Content
- Introduction
- 1. Theme urgency
- 2. Goal and tasks of the research
- 3. Review of research and development
- 3.1 Analysis of a mine accumulator electric locomotive as an object of automation
- 3.2 The simplified power scheme of management of a two-engine accumulator electric locomotive
- 3.3 Algorithm of automatic control of a mine accumulator electric locomotive
- Conclusion
- References
Introduction
In our country in the underground way extract about 30% of metal ores and mining and chemical raw materials, however at underground works it is engaged the bigger number of workers, than at open works is considerable. This results from the fact that at an underground way develop less powerful, than at an open way, or deep-laying fields. At an open way of development the land surface is broken, significant areas are occupied by dumps of dead rock. For the purpose of environmental protection it is necessary to spend large sums for land reclamation. The main direction of further development of the domestic mining industry is increase in labor productivity due to modernization of the enterprises on the basis of the new high-performance equipment and implementation of advanced technology of mining operations. Development of technology for extraction of ores is based on application of complexes of the machines and the equipment providing mechanization and automation of all productions.
One of the most important links in complex mechanization of underground extraction of ores is process of movement of ore from a face to a surface, including operations of release, loading and its delivery within a clearing face and transport on the main developments to a mine trunk. About 50% of all cost of production are the share of delivery and transportation of ore. In this regard the control system of a mine accumulator electric locomotive with the direct current motor in the motive and brake modes with a possibility of recovery of energy is developed and investigated.
Such main requirements as high level of quality are imposed to modern cars of miner transport, on reliability, reliability and durability, the aggregation, standardization and unification of assembly units providing assembly of transport vehicles of universal purpose, respect for sanitary standards on the noise level, vibration and dust content, automation on the basis of the microprocessor equipment and remote control of transport vehicles.At the enterprises of ore mining industry depending on appointment and mining-and-geological conditions use different types of transport vehicles. At underground mining as main types of miner transport apply delivery with use of rail transport, and in certain cases transport vehicles, underground dump trucks self-propelled pogruzochno. The main direction on underground mining operations on fossil is use of the high-performance equipment with the electric drive for transportation of fossil, auxiliary freights and people.
1. Theme urgency
The main direction of development of an electric haulage — implementation of line technology of transport of ore trolleys with the interbody overlapping and ground unloading providing continuous process of loading and unloading of structure. It allows to increase productivity of an electric haulage by 1.5 — 2 times and by 5 — 6 times to increase the capacity of loading points. The majority of the miner electric locomotives applied in mines have the traction electric drive with a contact control system. Such system allows to carry out step start-up and regulation of speed with application of a rheostat and also parallel and consecutive connection of traction engines. Rheostatic electrodynamic braking is applied. Such control systems of the traction electric drive are insufficiently reliable, their work is followed by considerable throws of starting and brake current and efforts. At the same time often there is a wheel slip of an electric locomotive concerning rails. Use of a rheostatic control system of the electric drive causes the increased losses of electric energy.
2. Goal and tasks of the research
The majority of the miner electric locomotives applied in mines have the traction electric drive with a contact control system. Such system allows to carry out step start–up and regulation of speed with application of a puskoreguliruyushchy rheostat and also parallel and consecutive connection of traction engines. Rheostatic electrodynamic braking is applied. Such control systems of the traction electric drive are insufficiently reliable, their work is followed by considerable throws of starting and brake current and efforts. At the same time often there is a wheel slip of an electric locomotive concerning rails. Use of a rheostatic control system of the electric drive causes the increased losses of electric energy. Development of the semiconductor equipment allows to replace the RKSU above-named systems with electroenergy efficient structures with transistor and pulse control systems (TRSU) of regulation of tension.
Application of such systems on mine electric locomotive transport will allow:
– to reduce by 35–50% consumption of electric energy an electric locomotive;
– to minimize losses of energy in all elements of a system;
– to smoothly regulate tension brought to the engine that will allow to regulate as much as possible forces of draft and braking under the terms of coupling;
– to achieve flexibility and simplicity of management with a possibility of automatic and remote control and also management on the system of many units;
– to automatically limit dangerous operating modes of all complex of the electric equipment of an electric locomotive;
– to apply the system of monitoring of a condition of the equipment;
– to carry out effective protection against slipping of an electric locomotive;
– to increase safety of work and service;
– to achieve the minimum dimensions, weight and cost.
In the mines not dangerous on gas and dust, it is expedient to use only accumulator electric locomotives which it is simpler on a design, it is cheaper and more convenient in operation, have the big capacity and speed of the movement, smaller power consumption.The exclusive place in this complex is taken by the direct current motor with consecutive excitement.
Advantages of direct current motors of consecutive excitement: the soft mechanical characteristic simplifying work and control of multi-engine systems with individual distribution of loads of the leading axes, a high limit on reloading ability.
Shortcomings are: low energy efficiency, in view of frequent use of relay and rheostatic management, and power loss on active elements, complexity of a design of the drive, complex maintenance in use, maintenance of speed at the different levels of the movement of the rolling stock. All these shortcomings are also a step for further modernization of an object.
The purpose of the master thesis is development and a research of a control system of a mine accumulator electric locomotive with the direct current motor in the motive and brake modes with a possibility of recovery of energy.
3. Review of research and development
3.1 Analysis of a mine accumulator electric locomotive as an object of automation
The mine electric locomotive is one of fixed assets of delivery of coal, materials and people in horizontal underground developments of coal mines dangerous on gas or dust, at the same time the most part from all quantity of electric locomotives, make accumulator electric locomotives. On electric locomotives the systems of the drive consisting of two traction electric motors of consecutive excitement and a rheostatic control system are widely used. This system of the drive possesses a number of the known merits and demerits. It is necessary to refer simplicity of the scheme and a design of the control unit to advantages of rheostatic control systems, and use of engines of consecutive excitement most corresponds to characteristics of an electric locomotive regarding ensuring lack of stalling. Shortcomings of rheostatic control systems are connected with the low sizes of efficiency caused by an expense of a limited stock of energy of the rechargeable battery on heating of rheostats of the scheme of management, and with consecutive excitement of engines of consecutive excitement it is necessary to refer impossibility of ensuring recovery of energy in the brake modes to shortcomings of schemes. For an exception of the specified shortcomings of schemes of management various without rheostatic systems began to appear. In without rheostatic schemes of management regulation of speed of the movement is carried out, as a rule, by change of tension or due to switching of sections of batteries or due to application of pulse schemes of management. Application of schemes of management with sectioning of batteries differs in considerable complexity and limited number of steps, at the same time the possibility of recuperative ways of braking is rather easily provided.
3.2 The simplified power scheme of management of a two-engine accumulator electric locomotive
Pulse schemes of management allow to provide smooth speed control by means of rather simple schemes of management, however for implementation of recuperative operating modes the power scheme significantly becomes complicated.
The simplified power scheme of management of a two-engine accumulator electric locomotive combining advantages of pulse schemes of management and schemes with sectioning of the feeding batteries is provided on figure 1. In the scheme, for implementation of a possibility of recovery in the brake modes engines are switched on according to the scheme of independent excitement.
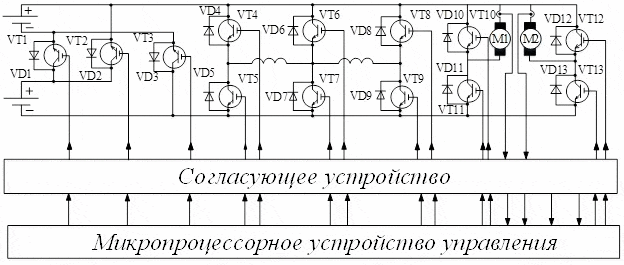
Pic. 1 – The simplified power scheme of management of a two-engine accumulator electric locomotive
(animation: 3 frames, delay between frames 0.5s, 71kb)
On the scheme power keys of VT1 – VT3 provide switching of two sections of batteries from consecutive in a parallel operating mode, at the same time the included condition of VT1 corresponds to consecutive turning on of batteries, and the included condition of keys of VT2 and VT3 corresponds to parallel inclusion of sections of batteries. Switching of a power supply system in a parallel operating mode does possible operation of the drive in the energy recovery modes. Power keys of VT4-VT9 are intended for management of excitement windings of M1 and M2 engines. At the same time the reverse of engines is carried out by change of the direction of current in excitement windings. Power keys of VT11 and VT13 are intended for management of current of an anchor of traction engines, and keys of VT10 and VT12 are intended for implementation of dynamic braking at reduction of speed when recuperative braking is not possible. All power keys are run through the coordinating device by the microprocessor control unit. The smoothness of management is reached due to application of the modes of pulse-width management of power keys, at the same time the device management controls currents in windings of the drive and the speed of the movement.
The overall performance of the provided scheme a mine accumulator electric locomotive is defined by an operation algorithm of the microprocessor control unit which analysis it is convenient to make on the basis of mathematical model of the drive. For an example the mathematical model of a traction electric locomotive of AM8D with DRT-13 engines was considered. Modeling was carried out for one engine. Mechanical characteristic of the engine in the mode of independent excitement is described by expression:
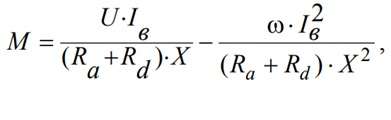
where: M - the electromagnetic moment developed by the engine, U – the supply voltage of a winding of an anchor, Iv – current of a winding of excitement, Ra and Rd – active resistance of a winding of an anchor and additional pole, the speed of rotation of an anchor, X – a constructive constant, for the DRT-13 engine - X=60.264. The equation of the movement can be described as:
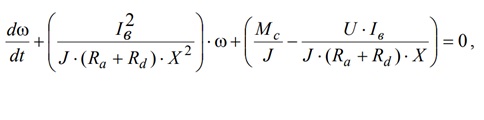
where: J – the given moment of inertia, Ms – the given resistance moment. Taking into account it the dependence of change of speed of rotation of the engine on time at invariable values of loading and parameters of management is received:
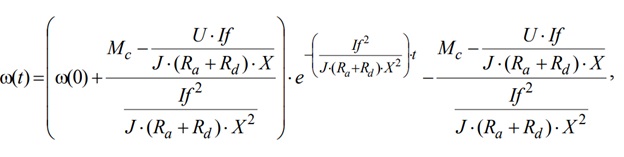
where: ω (0) – the speed of rotation of an anchor at the beginning of the modelled site, t – time from the beginning of the modelled site.
For the power scheme of management described above two control algorithms realized by the microprocessor control unit were considered. Purpose of management: to carry out dispersal of an electric locomotive with structure to the specified speed of electric motors 100 rad/seс, and after 10 seconds from the moment of start implementation decrease in the specified speed to size of 10 rad/sec.
3.3 Algorithm of automatic control of a mine accumulator electric locomotive
The first algorithm provides giving of tame teams for change of supply voltage of a winding of an anchor each 2 seconds for step change of speed without restrictions on current and acceleration. The second algorithm realizes the proportional law of management with restriction of limit current of an anchor. In an algorithm it is realized with sampling, and the step of sampling made 10 ms that is convenient for realization by means of the modern inexpensive microcontroller. Work of the drive of an electric locomotive was carried out at a constant of current of excitement 50A. Regulation of tension and currents in the scheme is carried out by PWM of management of the corresponding transistors. The dependence of change of tension on time for both algorithms is given in figure 2. Manual (step) regulation – dependence 1, automatic with the proportional regulator – dependence 2.
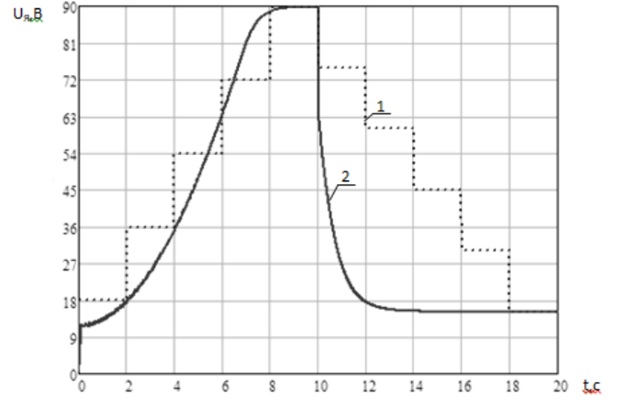
Pic. 2 – Change of supply voltage of a winding
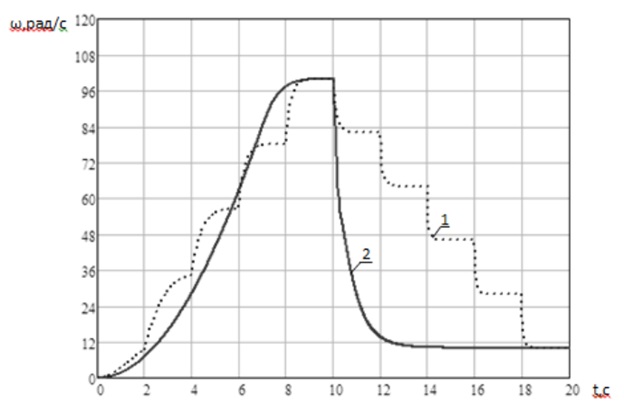
Pic. 3 – Change of speed of rotation of a shaft of the engine
The dependences of change of speed on time received as a result of model of modeling are given in picture 3.
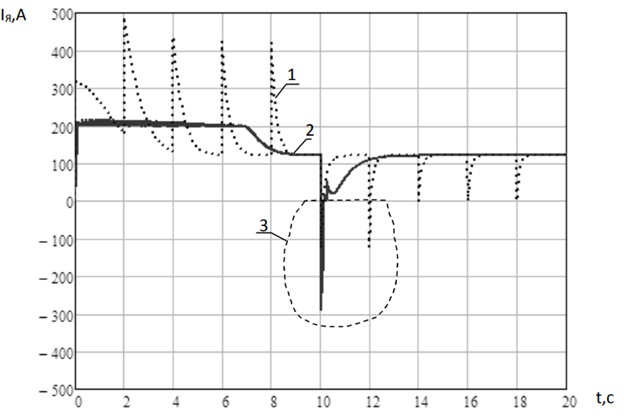
Pic. 4 – Change of current of an anchor at dispersal and braking
The area of negative currents (3) corresponds to recuperative braking. For its providing switching with consecutive to the parallel scheme of turning on of batteries was carried out, at the same time tension decreased twice.
Conclusion
The carried-out calculations showed operability of the accepted control system. At the same time it is enough to apply the simple proportional law of management with restriction of size of current of an anchor to implementation of management. At the same time the efficiency of recovery of energy at undervoltage twice due to switching of two sections insufficient, and leads division into 4 and more sections with appropriate level of undervoltage to complication of the power scheme of management.
References
- Беловидов, Б.С. Анализ различных типов приводов для рудничных автоматизированных электровозов / Б. С. Беловидов [и др.]. // Исследование работы автоматизация горных машин: тр. Новочеркасского политехнического института. – Новочеркасск: 1964. – Т. 159. – С. 31–38.
- Довженко В.П. Транзисторные модули для управления приводо рудничных электровозов / В. П. Довженко [и др.]. //Уголь Украины. – 2003. – № 10.–16– 18.
- Евстафенко П.Ф. Перспективы развития электрооборудования для удничного электровозного транспорта / П.Ф. Евстафенко [и др.]. //Уголь Украи-ны. –2003. –№ 10. – С. 22–23.
- Синчук О. Н, Удовенко О. А., Чумак В. В. Особенности переходных электромагнитных процессов в тяговом электроприводе с импульсным преобразователем напряжения рудничных аккумуляторных электровозов. // Электротехника, 2004, №6. – С.58-60.
- Системы управления рудничным электровозным транспортом. /О. Н. Синчук, Т. М. Беридзе, Э. С. Гузов и др. - М.: Недра, 1993.- 255 с.
- Пискунов С. В., Ворошилов В. С, Поляков В. А. Тяговые асинхронные двигатели для приводов подвижного состава городского электротранспорта. // Электротехника, 2005. - № 5. - С. 32 - 34.
- Конашинский А. Ю. Влияние электрических видов коррекции
электромеханических характеристик асинхронных тяговых двигателей
на их энергетические показатели. // Электровозостроение: Сб. науч. тр.
ОАО
Всерос. науч.-исслед. и проектно-конструкт. ин-т электровозостроения
(ОАОВЭлНИИ
). - Новочеркасск, 2000. - Т. 42. С. 228-241. - Мальцева О.П., Удут Л.С., Кояин Н.В. Системы управления асинхронных частотно-регулируемых электроприводов. – Томск: Изд. ТПУ, 2011. – 476с.
- Кладиев С. Н., Вильнин А. Д., Пякилля Б. И. Модель электромеханической системы подвижного состава рудничного электровоза // Современные технологии. Системный анализ. Моделирование. – 2013 – №. 1(37). – C. 65-68 [2814-2013]
- Вильнин А.Д., Кладиев С.Н. Структура тягового электропривода рудничного электровоза// Современные проблемы и пути их решения в науке, транспорте, производстве и образовании: сб. науч. тр. – Одесса, 2011. – Том 2. – С. 80-85.