Abstract
The contents
- Introduction
- 1. Theme urgency
- 2. Goal and tasks of the research
- 3. The effect of the modes magnetic abrasive processing on parameters of a roughness of internal surfaces in products from oxide ceramics
- Conclusion
- References
Introduction
Ceramic materials favorably differ from metal and polymer with high corrosion resistance and the ability to regulate the properties of the material within a wide range due to structural changes. Ceramic materials along with high hardness, as a rule, have increased brittleness, low resistance to bending and shock loads. Among modern ceramic materials & ndash; Aluminum oxide is widely used. The main properties of the material: very high strength, high hardness, high temperature stability, high wear resistance, high corrosion resistance, even at high temperatures, high thermal conductivity, resistance to aggressive media.
One of the methods for improving the microrelief of the surface layer is to magnetic abrasive polishing (MAP). The essence of the method: magnetic abrasive powder is located between the poles of electromagnets, creating a cutting tool in the form of a kind of polishing brush
. In the role of a bundle of abrasive grains, a magnetic field is used that has elastic forces acting on individual grains. When the workpiece moves through the working area, the powder exerts pressure on the part at each point of the surface, which leads to the removal of the metal and the smoothing of the microroughness. It provides obtaining roughness parameters Ra 0,01-1 ?m, decrease in waviness 8-10 times, grain size up to 2 times. This increases the contact strength and wear resistance of parts 2-3 times, increases the reference length of the profile to 75-85%. The method has the ability to handle both soft and viscous, and non-metallic materials. [ 1 ].
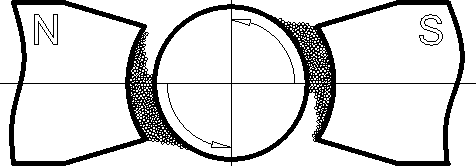
Plan of magnetic abrasive treatment
1. Theme urgency
Analysis of methods for improving the quality of surfaces has shown that the most promising methods for processing shaped surfaces are the methods of abrasive processing on a flexible bundle. Elastic bond between abrasive grains allows processing of spatially complex surfaces without the manufacture of a shaped abrasive tool. Among these methods, the most productive is magnetically abrasive treatment.
This method is easy to implement, environmentally friendly, provides high quality machined parts surfaces and a significant increase in their resistance to wear, corrosion and mechanical stress, has high productivity and successfully replaces the processes of chemical and electrochemical processing.
Master's work is dedicated to the actual scientific task of development a unified approach to the synthesis of Moore FSM, which is directing on hardware amount reduction in resultant device and is including algorithmic, combinatory and circuitry optimizing techniques. FPGAs by Xilinx, which combine functionality, programmability and availability to consumers, are used as the target basis. CAD Xilinx ISE, Verilog HDL and Java SE are applied as tools of the research.
2. Goal and tasks of the research
DThe aim of the study is to investigate the influence of the rotational speeds of the workpiece and tool on the surface roughness with a magnetic field. abrasive processing.
Main tasks of the research:
- Analyze the information available at the time of writing the master's work.
- Make an experiment, the essence of which will be to determine the effect of processing parameters on the quality of the surface layer of parts from technical ceramics (oxide and corbid) in the case of magnetically abrasive processing.
- Analyze the obtained data.
3. The effect of the modes magnetic abrasive processing on parameters of a roughness of internal surfaces in products from oxide ceramics
At the department of mechatronic systems of machine-building equipment DonNTU the device for experimental researches of MAO internal surfaces on the basis of lathe-turret lathe 1341 [ 2 ], shown in Fig. 1. The provided treatment scheme is the rotation of a magnetic abrasive powder inside the holes by an external magnetic field. The sample to be processed is a bushing made of Al2O3 with an inner hole 28 mm in diameter. The bushings were pretreated with a diamond grinding wheel 1A1 20x10x10 AC4 250/200 - 4 - M2-01 and 1A1 10x10x6 AC4 100/80 - 4 - V2-01 GOST 16167-90, which helped to provide the necessary initial roughness in the parameter Ra = 0, 25 ?m, as well as the required geometric accuracy of the hole.
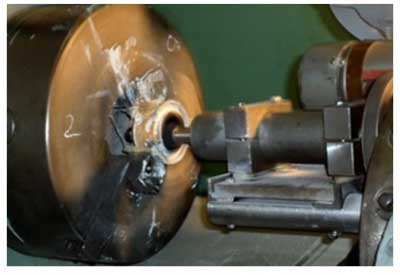
Figure 1. The device for experimental research MAO internal surfaces on the basis of lathe turret 1341.
Four magnetic neodymium rings, mounted on the mandrel of the polishing spindle, are located opposite to each other in opposite polarity and provide a total magnetic induction of 0.8 T. Between the magnets are mounted steel rings that pass through a magnetic flux generated by two adjacent magnets. As a magnetically abrasive powder, iron abrasive powder with synthetic diamond in the form of abrasive inclusions made by STC Electron
, Donetsk, was used. The size of the powder fraction is 180/100, the size of the abrasive is 7/5, the content of the abrasive in the grain is 40%. The machine works as follows. A workpiece is placed in the clamping device (cartridge). An abrasive powder is applied to the polishing mandrel. The spindle is then driven by a rotating clamping device with a workpiece mounted therein and a polishing spindle assembly. The gap between the mandrel and the workpiece was set to 1.5 mm, within which at least 4 layers of magnetic abrasive material can be contained and the lowest value of the established roughness is attained.
In studying the effect of the rotational speeds of the workpiece (Vd) and the tool (Vu) on the surface roughness, 2 ^ 2 experiments were carried out. The significance of levels and intervals of variation of factors are given in Table 1. In accordance with the accepted levels of variation, a full factorial experiment was carried out. At each point of the factor space the number of repetitions was three. The mean values of the results of the determination of the arithmetic mean deviation of the profile are given in Table 2 (y).
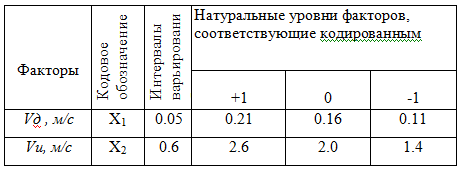
Table 1 - Levels and intervals of factor variation

Table 2 - Planning Matrix and Results of Experience
The dependence of the parameter Ra on the factors under investigation will be sought in the form of a regression equation of power type:

As a result of processing the experimental data, the following equation is obtained:

For the transition from coded factors to natural ones, we represent x1 and x2 in the form:
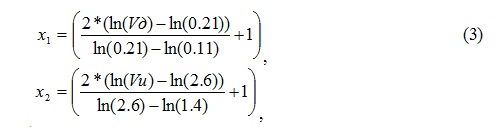
n equation (2) after the transformation we obtain:

The obtained dependence was checked for adequacy by the Fisher criterion. The calculated values of the Ra (ycalc) microrelief parameter are given in Table 2.
To analyze the obtained dependence 4, we construct two-dimensional response surfaces in the region of the factor change (Fig. 2). It can be seen from the figure that as the workpiece speed (Vd) increases, the roughness value of the ceramics with respect to the Ra parameter increases. As a result, when Vg & gt; 0, 25 m / s the microrelief of the surface layer does not improve in comparison with the initial value. Increasing the speed of the tool results in a decrease in Ra.
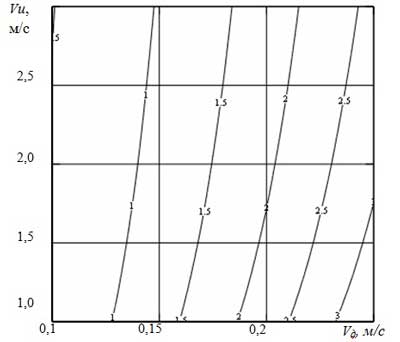
Figure 2. Two-dimensional response surfaces of the parameter Ra with varying workpiece speeds (Vd) and tool (Vи)
1. In carrying out experimental studies using the full factorial experiment, a regression dependence of the arithmetic mean deviation of the profile was obtained for magnetic abrasive processing of the inner surfaces of a part made of ceramics (Al2O3) against the rotational speeds of the workpiece and tool.
2. The regression dependence obtained allows one to choose the rotational speeds of the workpiece and the tool from the condition of ensuring the required arithmetic mean deviation of the internal surface profile of the holes in the aluminum oxide components in the MAP.
Conclusion
It is planned that in the course of my master's thesis, experiments will be carried out to determine the effect of processing parameters, namely the speed of the workpiece rotation, the speed of the tool, and the processing time on the quality of the machined surface in the details of the carbide ceramic when magnetically abrasive.
When writing this essay, the master's work is not yet complete. Final completion: July 2018. The full text of the work and materials on the topic can be obtained from the author or his supervisor after the specified date.
References
- Барон Ю. М. Магнитно-абразивная и магнитная обработка изделий и режущих инструментов.— Ленинград: Машиностроение, 1986. - 176 с.
- Гусев В.В. Магнитно-абразивная обработка внутренних поверхностей с использованием постоянных магнитов / В.В. Гусев, С.В. Кучереннко, К.С. Сухоручко// Наукові праці ДонНТУ. Серія: Машинобудування і машинознавство. – Донецьк: ДонНТУ, 2011. – Випуск 8 (190). – С. 145-151.
- Пустыльник Е. И. Статистические методы анализа и обработки наблюдений / Пустыльник Е. И. – М.: Наука, 1968. – 288 с.
- Бойко Н.Г., Федоров О.В. Основы научных исследований. Курс лекций. – Донецк: ДонНТУ, 2007 – 76 с.
- Семенченко И.И. Проектирование металлорежущих инструментов./ И.И. Семенченко, У.М. Матюшин, Г.Н. Цукров. - М.: Машиностроение, 1985. - т.1. - 290с, т.2. - 310с.