Content
- Introduction
- 1. Global Nickel market
- 2. Method of electrolytic refining of Nickel
- 3. Secondary Nickel
- Conclusion
- References
Introduction
The raw material base and mining of nickel-containing ores in Russia and the CIS. Nickel deposits in Russia, their location and reserves. In the CIS, nickel reserves are concentrated in 88 deposits, which are located in Russia, Kazakhstan and Ukraine. According to the estimates of InfoMine, the ores of these deposits contain about 20 million tons of nickel. At the same time, Russia accounts for about 93% nickel, Kazakhstan - 5% and Ukraine - 2%. The bulk of nickel reserves in the CIS (as well as in Russia) is accounted for sulfide copper-nickel ores (about 80%). Sulfide copper-nickel ores in the CIS are located in the Krasnoyarsk Territory (Norilsk group of deposits) and in the Murmansk region (Pechenga group of deposits). Silicate nickel ores are concentrated in the Urals region (Sverdlovsk, Chelyabinsk and Orenburg regions), in Kazakhstan and in Ukraine.
1. Global Nickel market
Nickel is found in nature mainly in the form of oxides, sulphides and silicates. Nickel ores are mined in approximately 20 countries on all continents, and smelting and refining capacities are available in 25 countries. Nickel is mainly produced and used in the form of ferronickel, oxides and other chemicals, as well as pure metal. Nickel is also obtained from scrap and waste, and large amounts of secondary nickel are supplied to the world market along with the primary metal produced. Sometimes the question is raised whether the natural resources of the planet risk being depleted. In the case of nickel, there seems to be little cause for concern. Nickel is the fifth most common element found on Earth. Only iron, oxygen, silicon and magnesium are more common. However, reserves that can be mined economically are, of course, more limited. Nickel reserves belong to proven reserves at known deposits. Nickel resources (estimated to be twice as large as nickel reserves) cover sub-economic reserves, that is, those that cannot be mined for profit yet. The development of new technologies will lead to the transformation of some resources into reserves. Geological exploration contributes to increasing reserves and resources. According to some sources, nickel resources on the seabed are many times greater than those located on land. The material and resource base of the Earth, according to researchers, has a nickel reserves of more than 100 years at the current pace of the mining industry.
Австралия | 20,000 |
Новая Каледония | 12,000 |
Бразилия | 7,500 |
Россия | 6,100 |
Куба | 5,500 |
Прочие страны | 23,900 |
Всего запасы | 75,000 |
Stable global economic growth until 2007 supported an increasing production of primary nickel. According to the International Nickel Study Group, in 2007 global production reached 1.416 million tons. However, the economic crisis led to a decrease in nickel production in the period 2008–2009 and metal production decreased to 1.32 million tons in 2009. Production quickly recovered in 2010 to 1.446 million tons and further increased to 1.589 million tons in 2011 and 1.79 million tons. in 2012. At annual average, production growth between 2001 and 2012 was approximately 3.7%. The new product began to be made in China in 2005 - it was nickel cast iron (Nickel Pig Iron (NPI)) in various forms and grades. Production slowly increased in the first few years, and in 2010 already amounted to more than 160 thousand tons, and in 2011 - about 250 thousand tons. Basically, this whole product is used domestically in China in the production of stainless steel and replaced traditional products such as nickel-containing metal and stainless steel. In addition to the new NPI production in China, several other nickel projects have been implemented in other countries of the world over the past decade. Examples are Alt Barro and Puma Onca in Brazil, with a combined capacity of more than 100 thousand tons per year with full production [1].
2. Method of electrolytic refining of Nickel
Electrolytic Nickel Refining Method Since ferric iron becomes bivalent in the process of dissolving secondary materials, to convert bivalent iron and / or monovalent copper, respectively, to the bivalent state, part of the solution is treated with an acid and an oxidizing agent, such as chlorine, for further use in the dissolution process recycled materials. The solution after the cleaning operation from iron is sent to the electrolyte, where it is cleaned from copper and cobalt in the usual way, as well as deeper cleaning from iron and other impurities or to the operation of special cleaning from cobalt. The combination of the proposed features of the invention ensures the achievement of the desired technical result, i.e. achieved significant savings in material energy resources [2].
Example 1. According to the present invention, 10,000 tons of nickel anodes containing 90% nickel (9000 tons), 2% cobalt (200 tons) and 3% iron (300 tons) are refined according to the traditional technology. When refining anodes, a nickel deficiency of 500 tons is created, which is covered by dissolving secondary materials of 1,000 tons of nickel-cobalt scrap to produce 500 tons of nickel, 100 tons of cobalt and 300 tons of iron in solution. In the process of hydrolytic purification from iron, a primary ferrous cake is formed, containing 300 tons of iron and 240 tons of coprecipitated nickel. A cobalt cake containing 200 tons of cobalt and 200 tons of co-precipitated nickel will be produced during the cleaning process of cobalt. During the processing of the solution obtained by dissolving the secondary materials, 227 tons of iron are precipitated with primary cake, and only 73 tons of iron remaining in the solution will require additional soda consumption. Thus, by the present method, the main amount of iron in the secondary materials is precipitated without using soda. Purification of cobalt chloride solutions from leaching of secondary materials is carried out by the extraction method, extraction with tertiary amines. Chlorine and soda directly for this operation are not used.
Example 2. The same raw materials are processed as in Example 1. The operations of nickel deficiency replenishment and iron removal are carried out in the same way. The cobalt leaching solution is cleaned by treating the primary cobalt cake obtained by hydrolytically cleaning the electrolyte from cobalt. Cobalt is precipitated by an excess of trivalent nickel hydroxide located in the primary cobalt cake. This operation also does not require additional consumption of soda and chlorine.
3. Secondary Nickel
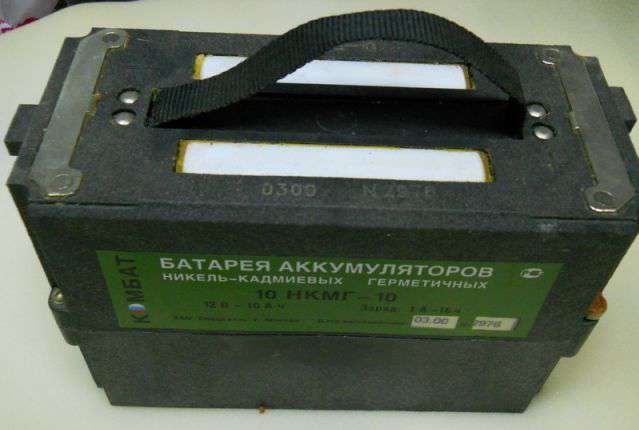
A significant segment of such recycled metals are spent nickel anodes and cathodes, which are easily detected with the naked eye, with some experience. They have a light gray color, waste items are usually covered with a greenish tinge. When glowing, nickel electrodes become yellow, they are also characterized by a short red spark, magnetised. The surface of the nickel cathodes is pimply, while the anodes are smooth.
The next common source of metal receipts at the points of acceptance - granular nickel, it is difficult to call it scrap, or waste, but you can pass it at a high price. The exceptions are ferronickel granules. They, like granulated metal grades H0 - H4, are used for alloying steel, but they have a lower acceptance cost, since it is not pure Ni, but its alloy with iron. Granular ferronickel can be distinguished by color: the metal is characterized by a dull gray tint. In contrast, nickel granules have a metallic sheen.
Heat-resistant nichrome - compound based on Ni (60 - 80%) and Cr. Grade alloy X15H60 additionally includes iron. This material comes to the secondary market in the form of heating elements, after operation inside the devices of heat exposure: kilns, drying and so on. Also nichrome can be found among the parts operated at high temperatures: rheostats, substrates for spraying systems [3].
Conclusion
It should be remembered that secondary nickel can be found in a wide range of products, from industrial parts to household and art objects. It can be broken medical instruments, jewelry and even nickel-plated pans. A separate section of scrap, nickel waste can be taken under the batteries. Even superseded Ni-Cd drives with electrical energy were replaced by metal hybrid rechargeable batteries. They also contain nickel, which, if you look closely, is found in almost all areas of human activity. It is only necessary to know this and find a receiving point conducting a waste assessment on the basis of specialized devices.
When writing this essay master's work is not yet completed. Final completion: May-June 2019.