of workpieces (Fig. 1).
![The device for placing the workpieces in the chamber for coating[7]](images/sz.png)
Figure 1 – The device for placing the workpieces in the chamber for coating[7]
The device has a Central (solar) fixed wheels 3 and the faceplate 6, performing the role of planetary gear set coaxially to the Central wheel and rotatable from the drive shaft 1. Also on the faceplate are satellites 5, rotating in bearings 8, which are pressed into the holes of the faceplate. Thus the rotation of satellites is carried out from a gear with a stationary Central wheel 3, when rotating the faceplate 6. In the holes of the satellites are set blanks, or devices for fixing of workpieces.
In the first device (Fig.2, a) blanks are placed on the same plane as the holes satellites 5, while the sun wheel 3 is mnogovintovoy in which all the gear rims located on the same level. The satellites are installed into the faceplate 6 connected with the drive shaft 1. Moving the workpieces on the circumference is carried out together with the faceplate, and their rotation around their axes from the satellites included in mesh with the teeth of a stationary sun gear 3.
In the second device (Fig. 2, b) the workpiece is placed on three levels, a sun wheel is travelcover gear unit. The faceplate 6 is made in the form of a pyramid, each stage of which is the number of satellites 5 with the workpieces. Also, the faceplate is rotated from the drive shaft 1 and the rotation of the satellites is transmitted from gear with fixed crowns of the sun gear 3.
In the third device (Fig. 2) there are two extra rows of blanks, the axes of which are perpendicular to the axis of the faceplate, and are crossed relative to the axes of the remaining blanks. On the Central wheel fixed two additional ring gear and bevel gear resulting in rotation of the workpiece with a horizontal axis. The faceplate has radial openings in which are mounted the pinion gears of bevel gears.
Considered options for construction of the rotating tables of the vacuum chamber due to their design features can be used in the following cases.
The first embodiment (Fig. 2, a) is characterized by small height of the table with blanks, and can be used for vacuum chambers with reduced height of the working space. However, due to the fact that the workpiece on the inner circumferences of the table are shaded from the adjacent blanks, restricting the flow from the side of the cathodes, the coating should be from the top of the cathode.
The second variant (Fig. 2, b) is characterized by a greater height of the table and allows you to have a greater number of billets at equal first the largest diameters of the tables. Also, the workpiece located on the inner circumferences of the table is not closed by the outer circumferences of workpieces, therefore, the coating on all blanks possible from the side of the cathode. Thus, this variant, along with a uniform access of the plasma flow for all workpieces, allows for more efficient use of work space of the vacuum chamber. Meanwhile, because the diameters of the circles of the arrangement of blanks largely depends on the size of the fixtures for mounting workpieces, this option should be used for HCC of large diameter.
The third variant (Fig. 2) allows you to place twice the number of workpieces, providing the greatest performance coating. However, due to the need for additional space to accommodate workpieces with a horizontal axis of rotation, and to prevent overlapping adjacent workpieces, increases the height of the rotating table. Also, due to the different position of the axes of the workpieces, the action of the plasma flow relative to the working elements of gears is different. Therefore, this option should be used for vacuum chambers with a large enough height of the working space, and the availability of cathodes, situated on the periphery and in the upper part of the vacuum chamber.
Implementation of the desired kinematic structure of movement of goods in the working area of the vacuum chamber, due to continuous change the position of the workpiece, allows to provide uniform flux coating to the entire toothed crown, and to accomplish the following tasks:
- eliminate shadow zones that hinder coating;
- to expand the technological capabilities of the process, allowing you to apply special types of coatings (Sika and functional - oriented) and with naturally varying thickness.
The coating thickness at any point of the product depends on the intensity of the plasma flow and the angle between the normal to the surface of the product. Note that the thickness of the coating on the product surface increases along the normal to each point of the original surface of the product, and depends on the angle between the normal to the surface point, and the total direction vector of the flow of the plasma jet (Fig. 3). The change of the vector of the flow, caused by the peculiarities of the kinematics of the movement of the product in a vacuum chamber.
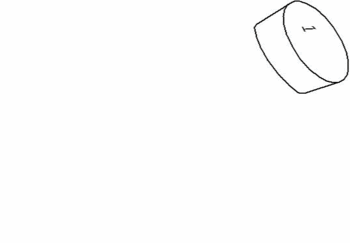
Figure 3 – The effect of the plasma flow in the surface points is applied
(animation: 9 frames, 79 kilobytes)
(yk – the angle from which the coating is applied, 1 – cathode, 2 – normal to the surface points, h – the thickness of the coating, v,u – the parameters of the surface of the product)
Conclusion
Thus in the work the analysis of key operational characteristics of the gears. The causes of teeth wear and also the method which allows to increase the efficiency of HCC. It was also analyzed the possible accommodation of workpieces in a vacuum chamber, it may be noted, as the number of workpieces placed in the chamber depends on the duration of technological exposure, the main direction of further improve performance of the coating process is to increase the number of workpieces in the chamber, while providing a desired position and kinematics of movement of the workpieces relative to the plasma flow
References
- Васильев А. Ф. Создание функционально-градиентных износостойких покрытий с регулируемой твердостью методом сверхзвукового холодного газодинамического напыления для изделий машиностроения. / А. Ф. Васильев, Д.А. Геращенков, Б. В. Фармаковский, М. А. Юрков /Сборник трудов XIV международной научно-технической конференции «Машиностроение и техносфера XXI века». – Донецк: ДонНТУ, 2007. Т.1. – С. 163 – 171.
- Внуков Ю.Н., Марков А.А., Лаврова Л.В., Бердышев Н.Ю. Нанесение износостойких покрытий на быстрорежущий инструмент. – Киев, Тэхника, 1992. – 143 с.
- Гончаров М.В. Технология и оборудование получения комплексных покрытий с особыми свойствами. / М.В. Гончаров, В.С. Гончаров // Современные тенденции развития автомобилестроения в России. Труды Всероссийской научно-технической конференции. – Тольятти: ТГУ, 2003. №3. С. 448 – 452.
- Костржицкий А.И., Лебединский О.В. Многокомпонентные вакуумные покрытия. М.: Машиностроение, 1987. – 208 с.
- Михайлов А.Н. Основные принципы и особенности синтеза функционально-ориентированных технологий машиностроения. / А.Н. Михайлов //Сборник трудов XIII международной научно-технической конференции: Машиностроение и техносфера XXI века. В 5-ти томах. – Донецк: ДонНТУ, 2006. Т. 3. С. 61 – 77.
- Михайлов А.Н. Основы синтеза поточно-пространственных технологических систем непрерывного действия. – Донецк: ДонНТУ, 2003. – 379 с.
- Михайлов А.Н. Основы синтеза функционально-ориентированных технологий машиностроения. – Донецк: ДонНТУ, 2008. – 346 с.
- Михайлов А.Н. Общие особенности функционально-ориентированных технологий и принципы ориентации их технологических воздействий и свойств изделий. / А.Н. Михайлов //Сборник трудов XIV международной научно-технической конференции: Машиностроение и техносфера XXI века. В 5-ти томах. – Донецк: ДонНТУ, 2007. Т. 3. С. 38 – 52.
- Технология производства и методы обеспечения качества зубчатых колес и передач. Учеб .пособие / В.Е. Антонюк, А.А. Сусин, С.П. Руденко и др.; под ред. В.Е. Старжинского и М.М. Канне. – Минск: УП "Технопринт", 2003. – 766 с.
- Юдин Д.Л. Пути повышения качества отделочно-упрочняющей обработки зубьев зубчатых колес ППД / Д.Л. Юдин, А.И. Иунихин, М.А. Порхачев, В.А. Фомин // Вестник машиностроения, 1981. – № 3. – С. 49 – 50.