Abstract
Content
- Introduction
- 1. Relevance of the topic
- 2. Purpose of the study
- 3. Review of existing research
- 4. Analysis of the general principles of technological machines, basic properties, features and characteristics
- Findings
- List of sources
Introduction
Automate – qualitatively the highest historical level of development of technology. What does automation mean? Following the definition given K. Marx, by the automation of technological processes, we understand the transfer of all functions for the direct processing of raw materials to a machine. The man is left with only the functions of observation, control over the operation of the machine and regulation of the process.[6][7]
Comprehensive automation of production is the highest form of automation of technological processes, providing a significant increase in productivity. labor, increasing output, improving quality and reducing the cost of its production.
What is the difference between complex automation and automation in general, the problems of which were formulated by K. Marx? Why are we not only talking about quantitative difference between these concepts?
The very name of the «integrated automation» It says that production automation issues are resolved in a comprehensive manner, that is, they cover all aspects of production process, including both basic and auxiliary operations of the manufacturing process of the product from the supply of the source material to the transfer of finished products to the warehouse and waste disposal. The processes of management of the technological process, operational management and planning of production as a whole are also automated. This causes a further and significant increase in all technical and economic indicators of production.[8][9][10]
1. Relevance of the topic
Currently, fasteners such as bolts, screws, washers, self-locking nuts, screws, nails, etc. are widely used. Separate process equipment is used for their manufacture, which is inefficient because it requires large maintenance costs. production areas, transportation of parts from the machine to the machine, etc., the solution to this problem is highly automated production. The simultaneous production of these products on one technological line will allow to increase the technical and economic indicators of their manufacture, to reduce cost price and avoid shipping costs.
2. Purpose of the study
The aim of the study is to increase the efficiency of production of fasteners based on multi-nozzle rotary lines based on the merger of a large-scale group. productions in diversified mass.
Currently, the problem of automating the manufacture of products is one of the most pressing. However, along with this, there is a desire of manufacturers meet the needs of each individual customer, which leads to the need to increase the range of products produced, along with the automation of their production. The implementation of a multi-product process for the manufacture of products on rotary systems will make it possible to realize serial production on highly efficient systems, intended for mass production. Designed group and modular technologies, as well as well-known design solutions allow these conditions to be implemented. processing, however, the implementation of these technologies on rotor systems faces a number of problems associated with the insufficient development of Various factors in the multiproduct process.
3. Review of existing research
Currently, a large number of studies on the development of rotors and rotary lines. The efforts of many scientists made significant contribution to development. Among them are L.N. Koshkin, V.V. Preiss, I.A. Klusov, and others.
4. Analysis of the general principles of technological machines, basic properties, features and characteristics
The technological machine in the process of manufacturing the product performs two main and opposite functions: technological movement and transport movement. Based on this situation and given that the production line should have the quality of continuity of technological and transport movements, L.N. Koshkin proposed a classification of technological machines, which is based on the nature of the relations of transport and technological movements among themselves. and their effect on the performance and design features of the machines. According to this criterion, all technological machines are divided into four classes. [1]
Machines of the third class (figure 1) differ from machines of the second class by the independence between transport and technological movements.
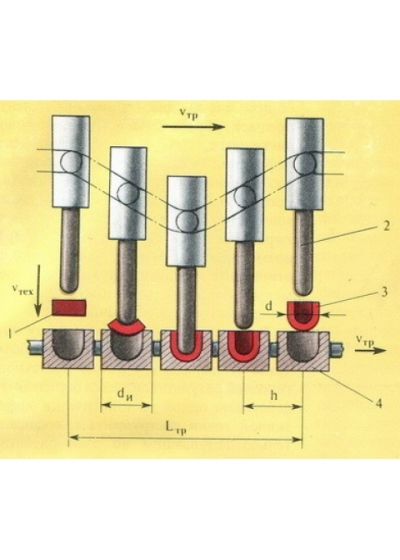
Figure 1 - Schematic diagram of the machines of the third class:
1, 3 - subject of processing; 2, 4 - tool;
The performance of third-class machines, as well as second-class machines, is determined by the length of the exhaust cycle, but unlike them, it is not limited directly to the technological speed processing, therefore, when creating machines of the third class, an increase in their productivity is theoretically connected only with an increase in the transport speed.
Findings
Multi-nozzle rotor systems allow them to be sufficiently loaded by expanding technological capabilities of these systems, and a comprehensive solution to the problems of the structural complexity of multi-rotor systems is the choice of a rational structure of the flow of products, followed by the design of rational structural elements of these systems.
List of sources
- Прейс, В.В. Технологические роторные машины вчера, сегодня, завтра/В.В. Прейс, М.:1986
- Михайлов, А.Н. Основы проектирования и автоматизации производственных процессов на базе технологий непрерывного действия/А.Н. Михайлов, Д.:2006
- Кошкин, Л.Н. Роторные и роторно-конвейерные линии/Л.Н. Кошкин, М.:1982
- Клусов, И.А. и др. Автоматизация сборочных процессов на роторных линиях - Киев, 1967 - 48 с.
- Кошкин, Л.Н. Комплексная автоматизация на базе роторных линий/ Л.Н. Кошкин, М.:,1999.
- Клусов, И.А. Роторные автоматические линии/И.А. Клусов,М.:, 1989
- Владзиевский, А.П. Автоматические линии/А.П. Владзиевский, М.:1958
- Феденя, А.К. Организация производства и управление предприятием: Учеб. пособие/ А.К. Феденя. – Мн.: Тетра-Системс, 2004. – 192с.
- Соломатин, Н.А. Управление производством: Учебник/ под ред. Н.А. Соломатина. – М.: ИНФРА – М, 2001. – 219 с.
- Владзиевский, А.П. Автоматические линии в машиностроении/ А.П. Владзиевский , М., 1988
- Кошкин, Л.Н., Густов, А.А. Роторные машины для механической обработки/ Л.Н. Кошкин, А.А. Густов, К.,2002.