Abstract
Содержание
- Introduction
- 1. Pb - like metal
- 1.1 Pb Consumption
- 1.2 Pb Production
- 2. Recycling
- 2.1 fragmentation of the batteries and separation of their components
- 2.2 desulphurization
- 2.3 Pyrometallurgical processing of Pb raw materials
- 2.4 refining of rough Pb
- 2.5 electrical Refining
Introduction
Known processes for Pb recovery from battery scrap include the use of a reflective furnace or a shaft furnace for Pb smelting. These processes produce large amounts of SO2, which is dangerous for the environment. Increased control over the composition of exhaust gases Pbs to a significant increase in the cost of the process. It was found that the problem of environmental protection can be largely solved by the process in which is conducted the hydrometallurgical conversion of PbSO4 to easily restore the connection, RIO without producing considerable quantities of SO2.
1. Pb - like metal
Pb is a malleable, relatively low melting point and heavy metal with a silvery-white color with a bluish tint. The density of Pb is 11.35 g/cm3. Pb is toxic. Pb has a rather low thermal conductivity, it is 35.1 W/(m·K), at a temperature of 0°C The metal is soft, cut with a knife, easily scratched with a nail. On the surface, it is usually covered with a more or less thick film of oxides, when cutting, a shiny surface opens, which in the air eventually dims. Melting point 600,61 K (327,46°C), boils at 2022K (1749°C). It belongs to the group of heavy metals. As the temperature increases, the density of Pb decreases.

Рисунок 1 - Pb ingot
1.1 Pb Consumption
Proven reserves of Pb exist in many countries around the world. According to the Geological service of the USA, currently the largest reserves of the metal has Australia - 36 million tons, the second largest reserves of China - 14 million tons. In Russia, the reserves for deposits of Pb amount to 9.2 million tonnes. Total world reserves suitable for production are currently estimated at 89 million tons. Each year, the world produces more than 4 million tons of Pb in ore with a market value of more than 6 billion dollars and the world market for advanced Pb stands at about $15 billion [1].
While Pb has a high economic value, its production is relatively economical. As with other metals, there are two main production routes. Production from mined Pb ore is, of course, the primary source of all Pb, but secondary production, when metal is recovered from processed products or from waste resulting from the production process, is of paramount importance.
Currently extracted from recycled Pb accounts for more than half the total produced in the world of metal. In the US, more than 80% of Pb is recycled, and in Europe, more than 60%. These significant figures are due to the fact that most Pb is used in recyclable products. And unlike many other materials, Pb recycling is cost-effective and therefore viable. For example, in North America, more than 80% of Pb produced is used in the production of batteries, of which more than 95% is subsequently recycled. Most Pb ores are mined in China, Australia, Mexico, Peru and the USA. In Russia, despite the impressive reserves, Pb production is at a relatively low level - about 105 thousand tons. The world Pber in the production of refined Pb is China, which accounts for about 50% of the world's metal. The European Union and the United States share the second and third places. Significant production volumes and in some Asian countries such as Japan, South Korea and India.
The scope of application of Pb changed in recent years and now approximately 80% of world consumption sector accounts for the production of electric batteries. Despite the fact that gasoline additives and solders are no longer the main consumption sectors, the ductility, density and corrosion resistance of Pb is still actively used in the construction of tanks for the storage of caustic liquids and as protection against x-rays and radiation. In addition, Pb is used in the manufacture of paints and pigments and other chemical compounds. Pb-acid batteries are used in cars. This type of battery was invented in 1859 and is the oldest form of battery. The reason for the widespread use of Pb in batteries in automotive and industrial engineering, is that Pb is able to provide a large amount of electricity in a short period of time, which is necessary to power the vehicle's starter motor. Batteries are also used to provide current, to drive heavier vehicles such as diesel or electric locomotives and submarines, and as a source of spare energy in installations with critical functions such as telecommunications and hospitals.
Pb is characterized by the highest utilization rate of all metals in secondary processing. Europe accounts for about 15% of global Pb consumption. Here, Pb is used mainly for the production of automotive batteries, which account for about 60% of the metal used. Other major sectors of the economy that consume this metal are, of course, the chemical industry, where Pb is used as a component in the production of reagents and paints, as well as the IT sector, where metal is used as solders and additives. Due to its unique physical and chemical properties, Pb has found a place in the production of various engineering products, such as protective coatings of buildings and structures (high corrosion resistance of metal, durability and ease of use-the main advantages in its use), as well as for use in medical needs, in the production of x-ray and spectrographic equipment. Pb consumption in America and Europe is more or less uniform, while Africa and Oceania account for only about 1.5% of global Pb consumption and Asia for about 50%. As a final product, Pb has found its application mainly in highly developed countries. Thus, the countries of America and Europe account for about 1.5 million tons of Pb per year, and in Asia - about 6 million tons per year. However, the dynamics of consumption growth in these geographical areas is different. If over the past 5 years, the use of Pb in Asia has almost doubled (accompanied by rapid economic growth in the region), in America the peak of metal consumption fell in 1999, after which the consumption of metal in the region even slightly decreased.
1.2 Pb Production
Recycling is the predominant direction of Pb production. The main source of secondary Pb is used batteries. Modern Pb-acid batteries contain several components suitable for processing, the most important of which are alloys based on Pb, the metal itself, its dioxide, and polypropylene. Previously, ebonite was used instead of polypropylene for the manufacture of battery cases. In table. 1 shows the content of components in used batteries [2].
Components | Structure for SAR, electrolyte | composition of OAB with fused electrolyte |
Electrolyte | 25 (~15% H2SO4) | 7.5 (H2SO4 residue) |
Pb gratings and poles | 28.0 | 34.5 |
Pb Sulfate | 19.0 | 23.5 |
Pb Oxide | 14.0 | 17.2 |
polypropylene | 4.0 | 5.0 |
Ebonite | 7.0 | 8.5 |
Separators (PVC) | 2.0 | 2.5 |
other components | 1.0 | 1.3 |
Total | 100.0 | 100.0 |
In Addition to battery scrap, secondary raw materials include various Pb-containing wastes from machine-building, metallurgical, chemical and other industries, which are partially processed together with battery scrap. This significant part of cheap and sufficiently high-quality Pb raw materials increases the efficiency of secondary Pb production together with the battery scrap.
The vehicle Fleet annually "produces" 180-200 thousand tons of Pb accumulators as waste, the content of Pb in which reaches 60%. According to expert estimates, in landfills, transport sites and other places throughout Russia is currently up to 1 million tons of Pb in used batteries. With the current situation with their processing (not more than 50%), this value increases by 50-60 thousand tons annually.
The creation of a recycling system for Pb raw materials and the prevention of the negative impact of Pb on the population should be one of the fundamental principles of the environmental policy of the Russian Federation. In industrialized countries, the increase in production of Pb from secondary raw materials was 15%, from ore raw materials – 8%.
The Increase in Pb production from ore is associated with significant difficulties: limited and irreplaceable ore reserves; reduction of metal content in ores by 20-50% in the last decade; high capital costs for the development of new fields, construction of mines, concentrators and metallurgical enterprises; increase in capital and operating costs for environmental protection facilities.
As shown in table 2, Pb recovery from waste has significant advantages over Pb recovery from ore.
Table 2. Comparison of the main indicators of Pb production from ore (numerator) and secondary (denominator) raw materials
Indicators | index Value |
Average content of the raw mass. dol.,% | 1,39/50 |
Extraction of the final product of the masses. dol.,% | 80/95 |
fuel consumption, kg/t of finished products | 700/500 |
quantity of exhaust gases, thousand m^3/t of finished products | 20/5 |
The Purpose of a car battery is clear to every motorist who is more or less well-versed in technical matters. With its first function-ensuring the start of the engine-we face every day. There is a second-rarely used, but no less significant - use as an emergency power source when the generator fails. In addition, in modern cars with injector injection battery acts as a voltage ripple smoother issued by the generator. From this it follows that you should be very careful to turn off the battery on the engine running.
All starter batteries currently available for cars are Pb acid batteries. The basis of their work is known since 1858, and to this day remains almost unchanged principle of double sulfation [3].
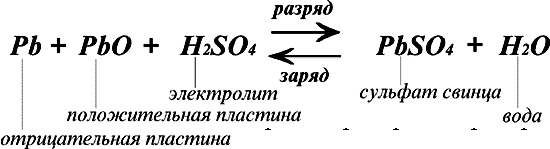
The principle of the double sulfation
As can be clearly seen from the formula, when the battery is discharged (right arrow), the active mass of the positive and negative plates interacts with the electrolyte (sulfuric acid), resulting in the formation of Pb sulfate deposited on the surface of the negatively charged plate and water. As a result, the electrolyte density decreases. When the battery is charged from an external source, reverse electrochemical processes occur (left arrow), which Pbs to the restoration of pure Pb on the negative electrodes and Pb dioxide on the positive electrodes. At the same time, the density of the electrolyte increases [3].
Any car battery is a container housing divided into six insulated can cells (picture 2).
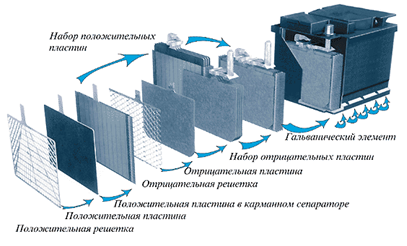
Picture 2 - Battery device
Each Bank is a complete power supply of the order of 2.1 V. The Bank has a set of positive and negative plates separated from each other by separators. As is known from the school course of physics, two differently charged plates are themselves a source of constant voltage, while their parallel connection increases the current. Serial connection of six cans and gives a battery with a voltage of about 12.6-12.8 V. Any of the plates, both positive and negative, is nothing but a Pb lattice filled with active mass. The active mass has a porous structure so that the electrolyte enters the deepest possible layers and covers a larger volume. The role of the active mass in the negative plates is Pb, in the positive-Pb dioxide.
2. Recycling
Recycling of Pb-acid batteries can be broken down into the following stages [4]:
- Draining and recycling of spent electrolyte.
- Crushing of batteries and separation of their components.
- Disposal of organic components of batteries.
- Desulphurization.
- Pyrometallurgical processing of Pb raw materials.
- Refining of Pb bullion.
Recycling of spent electrolyte. As a method of recycling the spent electrolyte containing sulfuric acid contaminated with impurities is used:
- lime neutralization with simultaneous purification of water from heavy metals. Water is discharged into the sewers, and calcium sulfate (gypsum) containing a certain amount of non-ferrous metals is sent to burial;
- neutralization of soda ash (Na2CO3) with the formation of sodium sulfate solution. The high cost of soda, significant energy consumption for evaporation of water and insufficient market capacity for sodium sulfate make this method of electrolyte processing is not always economically justified. Therefore, in some coastal and island countries purified sodium sulfate solution is dumped into the sea. Since the main impurity is iron, developed the technology of its extraction from the solution by extraction with liquid ion exchanger (diethylhexylphthalate acid);
- in some cases, the spent electrolyte can be used to wash gaseous SO2 in the production of sulfuric acid [4].
2.1 The fragmentation of the batteries and separation of their components
The Solid components are crushed and then cleaned and separated into components in special workshops. The purpose of processing is to obtain Pb-containing metal and oxysulfate fractions with a minimum content of organic matter and chlorine (PVC), as well as polypropylene with separation of waste organic and other materials (ebonite, PVC separators, polyethylene, glass fiber, etc.) with a minimum content of Pb and other elements modifying battery alloys [5].
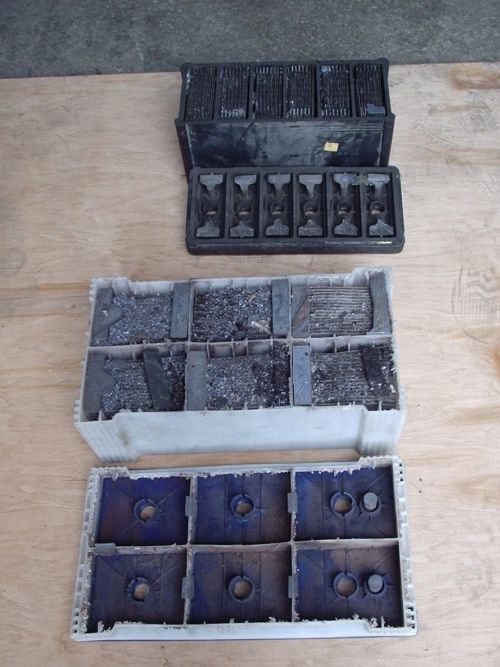
Picture 3 - Battery cutting
The enterprises use equipment complexes manufactured by specialized machine-building companies for mechanized cutting of Pb-acid batteries with automatic control of the parameters of technological operations. The main equipment of the units are crushers, separators of hydrodynamic type and classifiers of various designs. Due to the aggressiveness of circulating solutions of sulfuric acid, the equipment is made of acid-resistant stainless steel. The capacity of such installations is from 5 to 50 tons of batteries per hour.
Foreign and Russian companies have ensured that the cutting of scrap allows environmentally acceptable ways to almost completely transfer the Pb contained in the batteries into two commercial products with a high content of this metal (metal fraction and paste), to allocate commercial polypropylene and to obtain waste with a low content of Pb, which, after washing, can be used in road construction or buried in conventional landfills, that is, will not be dangerous to the environment.
Disposal of organic components of batteries. Organic components released in the process of battery cutting – polypropylene, ebonite, PVC separators, etc. – are mechanically contaminated with Pb-containing sludge and cannot be directly used in other industries.
The Main ways to find efficient use of organic components of used batteries are:
- Mechanical cleaning of sludge with water or circulating solutions.
- Mechanical removal of sludge from organic matter is carried out in various ways. In one of them is carried out washing and classification of polypropylene in several stages, its drying, melting, extrusion and granulation. Pellets are used in the manufacture of caps and cases of new batteries. Another way to remove sludge from the organic components of crushed batteries is to mechanically wash them in rotating drums with perforated walls. The rotation of the drum Pbs to the friction of the washed particles against each other and the Stripping of sludge from them, which is carried away by water jets through the holes in the walls of the drum into the sump. Production of commercial products from organic waste significantly increases production efficiency, as the cost of washed polypropylene crumbs exceeds the cost of metal Pb, although less than the cost of new polypropylene. At present, technical polypropylene of sufficiently high quality is obtained from the batteries. More difficult is the case with the ebonite, and in particular, PVC.
- Chemical dissolution of Pb and its compounds.
- For a more complete washing of PVC from Pb contained in the pores, it is possible to apply its chemical dissolution in solutions of various reagents, for example in dilute solutions of hydrochloric acid (Hcl). Pb from PVC passes into a solution from which it is precipitated.
- Use in road construction.
- Washed from sludge ebonite and PVC can be used as an additive to the buffer layers of the road in the construction of large highways. Finely ground washed ebonite can be used as an additive to asphalt. In many countries, battery manufacturers are increasingly using polyethylene and polypropylene separators instead of PVC separators, which completely eliminates the problems associated with the presence of PVC in the processing of spent batteries. It is necessary that domestic battery plants also completely abandoned the use of PVC in batteries.
- Мировой рынок свинца [Электронный ресурс]/ – Режим доступа: http://www.cmmarket.ru/markets/pbworld.htm
- Отработанные аккумуляторные батареи [Электронный ресурс]/ – Режим доступа:https://knigi.link/promyishlennaya-ekologiya_1441/otrabotannyie-akkumulyatornyie-batarei-59945.html
- Устройство аккумулятора и принцип его действия [Электронный ресурс]/ – Режим доступа: https://vuzlit.ru/1006544/ustroystvo_akkumulyatora_printsip_deystviya
- Мир знаний: Извлечение свинца из лома аккумуляторных батарей [Электронный ресурс]/ – Режим доступа: http://mirznanii.com/a/328915-2/izvlechenie-svintsa-iz-loma-akkumulyatornykh-batarey-2
- Долговечность батареи [Электронный ресурс]/ – Режим доступа: http://www.telinhelp.ru/ectags-455-2.html
- Извлечение свинца из лома аккумуляторных батарей [Электронный ресурс]/ – Режим доступа: http://refy.ru/113/339911-2-izvlechenie-svinca-iz-loma-akkumulyatornyh-batarey.html
- [Электронный ресурс]/ – Режим доступа: https://works.doklad.ru/view/BJ2Yg6m8_Jo/2.html
- Долговечность батареи [Электронный ресурс]/ – Режим доступа: http://www.telinhelp.ru/ectags-455-4.html
- Металлургия цветных металлов. Свинец. [Электронный ресурс]/ – Режим доступа: http://lmx.ucoz.ru/blog/metallurgija_cvetnykh_metallov_svinec/2012-02-15-144
- Долговечность батареи [Электронный ресурс]/ – Режим доступа: http://www.telinhelp.ru/ectags-455-5.html
2.2 desulfurization
In the pyrometallurgical processing of the paste, that is, the oxysulfate fraction of the battery cutting, sulfur from the sulfate ion passes either into the gas phase in the form of SO2, or into the sulfide-ferrous matte, or into a matte-slag melt consisting of iron, sodium and Pb sulfides. The formation of these new sulphur compounds increases the cost of preventing their pollution. The essence of desulfurization consists in the transfer of sulfate ion from Pb sulfate to solution, and Pb-in a less soluble compound that does not create difficulties in its pyrometallurgical processing. Sodium hydroxide and alkali metal carbonates or ammonium are used as desulfurizing reagents. From a solution it is possible to receive commodity sulfate of sodium which is used in production of detergents, glass, paper, etc [6].
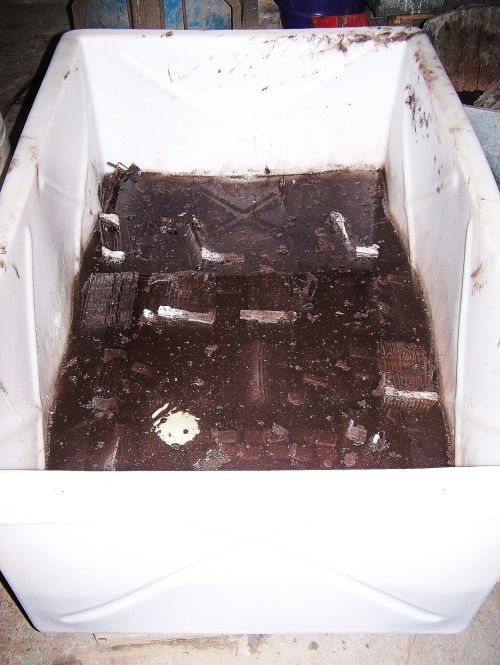
Picture 4 - Desulphurization
2.3 Pyrometallurgical processing of Pb raw materials
Was Originally developed methods of smelting in shaft and reverberatory furnace. Shaft furnace by use of heat and resilience is most effective, however, the process has significant drawbacks related to high consumption of coke, flue gas cleaning, disposal of toxins.
In a stationary reflecting furnace, the charge is heated and melted by the heat generated by the combustion of the fuel (fuel oil, natural gas) in the gas space above the furnace bath. Coke is used as a reducing agent. The disadvantages of this method of melting are: insufficient heating of the melt vertically, which Pbs to a slowdown in the recovery reactions and the formation of products difficult to separate from Pb, incomplete recovery of Pb from slag (the need for additional cleaning); a large volume of blast and the need to clean a large number of exhaust gases [7].
Further spread were rotary kilns and electric melting. In the first case, the heat of the walls heated by the torch is used and, unlike a stationary furnace, there is a constant heating of the melt from the inside and its mixing. The processes are carried out with greater speed and less fuel consumption. If you use oxygen in the blast instead of air, the volume of exhaust gases and the loss of heat with them is reduced. Melting in rotary kilns is used by 60% of the world's Pb battery processing plants. The main disadvantages of melting are the frequency of work, the adoption of special measures to avoid dust and gas contamination in the workplace, instead of receiving slag sodium matte slag melt, dangerous to the environment because of its chemical instability. When using ore-thermal electric furnaces, heat is released directly into the liquid slag layer with high resistivity when electric current passes through it, as well as during micro-arc charge in the gas phase at the electrode surface. In the electric furnace there are powerful convective flows that intensively mix the slag, heat it and contribute to a faster and deeper flow of reactions. The efficiency of heat in the electric furnace is about 70%, which is much higher than in the reflective furnace.
Direct heating of the slag eliminates the use of additional fuel and air blast for its combustion and therefore reduces the amount of waste gases and heat loss with them several times. The exhaust gases are sent to the oxidation chamber afterburning, then cooled, cleaned of dust in the bag filters and sulfur dioxide in the wet gas cleaning system. During the processing of the product of desulfurization paste sulfur dioxide content in gases is negligible, and their cleaning is simplified [8].
The main drawbacks of the electric furnace are a significant dependence of economic indicators of production on the cost of electricity, the periodic appearance of deposits on the walls of the furnace, which Pbs to the need to increase the melt temperature, that is, to increase the unproductive consumption of electricity, electrodes, refractories. Further improvement of the process and design of furnaces will allow you to create the most effective and least hazardous to the environment recycling of Pb batteries.
Another promising process for smelting secondary Pb raw materials is the use of Ausmelt technology, which is based on the use of a vertical cylindrical lining furnace with a long lance immersed in the melt from above. Through the lance, fuel and air or oxygen are introduced directly into the melt. It turns out direct heating of the melt and its rapid mixing with burning gases. Processing of materials takes place in two successive stages: melting of the charge, reducing depletion of slag. The gases of both stages are cooled and purified using traditional gas cleaning equipment.
Increased environmental performance in the Ausmelt process is achieved by fully covering the negative pressure furnace and sealing all openings. The in-furnace afterburning of process gases at a temperature above 1,300 °C and their subsequent rapid cooling make it possible to have a very low content of dioxins and furans. The disadvantages of the Ausmelt process are the production of rich and poor in Pb slag in one unit, which accelerates the wear of the lining, and presumably a short life of the submersible lance due to the burnout of the lower part.
2.4 Refining of rough Pb
When pyrometallurgical recovery heat get a rough Pb, curimage contaminated with arsenic. Rough Pb from secondary raw materials is refined mainly by pyrometallurgical methods, but in some cases electro-refining is used (after decontamination).
In the process of pyrometallurgical refining is performed first mitigation Pb (purification from antimony, arsenic, tin), and then obezbedjenje. Oxidative softening is based on a greater affinity of antimony and arsenic to oxygen than Pb. Alkaline refining (Harris process) is based on the ability of antimony and arsenic oxides to form compounds insoluble in Pb with alkali.
Decontamination is carried out in two stages. Rough decontamination of the molten Pb is carried out by liquation of copper crystals and its compounds due to the difference in specific weights and their concentration on the melt surface when Pb is cooled from 700-900 °C to 330-335 °C. The residual content of copper in the rough Pb after the liquation decontamination is 0.05-0.1%. For thin decontamination of rough Pb, copper sulfidation is used with mixtures of sulfur and sodium hydroxide, or pyrite and sodium hydroxide, or sulfur, sodium hydroxide and soda. The residual content of copper in Pb after decontamination is 0.005-0.006% [9].
Low-Temperature refining of Pb roughing in gas-or electricity-heated metal boilers with mechanical mixing (sometimes small-scale reflectant furnaces are used for oxidative refining) and a limited number of operations make the refining process of secondary Pb plants relatively low-cost, and the off-gases do not require cooling and can be cleaned of Pb-containing dust in bag filters in one stage.
2.5 electrical Refining
Electric refining consists of dissolving Pb from the anode, molded from rough metal, and its deposition on the cathode in the form of a fine pure metal. The cathodes extracted from the bath are washed with water and sent to boilers for melting and additional refining from antimony. Electricity consumption per 1 ton of Pb is 120 ... 170 kWh. Electro-refining is mainly used to clean the secondary Pb from unusual impurities of bismuth and silver [10].