ИНЖЕНЕР, № 1(25)–2(26)'2018 г.
ПРОГРЕССИВНЫЕ, СПЕЦИАЛЬНЫЕ И НЕТРАДИЦИОННЫЕ ТЕХНОЛОГИИ
УДК 621.92
Напрaвления повышения точности и эффективности обработки обтекателя
Афендиков А. С., Гусев В. В.(кафедра МСМО, ДонНТУ, г. Донецк)
Аннотация. В статье исследована проблематика обработки антенного обтекателя и перечислены факторы, влияющие на точность обработки, а также предложен вариант модернизации конструкции станка, для повышения эффективности обработки.
Ключевые слова:шлифование, точность, подача, угол поворота, микроуступ, угол поворота, шлифовальная бабка
Головной радиопрозрачный антенный обтекатель является важным элементом современных скоростных летальных аппаратов, управляемых методом радиолокационного наведения. Высокие скорости полёта обуславливают требования по стойкости материала к повышенным температурам, аэродинамическим силам. Наиболее распространённым материалом для обтекателей являются [1], : ситаллы, кварцевая и алюмосиликатная керамики, стеклокерамика литий-алюмосиликатного состава (ОТМ357). Для керамических изделий наиболее важными показателями качества поверхностного слоя, оказывающими влияние на эксплуатационные свойства деталей, являются точность формы, микрогеометрия и степень дефектности обработанной поверхности.
Целью настоящей работы является исследование формирования точности обработки ситаллокерамических обтекателей, в частности из ситалла АС–418, и анализ методов повышения точности их обработки.
Деталь представляет собой тело вращения с криволинейными образующими и круговыми направляющими. Образующие представляют собой монотонные кривые с единым законом геометрического формообразования (рис. 1). Профиль детали можно условно разделить на три участка: конический, параболический и цилиндрический. Профиль детали можно описать системой уравнений:
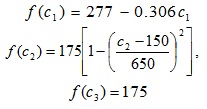
Вследствие высоких требований к точности изделия и твердости обрабатываемого материала при обработке данного класса изделий используется шлифование алмазными кругами. Обработка профиля антенного обтекателя ведется методом прямого копирования на станках модели РТ66202, оснащенные агрегатной шлифовальной головкой и системой прямого копирования. Обработка наружной поверхности изделия производится алмазным шлифовальным кругом IАI 200х10х3х76 АI – 315/250–4–М2–01. Как показал анализ формирования погрешности обработки наружного контура изделия [2], основная погрешность обработки связана со смещением профилирующей точки на образующей шлифовального круга, при его перемещении вдоль обрабатываемой заготовки.
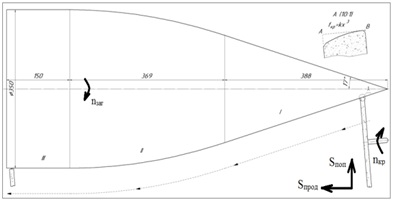
Рисунок 1 – Схема обработки обтекателя шлифовальными кругами с неравномерным износом профиля круга
При шлифовании кругом прямолинейного профиля обработка ведется одной из вершин инструмента (рис. 2), что приводит к очень быстрому износу алмазного слоя круга, алмазный круг поворачивают на некоторый угол β в плоскости оси вращения заготовки и вектора продольной подачи.
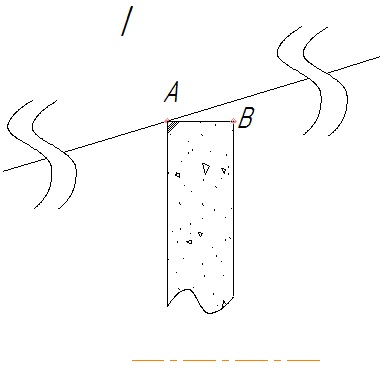
Рисунок 2 – Схема шлифования без поворота круга
Если принять профилирование детали на цилиндрическом участке равной нулю, то на конусном участке кинематическая погрешность Δe будет одинакова по всей длине участка для некоторого постоянного углу наклона β:
где α – половина угла конуса обтекателя.
Погрешность обработки на параболическом участке можно рассчитать аналогичным образом. Для любой точки на параболическом участке есть такая погрешность:
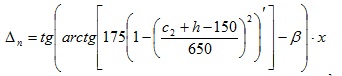
где h – ширина круга, мм.
Для устранения погрешности необходимо увеличить угол разворота оси шлифовального круга β до величины половины угла конуса α, что не позволяет конструкция агрегатной головки привода шлифовального круга.
При шлифовании поверхностей с образующими в виде полиномов третьей и четвертой степени применяются различные методы формообразования.При шлифовании валков с минимальным значение бомбировок (к≤1 мм на длине до 6000 мм) формообразование образующей [3] осуществляется цилиндрическим кругом по методу следа. При шлифовании бомбированных валов кругами с прямолинейной образующей возникает искажение образующей. В отечественных и зарубежных вальцешлифовальных станках широкое распространение при обработке крупногабаритных поверхностей получил метод огибания кругом с профилем в виде дуги окружности. Круги с выпуклой образующей исключают увеличение бомбировки по сравнению с расчетной. Однако и при использовании круга с профилем в виде дуги окружности при врезном шлифовании необходимо обеспечить управление процессом за счет регулирования врезной подачи так,чтобы на всех этапах цикла шлифования фактическая скорость снятия припуска не превышала допустимой.
На этапе врезания допустимая скорость снятия припуска обычно ограничивается мощностью привода главного движения, допустимым уровнем вибраций, размерной стойкостью шлифовального круга. На заключительной стадии цикла допустимая скорость снятия припуска ограничивается допустимой глубиной дефектного слоя, требуемой шероховатостью поверхности детали и точностью обработки. Итак, уровни скорости поперечной подачи на разных этапах шлифования различаются, поэтому для реализации оптимального цикла врезного шлифования необходимо управлять врезной подачей по определенному закону. С этой целью современные шлифовальные станки оснащаются устройствами ЧПУ с системой автоматического управления поперечной (врезной) подачей.
Для оптимизации процесса обработки данной заготовки из условий постоянства удельной энергии шлифования и сохранения постоянной формообразующей точки можно использовать поворотное устройство, разворачивающее круг при его движении вдоль образующей. С целью получения переменного по длине детали угла поворота шлифовального круга разработан специальный безлюфтовый привод [4].
Однако для более полного использования алмазоносного слоя круга необходимо изменить конструкцию шлифовальной бабки, перенести ШК на противоположную сторону шпиндельного узла. Использование такой шлифовальной головки возможно только в системах с автоматическим управлением, так как в данном случае у оператора станка нет возможности наблюдать за процессом обработки.
Таким образом, целью работы является проектирование системы автоматического управления поворотом шлифовальной бабки для уменьшения погрешности обработки профиля антенного обтекателя, эффективного использования алмазоносного слоя шлифовального круга, управления режима шлифования вдоль образующей обтекателя и циклом при многопроходной обработке.
Список литературы
- Суздальцев Е. И. Радиопрозрачные, высокотермостойкие материалы ХХI века / Е. И. Суздальцев // Огнеупоры и техническая керамика. – 2002. – №3. – С. 42–50.
- Гусев В. В. Влияние кинематической
погрешности шлифования на точность обработки антенных обтекателей / В. В. Гусев, Л. П. Калафатова, Д. В. Поколенко//Сучасні технології в машинобудуванні: Зб. наук.праць. – Вип.3. – Харків: НТУ
ХПИ
, 2009. – С. 231–236. - Кальченко В. И. Шлифование криволинейных поверхностей крупногабаритных деталей. – М.: Машиностроение, 1979.
- Быхалов А. Г. Устранение кинематической погрешности обработкипри наружном глубинном алмазном шлифовании антенного обтекателя /А. Г. Быхалов, В. В. Гусев // Інженер. Студентський науково–технічний журнал. – Донецьк: ДонНТУ, 2007. – №8. – С. 34–37.