Content
- Introduction
- 1. Relevance of the topic
- 2. The purpose and objectives of the study, the planned results
- 3. Review of research and development
- 3.1 Overview of international sources
- 3.2 Review of national sources
- 3.3 Review of found patents
- 4. Description of the developed mechanism
- Conclusions
- List of sources
Introduction
Today, lime is widely used in the world in a wide area. One of the best areas of application is construction. It is well proven and took the first position in it. The main factor in obtaining prepared lime is a kiln. They have received the widest application and distribution throughout the world due to its simplicity in construction and operation. To date, there are many designs of mechanisms for unloading the finished material from the kiln in the furnace, they all have the right to life, they have their own differences and dignity.
In addition to the unloading mechanism in kilns, they also use: a material loading mechanism, a burning device for burning, and of course the mine itself. Like all kinds of equipment, everything is subject to various kinds of damage and malfunctions that may occur during the operation of the mechanism.
The purpose of the study is to compare the already known systems for unloading limestone from a shaft furnace with the developed unloading mechanism. The main task is to compare the systems, find common features and design the installation that will be as efficient as possible and contain at least the shortcomings of the previous ones.
1. Relevance of the topic
Today, lime is widely used in the world in a wide area. One of the best areas of application is construction. It is well proven and took the first position in it.
2. Description of the object of study
The fundamental factor for the production of lime is a kiln for raw material. For the production of the finished product, it is necessary to use various combustible materials in the form of fuel; one of the following types of fuel can be used: natural, solid, gaseous, artificially solid, and liquid. The best is the use of coal, natural gas, coke, fuel oil in the form of fuel for this process.
Heating of unprepared limestone occurs in a furnace at a temperature of 200 to 800 degrees Celsius, while the heating of dolomites is in the range of 200 to 600 degrees Celsius. In the process of heating, the material increases in volume by 3-4% from the original, however, its compressive strength decreases by about 40% - 70%. If you describe this process more simply, then there is a reversible decomposition of the substance. In order to obtain the final product, it is necessary to raise the temperature to 1200 degrees.
The elasticity of pure limestone during dissipation reaches a pressure in the atmosphere of 101 kPa at a heating temperature of up to 898 degrees. For other carbonate substances, this indicator can vary in the limit from 800 to 950 degrees Celsius. During the limestone kiln firing process, the dissociation temperature should fluctuate in the range of 810-850 degrees. From this we can conclude that the burning rate of the material depends on the temperature inside the furnace, and the heat transfer coefficient between the materials.
The firing process can be described according to the principle of dividing the shaft furnace into separate thermal zones.
3.1 Overview of international sources
Following the patent search, the following foreign patents of mechanisms were found for comparison:
- Pat. 328627 Deutsches reich, klasse 80c / Firma G. Polysis in Dessau / Pattentlert im Deutschen Reiche vom. 4 Juli 1916
- Pat. 2153030 USA, IPC B65G65 / Device for feeding materials / William H. Venebl. - № 161172; filed 27.08.1937; 04/04/1939 published
- Pat. 351577 Deutsches reich, klasse 80c / Firma G. Polysis in Dessau / Pattentlert im Deutschen Reiche vom. 28 Juli 1919
- Application: 2016119781, 05.23.2016 / Published: 06/27/2017 Bul. No. 18 / Patentee (s): Federal State Autonomous Educational Institution of Higher Education "National Research Technological University" MISiS "(RU)
3.3 Review of found patents
Pat. 328627 Deutsches reich, klasse 80c / Firma G. Polysis in Dessau / Pattentlert im Deutschen Reiche vom. 4 Juli 1916
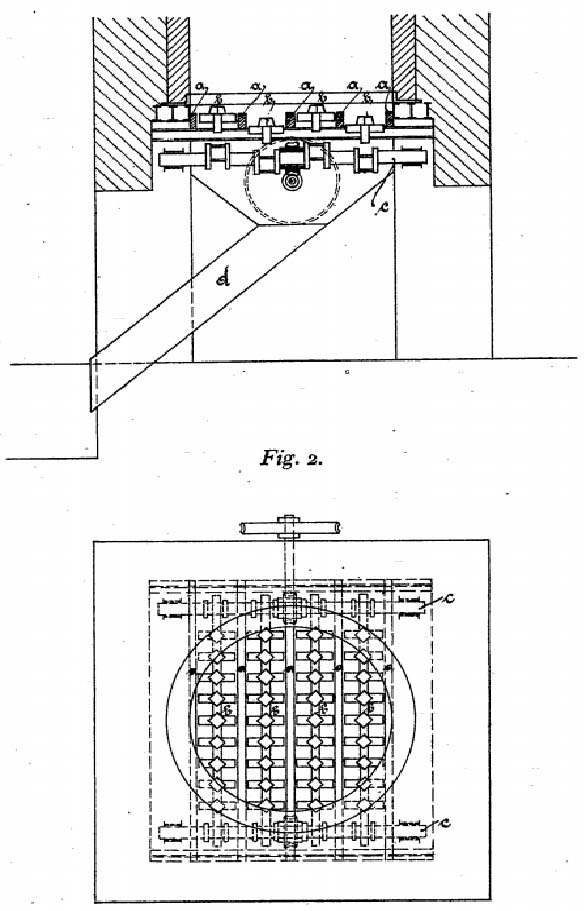
Figure 2 - General view of the mechanism for unloading lime
Pat. 2153030 USA, IPC B65G65 / Device for feeding materials / William H. Venebl. - № 161172; filed 27.08.1937; 04/04/1939 published
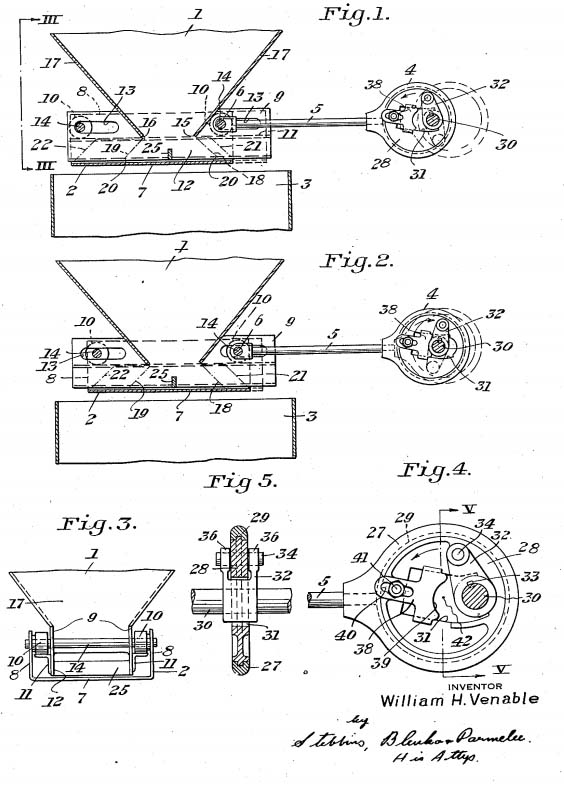
Figure 3 - Drive mechanism
3. Pat. 351577 Deutsches reich, klasse 80c / Firma G. Polysis in Dessau / Pattentlert im Deutschen Reiche vom. 28 Juli 1919.
The invention relates to unloading devices, and more specifically, to a unloading mechanism for removing coke and ash from gas generators of the mine type.
Some discharge mechanisms for removing coke and ash from shaft type gas generators were designed so that if a column of fuel in the mine was blown up from the periphery - the center - the dissociation of the fuel from the base of the column was arranged faster at the periphery than in the center.
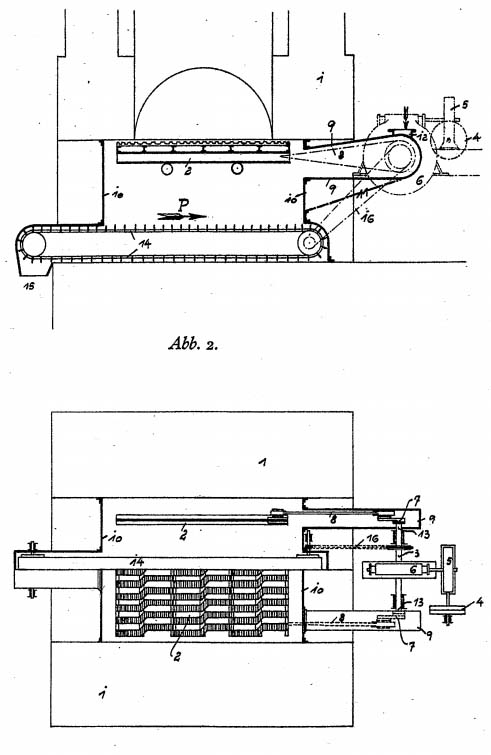
Figure 4 - General view of the mechanism, its devices in different projections
Application: 2016119781, 05/23/2016 / Published: 06/27/2017 Bul. No. 18 / Patentee (s): Federal State Autonomous Educational Institution of Higher Education "National Research Technological University" MISiS "(RU)
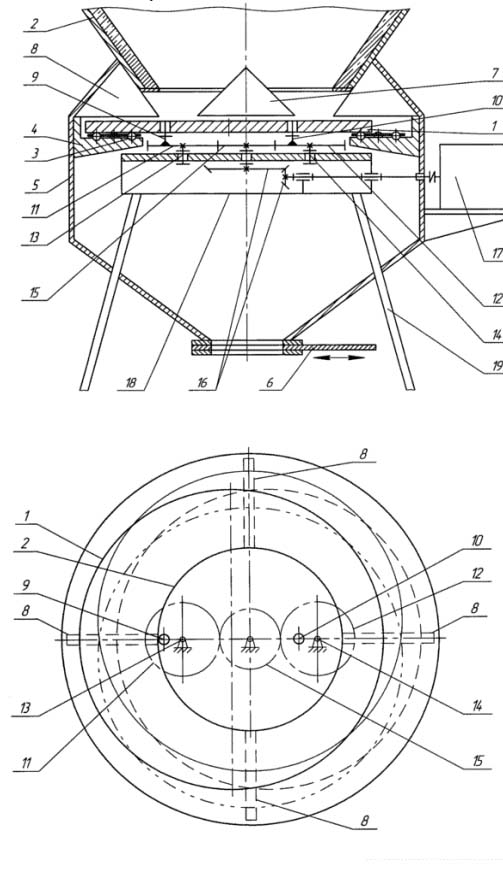
Figure 5 - General view of the mechanism for unloading lime
The device contains a sub, mounted on the rolling elements with the possibility of movement in a horizontal plane relative to the shaft of the furnace for issuing lime to the periphery through the gap between it and the lower part of the shaft, knives with an adjustable angle of attack for dropping lime into the receiving bin and a conical cap located in the center of the bottom of the mine above the hearth
4. Description of the developed mechanism
In this design, there are four scraper knives that are directly related to each other. Their connection is carried out with the help of connecting axles and slats. Unloading of the sintered material is carried out by pouring material through the edges of the unloading table due to the movement of the knives. At the same time, the main movements are performed exclusively by scraping knives, while the table itself remains stationary. It should be noted that the design of the mine was changed, it is crowned with a conical hole. This step was taken to ensure that the material is not affected by the natural angle of the slope, and he himself did not pour over the edge of the knives.
The general view and kinematic diagram of the device are shown below.
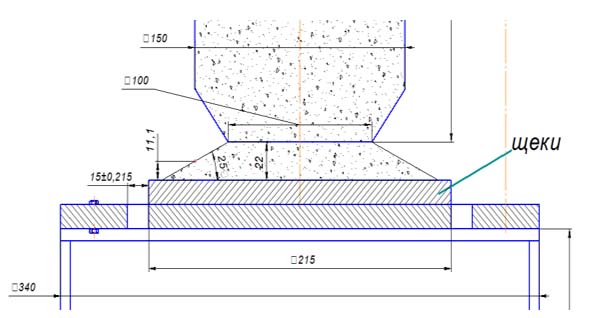
Figure 6 - General view of the unloading mechanism
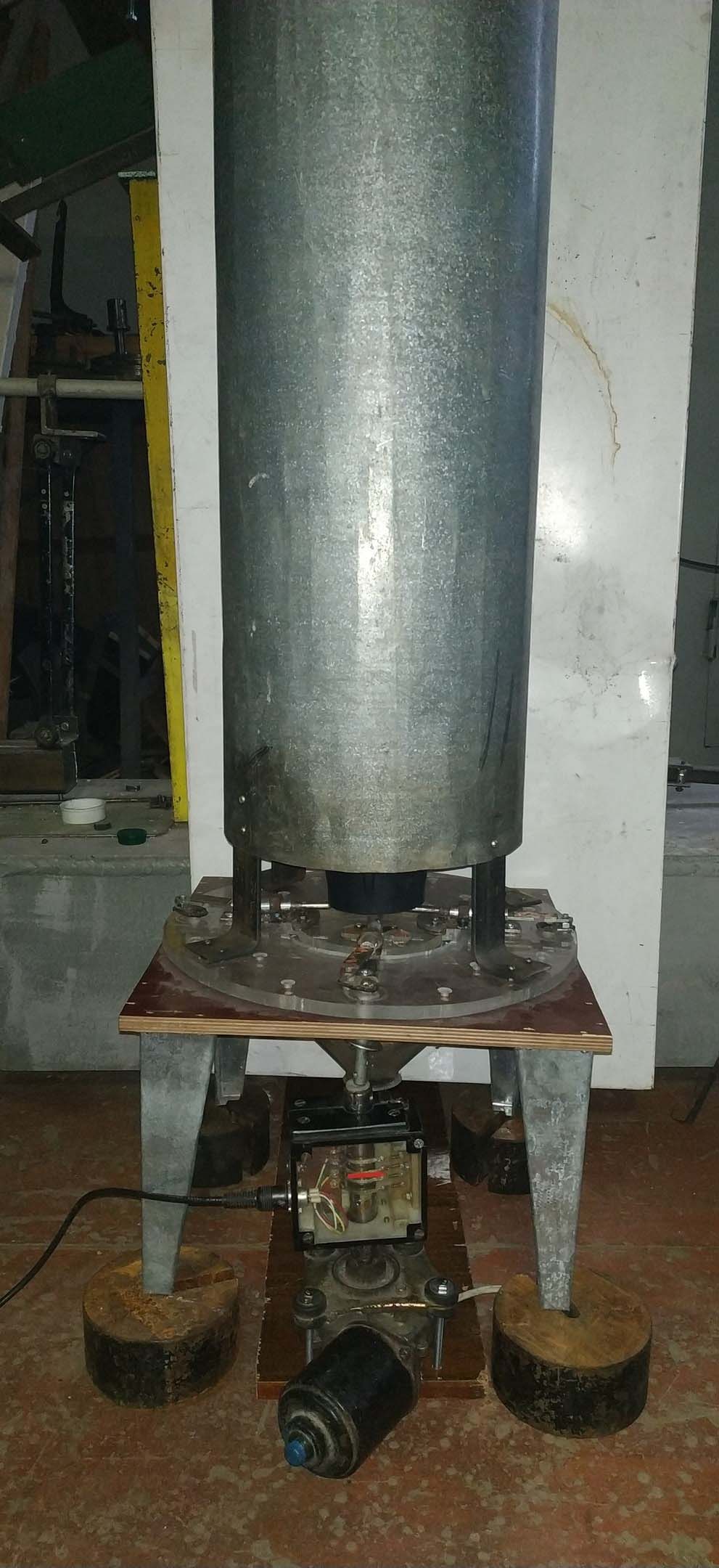
Figure 7 - Model photo
Findings
In the course of the master’s work, a patent search was conducted by country. Similar and distinguishing features were identified, and the following disadvantages were identified: uneven unloading of the finished product; difficult work; The prototype has a complex structure. It is possible to apply hardening to increase the reliability of the device.
Further research is aimed at obtaining experimental data and developing a calculation system with obtaining theoretical dependencies.
At the time of writing this essay, the master's work has not yet been completed.
Список источников
- Advanced patent search - Google; [Electronic resource]. - Access mode: Advanced patent search
- Patents for inventions of the Russian Federation and patent search in libraries of Russia and other states; [Electronic resource]. - Access mode: Patents for inventions of the Russian Federation
- Patent search in the database of patents and inventions registered in the Russian Federation and the USSR, free patent research; [Electronic resource]. - Access mode: Patent search in the base of patents and inventions of the USSR
- Расчеты печей силикатной промышленности. В.Н. Гурина, И.Б. Ревва – 2-е издание, Томский политехнический университет. 2011 г.
- Печи для производства извести, Справочник А.В. Монастырев, А.В. Александров. «Металлургия», Москва – 1979 г. – 10-70 с.
- Приводы машин: Справочник/В. В. Длоугий, Т. И. Муха, А. П.Цупиков, Б. В. Януш; Под общ. редакцией В. В. Длоугого. – 2-е изд., перераб. И доп. – Л.: Машиностроение, Ленингр. отд-ние, 1982. – 383 с.
- Башта Т. М. Гидропривод и гидропневмоавтоматика//М., «Машиностроение», 1972, 230 с.
- Монастырев А.В., Александров А.В. Печи для производства извести.Справочник. – М.: Металлургия, 1979. – 232 с.
- Табунщиков Н.П. Производство извести. – М.: Химия, 1974. – 240 с.
- Монастырев А.В. Производство извести. – М.: Высшая школа, 1978. –225 с.
- Производство извести и сатурационного газа на сахарных заводах / Н.П. Табунщиков, Э.Т. Аксенов, Р.Я. Гуревич, Л.Д. Шевцов. – М.: Легкая и пищевая промышленность, 1981. – 176 с.
- Баренбойм А.М., Галиева Т.М., Гинзбург Д.Б. и др. – М.: Строй-издат, 1964.
- Левченко П.В. Расчеты печей и сушил силикатной промышленности.– М.: Высшая школа, 2002. – 368 с.
- Никифорова Н.М. Теплотехника и теплотехническое оборудова-ние предприятий промышленности строительных материалов и изделий. – М.: Высшая школа, 1981. – 270 с.
- Огнеупоры и огнеупорные изделия. – М.: Издательство стандартов, 1975. – 671 с
- Воробьев Х.С., Мазуров Д.Я. Теплотехнологические процессы и аппараты силикатных производств. – М.: Высшая школа, 1965. – 773 с.