Abstract
The contents
- Introduction
- 1. Theme urgency
- 2. Goal and tasks of the research
- 3. Review of research and development
- 3.1 The system of adaptive control of the process of machining of parts on CNC machines
- 3.2 Control system of hydraulic machines for the example of thermoplastic automatic machine
- Conclusion
- References
Introduction
Automatic control and monitoring systems (hereinafter ACS) are an integral part of modern enterprises and play a key role in ensuring their reliable and safe operation. Modern automatic control systems usually serve two main tasks: automatic control of technological processes (TP) and automatic monitoring of parameters and operating modes.
1. Theme urgency
TAutomation TP allows you to significantly increase the efficiency of specific equipment (object management) and the work of the enterprise as a whole. Automation of the technological process is based on the description of technological operations (technological algorithms) developed by process engineers and providing the TP itself. Automation allows to significantly reduce the time spent on performing standard (predefined) actions (operations, cycles) of the automated equipment, by increasing the speeds of the executive mechanisms of control objects, the absence of a stop between the execution of individual actions by moving parts, the realization of the joint motion of several mechanisms, controlled equipment, etc. In today's time there are many different ACS, and in this paper, we consider only a few of them.
2. Goal and tasks of the research
The main goal of automation and mechanization of machines during modernization is to reduce the auxiliary time while maintaining or improving the accuracy of processing and facilitating the work of the machine operator.
Recently, the improvement of accuracy and other qualitative indicators of the equipment being modernized is of paramount importance. Experience shows that the modernization of precision machines to improve their accuracy in most cases is economically justified, since the acquisition of new equipment of a higher class of accuracy is always associated with significant material costs. In the preparation of modernization plans, rationalization proposals are taken into account. And the greatest effect is, as a rule, those proposals, which are developed by creative teams in the composition of machine operators, masters and engineers.
Main tasks of the research:
- Analysis of modern automatic control systems.
- Selection of the parameters of the automatic control system.
- Designing of automatic control system for lathe model 16K20T1
Research object: process of turning the workpiece.
Research subject: The process of improving the quality of processing when turning cylindrical surfaces.
3. Review of research and development
3.1 The system of adaptive control of the process of machining of parts on CNC machines
Next consider the system of adaptive control of the process of machining of parts on CNC machines.
When machining a part with a tool, various factors influence the tool: mechanical loading, electric currents, vibrations, chemical influences, elastic deformations of TOC, build-up. All this leads to intensive wear of the structural elements of the tool and, even, to its breakdown. Which leads to a decrease in accuracy, quality, productivity, or the appearance of a marriage, which entails economic losses and a high cost of the parts being processed [7].
Therefore, to improve the quality parameters, accuracy, cost of the parts being processed, it is necessary to use the adaptive control system of the cutting tool, directly in the process of processing, which will enable us to identify the moment preceding the tool breakdown, in order to replace it timely.
The adaptive cutting process control system must have high accuracy of information about the cutting zone and tool status, in real time monitor the degree of wear, the EMF of the tool-detail pair, and the force acting on the tool. The system should work stably, as well as with a low probability of false assessment of the condition of the cutting tool and malfunctions in the system for automated control of the part processing process. The implementation of this system should be such that it can be applied without special design changes to the machine drives and technological processing system (TOC) [8].
According to the research conducted at the National Technical University of Ukraine, the most suitable for information parameters, on the basis of which it is possible to judge the state of the processing tool, is the emf of cutting and the cutting force.
Proceeding from this, the system of adaptive control of the cutting process is based on measuring the emerging EMF cutting and the cutting force that arise during the processing in a natural way.
The main parameter for the control is the EMF cutting, which occurs as a consequence of the temperature rise in the cutting zone, since the increase in EMF indicates an increase in the tool-detail contact (CID), which in turn indicates an increase in tool wear.
The adaptive process control system for the machining of parts has 2 control loops. The first control loop is a subsystem for fast emergency shutdown of the machine drives, which, if the allowable cutting force is exceeded, sends a command to safely remove the cutter from the cutting area and turn off the machine drives. The second circuit is a subsystem for estimating and predicting tool wear based on EMF cutting signals.
The figure (Figure 1) shows the block & ndash; scheme of the device implementing the proposed system of adaptive control.
В соответствии с предлагаемой системой в процессе обработки измеряют сигналы термоэдс, и ЭДС упругих перемещений технологической системы с помощью датчиков 1, отделяют постоянные и переменные составляющие сигналов, измеряемых в блоке 2, который может быть выполнено в виде электронного фильтра. Постоянные составляющие подают в блок управления 3, где формируют управляющие команды на изменение режимов резания, а переменные с помощью преобразователя 4, который может быть выполнен в виде когерентного оптического процессора, превращают во взаимокоррелирующие функции, которые считываются в устройстве 5, а затем подают в блок коррекции 6, которым формируют корректирующие команды на смену режимов резания. Команда корректировки на изменение режимов резания попадает в блок управления 3, где создаются команды управления приводами станка.
<
Figure 1 – Block diagram of the adaptive process control system for the machining of parts on CNC machines [9]
The use of the proposed method makes it possible to obtain more accurate information on the wear rate of the cutting tool in the process of processing with a high degree of accuracy with respect to a number of parameters and, thus, to use the tool to its fullest extent in its stability properties, which ultimately allows increasing the productivity of machining of parts on CNC machines and reducing prime cost of the processed parts.
3.2 Control system of hydraulic machines for the example of thermoplastic automatic machine
And the last is a control system for hydraulic machines using the example of a thermoplastic automatic machine.
Main functions of the system:
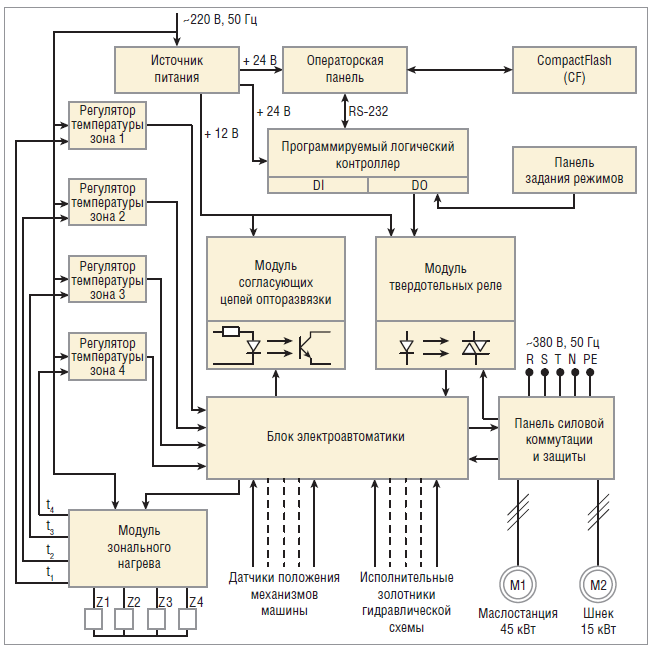
Figure 3 – Structural diagram of the automatic injection molding machine control system [10]
Legend: M1, M2 - electric motors; Z1 ... Z4 - heating elements; R, S, T - voltage phases; N is the neutral; PE - grounding; t1 ... t4 - temperature in the heating zones; DO, DI - discrete inputs and outputs [10].
The proposed version of the modernization of the SST has been introduced so far only at two machine-building enterprises: OJSC Tula Arms Plant
and OJSC Tula Machine-Building Plant nm. Ryabikov
. Almost two years of operation confirmed the validity of the engineering solutions chosen, which made it possible to achieve:
In addition, the configuration of the hardware and software of the system allows, in the case of modernization, to adapt in the shortest possible time to the hardware features of almost any hydraulic injection molding machine, which gives a real chance for replicating the developed system in similar plants and, as a result, .
Conclusion
Master's work is dedicated to improving the quality of processing due to the modernization of the control system of the lathe 16K20T1. When writing this essay, the master's work is not yet complete. Final completion: June 2018. The full text of the work and materials on the topic can be obtained from the author or his supervisor after the specified date.
References
- Бобров З.Ф. Основы теории резания металлов / З.Ф. Бобров. - М.: Машиностроение, 1975. - 344 с.
- Грановский Г.И. Резание металлов / Г.И. Грановский, В.Г. Грановский. - М.: Высшая школа, 1985. – 304 с.
- Основы автоматизации и управления технологическими процессами в машиностроении / Под ред. В.Ц. Зориктуева. - Уфа: Уфимск. гос. авиац. техн. ун-т, 2000. - 406 с.
- Рубенштейн С.А. Основы учения о резании металлов и режущий инструмент / С.А. Рубинштейн [и др.]. – М.: Машиностроение, 1968. – 386 с.
- KazouT., H. O. Wang. Fuzzy control systems design and analysis. JohnWiley&Sons, Inc, 2001. 303 p.
- Зориктуев В.Ц. Система автоматического управления режимами резания на основе нечеткой логики / В.Ц . Зориктуев, Р.Р. Шангареев. - Уфа: УГАТУ, 2010. - 8 с.
- Васильев С.В. ЭДС и температура резания / С.В. Васильев // Станки и инструмент, 1980, №10. – C. 20-22.
- Остафьев В.А. Адаптивная система управления / В.А Остафьев, В.В. Шевченко, Г.С. Тымчик // Механизация и автоматизация управления. – Киев, №1, 1983. – С. 18-20.
- Шарабура С.Н. Система адаптивного управления процессом обработки деталей на станках с ЧПУ / С.Н. Шарабура, В.В. Шевченко // Современные научные исследования и инновации. 2014. – № 6. Ч. 1.
- Деркач А.Д. Примеры решений на базе сенсорных панелей Weintek для АСУ ТП и встраиваемых систем / А.Д. Деркач, Р.В, Камалиев. В.Н. Маценко // Современные технологии автоматизации. – 2014. – № 3.