Реферат за темою випускної роботи
Зміст
- Вступ
- 1. Актуальність теми
- 2. Мета і завдання дослідження, плановані результати
- 3. Огляд досліджень і розробок
- 3.1 Класифікація гальмівних пристроїв
- 3.2 Існуючі системи гальмування
- 3.3 Фрикційні пари гальмівних пристроїв
- 4. Вибір і аналіз геометричної форми фрикційної колодки
- Висновки
- Список джерел
Вступ
В основних напрямках економічного і соціального розвитку ДНР, вказується на необхідність у вугільній промисловості. У складному ланцюгу операцій, пов'язаних з видобутком вугілля, важливе число займають підйомні установки. Загальна тенденція до підвищення концентрації виробництва, необхідність переходу до розробки більш глибоких горизонтів накладають свої відбиток на характер розвитку і вдосконалення обладнання шахтного підйому.Збільшення обсягів видобутку корисних копалин вимагає розробки більш глибоких горизонтів а значить, і підвищення ефективності і надійності роботи шахтних підйомних установок, що, будучи створені і освоєні промисловістю, за технічними характеристиками не поступаються кращим зарубіжним зразкам.
Значні резерви підвищення продуктивності шахтного підйому сучасних шахт є в збільшенні ємності і швидкості руху підйомних посудин скорочення часу перехідних процесів (уповільнення, прискорення) в результаті вдосконалення конструкції підйомних машин і систем керування електроприводом підйому.За останні тридцять років в нашій країні максимальна швидкість руху судин шахтних підйомних установок збільшився в 1,4 рази і досягла 14 м / с, глибина підйому – в 1,8 рази і становила на ряді шахт 1500–2000 м, вантажопідйомність судин – в 3 рази і досягла для вугільних шахт 30 т, для залізорудних – 50 т. Передбачається, що в найближчі роки глибини підйому, швидкість руху і корисна ємність судин будуть рости більш інтенсивно. Проектуються шахтні підйомні машини ємністю скипів 50 т для вугільних і 100 т для залізорудних шахт при максимальній швидкості руху підйомних посудин 20 м / с.При створенні таких надпотужних комплексів на перший план виступають питання їх безпечної експлуатації. Відомо, що основним засобом захисту підйомної установки від аварії є її гальмівна система.
1. Актуальність теми
Збільшення обсягів видобутку корисних копалин вимагає розробки більш глибоких горизонтів а значить, і підвищення ефективності і надійності роботи шахтних підйомних установок, що, будучи створені і освоєні промисловістю, за технічними характеристиками не поступаються кращим зарубіжним зразкам. За останні тридцять років в нашій країні максимальна швидкість руху судин шахтних підйомних установок збільшилася в 1,4 рази і досягла 14 м / с, висота підйому – в 1,8 рази і становила на ряді шахт 1500–2000 м, вантажопідйомність судин – в 3 рази і досягла для вугільних шахт 30 т, для залізорудних – 50 т. Передбачається, що в найближчі роки глибини підйому, швидкість руху і корисна ємність судин будуть рости більш інтенсивно. Проектуються шахтні підйомні машини ємністю скипів 50 т для вугільних і 100 т для залізорудних шахт при максимальній швидкості руху підйомних посудин 20 м / с.
При створенні таких надпотужних комплексів на перший план виступають питання їх безпечної експлуатації. Відомо, що основним засобом захисту підйомної установки від аварії є її гальмівна система. Не випадково в останні роки багато дослідників приділяють особливу увагу вивченню динамічних процесів, що протікають в елементах гальмівної системи і підйомної установки в режимах гальмування, питань ефективності застосування і надійності гальмових систем, створення нових технічних засобів, що забезпечують програмне запобіжне гальмування. Великий внесок у вирішення проблеми забезпечення безаварійної експлуатації шахтних підйомних установок внесли Е. С. Трауб, А. Г. Степанов, Н. Г. Гаркуша, А. Н. Шатило, Л. В. Колосов, А. А. Белоцерьковскій, А. П. Нестеров та інші радянські вчені. На основі результатів досліджень динаміки підйомної установки як багатомасової системи з пружними зв'язками ними розроблені нормативні вимоги і засоби, що забезпечують безпеку експлуатації шахтних підйомні х установок в режимах гальмування. Разом з тим існуючі методи розрахунку і теоретичного дослідження динаміки гальмівних систем, необхідні для визначення їх раціональних параметрів, істотно відстають від вимог практики. До останнього часу недостатньо повно розроблені питання динаміки підйомної установки при робочому і запобіжному гальмуванні механічними гальмами як з пневматичними, так і з гідравлічними гальмівними приводами, а також методи розрахунків нагріву і зносу колодкових і дискових гальм. Таким чином, на підставі вище викладеного, питання – розробка дискового гальма для шахтної підйомної машини – є актуальним.
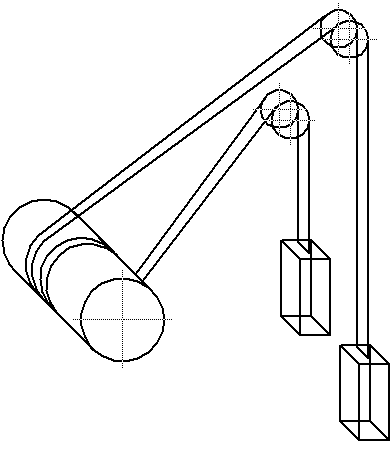
Малюнок 1 – Принцип работи подйомної машини
2. Мета і завдання дослідження, плановані результати
Мета – розробка раціональної схеми гальмівного пристрою шахтної підйомної машини Ц 3,5х2А і визначення його основних параметрів.
Зазначена мета може бути реалізована вирішенням наступних приватних завдань:>
- Аналіз існуючих систем гальм.
- Аналіз застосовуваних фрикційних матеріалів.
- Розробка ефективної схеми гальма шахтної підйомної машини.
- Вибір фрикційних матеріалів гальмівної накладки.
- Розрахунок гальмівного пристрою.
- Визначення питомої тиску на колодку тертя.
- Визначення температури в момент гальмування на поверхні накладки і диска.
- Розрахунок максимального зусилля притискання гальмівної накладки до диска.
- Визначення економічного ефекту від застосування дискового гальмівного пристрою.
3. Огляд досліджень і розробок
Для забезпечення нормальної експлуатації підйомно–транспортні машини забезпечуються надійно діючими гальмівними пристроями. Гальма повинні зупиняти машину і вантаж на певному шляху гальмування і утримувати вантаж в підвішеному стані при заданому запасі гальмування при заданому значенні уповільнення. Гальма будь–якого виконавчого механізму не тільки забезпечують безпеку роботи цього механізму і всієї машини в цілому, але і впливають па продуктивність. Значення гальмівних пристроїв зростає в зв'язку з інтенсифікацією виробництва, збільшенням рухомих мас, швидкостей руху і частоти гальмування. В сучасних підйомно–транспортних машинах гальма протягом короткого періоду часу повинні перетворювати в теплову енергію значна кількість механічної енергії і передавати її в навколишнє середовище без зниження працездатності гальма і машини в цілому.[1]
3.1 Класифікація гальмівних пристроїв
За конструктивним виконанням робочих елементів – на гальма:
- колодкові – з робочим елементом у вигляді колодки, що треться по зовнішньої або внутрішньої поверхні гальмівного барабана;
- стрічкові – з робочим елементом у вигляді стрічки тертьової з гальмівного барабану;
- дискові – з робочим елементом у вигляді цілих дисків або окремих сегментних колодок;
- конічні – з робочим елементом у вигляді конуса.Останні два конструктивні різновиди гальм зазвичай об'єднують в одну групу гальм із замикаючим зусиллям, діє уздовж осі – в групу гальм з осьовим натисканням.
За характером дії приводного зусилля – на гальма:
- нормально замкнутого типу, замикання яких створюється постійно діючої зовнішньої силою (вагою замикає вантажу зусиллям пружини і т.п.), а
- розмикання – тільки при впливі на нього приводу гальма;
- нормально–розімкнутого типу, розмикаються за допомогою постійно діючого зовнішнього зусилля, а замикаються тільки при впливі на нього приводу гальма;
- комбіновані, що працюють в нормальних умовах як гальма нормально розімкнуті, а в аварійних умовах – як гальма нормально замкнуті дією замикаючого зусилля.
За принципом дії – на гальма:
- автоматичні – нормально замкнутого типу, замикаються незалежно від волі обслуговуючого персоналу при відключенні двигуна механізму, на якому встановлено гальмо;
- керовані – замикання або розмикання яких проводиться обслуговуючим персоналом при впливі на орган управління гальмом, незалежно від приводу механізму.
За призначенням:
- на стопорні гальма, зупіняють Механізм, вступаючі в дію в кінці руху,
- на гальма, что обмежують швидкiсть руху в питань комерційної торгівлі межах течение Усього перiоду роботи. Відповідного виконавчого механізму (спускні гальма и регулятори швідкості).
До всіх гальмах, незалежно від їх конструкції, пред'являються наступні основні вимоги: висока надійність конструкції, достатній гальмівний момент для заданих умов роботи, плавність гальмування, швидке замикання і розмикання, конструктивна міцність елементів гальма, простота конструкції, визначає низьку ціну виготовлення, зручність огляду, регулювання і заміни зношених деталей, стійкість регулювання, забезпечує надійність роботи гальмівного пристрою, мінімальний знос тертковим елементів, температура оверхностей тертя, в процесі роботи не перевищує граничну, встановлену для даного типу гальма при цьому фрикційної матеріалі, мінімальні габарити і маса. При роботі у вибухонебезпечному середовищі повинні застосовуватися підйомно–транспортні машини спеціального вибухобезпечного або вибухо–захищеного виконання. [2]
3.2 Існуючі системи гальмування
Дискові гальма на багатоканатною підйомної машини використовуються ведучі частини дискових гальмівних пристроїв з випуском робочої рідини при робочому і запобіжному гальмуванні.
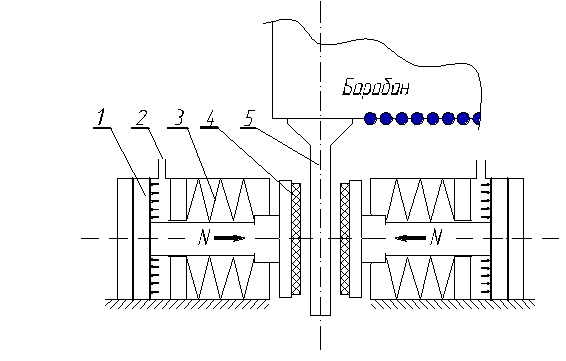
Малюнок 2 – Дискове гальмо
Гальмівні колодки
Розрізняють колодкові гальма з зовнішнім і внутрішнім розташуванням гальмівних колодок щодо металевого елемента фрикційної пари. У перших сила тертя при гальмуванні виникає в результаті контакту фрикційної накладки з зовнішньої утворює поверхнею шківа (бандажем ходового колеса), а в інших – з внутрішньої утворює поверхнею гальмівного барабана. Одноколодочние гальма не знаходять широкого застосування (за винятком гальм залізно дорожнього рухомого складу), так як створюють значні зусилля, згинають гальмівний вал. Кріплення гальмівних колодок до важелів – шарнірне або жорстке. При жорсткому кріпленні знос фрикційних накладок по лузі охоплення колодок менш рівномірний.
Виконавчим органом в гальмівних пристроях шахтних підйомних машин зазвичай застосовується гальмо Двоколодкове. Стрічкові гальма в шахтних підйомних машинах не допускаються ПБ через можливість розриву стрічки. Крім того, ці гальма надають згинаючи вплив на вал гальмівного шківа.
Виконавчий орган буває одинарним, чинним па один гальмівний обід, і спареним, чинним на два гальмівних обода. В останньому випадку кожен обід має свою пару гальмівних стійок або балок з колодками, пов'язаними загальної передачею важеля з приводом.
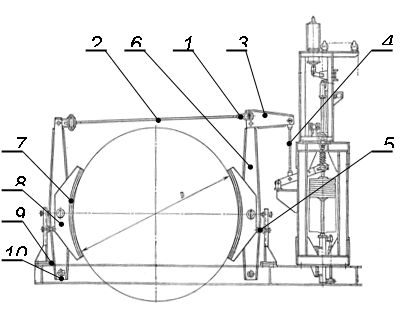
Малюнок 3 – Колодкове гальмо
Гальмівні пристрої з пружинно–гідравлічним приводом гальма мають два виконавчі органи, два пружинно–гідравлічні приводи, станцію управління та блокування. Виконавчі органи працюють синхронно і використовуються як при робочому, так і при запобіжному гальмуванні. Кожен виконавчий орган гальма типу колодки впливає на гальмівний обід барабана, створюючи половину величини необхідного гальмівного моменту.
Cтрічкові гальма
У стрічкових гальмах (мал. 4) гальмування здійснюється за рахунок тертя гнучкої сталевої стрічки про зовнішню поверхню циліндричного гальмового шківа або внутрішню поверхню циліндричного барабана. Підвищення коефіцієнта тертя досягається шляхом закріплення на робочій стороні стрічки накладки з фрикційного матеріалу. При однакових замикаючих зусиллях, коефіцієнті тертя і діаметрах шківів (барабанів) гальмівний момент стрічкового гальма значно більше, ніж колодкового. Стрічкові гальма застосовують в екскаваторах, дорожніх машинах, ковальсько–пресовому обладнанні, у вантажопідйомних машинах і механізмах. До стрічкових відносяться також гальма стрічково–колодкові і шарнірно–колодкові.
Кут охоплення стрічкою шківа зазвичай становить близько 270 °, проте окремі конструкції досягають 590 °.
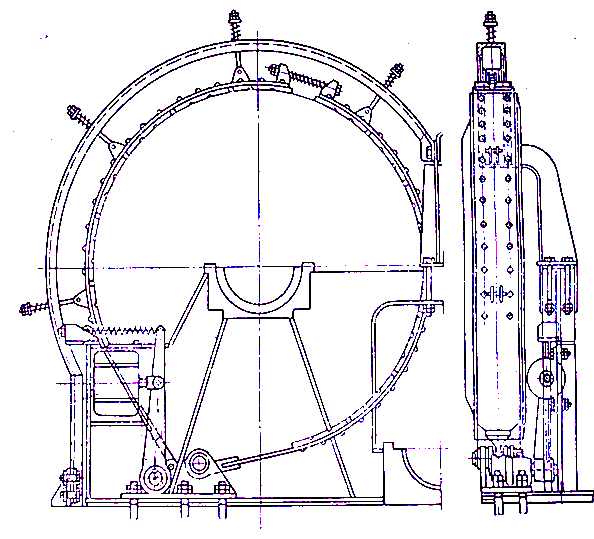
Рисунок 4 –Стрічкове гальмо
Гальма з зовнішньої стрічкою, в залежності від схеми її приєднання до важеля поділяють на прості, диференціальні, підсумовують, двосторонньої дії. У простому гальмі найбільш навантажений набігає (який натягується силою тертя при обертання шківа) кінець стрічок прикріплений до нерухомої частини робочого механізму, а збігається – до важеля. У диференціальному гальмі кінці стрічки приєднані до важеля з обох боків від осі його коливання, а в підсумованого – в одну сторону. У гальмі двостороннього дією набігаючого (нерухомо закріпленим) стає в залежності від напрямку обертання шківа той чи інший кінець стрічки. Прості і диференціальні гальма застосовують в механізмах, для яких не потрібно забезпечення однакового гальмівного моменту. [3]
3.3 Фрикційні пари гальмівних пристроїв
Показники якості гальмівних пристроїв визначаються в основному конструктивним виконанням вузла тертя і оптимальним поєднанням матеріалів фрикційної пери. Для забезпечення стабільності гальмівного моменту, підвищення надійності і зносостійкості елементів гальма застосовують спеціальні матеріали з підвищеними фрикційними властивостями (фрикційні накладки) в контакті з металевим контртіло. Фрикційні накладки виготовляють зі шкіри, пробки, модифікованої деревини, металів, асбополімерних композицій, порошкових матеріалів. Вони швидко зношуються елементи в порівнянні з металевими контртіло і тому повинні бути достатньо дешевими, а фрикційний вузол повинен мати таку конструкцію, при якій забезпечується швидка заміна зношених накладок.
Матеріали для фрикційних накладок
При виборі матеріалів пари тертя рекомендується враховувати вид контакту її елементів, значення коефіцієнта взаємного перекриття, вимоги до контактної жорсткості вузла тертя, вид охолодження, наявність або відсутність мастильного матеріалу.
Фрикційні матеріали повинні мати стабільний коефіцієнт тертя, задані механічні та теплофізичні властивості, добре пріробативаться до контртіло (при першому гальмуванні Мт> 0,8Мрасч), повинні бути технологічними, корозійностійким, мати достатню механічну міцність, масло, волого– та вогнестійкістю, високою зносостійкість низькою схильністю до схоплювання в гарячому і холодному стані. Верхня і нижня межі коефіцієнта тертя загавкають залежності від конструкції, призначення і умов експлуатації гальмівного пристрою. Нижня межа коефіцієнта тертя визначає умова забезпечення заданого гальмівного моменту, а верхній збереження стійкості русі транспортного засобу при максимально допустимих уповільненнях. Значення коефіцієнта тертя для гальмівних пристроїв підйомно–транспортних машин, рекомендованих складають 0,35–0,45.
Зносостійкість визначає термін служби фрикційних накладок, міжремонтні пробіги машин і час ремонтних простоїв. Оцінюють її виходячи з типу гальма, умов експлуатації і якості фрикційного матеріалу.
Теплофізичні властивості пари тертя гальма визначаються в основному теплоємністю і теплопровідністю матеріалів. Теплоємність сприяє зниженню температури пара тертя за рахунок поглинання теплоти, а теплопровідність – за рахунок перенесення теплоти від поверхні тертя в глиб матеріалу і далі до поверхні охолодження.
Механічні властивості є важливим показником матеріалів. Фрикційне пара гальма працює в умовах складного напруженого стану. Напруження стиску фрикційної накладки приблизно рівні нормальному тиску. Сила тертя при гальмуванні викликає в накладці розтягують напруги і напруги зрізу. Напруження зрізу орієнтовно рівні добутку коефіцієнта тертя на нормальний тиск. При терті фрикційних матеріалів в області підвищених температур їх твердість пропорційна площі фактичного контакту поверхонь, що труть, і визначається тиском на плямі фактичного торкання.
Модуль пружності фрикційного матеріалу при пружному контакті впливає на характер фрикційної взаємозв'язку і визначає фактичну площу контакту і тиск на плямах контакту. Фрикційний матеріал повинен мати мінімальні теплове розширення, усадку і високий модуль пружності, так як при жорсткому кріпленні накладки до металевого каркасу внаслідок теплового розширення і усадки фрикційного матеріалу можуть виникати значні температурні і усадочні напруги в накладці. Процес накладення фрикційної накладки на контртіло характеризується ударним додатком навантаження, тому фрикційний матеріал повинен володіти високою ударною в'язкістю.
При повторно–короткочасному режимі гальмування фрикційна накладка відчуває багаторазові циклічні навантаження і повинна мати достатній опір втоми при циклічних діях. Фрикційні й інші характеристики пари тертя визначаються умовами її роботи. За температурними показниками розрізняють досить легкий режим роботи (до 100 ° С), легкий (до 250 ° С), середній (до 600 ° С), важкий (до 1000 ° С) і надважкий (понад 1000 ° С). Області застосування пар тертя гальмівних пристроїв. [4]
4. Вибір і аналіз геометричної форми фрикційної колодки
У процесі розрахунку нагріву диска і фрикційних накладок дискового гальма прийняті наступні допущення: Тепловий потік, підводиться до гальмівного диску, розподіляється рівномірно по кільцевій площею тертя, а потік підводиться до фрикційних накладок, рівномірний по їх площі тертя; Тепловий потік, розвивається на поверхні тертя, лінійний і спрямований по нормалі до поверхні тертя.
Аварійність на шахтному підйомі становить близько 4%, а смертельний травматизм більше 3% від загального числа аварій і випадків смертельного травматизму на шахтах. Основні небезпеки на канатному підйомі і спуску людей і вантажів по вертикальних і похилих виробках наступні: падіння в вертикальних або вільне скочування в похилих виробках вантажних і людських підйомних посудин; удари і різкі зупинки людських підйомних посудин; падіння у виробки перевозяться в посудинах вантажів або інших предметів; падіння людей. Падіння (вільні скочування) підйомних посудин, призводить до травмування людей, що знаходяться в підйомному посудині або нижче судини, відбувається при обриві підйомних канатів або сцепок. Удари людських підйомних посудин в кріплення або армування при недотриманні встановлених зазорів, а також удари і різкі зупинки при перепод'йеме судини або напуску каната можуть привести до серйозного травмування людей, що знаходяться в підйомному посудині. Падаючі на вироблення вантажі і предмети небезпечні для працюючих в ній і перевезених людей. Очевидна також небезпека падіння людей у виробленні при посадці в підйомна посудина, висадці з нього або при його русі.
Число людей, яких можна одночасно перевозити в кожному поверсі кліті, визначається з умови вільного їх розміщення і не повинно перевищувати п'яти на 1 м2 корисної площі підлоги.
Для забезпечення строго спрямованого руху і виключення коливань або крутіння підйомні посудини забезпечені направляючими черевиками, що ковзають по провідникам. Останні є елементами армування стовбурів і можуть бути твердими або еластичними. Як тверді провідники застосовують рейки, металевий коробчатий профіль або дерев'яні бруси, як еластичних – канат.
Напрямні башмаки на підйомних посудинах можуть бути ковзаючим твердим або пружними – у вигляді пружних роликових опор. Гідність останніх полягає в тому, що вони знаходяться в постійному контакті з провідниками, тоді як у міру зносу контактних поверхонь твердих напрямних башмаків ковзання та провідників зазор між ними збільшується.
,/p.Однак пружні напрямні менш надійно утримують підйомні посудини від бічних зсувів. Тому Правила безпеки дозволяють застосовувати їх тільки в поєднанні з твердими черевиками, службовці в якості запобіжного заходу. Їх встановлюють безпосередньо на несучі конструкції підйомному посудині.Зазори між контактними поверхнями напрямних башмаків і провідників строго регламентуються Правилами безпеки в залежності від типу і матеріалу провідників і напрямних. Так, мінімальний зазор між напрямними башмаками ковзання і контактних поверхонь металевих провідників складає 5 мм з кожного боку, а максимальний – 10 мм. Для дерев'яних провідників він дорівнює відповідно 10 і 15 мм.
Сталеві канати, що застосовуються на шахтних підйомних установках, повинні відповідати вимогам діючих ГОСТ або технічних умов. У пристроях, що служать для транспортування людей, повинні застосовуватися тільки канати марки В, тобто канати високої якості. Якість каната визначається механічними властивостями проводів і вказується в заводському акті–сертифікаті. Головні канати людських і вантажно–людських підйомних установок повинні бути марки В, інші канати – не нижче марки І. Використання канатів марки ІІ на шахтах не допускається.
Всі підйомні канати перед навішуванням повинні бути випробувані за єдиною методикою на канатно–випробувальних станціях, зареєстрованих в МакНДІ. Випробуванню підлягають відрізки каната довжиною не менше 1,5 м.
Придатність канатів для використання в підйомних установках визначається величиною запасу їх міцності. Запас міцності це відношення сумарного розривного зусилля дротів каната, що витримали іспит, до розрахунку статичного навантаження на нього. Розрахункова статичне навантаження складається з ваги підйомної посудини з причіпним пристроєм, ваги максимального; вантажу і головного каната довжиною від точки сходу його зі шківа до точки прикріплення до посудини при знаходженні останнього в приймальному майданчику нижнього горизонту. Якщо канат врівноважує важче головного, то до ваги судини і вантажу додають вага не головного, а каната, врівноважує. При навішування канати повинні мати запас міцності не нижче 9–кратного для людських підйомних установок, 7,5 кратного – для грузолюдськіх і 6,5–кратного – для вантажних.[5]
Висновки
У шахтної підйомної машини гальмівний пристрій є одним з найважливіших і відповідальних вузлів. У даній дипломній роботі виконано аналіз існуючих гальмівних систем з колодковими, стрічковими і конусними гальмами, розроблена схема дискового гальмівного пристрою і розглянуті основні елементи його виконавчого органу (привід).
Недоліками радіальних гальм є:
- Низька швидкодія;
- Низький ККД за рахунок багатошарнірний системи;
- Нестабільна характеристика;
- Великий кут охоплення, велика поверхня охолодження і можливість перегріву і аварії;
- Низька ремонтопридатність;
- Складність конструкції (радіальний зазор регулюється пружинними тягами)
- Низька надійність в порівнянні з дисковими гальмами.
Переваги дискових гальм:
- Взаємне урівноваження сил притиснення гальмівних колодок до диска, в результаті чого барабан і лобовини не навантажувати радіальними зусиллями;
- Велика компактність і менша вага при рівних гальмівних моментах;
- Менше інерційність і значно більшу швидкодію рухомих деталей;
- Велика точність управління машиною;
- Менше теплова деформація плоскій поверхні гальмівної колодки і більш сприятливі умови охолодження гальмівного поля (шляхом конвекції і випромінювання)
- Відсутність впливу теплового розширення диска на ефект гальмування;
- Простота виготовлення плоского диска і ремонту робочої поверхні з метою відновлення необхідної її чистоти;
- Невелика інерція гальма, внаслідок чого знижуються динамічні навантаження на основні вузли підйомної установки і збільшується точність управління підйомною машиною.
На багатоелементними дисковому гальмовому пристрої виконавчий орган безпосередньо пов'язаний з приводом, виключаючи при цьому проміжні пристрої (важелі, тяги та ін.).В результаті проведеної роботи запропонована схема і розраховані основні параметри дискового гальмівного пристрою до шахтної підйомної машини Ц–3,5х2А
Для творення необхідного гальмівного моменту 1050 кНм, певну кількість гальмівних елементів – 16 штук. Розрахований діаметр циліндра 129 мм і штока – 40 мм, для забезпечення зусилля притиснення гальмівної колодки 100 кН. Визначено максимальний тиск на гальмівну колодку, при великому притисканні її до диску 1,55 МПа, який знаходиться в допустимої межі для обраного фрикційного матеріалу.
Розрахована температура гальмування на поверхні тертя, при п'яти секундному гальмуванні, яка становить для колодки 134,5 ° С, для диска – 109,7 ° С, не перевищує номінальний струм для обраного фрикційного матеріалу – при цьому термін служби гальмівного пристрою збільшується з 18 міс . для колодкового гальмівного пристрою до 23,4 міс. при дисковому гальмовому пристрої, тобто майже на 30%. Річний економічний ефект від збільшення терміну служби дискового гальмівного пристрою по амортизаційних відрахуваннях становить 21540 грн. на один пристрій.
Значні переваги дискових гальмівних пристроїв щодо гальмівних пристроїв радіального типу, а також широке застосування на зарубіжних підйомних машинах різних фірм дозволяють припускати що дискові гальмівні пристрої отримають широке застосування і на вітчизняних, особливо на великих шахтних підйомних машинах.
Список джерел
- Песвианидзе А. В. Расчет шахтных подъемных установок: Учеб. Пособие для вузов. – М.: Недра,2005. – 250 с: ил. ISBN 5–247–01840–0.
- Конспект Лекций по дисциплине «Горная механика» Шахтные подъемные установки, механическая часть подъемных установок 2008г.
- С. С. Сиротин. Шахтные подъемные установки. Учебное пособие для студентов горных специальностей. Алчевск: ДГМИ,2007 – 174 с.
- Юдис, Борис Яковлевич. Совершенствование системы предохранительного торможения подъемной установки Алчевск: ДГМИ,2009. – 140 с.
- А.Д. Мехтиев, Проблемы эксплуатации и анализ состояния подъемных установок. Карагандинского государственного технического университета(КарГТУ).
- ГОСТ 2.104–2006. ЕСКД. Основные надписи. – М.: Стандартинформ, 2006. – 18 с.
- ГОСТ 2.105–95*. ЕСКД. Общие требования к текстовым документам. – М.: Стандартинформ, 2006. – 30 с.
- УГОСТ 2.301–68*. ЕСКД. Форматы. [Электронный ресурс] / Электронная библиотека CD «Строительство» v 2.01. (221 файл, 112 Mb) – Пермь: Служба НТИ, 2003.
- ГОСТ 2.321–84. ЕСКД. Обозначения буквенные. – М.: ИПК Изд–во стандартов. 2001. – 4 с.
- . ГОСТ 7.1–2003. Библиографическое описание. Общие требования и правила составления. – М.: Изд–во стандартов. 2004. – 170 с.
- ГОСТ 7.82–2001. Библиографическая запись. Библиографическое описание электронных ресурсов. – М.: Изд–во стандартов. 2002. – 54 с.
- Единая система конструкторской документации. Основные положения. – М.: Изд–во стандартов, 1983. – 351 с.