Abstract
Content
- Introduction
- 1. Theme relevance
- 2. Goal and tasks of the research, the planned results
- 3. Review of research and development
- 3.1 Conveyor belt as an automation object
- 3.2 Overview of existing conveyor automation equipment
- 3.3 Circuit solutions for a conveyor belt automation device
- 4. Operational requirements for an conveyor belt automation device
- Conclusion
- References
Introduction
Belt conveyors are able to achieve a continuous transportation of goods over long distances, which for technological reasons leads to their indispensability in mines. Therefore, of particular importance to the issues of reliable and safe operation of conveyor lines.
To control the technological parameters of belt conveyors is essential to ensure continuous and trouble-free operation of the conveyor, and the desired performance of the conveyor and also to stabilize the tension of the belt. To solve these tasks it is necessary to exercise operational control and management, or as it is called – the diagnosis of the conveyor line.
Diagnosis – the process of monitoring the object in real time or analysis of the system as a result of her work after the fact. Diagnostic system the conveyor line must provide continuous control of technological parameters of the working and emergency modes.
1. Theme relevance
The development of automation of mine conveyor lines over a long period was determined by the need to reduce the complexity of management and increase the safety of operation of conveyor vehicles. In this regard, automated control of the conveyor line has become widespread, the technical essence of which is to centralize the control of the start-stop processes of conveyors, as well as to provide automatic protection against the development of an accident in the event of an emergency.
Diagnosing the condition of the conveyor belt, or rather, continuous monitoring of the tension and operational control of the load on the conveyor belt is a very urgent task, which will significantly increase the productivity of conveyor transport and the functioning of the mine as a whole, by preventing emergency shutdowns and losing time, since a simple mining section is unacceptable.
The belt conveyor control equipment has limited functionality and an outdated element base. Thus, the problem of developing an automatic control unit for a conveyor belt of conveyor lines is relevant.
2. Goal and tasks of the research
The goal of the master's thesis is to increase efficiency and ensure trouble-free operation of conveyor transport by developing a system for monitoring and diagnosing the condition of the tape carpet in the operating mode. Provide continuous control of conveyor belt tension, operational load regulation, light and sound indication of emergency situations.
Main tasks of the research:
- analysis of the conveyor belt as an automation object;
- analysis of existing developments in the automation of conveyor transport;
- development of a mathematical model of a diagnostic system and automatic control;
- development of circuit solutions. Structural, functional diagram of an automation device, operation algorithm;
- practical implementation of the automatic control system. Development of a mnemonic diagram of a diagnostic system.
Research object: mine conveyor belt.
Research subject: principle of control of conveyor belt tension and load stabilization.
3. Review of research and development
3.1 Conveyor belt as an automation object
The technological process of conveyor transport of the mine is one of the most important in the coal industry, as well as the most popular among other methods of transporting goods in the mine. Therefore, the task of automation. The process of conveyor transport is relevant. Conveyor belt lines due to their qualities (significant productivity, long transport length, the ability to continuously move loads, the suitability of automation and remote management, high safety of work, etc.), are the most effective means of moving bulk materials in mines (mines). They are used not only for transporting bulk cargo, but also for transporting people [1].
The advantage of belt conveyor lines is that they are quite simple to install in their simple design. Flexible endless the tape bends around the drive drum and the tension drum, and in the span between them it relies on a series of roller bearings installed with a certain spacing on the frame. The material enters the tape through the feed funnel and is unloaded through the drive drum [2].
A characteristic feature of mine conveyor lines is the high unevenness of cargo flow caused by the fact that the treatment and preparatory faces [3]. It is technological pauses in the operation of mechanisms that cause a variable flow of goods. Uneven receipt load leads to irrational use of drive power (underload), as well as excessive wear of the traction body and reduce the reliability of the AD (at overload) [4].
Having analyzed the operating mode and probable emergency situations in the operation of the conveyor belt, we can conclude that the critical load on the tape and easing the tension of the tape are the most common emergency situations, in view of the unstable cargo flow from the mining or preparatory site.
The load on the belt or the linear weight of the load can be adjusted by changing the speed of the belt by controlling the drive motor of the conveyor frequency converter, or by changing the mass flow rate of the cargo from the hopper by reducing the working cross section using a fixed gate valve.
Also, to solve the problem of operational control, indication, archiving the parameters of the operating and emergency modes, a Scada system was developed, based on the work of a programmable logic controller and mnemonic diagrams on the dispatcher workstation. The principle of operation of the conveyor line control panel or mimic diagrams of the diagnostic system is shown in Figure 1.
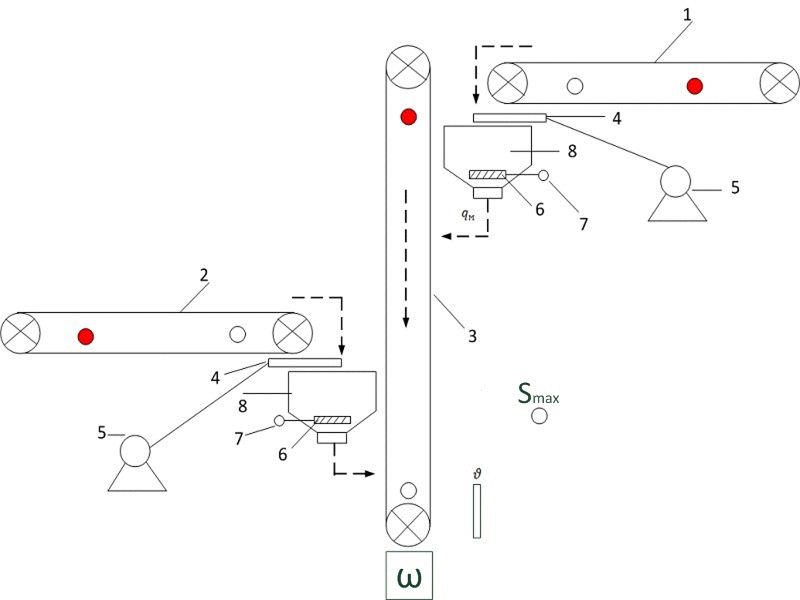
Figure 1 – General view of the mnemonic diagram of the diagnostic system on the dispatcher workstation.
(animation: 8 frames, 8 cycles, 276 kilobytes)
The figure indicates: 1, 2 – supplying local conveyors; 3 – receiving main conveyor; 4 – shutter for transferring to hopper loading mode; 5 – shunting winch of the hopper loading flap; 6 – gate; 7 – gate drive; 8 – hopper.
3.2 Overview of existing conveyor automation equipment
Currently, the following conveyor line automation equipment is known:
Complex АУК.1М – is designed to control and monitor the operation of stationary and semi-stationary unbranched conveyor lines, consisting of belt and scraper conveyors with the number of conveyors up to 10. The АУК.1М complex can also be used to control branched conveyor lines (up to three branches, each of which is controlled as an unbranched conveyor line) The number of conveyors in a line in one direction is not more than 10.
Automated conveyor control system АУК.3 – It is intended for the automated control of unbranched conveyor lines, consisting of belt and scraper conveyors with a total number of conveyors in the line up to 10 inclusive, by executive bodies of storage bins, monorail cableways (freight), rail ropes, ground roads (freight) and multi-cable chair-type roads. The complex is a component product of a conveyor belt (conveyor line). The АУК.3 complex is compatible with the АУК.1M complex in terms of control and communication lines.
Automated control system for branched conveyor lines САУКЛ is designed to:
- centralized automated management and control of branched and unbranched conveyor lines, consisting of belt conveyors designed to transport goods and transport people, with the number of conveyors controlled through one set of APU and ALS up to 60 units, and an unlimited number of routes;
- centralized or local automated management and control of individual conveyors, whether or not part of the conveyor line;
- remote control and status monitoring related auxiliary equipment;
- automatic registration and storage of information about the operation of conveyors and related equipment, control commands and settings, protective shutdowns and locks [5].
3.3 Circuit solutions for a conveyor belt automation device
Figure 2 shows a functional diagram diagram of a belt conveyor automation device
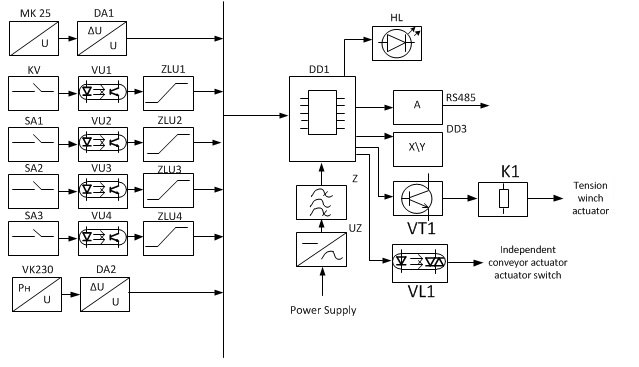
Figure 2 – Functional diagram of a belt conveyor automation device
The circuit works as follows. At the input of the microcontroller, a signal is received about the value of the load weight on the tape from the weight sensor through the matching unit, then the tension settings are selected in software depending on the weight of the load. Signal about the value of the tape tension from the analog tensile sensor and a signal from a discrete sensor of the limit switch of the tensioning winch, they enter the matching unit further into the microcontroller. Processing takes place in the microcontroller received data from sensors in accordance with the recorded program. The microcontroller supplies the generated control signals through the command input unit control to the actuator of the IU. On the control and display panel there are LEDs and an information board that inform that whether the following technological parameters are normal: the speed of the tape, its tension, is there no gathering of the tape. Also placed on the external panel operator control buttons: Tuber-switch from manual control to automatic, manual start / stop buttons.
4. Operational requirements for an conveyor belt automation device
To ensure the safe operation of belt conveyors, a prerequisite is the straightness of production the entire length of the conveyor stand and the absence of sections with a sharp change in the angle of its inclination in the vertical plane [7].
In accordance with the requirements of the safety Regulations of belt conveyor should be equipped with: sensors control the lateral gathering of the ribbon type KSL which disables the conveyor drive when the gathering tape in the direction of more than 10% of its width; devices for cleaning tapes and drums; brakes; devices catching a freight branch of the tape when it is break, or devices that control the integrity of the cables and butt joints of rubber-rope belts in mines with angle more than 10 degrees; means of protection to ensure disconnection of the drive of the conveyor in excess of the permissible level of the transported material in areas of congestion, reducing the speed of the tape to 75% of nominal (slip), exceeding the nominal speed of the belt conveyors Bremerhaven 8%; a device for to disconnect the drive of the conveyor from any point along its length; a means of dust control in places of overloads; automatic and manual fire suppression [8].
This master's work is not completed yet. Final completion: June 2019. The full text of the work and materials on the topic can be obtained from the author or his head after this date.
References
- Стадник, Н. И. Справочник по автоматизации шахтного конвейерного транспорта / Н. И. Стадник, В. Г. Ильюшенко, С. И. Егоров и др.– Киев: Техника, 1992. – 436 с.
- Батицкий, И. А. Автоматизация производственных процессов и АСУ ТП в горной промышленности/ И. А. Батицкий, В. И. Куроедов, А. А. Рыжков. – Москва: Недра, 1991. – 303 с.
- Пейсаховича, Г. Я. Подземный транспорт шахт и рудников/ Под общей ред. Г. Я. Пейсаховича, И. П. Ремизова. – М.: Недра, 1985. – 565 с.
- Маренич, К. Н. Электрооборудование технологических установок горных предприятий: учебник для вузов / К.Н. Маренич [и др.] ; К.Н. Маренич, В.В. Калинин, Ю. В. Товстик и др. – Донецк : ДонНТУ ; Харьков : УІПА, 2009. – 372с.
- Курносов, В. И. Научные основы автоматизации в угольной промышленности: опыт и перспективы развития: монография / В. Г. Курносов, В. И. Силаев; Междунар. институт независимых педагогических исследований МИНПИ – ЮНЕСКО, ОАО
Автоматгормаш им. В. А. Антипова
. – Донецк: изд-воВебер
(Донецкое отделение), 2009. – 422 с. - Груба В. И. Технические средства автоматизации в горной промышленности. – В.И. Груба, Э. К. Никулин, А. С. Оголобченко –К.: ИСМО, 1998. – 373 с.
- Овсянников, Ю. А. Автоматизация подземного оборудования: справ. рабочего / Ю. А. Овсянников, А. А. Кораблев, А. А. Топорков. – Москва: Недра, 1990. – 287с.
- Правила безопасности в угольных шахтах [Электронный ресурс]: утв. приказом Гос. Комитета горного и тех. надзора ДНР и Министерством угля и энергетики ДНР 18.04.2016 г. № 36/208: ввод в действие 17.05.2016. – Донецк, 2016. – Режим доступа:https://doc.minsvyazdnr.ru. – Загл. с экрана.
- Каминский, М. Л. Монтаж приборов и систем автоматизации / М. Л. Каминский, В. М. Каминский. – Москва : Высшая школа, 1997. – 304 с.
- НПАОП 10.0 – 5.18 – 04. Инструкция по противопожарной защите угольных шахт.