Abstract
Contents
- Introduction
- 1. Theme urgency
- 2. The purpose and objectives of the study, the planned results
- 3. Review of research and development
- 3.1 Functions of the device for automatic control of the conveyor belt of the technological process of the mine transport
- 3.2 Ensuring safe operation of the automation device
- Conclusion
- References
Introduction
Due to difficult production conditions, the majority of mining automation equipment requirements require increased reliability, protection in conditions of humidity, dust, vibration and, mainly, spark and explosion safety.
The tasks of automation are to ensure high production efficiency, operational safety through automatic monitoring of the main parameters of equipment and hazardous factors (gas, lack of ventilation), prevention of dangerous modes of operation of equipment and personnel, automatic alarms, interlocks, regulation and control.
The effectiveness of the introduction of automation depends on the flow of operations in production technology, the availability of integrated mechanization, the proper operation of equipment and other components.
The main means of delivery of goods at modern mining enterprises is conveyor transport. Belt conveyors effectively replace locomotive and cable hauling, which is due to their advantages such as continuity, wide possibilities for automation, the ability to transport goods in inclined workings, the ease of building and branching the line, relative safety.
1. Theme urgency
The main feature of conveyor transport as a control object is the high unevenness of the freight flow, caused by the fact that the conveyor line is a transport object serving its cleaning and preparatory slaughter in its technological purpose. And technological pauses in the operation of mechanisms (emergency stopping of lava, periodic changes in the speed of moving the combine along the lava, etc.) are the cause of uneven cargo traffic. The unevenness of the receipt of the load leads to an inefficient use of the drive's power (with underload), as well as excessive wear of the traction body and a decrease in the reliability of the blood pressure (with overload)[ 2].
Currently, there are 2 ways to reduce the unevenness of the cargo flow: the regulation of the speed of the drive motor of the conveyor and the use of intermediate storage bins.
The traffic from the lava is not a constant value, as a result of which, for a considerable part of the time, the conveyor works with incomplete loading. The power of the drive motors of the conveyors reaches hundreds of kilowatts, so improving the drive's energy performance will help reduce energy costs. To solve this problem, it is advisable to regulate the speed of the belt, depending on the cargo flow[ 14] .
There are two main ways to measure the mass of the cargo flow –it is a tensor and a balance using an ultrasonic measuring device.
The ultrasonic device measures the volumetric capacity cyclically with the frequency of the mains supply. Performance is measured only when the belt moves at the nominal speed. The ultrasonic pulse directed towards the tape that moves reflects from the surface of the material and is sent to the receiving transducer. The receiving transducer generates an electrical pulse, which is sent to the comparison unit. In the comparison block, the time of sending the pulse is compared with the time of its return, and an electric pulse is generated proportional to the time of passage by the ultrasonic pulse of the forward and return path[ 5] .
2.The purpose and objectives of the study, the planned results
The aim of the master's work is to increase the efficiency of the belt conveyor by justifying the control algorithm and developing an automation system with automatic conveyor control.
Requirements for the automation system of the belt conveyor are as follows:
- start and stop the pipeline;
- control of technological parameters and operating modes of the belt conveyor;
- automatic protection of the belt conveyor and its drive motor when the current values of technological parameters deviate from the specified or the mode of operation of the conveyor;
- automatic regulation of the operating mode of the belt conveyor depending on the cargo flow;
- data transmission to the computer of the belt conveyor automation system (upper level of control) for storing information and visualizing the status of the conveyor operation modes;
- reception of control commands from the industrial computer of the automation system;
- the design and the circuit
solution of the technical means of the automation system must comply
with the requirements of the
Rules for the manufacture of explosion
–proof andmine electrical equipment
– be an explosion-proof explosion–proof enclosure and an intrinsically safe electrical circuit, and be installed and operated in accordance with theRules for the Technical Operation of Coal and Shale Mines
[ 6] .
3. Review of research and development
Analysis of the mine conveyor belt as an automation object.
The technological process of transport of a mining enterprise is carried out by means of conveyor and rail transport.
The process of conveyor transport of a mine is a technological process of moving rock mass, materials, and in some cases people as well, with the help of conveyors for mine workings [5,14] .
On the mines for conveyor transport are used belt and scraper conveyors. The object of automation in master's work is a belt conveyor as part of a conveyor line. A belt conveyor is a continuous transport device with an integrated load–carrying and traction body in the form of a closed flexible belt. The belt is driven by a frictional force between it and the drive drum; is supported along the entire length by stationary roller bearings. The general view of the mine belt conveyor is shown in figure 1.
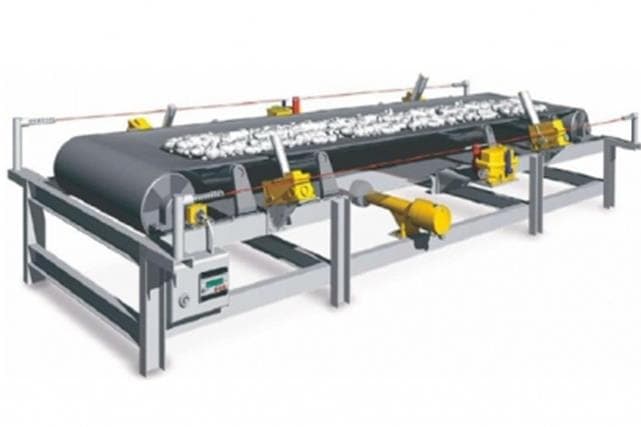
Figure 1. General view of the mine belt conveyor
In large coal mines, coal is transported from the face faces to the skip hoist through a multiline transport line consisting of precinct conveyor lines and prefabricated conveyors – trunk conveyor lines. The local belt conveyor line provides transportation of coal from the face face to the place of transshipment to the main conveyor line. As a rule, overloading is carried out through a storage bin. Currently, almost all conveyor lines in the mines are automated. The main type of control is automated control, the technical essence of which is to centralize the control of the start – up processes – stopping the conveyors in the line, providing automatic protection from the development of the accident in the event of emergency situations [9].
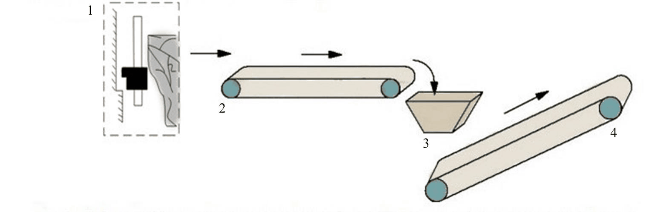
Figure
2 -Technological scheme of a multithreaded coal transport line from the
bottom face
(animation: 4 frames, 125 kilobytes)
(1 – cleaning face, 2 – preconditioner conveyor
line, 3 – bunker,
4 – trunk conveyor line)
3.1 Functions of the device for automatic control of the conveyor belt of the technological process of the mine transport
The automatic control device must perform the following functions:
–
starting the belt conveyor by switching on the magnetic starter of the
drive motor of the conveyor;
–
stopping the conveyor belt by disconnecting the magnetic starter of the
drive motor of the conveyor;
–
speed control of the belt;
–
control of the withdrawal of the belt from the roller conveyor of the
conveyor;
–
control of shaking the place of transfer of the transported material to
a subsequent conveyor or to a receiving hopper;
–
monitoring the speed of the drive drum;
–
control of the emergency level of loading of the receiving capacity of
the conveyor;
–
control of the presence of fire hazard;
–
control the speed of the tape;
–
control of the torque on the shaft of the drive motor;
–
protective shutdown of the conveyor when the belt speed is reduced by
more than 25% of the nominal value in the unregulated operating mode by
switching off the magnetic starter of the drive motor of the conveyor;
–
protective shut–off of the conveyor when the belt slips in
unregulated
mode with respect to the drive drum by disconnecting the magnetic
actuator of the drive motor of the conveyor;
– protective disconnection of the conveyor when the belt
comes off the
conveyor roller conveyors by disconnecting the magnetic actuator of the
drive motor of the conveyor;
– protective disconnection of the conveyor when shunting the
place of
transfer of the transported material to the subsequent conveyor or to
the receiving hopper by switching off the magnetic starter of the drive
motor of the conveyor;
–
protective shutdown of the conveyor at an emergency loading level of
the receiving capacity of the conveyor by switching off the magnetic
starter of the drive motor of the conveyor;
–
protective shutdown of the conveyor in the presence of fire hazard by
switching off the magnetic starter of the drive motor of the conveyor;
–
protective shutdown of the conveyor when the belt is overloaded by
disconnecting the magnetic actuator of the drive motor of the conveyor;
–
conveyor status indication (on, off);
–
indication of the cause of the conveyor stop:
a) operational stop;
b) stopping due to a decrease in the speed of the tape;
c) stop due to the withdrawal of the belt from the conveyor roller
conveyor;
d) shutdown due to shaking the place of transfer of the transported
material to a subsequent conveyor or to a receiving hopper;
e) stop due to the emergency loading level of the receiving capacity of
the conveyor;
f) stop due to fire hazard;
g) stop due to tape overload – transmission of data on the
state of
the conveyor and the reasons for stopping it in the industrial computer
of the automated work console of the dispatcher to the central control
room of the mine or to the console of the transport dispatcher of the
mine [4,13].
3.2 Ensuring safe operation of the automation device
The device for automatic regulation of the linear load on the conveyor belt is designed to provide a control action to the actuators of the belt conveyor drives and the tension station during start – up and during operation of the conveyor line. The control signal is reproduced from signals from the sensors controlling the speed of the tape, the withdrawal of the tape, the load of the transported material, the speed of the drive drum, fire hazard, tape tension, torque on the shaft of the drive motor, and the signal from the AUC – BN to the start and stop of the conveyor. The device protects the conveyor belt from inadmissible operating modes. The device for automatically regulating the linear load on the conveyor belt consists of the number of conveyor belts in the line. The device can be installed on one and several conveyors [12].
Conclusions
In the master's thesis, the analysis of the mine belt conveyor as an object of automation is performed and requirements are formulated for the device for automatic control of the conveyor belt.
The structure of automation system by a belt conveyor is proposed, which has two levels of control: the upper one is the level of the main dispatcher of the mine and the lower level of the belt conveyor. At the upper level, a computerized industrial workstation is provided, and on the lower level a new device designed in the work is provided – an automatic load stabilization device for the belt conveyor of the AUC – BN type.
When designing the AUC – BN device, all the design stages were performed: device functions were formulated, an algorithm for automatic control of the belt conveyor was developed, structural diagrams of the automation system and AUC – BN devices were developed, and a basic circuit diagram for the AUC – BN device was developed.
At the time of writing this essay master's work is not yet completed. Final completion: June 2018. The full text of the work and materials on the subject can be obtained from the author or his manager after the specified date.
References
- НПАОП 10.0-1.01-10. Правила безпеки у вугільних шахтах. Наказ Державного комітету України з промислової безпеки, охорони праці та гірничого нагляду №62 від 23.03.2010. – 150с.
- Пейсаховича Г.Я. Подземный транспорт шахт и рудников/ Под общей ред. Г.Я. Пейсаховича, И.П. Ремизова. –– М.: Недра, 1985. – 565 с.
- Груба В. И. Технические средства автоматизации в горной промышленности. – В. И. Груба, Э. К. Никулин, А. С. Оголобченко – К.: ИСМО, 1998.– 373 с.
- Стадник Н.И. Справочник по автоматизации шахтного конвейерного транспорта / Н. И. Стадник, В. Г. Ильюшенко, С. И. Егоров и др. – К.: Техника, 1992. – 438с.
- Иванов А.А. Автоматизация подземных горных работ/ Под ред. проф. А. А. Иванова. – К.: Вища школа, 1987. – 328с.
- Бедняк Г.И. Автоматизация производства на угольных шахтах/ Г. И. Бедняк, В. А. Ульшин, В. П. Довженко и др. – К.: Техника, 1989. – 272с.
- Хананов
Д.В. Аналіз процесів нагріву конвеєрної стрічки
при повній пробуксовці приводного барабана шахтного конвеєра в
аварійному режимі роботи. Наукові праці Донецького національного
технічного університету. Донецьк: ДВНЗ
ДонНТУ
, 2009. – 256–265c. - Толпежников Л.И. Автоматическое управление процессами шахт и рудников. –М.: Недра, 1985. –352 с.
- Овсянников Ю.А. Автоматизация подземного оборудования/Овсянников Ю.А., Кораблев А.А., Топорков А.А. : Справочник рабочего. - М.: Недра, 1990. – 287с.
- Жуйков В.А. Схемотехніка електронних систем: Підручник в двох томах/ Жуйков В.А., Бойко В.І., Зорі А.А., Співак В.М.. – К.: Аверс, 2002. - 772с. Том I. Аналогова схемотехніка та імпульсні устрої / Жуйков В.А., Бойко В.І., Зорі
- Гутников В. С. Интегральная электроника в измерительных устройствах. – Л.: Энергоатомиздат, 1988. – 304с.
- Петков О. Н. Разработка и исследование системы автоматического управления скоростью ленточного конвейера по входному грузопотоку / Диссертация на соискание ученой степени кандидата технических наук. – М.: Московский Ордена Трудового Красного Знамени Горный Институт, 1984. – 143с.
- Шахмейстер Л. Г., Дмитриев В. Г. Вероятностные методы расчета транспортирующих машин. – М.: Машиностроение, 1983. – 256с.
- Дмитриева В. В., Певзнер Л. Д. Автоматическая стабилизация погонной нагрузки ленточного конвейера: Отдельные статьи Горного информационно-аналитического бюллютеня. – 2004. – № 12. – М.: Издательство Московского государственного горного университета. – 25с.
- Папоян Р. Л. Повышение эффективности использования шахтных конвейерных линий автоматическим, регулированием скорости и определением грузопотоков. Кандидатская диссертация. – М., 1967. – 213с.