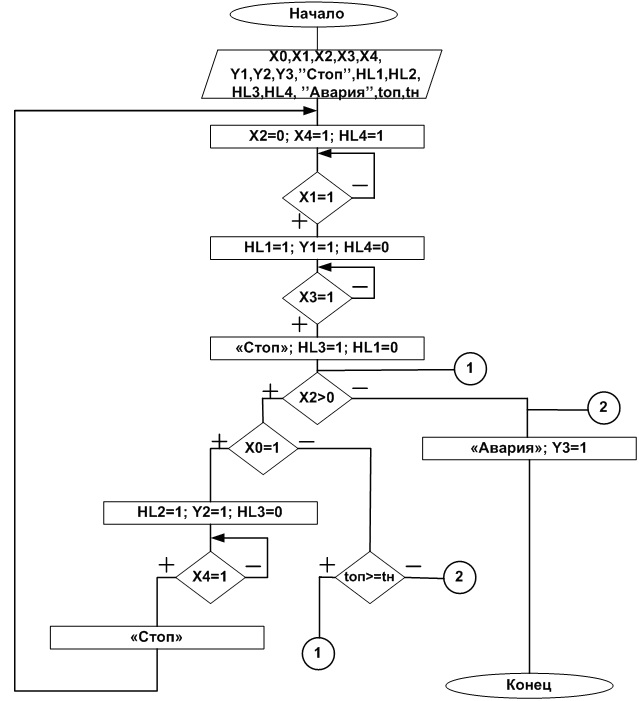
Рисунок 1 – Алгоритм работы устройства стабилизации грузопотока конвейерной линии
Автор: Бутко А. А., Чичикало Н. И.
Источник: Шоста міжнародна науково-практична конференція Інтегровані інтелектуальні робототехнічні комплекси
, 27-29 травня 2013 р. – Київ, НАУ – 2013, с. 55-57.
Основной особенностью конвейерного транспорта как объекта управления является высокая неравномерность грузопотока, вызванная тем, что конвейерная линия по своему технологическому назначению является транспортным объектом, обслуживающим очистной и подготовительный забой. А технологические паузы в работе механизмов (аварийная остановка лавы, периодические изменения скорости перемещения комбайна вдоль лавы и т.д.) являются причиной неравномерного грузопотока. Неравномерность поступления груза ведет к нерациональному использованию мощности привода (при недогрузке), а также чрезмерному износу тягового органа и снижению надежности АД (при перегрузе) [1].
В настоящее время существует два способа уменьшения неравномерности грузопотока: регулирование частоты вращения приводного электродвигателя конвейера и применение промежуточных накопительных бункеров. Однако использование частотно-регулируемого привода имеет ряд спорных моментов: диапазон регулируемой частоты для конвейеров ограничен и не приводит к экономии энергии; при уменьшении частоты вращения надо обеспечить рабочий момент на валу двигателя, к тому же длительная работа в режиме пониженных частот приведет к принудительному охлаждению, как двигателя, так и преобразователя. Помимо этого данный подход не позволяет обеспечить выравнивание грузопотока для последующих конвейеров в цепи, что требует применения регулируемых приводов на каждом конвейере [2].
Таким образом, с точки зрения повышения энергоэффективности, в шахте целесообразно регулировать не производительность конвейера, а поступающий на него грузопоток, приближая его к номинальному значению, тем самым предотвращая режим холостого хода и увеличивая КПД конвейерной установки. Это может быть достигнуто за счет применения аккумулирующих бункеров (бункеров-питателей), объем, и производительность которых будут определять, и выравнивать грузопоток на забункерной конвейерной линии [3].
Для учета производительности бункера необходимо знать состояние его загрузки (уровень угля в бункере). Зная этот параметр, а также массу породы на ленте забункерного конвейера, можно обеспечить равномерное распределение погонной нагрузки на ленту забункерного конвейера за счет регулирования положения шиберного затвора бункера.
Таким образом, главной целью создания устройства стабилизации грузопотока конвейерной линии является повышение эффективности и надежности конвейерного транспорта за счет уменьшения неравномерности загрузки магистральных конвейеров.
На рисунке 1 приведен алгоритм работы устройства стабилизации грузопотока конвейерной линии, который в полной мере описывает принцип работы данного устройства.
Рисунок 1 – Алгоритм работы устройства стабилизации грузопотока конвейерной линии
На рис. 1 показаны следующие обозначения:
Х0 – нижний уровень угля в бункере;
X1 – верхний уровень угля в бункере;
X2 – удельный вес угля на конвейерной ленте;
X3 – срабатывание концевого выключателя КВ1 на полное открытие шибера бункера;
X4 – срабатывание концевого выключателя КВ2 на полное закрытие шибера бункера;
Y1 – включение двигателя шибера на открытие;
Y2 – включение двигателя шибера на закрытие;
Y3 – включение в работу специальной бункероочистительной установки;
Стоп
– выключение двигателя шибера бункера;
HL1 – световой индикатор верхнего уровня;
HL2 – световой индикатор нижнего уровня;
HL3 – световой индикатор на срабатывание концевого выключателя КВ1 (полное открытие шибера бункера);
HL4 – световой индикатор на срабатывание концевого выключателя КВ2 (полное закрытие шибера бункера);
tоп – время, за которое уровень угля в бункере достигнет нижнего значения;
tн – номинальное время, за которое уровень угля в бункере достигает нижнего значения;
Авария
– подача сигнала на отключение участковой конвейерной линии и оповещение диспетчера шахты об аварии.
Следует отметить следующее: емкость бункера 20 м3; масса незаполненного бункера составляет 6 тонн; масса полностью заполненного углем бункера составляет 20 тонн; высота разгрузки от верхнего значения до полного опустошения равна 2 м, а высота разгрузки от верхнего значения до нижнего – 1,7 м; номинальное время за которое уровень угля в бункере достигнет нижнего значения после того, как достиг соответственно верхнего значения составляет в среднем 7-10 минут с момента полного открытия шибера бункера; в качестве двигателя шибера используется маломощный асинхронный двигатель, мощность которого составляет 5,5 кВт.
Таким образом, предложенное устройство стабилизации грузопотока за счет применения технологических ресурсов (способов предупреждения, ликвидации сводов) обеспечивает оптимальное управление транспортной системой шахты.
1. Малиновский А. К. Автоматизированный электропривод машин и установок шахт и рудников / А. К. Малиновский. – М.: Недра, 1987. – 280 с.
2. Толпежников Л. И. Автоматическое управление процессами шахт и рудников / Л. И. Толпежников. – М.: Недра, 1985. – 352 с.
3. Гаврилов П. Д., Гимельштейн Л. Я., Медведев А. Е. Автоматизация производственных процессов: Учебник для ВУЗов / П. Д. Гаврилов, Л. Я. Гимельштейн, А. Е. Медведев. – М.: Недра, 1985. – 216 c.