Abstract
Contents
- Introduction
- 1. Properties of titanium
- 2. Advantages and applications of titanium in mechanical engineering
- 3. Titanium alloys with other metals and alloying elements
- 4. Titanium oxides
- References
Introduction
Titanium and its alloys are an important structural material, which is widely used in many branches of technology. The main part of the waste titanium formed in the process of machining semi-finished products into products are metal with oxidized surface. The most common type of oxidized titanium waste is chips. Therefore, the rational use of oxidized titanium chips as metal raw materials, the maximum oxygen content of which exceeds 2%, and 80% of which is concentrated on the metal surface in the form of an oxide film, is one of the most important problems of titanium metallurgy.
1. Properties of titanium
High corrosion resistance in many aggressive natural and industrial environments is one of the distinctive properties of titanium and its alloys. The resistance of titanium alloys in a number of media is determined by the inertia of the surface oxide film and the speed of its formation or recovery, especially in oxidizing media and in the presence of water. Film character of corrosion resistance of titanium is obvious, but the characteristics and nature of passivation from changes in the external environment and internal structural state is studied is far from complete, although the level of corrosion resistance is strongly dependent on these factors. Therefore, it is often possible with the help of small inhibitory additives to reduce or prevent dangerous under normal conditions exposure to titanium aggressive environment. At the same time, in some cases there is an unexpected increase in corrosion without clear enough reasons.
Pure Titanium is a chemically active transition element, in compounds it has oxidation States +4, rarely +3 and +2. At normal temperature and up to 500-550 °C corrosion resistant, due to the presence on the surface of a thin but durable oxide film. With oxygen in the air interacts significantly at temperatures above 600 °C With the formation of Tio2. Fine titanium chips at the lack of grease may ignite during mechanical treatment. With a sufficient concentration of oxygen in the environment and damage to the oxide film by impact or friction, it is possible to ignite the metal at room temperature and in relatively large pieces. The oxide film does not protect Titanium in the liquid state from further interaction with oxygen (unlike, for example, aluminum), and therefore its melting and welding must be carried out in a vacuum, in a neutral gas atmosphere or under flux. Titanium has the ability to absorb atmospheric gases and hydrogen, forming brittle alloys, unsuitable for practical use; in the presence of an activated surface, hydrogen absorption occurs already at room temperature at a low speed, which increases significantly at 400 °C and above. The solubility of hydrogen in titanium is reversible and this gas can be removed almost completely by annealing in vacuum. With nitrogen, Titanium reacts at a temperature above 700 °C, and nitrides of the TiN type are obtained; in the form of a thin powder or wire, Titanium can burn in a nitrogen atmosphere. The diffusion rate of nitrogen and oxygen in titanium is much lower than that of hydrogen. The layer resulting from the interaction with these gases is characterized by increased hardness and brittleness and must be removed from the surface of titanium products by etching or machining. Titan vigorously interacts with dry Halogens, in relation to wet Halogens resistant, as moisture plays the role of an inhibitor. The metal is stable in nitric acid of all concentrations (except for red Smoking, causing corrosion cracking of Titanium, and the reaction sometimes goes with an explosion), in weak solutions of sulfuric acid (up to 5% by weight). Salt, hydrofluoric, concentrated sulfuric and hot organic acids: oxalic, formic and trichloroacetic react with Titanium.
2. Advantages and applications of titanium in mechanical engineering
The great demand for titanium and its alloys, due to the extremely high physical and mechanical properties of this metal, in fact, for the first time experienced the aviation industry. When in the late 40's-early 50-ies were created by jet aircraft with a sound and supersonic speeds, there is a need for new construction material for housings, casings, motors. It could be obtained only on the basis of titanium, known in those years for its unique characteristics. And today, aviation and space technology mainly determines the need for titanium and dictates the pace of development of the production of this metal. Until the end of the 60-ies of titanium in aircraft is mainly for the manufacture of gas turbines. In the 70-80-ies. titanium alloys are widely used for making various parts of glider aircraft parts: spars, beams, frames, chassis parts, etc. In comparison with parts made of steel win almost 40% of the mass. Became very widely used high-temperature titanium sheet for covering the hulls of supersonic aircraft. For example, in the American supersonic fighter F-14 used more than 3 tons (or 30% of the mass of the airframe) of titanium, in the liner "Boeing-2707", taking on Board 300 passengers and flying at double sonic speed - 47 tons of titanium (90% of the mass), in the fighter-interceptor F-12A - 3,3 t (95% of the mass).
The Wide and rapid spread of titanium alloys as structural materials for various purposes is explained by the advantages that titanium and its alloys have in comparison with other materials. Titanium is 18 times more expensive than stainless steel. However, since the weight of titanium required for the manufacture of a particular product (the name of the product is not given) is less than the weight of steel, titanium used for the manufacture of parts will cost more than steel, not 18, but 10 times. Further, since the difference in the cost of finished products made of titanium and the starting material (titanium) is lower than for steel, the finished titanium products will cost more than steel products, only three times. Finally, if we consider that in some cases the service life of titanium products is many times higher than the service life of steel parts, the use of titanium in these cases is more profitable than the use of steel.
Titanium and its alloys have great prospects in mechanical engineering. However, today the use of this metal in machine-building sectors of the national economy is still limited. This is explained, firstly, by the scarcity and rather high cost of titanium; secondly, the lack of information about the properties of titanium and its alloys when used in mechanical engineering; thirdly, the technological difficulties of titanium processing (anti-friction properties, hard weldability, etc.). And yet, despite the complexity of the introduction of a new material, titanium and its alloys in the last decade began to be used in the manufacture of many types of equipment in chemical engineering. At the plants of this industry, titanium alloys are serially produced for shut-off and pumping equipment, a variety of containers, pipes, columns, filters, autoclaves, special column equipment designed to work with highly corrosive liquids and vapor-gas mixtures. This is a different tower from a sheet of titanium special design of adsorbers: bubbling, distillation, spray etc. Titanium and its alloys are widely used in the manufacture of heat exchange equipment used in the industry for heating, boiling, evaporation, condensation and cooling of various aggressive media: liquid, gas, steam, paste and even solid. Produce heat exchangers with a variety of heat exchange area - from 2 to 160 m2, refrigerators-from 30 to 140 m2, capacitors, boilers, heaters-from 30 to 150 m3. For all types of these devices, titanium and its alloys make it possible to increase corrosion resistance and heat transfer efficiency at a minimum wall thickness. Another advantage of using titanium alloys in heat exchangers is that they are less susceptible to wetting and precipitation on their surface. This, in turn, provides a high heat transfer coefficient during the operation of the device. Very effective use of titanium alloys in the filter apparatus. Filtration-separation of suspended solids from the liquid phase - a process very common in many chemical and technological industries. Its intensification affects the productivity of the entire technological chain as a whole. Thus, the use in automatic filter presses of parts in contact with the aggressive medium of titanium alloys increases the performance of the filter surface unit by 4-15 times. In this case, titanium filter presses can be used to filter suspensions with a temperature up to 300-350° C and with a content of suspended particles from 5 to 600 g/m3. Titanium alloys are also used to produce disc and belt vacuum filters, cartridge and ceramic filters for clarification and thickening filtration.
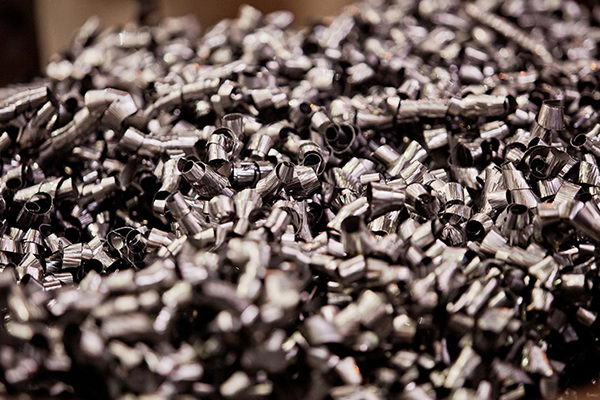
figure 1-titanium Chip
3. Titanium alloys with other metals and alloying elements
Titanium Alloys with aluminium They are most important in technical and industrial terms. The introduction of aluminum into technical titanium, even in small quantities (up to 13%), can dramatically increase the heat resistance of the alloy while reducing its density and cost. This alloy is an excellent structural material. The addition of 3-8% aluminum increases the conversion temperature of & alpha;-titanium in & beta; - titanium. Aluminum is practically the only alloying stabilizer α-titanium, increasing its strength at the constancy of the properties of plasticity and viscosity of the titanium alloy and increasing its heat resistance, creep resistance and modulus of elasticity. This eliminates a significant drawback of titanium. In addition to improving the mechanical properties of alloys at different temperatures, increases their corrosion resistance and explosion hazard when working parts of titanium alloys in nitric acid. Aluminum-titanium alloys are produced in several grades and contain 3-8% aluminum, 0.4-0.9% chromium, 0.25-0.6% iron, 0.25-0.6% silicon, 0.01% boron. All of them are corrosion-resistant, high-strength and heat-resistant titanium-based alloys. With an increase in the aluminum content in the alloys, the melting point is slightly reduced, but the mechanical properties are significantly improved and the softening temperature increases. These alloys retain high strength up to 600° C.
4. Titanium oxides
Titanium forms a number of oxides. Of these, the most studied are TiO2, Ti2O3 and TiO. In addition, there are oxides of intermediate composition, for example Ti3O5 and a number of others. They represent the titanates (or titanite) titanium, i.e., contain the titanium atoms of different valences. Higher oxides are amphoteric, lower valence oxides have a basic character. Titanium dioxide TiO2 is the main product of titanium raw materials processing. It is a white powder. In nature, it occurs in the form of three minerals — rutile, anatase and brookite, which are modifications of titanium dioxide. Only rutile and anatase are artificially obtained, and α- and β-modifications are known for the latter. Brookite, crystallizing in the rhombic system, when heated above 650° irreversibly turns into rutile. This is accompanied by a decrease of about 2%. Anatase (α-modification) is obtained by heating at a temperature no higher than 400° titanium hydroxide. At 642° α - anatase reversibly goes to β - modification. The latter at 915° irreversibly turns into rutile. Thus, rutile is the most stable modification of titanium dioxide. Titanium dioxide is practically insoluble in water and dilute acids. It dissolves in concentrated sulfuric, hydrochloric and nitric acids when heated and in hydrofluoric acid.
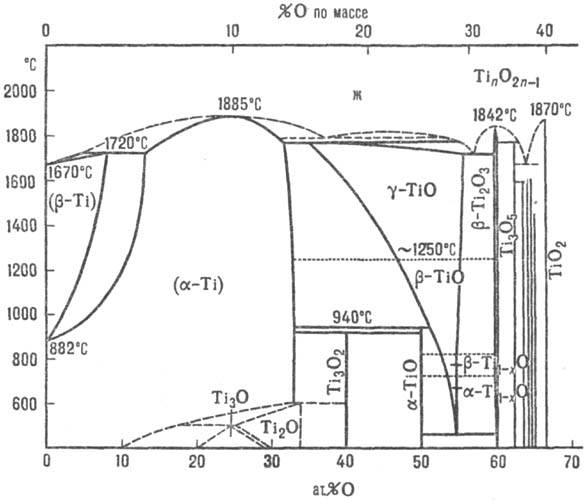
figure 2-property of titanium oxides
Titanium Oxide Ti2O 3 — dark-violet powder is obtained by reducing Ti 2 with hydrogen at a temperature of 1200-1400°. 3 titanium oxide TiO is a substance of Golden yellow color with metallic luster. Nitrous oxide is obtained by annealing in vacuum at a temperature of 1550° a mixture of titanium metal powder with titanium dioxide, as well as by reducing TiO2 magnesium, aluminum or carbon. A study of the titanium-oxygen system showed that the crystal lattice of the cubic type characteristic of titanium oxide is preserved in the region of compositions from TiO0.69 to TiO1.33.
Waste after machining titanium is about 45% of the total waste. The quality of waste is determined by the degree of contamination with harmful impurities, primarily oxygen. Thus, waste can be divided into two types: conditioned and substandard. Conditioned waste in the form of pure non-oxidized chips is used for charging in the smelting of ingots of titanium alloys and powder production. Substandard waste in the form of oxidized chips with an oxygen content of more than 2% (as titanium chips found in briquettes, packages) is involved in the turnover of metallurgical titanium with the help of multi-stage and expensive technologies or even removed from it. To a group of technologies designed to restore titanium are: - processing into titanium slag: the charge consisting of an ilmenite concentrate and a carbon reducing agent in a ratio of 1:(0.09-0.15), respectively, is ground to a particle size of 40-73 microns, mixed with a binder with the addition of water in an amount of 6-7.3% by weight,pellets are made and dried at a temperature of 200-400°C. the Metallization of pellets is produced in a tubular furnace at a temperature of 1100-1300°C. Hot pellets are melted in an electric furnace at a temperature of 200-400°C. 1830-1870 ° C and withstand the melt in the electric furnace before casting for 3-5% of the total duration of melting. As ilmenite concentrate, iron-titanium concentrates with low impurity content containing 50-55% Tio2, 32-36% FeO, 10-15% Fe2O3, up to 0.5% Al2O3, up to 0.8% SiO2, up to 0.1% are used CR2O3, up to 0.6% MPO, up to 0.05% P2O5, up to 0.3% V2O5, up to 0.1% Cao and up to 0.7% Mao. Used in the reduction processes carbon reducing agent-metallurgical coke, pitch coke, petroleum coke, coal contains active carbon of at least 80% and sulfur of not more than 1%;
Etching, several methods of surface treatment of oxide films are known in the production of titanium semi-finished products: mechanical removal, electrochemical treatment, etching in alkaline melts, chemical etching in aqueous solutions of acids. Rutile is the most chemically inert polymorphic modification of titanium dioxide, so the removal of the oxide film from the surface of titanium by etching is possible only in very aggressive environments. It is quite simple and economical with the appropriate selection of reagents hydro metallurgical treatment of oxidized titanium chips, with the torus oxide film is removed mainly due to the penetration of the etching solution through the heterogeneity and imperfection of the oxide structure. The destruction of the films occurs by peeling when the metal substrate is etched. Since titanium in hydrochloric acid at 25 ° C retains stability only up to the acid concentration of 5%, and with an increase in its concentration to 10%, titanium begins to corrode, therefore, 10% HCl solution with NaP additive was chosen as the basis for the Etchant for hydrometallurgical deoxidation of oxidized titanium chips. Study of hydrometallurgical deoxidation of oxidized titanium chips in hydrochloric acid solutions and process optimization The chemistry of etching titanium hydrochloric acid solutions containing sodium Fluoride. To clarify the circumstances related to the possibility of the formation of a protective layer of titanium fluoride compounds, the change in the composition of the etching solution was considered as the process of etching the oxidized chips of a complex-alloyed titanium alloy VT23
References
- Плавка и литье титановых сплавов. Андреев А.Л., Аношкин Н.Ф. и др. М., Металлургия, 1994, стр.128-135.
- Титан. В.А.Гармата и др., М., Металлургия, 1983, стр.526
- Исследование оптимальных параметров удаления оксидных пленок с некондиционных титановых отходов. Нестеренко Т.Н., Сероус В.Л., 1989, стр. 27