Реферат по теме выпускной работы
Содержание
- Введение
- 1. Актуальность темы
- 2. Цель данной работы
- 3. Основное содержание и результаты работы
- 3.1. Общие характеристики зубчатых колес. Требования, предъявляемые к зубчатыми колесами на этапе проектирования
- 3.2. Классификация элементов зубчатых колес по функциональному назначению
- 3.3. Виды разрушения зубчатых колес
- Выводы
- Список источников
Введение
Зубчатые колеса являются одними из наиболее широко используемых деталей передаточных механизмов, коробок скоростей, механизмов приводов, насосов и прочего оборудования, элементы которого совершают вращательное движение.
Сроки службы строительных, погрузочно-разгрузочных, землеройных, сельскохозяйственных, горных, кузнечно-прессовых и других машин весьма ограничены.
В большинстве случаев эти машины оснащены редукторами, имеющими зубчатые передачи сравнительно крупного модуля.
Зубчатые передачи являются, и будут оставаться в обозримом будущем, одним из основных элементов трансмиссий большинства известных типов машинных агрегатов.
Зубчатая передача, как продукт производства – это наукоемкая, материалоемкая и трудоемкая продукция. Основная доля (85.90%) выхода из строя деталей и узлов машин обусловлена изнашиванием, а также усталостными разрушениями. Особое место занимают внезапные отказы передач, такие как: поломки и сколы зубьев, которые часто являются следствием внезапной остановки эксплуатации машины, приводят к аварийной ситуации и требуют увеличения затрат на ремонт. Тем более, что на ремонт и эксплуатацию машинного парка затрачивается в 4. 10 раз больше средств и материалов, чем на изготовление. Следовательно, повышение качества и эффективности изготовления и ремонта зубчатых передач является одной из важнейших задач для всего машиностроительного комплекса.
Решение данной проблемы может осуществляться, как в рамках существующих технологий, так и путем поиска новых решений.
Важным является разработка методов исследования тяжелонагруженных узлов трения – зубчатых передач, широко используемых в машинных агрегатах, для создания их стабильных эксплуатационных характеристик.
В связи с этим, необходимо было в современных условиях рыночных отношений найти область, где регулярно и в большом количестве используются тяжелонагруженные крупномодульные зубчатые передачи, ведется статистика сроков их работы во времени, определяются и фиксируются межремонтные периоды их эксплуатации, а также иметь возможность широкого внедрения зубчатых колес, изготовленных по новой технологии. В связи с этим для внедрения нами были выбраны железнодорожные предприятия Министерства транспорта РФ. Так, по данным, полученным из департамента Министерства транспорта РФ, обрабатывающего статистические данные, за девять месяцев 2003 года вышло из строя 1677 зубчатых колес тяговых редукторов электропоездов.
Обеспечение повышения надежности и долговечности зубчатой передачи мы связываем с применением обработки методом поверхностно-пластического деформирования (ППД), с одновременным упрочнением эвольвент и впадин между зубьями.
Крупный вклад в теоретическое обоснование процесса ППД и других способов упрочнения различных деталей машин внесли ученые: П. Г. Алексеев, Б. М. Асташкевич, А. П. Бабичев, М. А. Балтер, В. М. Браславский, Н. А. Б уше, А. М. Дальский, Ю. В. Димов, М. С. Дрозд, Д. Г. Евсеев, М. А. Елизаветин, М. М. Жасминов, НЛХЗобнин, В. Г. Коновалов, В. И. Костецкий, И. В. Кудрявцев, В. Д. Кузнецов, И. А. Одинг, Д. Д. Латпев, В. Н. Подураев, А. И. Промпов, Ю. Г. Проскуряков, Э. В. Рыжов, Э. А. Сатель, В. М. Смелянский, В. М. Сорокин, Л. А. Хворостухин, Н. Ф. Хлебалин, Л. М. Школьник, Ю. Г. Шнейдер, Д. Л. Юдин, П. И. Ящерицин и др.
Основная задача, возникающая при ППД – отыскание таких конструкторских, технологических решений и условий обработки, которые бы обеспечили заданное качество при максимальной производительности.
Для надежной и долговечной работы зубчатых колес к ним предъявляется ряд требований по точности основных параметров зубчатого зацепления, нормируемых степенью точности по четырем показателям. При этом физико-механические свойства рабочих элементов зубьев назначаются укрупненно, и чаще всего достигаются термической обработкой всего зубчатого колеса.
1. Актуальность темы
Изготовление зубчатых колес представляет собой сложный многоэтапный технологический процесс, наиболее длительная и трудоемкая часть которого составляет обработка зубьев. Однако существующие технологии не позволяют обеспечивать современные, все возрастающие требования к эксплуатационным параметрам зубчатых колес, особенно в условиях переменного действия эксплуатационных функций на рабочие элементы, а именно: скоростей относительного скольжения рабочих профилей зубьев, удельных нагрузок в зонах кромочного контакта, контактных напряжений в зонах взаимодействия рабочих поверхностей и пр.
Основное направление повышения качества зубчатых колес направлено на повышении точности и качества рабочих поверхностей зубьев, при этом не учитывается функциональная направленность технологических воздействий на обеспечения требуемых свойств конкретных элементов.
Обеспечение требуемых свойства элементов зубчатых колес в соответствии с условиями их эксплуатации, возможно за счет применения функционально-ориентированного подхода , основанного на полной адаптации изделия в процессе его изготовления к условиям эксплуатации в машине. Применение данного подхода позволяет изготавливать зубчатые колеса рабочих элементы которых имеют наиболее высокую износостойкость и равномерность износа по высоте зуба в течении всего срока эксплуатации.
2. Цель данной работы
Цель данной работы – повышение эксплуатационных свойств зубчатых колес за счет применения функционально-ориентированного подхода в структуре операций технологического процесса.
В соответствии с поставленной целью необходимо решить следующие задачи: разработать классификацию элементов зубчатых колес по функциональному назначению, разработать схемы технологического воздействия на базе принципов функционально-ориентированных технологий, предложить варианты реализации разработанных схем известными технологическими методами.
3. Основное содержание и результаты работы
3.1. Общие характеристики зубчатых колес. Требования, предъявляемые к зубчатыми колесами на этапе проектирования
Основу конструкции любого механизма составляют элементы, призванные передать механическое усилие от двигателя на рабочий орган. В зависимости от принципа действия принято различать несколько видов таких передач: клиноременные, фрикционные или червячные. Но самое широкое распространение в технике получили зубчатые передачи.
Такие механизмы в простейшем случае использующие сопрягаемую пару, включающую ведущую шестерню и колесо зубчатое. Благодаря зубчатой форме поверхности эти элементы входят в зацепление между собой и за счет этого передают вращение с одного вала на другой. Кроме возможности передать механическую мощность, такая передача способна обеспечить изменение скорости вращения выходного вала, относительно входного. Благодаря таким свойствам, практически в каждом промышленном механическом устройстве встречается редуктор, понижающий скорость вращения или мультипликатор, наоборот увеличивающий ее. В более сложных механизмах, так называемых коробках передач, группа зубчатых колес способна выполнить ступенчатое изменение скорости.
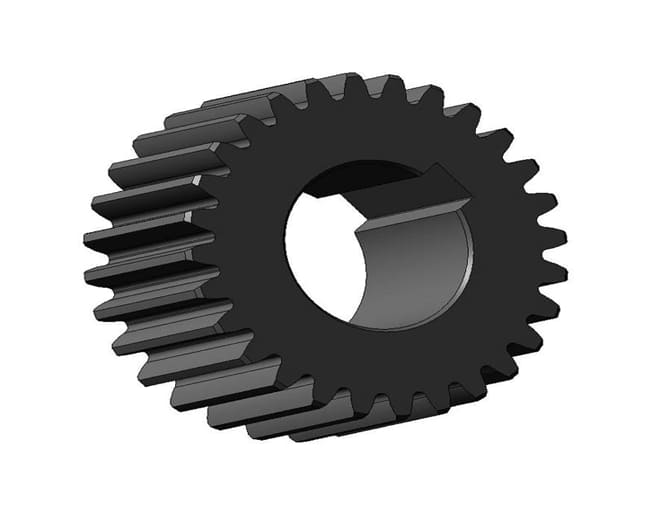
Рисунок 1 – Зубчатое колесо
Широкое распространение зубчатые передачи получили благодаря высокой надежности и способности передавать момент в большом диапазоне нагрузок и скоростей вращения (рис. 1). При этом конструкция таких механизмов отличается относительной простотой и компактностью. Зубчатые передачи не предъявляют высоких требований к обслуживанию и характеризуются длительным сроком службы.
Наряду с очевидными достоинствами, этим механизмам присущ и ряд недостатков. В отличие от других типов передач, они более сложны в изготовлении, требуют более высокой точности обработки и применения специализированного обрабатывающего оборудования. Выбор материалов для зубчатых колес должен обеспечить сопротивляемость значительным механическим усилиям. Высокая жесткость, реализуемая зубчатой передачей, способствует минимизации потерь при передаче механической энергии. КПД таких механизмов приближаются к абсолютным значениям. Но при этом конструкция не позволяет преодолевать большие значения динамической нагрузки, что часто приводит к разрушению механизма. Еще одним негативным явлением, возникающим в процессе работы зубчатой пары, становится шум. Его уровень напрямую связан частотой вращения механизма и зависит от качества изготовления колес.
Зубчатые колёса обычно используются парами с разным числом зубьев с целью преобразования вращающего момента и числа оборотов валов на входе и выходе. Колесо, к которому вращающий момент подводится извне, называется ведущим, а колесо, с которого момент снимается – ведомым. Если диаметр ведущего колеса меньше, то вращающий момент ведомого колеса увеличивается за счёт пропорционального уменьшения скорости вращения, и наоборот. В соответствии с передаточным отношением, увеличение крутящего момента будет вызывать пропорциональное уменьшение угловой скорости вращения ведомой шестерни, а их произведение –механическая мощность – останется неизменным. Данное соотношение справедливо лишь для идеального случая, не учитывающего потери на трение и другие эффекты, характерные для реальных устройств.
3.2. Классификация элементов зубчатых колес по функциональному назначению
Согласно особенностям функционально-ориентированных технологий, каждое изделие может быть разделено по уровням глубины технологий, где каждая часть. изделия может быть представлена совокупностью элементарных зон, каждая из которых представлет собой простые плоские или пространственные геометрические фигуры (точки, линии, поверхности, поверхностные слои и объемные зоны).
Классификация зубчатых колес на элементы по функциональному назначению рассмотрено в работе. При этом любое зубчатое колесо может быть представлено совокупностью исполнительных (рабочих и базирующих), связующих, вспомогательных и дополнительных функциональных элементов (рис. 2).
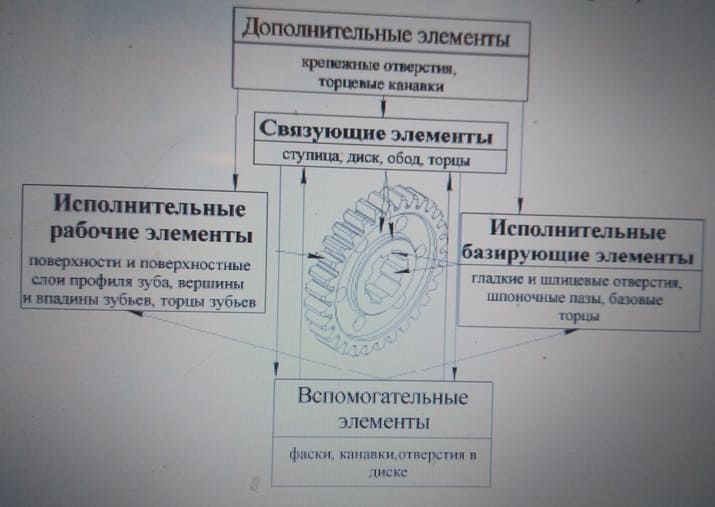
Рисунок 2 – Классификация элементов зубчатых колес по функциональному назначению
В рассмотренной классификации основными элементами, определяющими работоспособность зубчатой передачи, являются исполнительные рабочие элементы, а именно – элементы зубчатого венца, передающие крутящий момент сопряженному звену. Исполнительные рабочие элементы зубчатых колес состоят из следующих зон: объема тела зуба, эвольвентной поверхности и поверхностного слоя профиля зуба, объемные линии на пересечении эвольвентной поверхности и поверхностей вершины и профиля зуба, объемный участок у основания зуба, скругленная поверхность и поверхностный слой у торца зуба и объемный элемент у торца зуба. Основной причиной выхода из строя зубчатых колес является износ зубьев по рабочей поверхности эвольвентного профиля, который проявляется механическим износом, усталостным выкрашиванием, заеданием и поломкой зубьев вследствие действия напряжений изгиба у основания зуба.
3.3. Виды разрушения зубчатых колес
Рассмотрим основные способы обеспечения свойств направленные на устранение указанных причин преждевременного износа и выхода их строя зубчатых колес (рис. 3).

Рисунок 3 – Виды разрушения зубчатых колес: а) поломка зубьев; б) механический износ рабочей поверхности; в) усталостное выкрашивание
Пластическая деформация и поломка зубьев (рис. 3, а) у основания возникает по причине длительного действия знакопеременных окружных сил в зонах у головки зуба. Наиболее характерен данный вид износа для колес с малым числом зубьев, у ножки которых при нарезании образовалось сужение. Это приводит к возникновению повышенных напряжений изгиба, что является причиной указанных разрушений. Для избежания этого объемным зонам у основания зуба необходимо обеспечивать более высокую прочность изгиба, причем данные свойства должны изменяться по мере углубление к середине тела зуба. Это можно обеспечить за счет использования местной закалки, в частности закалки ТВЧ со специальным сердечником, выполненным по форме впадины зуба, с плавной регулировкой температуры нагрева и интенсивности охлаждения.
Механический износ зубьев (рис. 3, б) а также его неравномерность вызваны главным образом взаимным скольжения профилей зубьев, скорость которого плавно изменяется при перекатывании профилей от головки к ножке зуба. Переменность скорости взаимного скольжения способствует неравномерному износу по высоте зуба и искажению исходного профиля зуба. При этом максимальное скольжение и максимальный износ при однородных свойствах материала зубчатого колеса, возникает на головке и ножке зуба, а в полюсе зацепления он минимален (рис. 3, б). Основной технологической задачей при этом является обеспечение свойств участков поверхностного слоя зубчатого профиля в зависимости скорости взаимного скольжения в точке контакта, что может быть достигнуто при изменении свойств сопрягаемых поверхностей в соответствие со скоростью взаимного скольжения. Возможным вариантом является плавное уменьшение коэффициента стойкости к механическому износу в соответствии с графиком скорости взаимного скольжения профилей. Это можно достичь следующими вариантами технологических воздействий на рабочие поверхности зубьев:
– термической обработкой на переменную глубину по высоте зуба за счет изменения скорости прогрева и охлаждения в отдельных участков профиля зуба;
– обкатка рабочих поверхностей зубьев с различным усилием обката, таким образом обеспечивая различную степень наклепа по зонам зубьев;
– нанесением многослойных покрытий переменной толщины и с изменяющимися свойствами по высоте зуба;
– химико-термической обработкой с различной поверхностного слоя по зонам рабочего профиля зуба.
Выкрашивание с поверхности зубьев (рис. 3, в) обусловлено действием контактных напряжений при взаимодействии пары зубьев. Данный износ характерен для начального периода эксплуатации зубчатых передач – в период приработки, и проявляется главным образом в зонах поверхности у ножки и у полюсной линии зуба. Поэтому для устранения данного износа технологические воздействия должны быть направлены на повышение контактной прочности зубьев в зонах у ножки и полюсной линии с дальнейшей отделочной механической обработкой для достижения заданного параметра шероховатости. Кроме этого для устранения усталостного выкрашивания необходимо более благоприятное распределение пятна контакта зубьев и рациональные условия смазки зоны зацепления.
Выводы
Выбор конкретного способа отделочной и упрочняющей обработки элементов зубьев должен быть обусловлен условиями эксплуатации конкретной зубчатой передачи и ее назначения, что позволяет максимально адаптировать изделие к внешним условиям его использования.
Таким образом, в работе предложены основные пути повышения эксплуатационных свойств зубчатых колес, направленные на уменьшение и исправление неравномерности механического износа, деформации и поломки зубьев, а также разрушений, связанных с усталостным выкрашивание с поверхности зубьев. Рассмотренные способы должны применяться в комплексе и учитывать конкретные условия эксплуатации зубчатой передачи.
Список источников
- Допуски и посадки. Справочник. В 2-х ч./ В. Д. Мягков, М. А. Палей и др. – Л.: Машиностроение, 1983 г. Ч.2. 448 с.
- Михайлов А. Н. Основы синтеза функционально-ориентированных технологий машиностроения. – Донецк: ДонНТУ, 2008 – 346 с.
- Лахин А. М., Михайлов А. Н., Фомин И. А. Повышение эксплуатационных свойств рабочих элементов зубчатых колес на базе функционально-ориентированного подхода // Прогрессивные технологии и системы машиностроения:Международный сб. научных трудов. – Донецк: ДонНТУ, 2010 Вып. 39 С. 127–132.
- Кудрявцев В. Н. Зубчатые передачи. – М.:
Машгис
, 1957 – 263 с. - Базров Б. М. Основы технологии машиностроения: Учебник для вузов / Базров Б.М. – М.: Машиностроение, 2005. – 736 с.
- Гинзбург Е. Г. Производство зубчатых колес. Ленинград:
Машиностроение
1978 г. - Гришко В. А. Повышение износостойкости зубчатых передач. М.: Машиностроение, 1977. – 232 с.