Фінішна обробка зубів зубчастих коліс
Зміст
- Вступ
- 1. Актуальність теми
- 2. Мета і задачі дослідження
- 3. Огляд досліджень
- 3.1 Вимоги, що пред’являються до зубчастих передач
- 3.2 Ознаки зниження працездатності зубчастих передач
- 3.3 Обробка зубчастих коліс
- Висновки
- Перелік посилань
Вступ
У сучасному світі більшість машин і механізмів важко уявити без зубчастих коліс. Хоча ім’я винахідника зубчастого колеса невідоме, безумовно, його можна назвати одним з великих винахідників. Своє застосування зубчасті колеса знайшли ще в глибоку давнину. Їх застосування обумовлювалось необхідністю перетворення і передачі механічної енергії від природного джерела до споживача. Спочатку вони відрізнялися своєю формою від сучасних і виготовлялися з дерева. Починаючи з XVIII ст., з розвитком таких наук як геометрія, кінематика і механіка, профіль зубів удосконалювався, набуваючи більш раціональну форму і обриси.
Зараз зубчасті передачі є одним з найважливіших елементів різних приладів, машин і механізмів. Від їх якості залежать експлуатаційні властивості і надійність цих машин. Вони застосовуються для перетворення обертального руху в поступальний, а також для передачі обертального рухи між осями валів. Застосування зубчастих передач обумовлено низкою переваг в порівнянні з іншими видами передач. Цими перевагами є:
- надійність в роботі;
- сталість передавального числа;
- довговічність;
- високий ККД;
- простота експлуатації;
- компактність;
Зубчасті колеса класифікуються в залежності від конструктивного виконання: циліндричні, черв’ячні, конічні.
1. Актуальність теми
Зубчасті передачі є найбільш поширеним видом силових передач. Якість їх роботи залежить від точності і якості поверхонь зубів зубчастих коліс, які досягаються головним чином на етапах обробної і зміцнюючої обробки. Зубчастий вінець є елементом зі складним періодичним профілем і виходить шляхом механічної обробки. Це вимагає високих витрат трудомісткості механічної обробки і призначення додаткових припусків, пов’язаних з досягненням необхідної точності і якості зубів. Фінішна і обробна обробка зубів, зважаючи на велику площу поверхні зубчастого вінця, вимагає не менших витрат трудомісткості, яка значно збільшується при підвищенні вимог до точності зубчастих коліс. Тому в даний час актуальною є завдання підвищення продуктивності і якості обробної обробки зубів зубчастих коліс.
На підставі вищевикладеного, дана робота актуальна, і присвячена вирішенню питань підвищення продуктивності і якості обробної обробки зубчастих коліс перед нанесенням покриттів.
2. Мета і задачі дослідження
Мета роботи: Підвищення продуктивності і якості обробки зубів зубчастих коліс за рахунок вдосконалення технології фінішної обробки зубів і нанесення спеціальних покриттів.
Основні завдання дослідження:
- Виконати аналіз умов роботи зубчастих коліс, визначити основні вимоги до зубчастих колес для забезпечення надійної і безвідмовної їх роботи
- На основі морфологічного аналізу, визначити найбільш раціональні методи обробної і зміцнюючої обробки зубів.
- Розробити загальну структуру технологічного процесу обробної і зміцнюючої обробки зубів, що забезпечує підвищення експлуатаційних характеристик зубчастих коліс.
- Запропонувати раціональний метод фінішної обробки зубів, що забезпечує підвищення продуктивності полірування бічних поверхонь зубів.
- Виконати дослідження впливу вхідних параметрів фінішної обробки на якість одержуваної поверхні зубів.
- Розробити рекомендації щодо підвищення продуктивності фінішної обробки зубів і якості оброблюваних поверхонь.
3. Огляд досліджень
3.1 Вимоги, що пред’являються до зубчастих передач
На працездатність зубчастого зачеплення впливають такі зовнішні фактори [1]:
- Значення фактичної додається силового навантаження, оскільки розрахункова, номінальна навантаження не призводить до зміни форми зуба і не залишає значних слідів деформації на робочій поверхні зубчастої передачі.;
- Наявність абразивних частинок, що сприяють абразивному зносу; або хімічних речовин викликають корозію поверхонь зубів, що сприяють виникненню газової або рідинної ерозії. Основна причина корозії – наявність води в мастильному матеріалі – проявляється у вигляді рівномірного або нерівномірного шару іржі на поверхні зубів. Ступінь корозії може бути різною.;
- Ступінь взаємного переміщення зубчастого колеса щодо вала. Нерухомість посадочних поверхонь зубчастого колеса і вала задовольняє проектним вимогам у тому випадку, якщо сполучаються деталі залишаються нерухомими при додатку навантаження. Поява малих переміщень сполучаються деталей призводить до фреттинг–корозії, що виявляється у вигляді темних плям на посадковій поверхні деталі.;
- Характер взаємодії контактуючих поверхонь, яка визначається видом тертя на контактуючих поверхнях. Якщо переважає рідинне тертя, що забезпечує мінімальний коефіцієнт тертя, і відбувається повне розділення контактуючих поверхонь шаром масла, то стан оцінюють як добрий. В цьому випадку переважаючим є окислювальний знос. Виникнення граничного тертя призводить до контакту двох деталей, проявляючись в поліруванні робочих поверхонь зубів. Найбільш часто граничне тертя проявляється на початковій стадії приробітку нових зубчастих коліс.
Умови роботи зубчастих коліс визначаються їх швидкохідністю, рівнем контактних і згинальних навантажень.
В процесі експлуатації зуби зубчастих коліс піддаються [1]:
- вигину при максимальному одноразовому навантаженні ( при різкому гальмуванні, заклинюванні, при додатку максимального крутного моменту);
- вигину при багаторазових циклічних навантаженнях, що призводить до розвитку найбільших напруг в корені зуба і втомного руйнування;
- контактним напругам на бічних робочих поверхнях зубів, що призводить до утворення контактно-втомного викришування (пітингу);
- зносу бічних поверхонь (через попадання абразивних частинок, бруду, пилу в зону контакту), або торцевих поверхонь зубів (при перемиканні передач в коробках передач).
У зв’язку з цим зубцям зубчастих коліс пред’являються такі вимоги:
- висока зносостійкість робочих поверхонь;
- високий ККД;
- безшумність і плавність ходу;
- висока кінематична точність передачі;
- висока втомна міцність зубів.
Ці вимоги можуть бути реалізовані за допомогою термічної, хіміко–термічної, чистової, обробної обробки, зміцнення методом ППД.
Разом з цими вимогами приписуються вимоги по точності зубчастих коліс. Допуски на циліндричні зубчасті передачі визначені стандарт. ГОСТ 1643-81 встановлює 12 ступенів точності зубчастих коліс і передач [2].
Для кожного ступеня точності встановлені незалежні норми допустимих відхилень параметрів, які визначають: кінематичну точність; плавність роботи; контакт зубів в передачі [2].
Також ГОСТ 1643-81 встановлено шість видів сполучень, що визначають гарантований бічний зазор. Бічний зазор – це відстань, виміряне по нормалі між неробочими профілями зубів Сполучених коліс.
Мінімальна величина бічного зазору необхідна для:
- розміщення мастила;
- компенсації температурних деформацій;
- компенсації похибок виготовлення і монтажу передачі.
Точність виготовлення зубчастих коліс і передач задається ступенем точності, а вимоги до бічного зазору – видом сполучення по нормалі бічного зазору.[2]
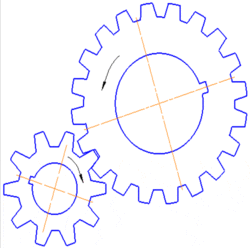
Малюнок 1 – Зубчаста передача (анімація: 8 кадрів, 65 Кбайт)"
3.2 Ознаки зниження працездатності зубчастих передач
Основні ознаки зниження експлуатаційних властивостей зубчастих передач [3]:
- Шум в роботі. Виникає внаслідок ударів і тертя Сполучених пар зубів. Причинами можуть бути: підвищені бічні зазори, пульсуючі знако-змінні навантаження, взаємне ковзання профілів, кромочний контакт.;
- Механічний. Виникає внаслідок тертя робочих профілів при відсутності або недостатній кількості мастильного матеріалу в зоні контакту зубів. Наявність твердих частинок продуктів зносу в мастильному матеріалі.;
- Викришування. Причиною можуть бути контактні напруги, гідродинамічні явища в мастильному матеріалі.
- втомний знос. Супроводжується появою тріщин на робочому профілі зубів. Причини: контактні напруги, динамічні навантаження різні за величиною і напрямком.;
- Окислювальний знос. Причина: робота зубчастих передач в агресивних середовищах і в умовах підвищеної вологості.;
- Деформаційний знос. Виявляється у вигляді пластичної деформації поверхневого шару зубів. Причини: невідповідність форми сполучаються зубів теоретичного профілю. Кромочний контакт. Нерівномірний розподіл навантаження по довжині зуба.;
- Заїдання. Обмеження вільного обкатування сполучаються зубів.;
- Поломка – виламування окремих зубів. Дія підвищених згинальних напруг у ніжки зуба, нерівномірний розподіл навантаження по окремих зубах, викликане похибкою окружного кроку, дія пульсуючих знако–змінних навантажень.
Серед розглянутих ознак, шум в роботі, поломка і заїдання викликані головним чином порушеннями нормальних умов роботи зубчастої передачі, а знос є поступовою втратою ЗК первісної форми, розмірів і властивостей, і може стати причиною інших ознак порушення експлуатаційних характеристика. Таким чином основним завданням сучасних технологій є зниження швидкості поширення зносу різних елементів ЗК [3].
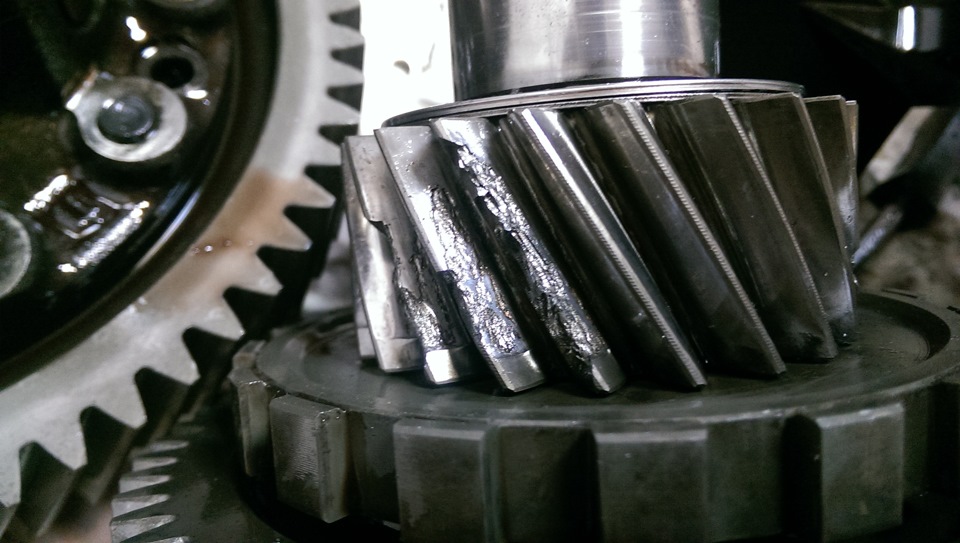
Малюнок 2 – Наслідки заїдання зубчастого колеса
3.3 Обробка зубчастих коліс
Обробка зубчастого вінця відбувається в три етапи:
- попередня;
- чистова;
- фінішна.
Обробна або фінішна обробка зубів. На цьому етапі здійснюється абразивна обробка зубів з метою забезпечення точності і якості поверхні, порушених при виконанні зміцнюючої обробки і подальшого досягнення точності для приведення зубчастого колеса до відповідності вимогам креслення. Використовується зубошліфування (методом копіювання або обкатки), зубохонінгування і притирання зубів.
Слід зазначити що зубчасті колеса, піддаються нанесення зносостійких покриттів, хоч і не вимагають дорогої термічної обробки, однак мають деякі особливості обробки робочих поверхонь зубів, оскільки в подальшому вони є підкладкою під покриття.
Основною вимогою до поверхні підкладки є її низька шорсткість (до Ra=0,16...0,08 мкм) і достатня чистота поверхні, виключає присутність в поверхневому шарі неорганічних включень і масляних плівок. Останнє досягається ультразвукової мийкою і знежиренням безпосередньо перед приміщенням виробів в камеру для нанесення покриттів. Досягнення необхідної шорсткості поверхонь зубів вводить додаткові етапи обробної механічної обробки. Після досягнення точності зубчастого вінця, що виражається комплексом параметрів відповідних заданому класу точності, проводиться подальша обробна обробка зубів. Шорсткість після розмірної обробки зубів не повинна бути більше Ra=1,6 мкм, що може бути досягнуто зубошліфуванням, шевінгуванням або зубохонінгованіем. Подальший обробка повинна бути спрямована головним чином на згладжування мікронерівностей поверхні з метою досягнення більш низької шорсткості. Для цього використовується полірування [4]. Причому для досягнення зазначеної шорсткості під нанесення покриття потрібно 3 етапи. На першому етапі–попереднє полірування, в якості інструменту використовується бавовняний або фетровий круг, накатаний абразивним порошком електрокорунду білого зернистістю 6-3. В результаті досягається шорсткість Ra=0,63-0,32 мкм. Швидкість кола 25-30 м/с, швидкість подачі 4-6 м / хв, Тиск полірувального кола 0,2 МПа. Остаточне полірування до шорсткості Ra=0,32-0,16 мкм проводиться м’якими бавовняними колами пасмами на основі окису хрому або окису заліза, або накатані микрошлифпорошком зернистістю М2-М14. Швидкість кола 30-35 м/с, подача 6 м/хв, тиск 0,1-0,15 Мпа. Третій етап – глянцювання до шорсткості Ra=0,08-0,04 мкм проводиться м’яким повстяним колом пастою на основі окису хрому з зернистістю микрошлифопорошка М10-М7. Швидкість кола 30-35 м/с, швидкість подачі – 6-8 м/хв, тиск інструменту на деталь 0,05-0,1 Мпа [4].
4. Висновки
В роботі розглянуті: вимоги до зубчастих передач, причини виходу з ладу та зниження експлуатаційних властивостей зубчастих коліс, особливості обробної обробки зубів зубчастих коліс, що піддаються нанесенню зносостійких покриттів. Проведено аналіз розглянутих ознак зниження властивостей зубчастих передач, і способи їх усунення. Поставлені цілі і завдання майбутніх досліджень.
Перелік посилань
- Александров Л. И., Артеменко Л. П., Костюк Д. И. Зубчатые передачи. Харьков: Издательство харьковского университета, 1964. 276 с.
- Бароне, Тордьон Точное распределение напряжений в стандартных зубьях и геометрические коэффициенты.//Труды американского общества инженеров – механиков, Серия В, 1973. № 4. С. 271–176.
- Аттиа Шум эвольвентных косозубых колес//Труды американского общества инженеров –механиков, Серия В, 1969. № 1. С. 179–186.
- Адам Я. И., Антонов О. И., Жарков В. В., Копф И. А., Овумян Г. Г. Чистовая обработка зубьев крупных закаленных колес // Вестник машиностроения, 1980. № 9
- Айрапетов Э. Л., Апархов В. И., Мельникова Т. Н., Филимонова Н. И. Неравномерность распределения статической нагрузки в косозубых и шевронных зубчатых передачах // Вестник машиностроения, 1997. № 10.
- Айрапетов Э. Л., Афонский Б Д., Генкин Б. Д., Луценко В. И., Мдинарадзе Н. И. Об анализе кинематической погрешности зубчатых передач с использованием фильтрации// Вестник машиностроения, 1985. № 3.
- Байков А. Н., Шрайбман С. М. Нарезание колес с малым числом зубьев на зубодолбежном станке // Вестник машиностроения, 1973. № 7.